August 2022 Vol. 77 No. 8
Features
The Road to Safety Starts with Stability
How Offset Compaction Roller Attachments Ensure a Safer Jobsite
Lynn Marsh | President, Road Widener LLC
Safety is the highest priority on any construction job site, but not every equipment solution aids in attaining that safety goal. In fact, in 2020, more than 174,100 injuries and 124 deaths occurred on construction job sites throughout the United States.
As alarming as those numbers are, the true picture could have been much worse. Those statistics only encompass reported cases. Many job-site accidents and near misses – with potentially dire consequences – are never reported.
The United States Department of Transportation (USDOT) has made a significant move toward improved safety with its initiative to reduce traffic fatalities to zero by 2050. Not only does this apply to crashes due to highway traffic, but it also protects construction workers when building or repairing roads in both urban and rural areas.
The Moving to Zero movement, skyrocketing insurance premiums and injury risk are making safety features a key consideration for most contractors, prompting manufacturers in all segments to focus on innovations to eliminate that danger.
Compaction equipment is a prime example of a potentially problematic design, especially on uneven or side-sloped surfaces. It is not uncommon for road construction crews to witness a silent rollover, watching their crewmember jump to safety when the equipment they are operating unexpectedly gives way to gravity while compacting a steep slope.
Many ride-on compaction rollers often succumb to rollover accidents due to their rigid design and high center of gravity, which offers little protection or stability for crew members.
Manufacturers are taking steps to eliminate this far too common job-site incident and are doing so in the form of an attachment paired with equipment they already own. Featuring an offset arm, crews can safely and effectively compact material from flat ground using the compaction attachment – allowing for safe work at virtually any angle.
Safety is in the design
This new approach to compaction is achieved by relocating the drum to a remote-controlled offset arm that can be attached to almost any grader, compact track loader, wheel loader or skid steer – immediately solving the safety issue. By employing an attachment, the host machine provides a separate source of power for the compaction drum and, thanks to the offset arm, enhances stability and safety for the operator.
With its offset position, the drum can pivot up to 30 degrees and reach 30 inches below the mounting point. The host machine can drive safely on flat ground while the attachment arm extends to the furthest, steepest edge of sloping road shoulders and ditches. This allows the roller to easily compact slopes at various angles that would flip a traditional compaction machine.
The increased safety offered by the offset roller design reduces workers comp claims, lowers insurance premiums and enhances a contractor’s overall safety ratings – a key factor for contractors in a competitive bidding environment.
Further, shifting the drum to an offset arm attachment doesn’t just drastically improve safety, it also unlocks a host of other benefits.
Maximum capabilities in a compact package
Although safety is the top priority on any job site, the efficiency and quality of a job, along with equipment versatility, also prove critical.The attachments effectively compact a range of materials, from gravel, stone and topsoil to even hot asphalt mix.
With the high infrastructure demand and scarce, inexperienced workforce, ease of use – in terms of equipment – is key to a project’s overall efficiency. Some offset compaction attachments incorporate remote controls, combining safety with an intuitive operation that is easy to learn, and allows the operator to adjust the height, angle, extension and compaction adjustments all from the comfort of the host machine’s cab.
While a compaction roller attachment may not achieve density as quickly as a ride-on roller on a flat roadway, it excels in a sloping ditch or trench, which places an operator in a hazardous position. Because of the rigid design of traditional compaction rollers, and the stability issues working on a slope, operators tend to drive at a slower rate, resulting in a slower compaction rate.
Alternatively, the offset compaction roller attachment allows an average vibratory density of 106.5 pounds per cubic foot in just one pass on a typical gravel shoulder.
Efficiency is not only seen through the work on the job but also by reduced transportation challenges. The compact design of compaction attachments allows them to fit on any common trailer along with the host machine – and other core attachments – and be towed by a standard pickup truck. No heavy-haul trailers or permits are required.
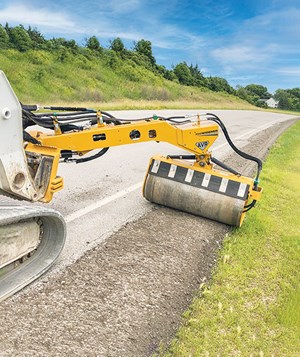
Additionally, compaction roller attachments can offer contractors the ability to expand their application capabilities and win more bids by incorporating an adaptable system into their business model. Compaction roller attachments can be purchased in a variety of interchangeable drum widths, ranging from 2 to 4 feet, providing heightened adaptability.
To get the same benefit with traditional compaction machines, contractors would have to purchase multiple self-propelled units, all with engines and transmissions that would need to be continuously maintained. This flexibility opens up more opportunities for contractors, allowing them to meet a range of job specifications without the hassle of maintaining, hauling and storing several pieces of equipment.
Stamp of approval
The safety and productivity benefits of compaction roller attachments are powerful, and the data that demonstrates the impact they bring to the industry speaks volumes.
The New Hampshire Department of Transportation (NHDOT) conducted a study to measure the effectiveness of offset compaction roller attachments connected to a wheeled skid steer, versus the traditional steel drum and rubber-tired rollers used by NHDOT contractors.
The study examined the density of gravel compaction on a road shoulder to determine which method of compaction would yield the most consistent results in terms of gravel density, ensuring a longer wear life of the road shoulder. NHDOT recognized that longer wear life would result in saving thousands of dollars for the state that could be reallocated to other areas to improve infrastructure.
In the past, contractors for the NHDOT primarily used self-propelled rollers in static mode to prevent the risk of rollovers or sliding into ditches. To prove the effectiveness of the study, the self-propelled rollers were utilized in both static and vibratory modes to accurately compare with the offset compaction roller attachment, which was only capable of operating with vibration.
For this compaction testing, the material was placed two ways for each roller, first being approximately a half-inch higher than the existing pavement prior to compaction, and second, the material was placed flush with the existing pavement.
The results of the study showed that the offset compaction roller attachment had almost equal compaction when tested against the two other rollers that were eight to 22 times greater in weight. Additionally, the variance of the offset compaction roller attachment was the least out of the three.
In summary, the offset compaction roller provided a more consistent density of compacted gravel and gave workers added flexibility with its offset arm, eliminating the risk of injury and rollovers compared to other methods.
Additionally, the compaction attachment improved efficiency by allowing the operator to remotely control the position of the roller from the host machine, enabling coverage over the entire shoulder as compared to ride-on methods that require straddling the shoulder or not allowing for full compaction coverage.
Minimal maintenance
When it comes to the impact of maintenance, traditional ride-on compaction rollers have several grease fittings that need to be maintained, and they often have a buildup of debris that requires frequent cleaning. However, with compaction roller attachments, there is almost no maintenance to speak of.
Without the need for an engine, powertrain or any associated parts of its own to operate, advanced offset compaction rollers require 90 percent less maintenance than ride-on compaction machines, by cutting out traditional engine and transmission service.
In a world where so many elements are outside of our control – the supply chain, the price of fuel, inflationary costs, and more – it is more critical than ever that contractors control risk and costs wherever they can. And their equipment investment is a great place to start.
By carefully evaluating equipment selection and choosing options that maximize the capabilities of their current fleet, contractors will see an increase in the efficiency and profitability of their business while providing unparalleled safety for their crew. UC
ABOUT THE AUTHOR: Lynn Marsh is the president of Road Widener LLC and has 20 years of experience in the road construction industry.
FOR MORE INFORMATION:
Road Widener, (844) 494-3363, roadwidenerllc.com
Comments