January 2019 Vol. 74 No. 1
Rehab Technology
NASSCO Standard Bearers: Larry Kiest
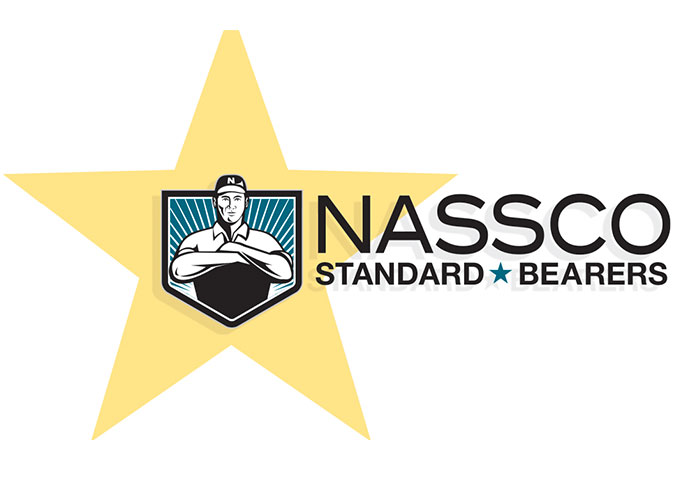
EDITOR’S NOTE:
NASSCO just completed its 44th year and continues to set standards for the assessment and rehabilitation of underground infrastructure. As the association experiences remarkable growth, this series profiles those who have made significant contributions, and impacted the continued acceptance and growth of trenchless rehabilitation methods. This is a bi-monthly installment in a series of articles exploring the history of NASSCO through the eyes of industry leaders.
This month, NASSCO honors Larry Kiest, founder of LMK Technologies. Kiest has many inventions to his name and has continuously worked to enhance the underground infrastructure industry. He has served on multiple industry boards and committees, and is a regular expert speaker at conferences. A true overall industry leader and inspiration, Kiest remains actively involved in striving to improve and enhance industry products and performance.
I was born, raised and, for the past 25 years, have run LMK Technologies, a leader in CIPP products, in Ottawa, Ill. Located 1.5 hours outside of Chicago, this small town provided me with everything I needed to develop the skills and experience to identify opportunities to repair underground infrastructure and take those opportunities to market.
When I graduated high school at 17, my dad, Larry Sr., sent me to get my laborer’s card and then literally threw me into the trenches of the company he still owns to this day, Larry’s Universal Inc. I started out as a “bottom man” laying sewer and water pipes. I was lucky enough to have worked in the trench with an old timer who taught me the tricks of the trade for laying pipe by digging a bell hole, pushing the pipe home, and bedding the pipe on-grade.
Being the owner’s son, the field guys used to joke that I had a roofer’s card because I did every job under the roof. I looked at it as the best education I could ever get. I was trained by experienced plumbers many years older than me who had been doing this work for 30, 40 or even 50 years before I came around. I paid close attention to everything they did.
Once I gained some basic knowledge from my in-the-trench, on-the-job training, my dad taught me how to set up and run batter boards to maintain line and grade for the sewer pipes we installed. Yes, once I learned how to squint one eye and align two strings so that I could only see one string and simultaneously read a grade pole, I was ready for the next phase of my on-the-job education. That’s when my dad sponsored me as an apprentice plumber in the five-year apprentice program through the Illinois Department of Public Health.
When the apprenticeship was complete, I went to Springfield, Ill., to take the tests necessary to become a licensed plumber in my own right. My dad is one of the hardest working guys I know; that said, he made sure I had my chauffeur’s license (before the days of CDL) on the day I turned 16 and, once I completed my plumber’s apprenticeship, my dad then had me join the operators in my hometown where I worked as an apprentice through Local 150 Operating Engineers.
Long days – and nights
There was no such thing as a short day working for my dad. He had me running heavy equipment by day and doing service work by night. In the early 1980s we installed all the underground utilities for local developers. That meant we cleared the land, installed storm sewers, sanitary sewers, lift stations, water mains and service lines, and we even did a fair amount of auger boring under railroad tracks, roads and even a 330-foot push of 36-inch under Interstate 80.
The construction work ended at 3:30 p.m., and that’s when I jumped in my plumbing van and responded to service calls. I was the plumber who worked every holiday or after hours, answering service calls when other plumbers wouldn’t. While others saw it as a distraction, I saw it as an opportunity to build our family business.
One of those calls came many years ago from the Lodge at Starved Rock State Park, a beautiful wilderness area overlooking the Illinois River with steep sandstone canyons formed by glacial meltwater. It was the Fourth of July during the mid-1980s, and the Lodge was full for the holiday. The entire sewer system was backed up with tree roots and grease.
Another plumber and I went out to clean the pipe. We found the sewer pipe went from the building through the woods, where we located the blockage near a cliff. We hand-dug the pipe only a few feet deep and made the repair. We saved the day for the Lodge and, because of this one service call, we ended up with the contract to service the park for many years.
The part of my job that I’ve always enjoyed most is finding solutions to problems. I learned this from my dad, who learned it from working with my grandpa and my great uncle, who were also plumbers. The old sewers installed in small-town Ottawa (the silica sand capital of the world) date back to the mid-1800s and were made using dynamite and steam shovels. Years later, as pipe defects occurred, the silica sand used as trench backfill poured through the pipe like an hour glass, and huge cavities were formed under the pavement. The flow then carried the sand downstream, creating an ongoing problem all over the West side of town.
Before we knew anything about CCTV cameras, my dad and I were sleeving lateral sewer pipes by digging a short trench about 8-feet deep (since most of the homes have basements) just big enough to break-away a short section of the pipe and insert four-inch PVC inside of the six-inch clay pipe. It was a very crude, yet effective, method compared to open cut and replace methods.
Without a CCTV sewer camera, we used a tape measurer to gauge the length from the excavation point to the city sewer main located in the center of the street. We then subtracted a foot and that’s the length of PVC we pushed down the old pipe. You might say this was my first introduction to trenchless technology!
Our sleeving operation had its challenges and I can remember we hit a lot of offset joints. We overcame that by applying pressure against the new pipe while rotating the pipe using a pipe strap to hop over the offset joint. When we came to bends in the pipe, however, we couldn’t go any further. I thought, “I need to find a pipe that is smaller, more flexible, one I could push down like a hose and then expand to full size.” That first idea didn’t go anywhere, but it was the start of my desire to solve problems, which just snowballed from there.
Eye-opening
I learned about the NASTT No-Dig conference and in 1991 flew – for the first time in my life –to Kansas City, Mo., where the show was held. I walked in and was like a kid in a candy shop. I was so excited, stopping by every exhibitor’s booth and scooping up all the information I could get my hands on.
Two days later, I was in a manhole located by a railroad track, picking up bricks that had fallen into the invert, trying to make repairs using quick-setting mortar and brick. The problem was, every time a train rolled by, the ground shook, and the bricks were jarred loose. Luckily, I remembered some literature on repairing manholes that I had picked up from the show.
I called APM/Permaform and spoke with Bill Shook, and in October 1991 I signed a license to rehabilitate manholes. That month I also started my own company, Performance Pipelining. Bill sent me everywhere fixing manholes – to the Grand Cayman Islands, Israel, Canada and all over the United States. I quickly became an expert in manhole rehabilitation (and flying!), which fueled my passion to discover other technologies.
Already proven in Europe, I knew cured-in-place pipe lining was going to be the next big thing in the United States. Working for Insituform Midwest as a sub-contractor doing their manhole rehab, along with some spot repairs using Link-Pipe out of Canada, I was intrigued by how they inverted this liner tube through a pipe. I was inspired by Insituform’s technology, which led me to develop my very first patent: a sectional CIPP liner that can be remotely inverted anywhere in the pipe.
I was developing solutions for my trenchless construction company and it was those solutions that led me to start LMK Technologies. The first conference where my company had an exhibit booth was in 1993 at what was then called the Pumper & Cleaner Show in Nashville, Tenn. I quickly became a trenchless tradeshow fan and attended every regional and national industry conference that I could. Being young in the trenchless industry and in operating my own business, I needed to know the ropes in what I considered a highly skilled industry with engineers and a lot of smart people.
That is where Bill stepped in; he knew everybody, while I knew no one. In those early years of my Performance Pipelining/LMK businesses, Bill was, and always will be, my mentor. Long ago we used to share exhibit booths and I remember the day we upgraded from a 10’x10’ to a 10’x20’ booth; it was a big deal and represented my company’s growth. With a lot of support and a lot of hard work, I sold my very first patent license in 1994 to a Toronto-based company called Telescan.
Bill also introduced me to NASSCO and I immersed myself in committee participation, because I knew that was a great way to contribute my knowledge, learn from others and meet industry peers. One year at a NASSCO Annual Conference I took a quick bathroom break and came back in to a room filled with laughter. The joke? While I was out of the meeting, they nominated me to serve as the chair of the Lateral Committee. I accepted, and that’s where it all began. I remember burying myself in a room for about a week, writing and sharing my ideas with other NASSCO Lateral Committee members, finally delivering a lateral specification guideline that helps set standards to this day.
There’s a lot to smile about when I think about all that went on throughout the years in the making of the trenchless industry to what it is today. One of those memories is of Alan Thomas, NASSCO’s executive director at the time, who would always introduce me by saying, “Larry has been working on this thing for laterals. Whoever gets that figured out, it will be a big deal.” I never imagined just how much of a big deal that would be. It was people like Alan who were a big inspiration to me.
RehabZone Live
I can’t express enough the importance of NASSCO committee participation. In addition to serving on the NASSCO Board of Directors for multiple terms, which I considered to be a great privilege, I was also deeply involved in the RehabZone, an annual event at the UCT Show. I wanted to bring a more interactive opportunity to NASSCO and UCT, so I co-chaired and eventually chaired the RehabZone Committee in exchange for a couple things: the ability to serve beer and show live technology demonstrations. They obliged, even throwing in a popcorn machine!
The first year, I brought a semi-trailer down with the NASSCO booth inside and a bunch of stuff for live demonstrations. We had set up an entrance into the RehabZone using an air inverting liner that cycled back and forth through glass pipes, passing through multiple 90-degree bends. There was also a manhole rehab demonstration, a CIPP lateral lining demonstration, and laser profiling demonstrations.
Grouting was another popular demonstration, and the late Dick Schantz was very instrumental in helping with this event. When the timer broke and the air-inverted liner demonstration through the glass pipe was dead in the water, it was Dick who was quick to help me. He rigged up something to get us through the show; he was a one of a kind, and I sure do miss him. All in all, the show was a great success and the RehabZone has grown in popularity every year since that time.
No matter what NASSCO committee I participated in, or which term I served on the board, I have seen NASSCO take a proactive role in providing education and awareness on trenchless technologies and setting standards for the assessment, maintenance and rehabilitation of underground infrastructure, as well as assuring the continued acceptance and growth of trenchless technologies.
Standards are critical. I am still a licensed plumber to this day, and I can tell you that the work performed by a plumber is regulated by the state, and plumbers must completely comply with certain standards and codes. In the plumbing world those codes are like religion. I understood that very early on in my career as a plumber, but when I was introduced to the world of trenchless pipe repair, I saw a lot of “whatever-you-can-make-fly” situations get accepted, primarily due to low cost and compounded by a low-bid environment.
I knew we could do better, and as I continued to watch Insituform folks, I recognized how they advanced the CIPP industry through the development of the proprietary ASTM F1216 Standard. Back in the day and still today, that is the industry standard specified throughout North America for rehabilitating mainline sewers using CIPP.
Having seen the impact of the F1216, I recognized the need to also develop standards for laterals, sectionals, manholes and so on. Going through the laborious process, I wrote ASTM standards for these processes, along with a trenchless clean-out system for vacuum excavation. Most recently, I worked with one of my good friends, Tim Back, P.E., to develop the F3240 Standard for gaskets used to seal and prevent leaks in all types of CIPP.
Getting better never ends
There was – and still is – a lot of opportunity within NASSCO and other organizations to develop specifications, improve engineering practices and evaluate the low-bid concept compared to long-term best value. In the end, our industry and the customers we serve can’t afford low cost, short-lived solutions.
My hope for NASSCO’s future is to continue to promote education in our industry. As our industry grows and advances, we must improve quality control, develop more stringent standards and influence codes with regulatory agencies. That is also a major focus of LMK. We recently built a 10,000-square-foot facility designed specifically for education. We host educational events and training in the center and also offer the space complimentary to industry organizations for training events. It’s all with one goal in mind: to promote long-lasting, quality trenchless products and services by setting industry standards that continually raise the bar and advance the industry.
I am excited about NASSCO’s membership, committees and its focus on supporting skilled trades to encourage more young people to enter our industry. NASSCO recently became a national sponsor of SkillsUSA, a non-profit organization that trains middle- and high-school students across the country in construction trades and other skills. I am anxious to see how NASSCO’s support will help build awareness of career opportunities in trenchless technologies. Not everyone is cut out for college; presenting skilled trades as an honorable and extremely viable career choice is good for our industry and our communities.
Look at me, for example. In my graduating yearbook, I was voted “Least Likely to Succeed.”
Comments