September 2018 Vol. 73 No. 9
Features
Hard Rock Directional Completes 8,414-Foot Intersect Drill Under Midland, Texas
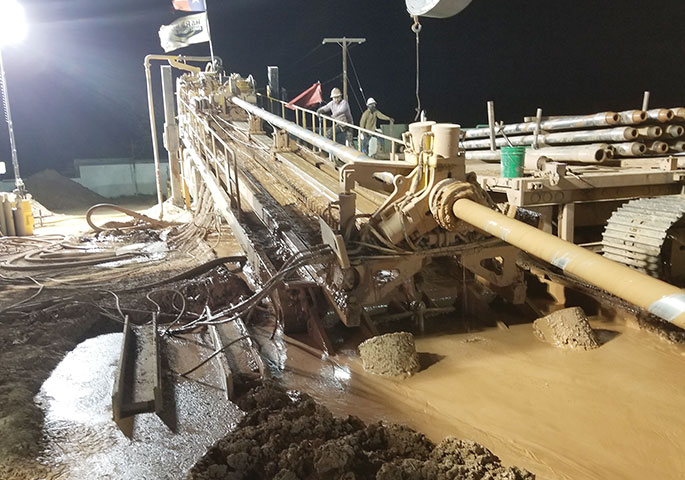
Hard Rock Directional Drilling LLC recently completed an 8,414-foot-long horizontal directional drilling (HDD) installation of 30-inch diameter steel pipe in Midland, Texas. Three smaller-diameter flex steel pipes were placed in the larger pipe before it was pulled in.
The complex project included an intersect 5,000 feet from the starting side of the installation.
Project owner was Fasken Oil and Gas and the pipeline contractor was Kingsley Construction Inc. The HDD segment is part of a new pipeline that will carry oil, gas and water from wells to be drilled. All product will be moved through the pipelines to a Fasken bank battery. The total length of the pipeline is 4.5 miles.
Directional drilling was employed on the 8,400-foot portion of the route because it went through the middle of the city of Midland and crossed two major roads.
“A challenge was, of course, the length of the installation and the diameter of the pipe,” said Cory Baker, Hard Rock general manager. “We spent a long time planning and assisting with the design of the project.
“Another challenge was working in the public eye, which always brings concerns. Also, drilling under and adjacent to two major roads required care to prevent the inadvertent fluid returns, so we constantly monitored drilling fluid properties and the amount of fluid we had coming back.”
Intersect solution
Two Vermeer drill rigs were employed on the project: a D1000x90, which bored 5,000 feet, and a D500x500, which bored 4,000 feet.
“We decided,” explained Baker, “to use the intersect method due to the projected 8,500-foot length of the crossing and because there was a horizontal S-curve at the exit point of the crossing. We knew we would be more successful in completing the S-curve by having a rig on the exit side. The planned intersect point was in the tangent of the crossing where both paths were flat and level and could have the Tru-Tracker wire above this point for locating the downhole steering sensors.”
In fact, the crews were able to use the Tru-Tracker system the entire length of the crossing.
“For this reason,” he continued, “we chose Tensor to accomplish the intersect, since we were able to track the entire length once we reached the intersect point. We were able to make the intersect on the first attempt. We used our own in-house Steer Hands to operate the tooling.”
Ground conditions were sandstone and limestone. The drill units used 8-inch mud motors. Twelve-and-three-quarter-inch bits were used to ensure there was sufficient annular space around tool joints to keep annular pressure of the hole as low as possible.
The average depth of the crossing was 60 feet.
“We chose this depth,” Baker said, “from looking at the GEO information from the core drills to assure we were in the most suitable ground conditions to be successful for this length and size of crossing. It took a total of 10 days to complete the interest and have the bit out on the other side.”
Kingsley supplied support equipment for pipe handling, which included track hoes and side booms. Pipe was strung out and welded into one string on the exit end. Fasken had to acquire temporary work space from a ranch that ran beside the DOT right-of-way to provide plenty of room to lay out the entire length of the 30-inch pipe.
Extra pipe
Two 8-inch diameter and one 6-inch diameter flex steel pipes were placed in the 30-inch casing prior to pull in. The assembled string with flex pipes inside weighed 1.8 million pounds. The pipe was placed on 190 rollers for support.
“We did three ream passes which were 24, 36 and 48 inches,” Baker said. “We used hole openers with a heavier bearing for longer life and were able to make the distance on this particular crossing.”
The large drill rig pulled in the pipe within 23 hours.
“We did not have any unexpected challenges,” Baker added, “but the most challenging was the displacement of the mud in the hole as we pulled. The displacement calculated out to 312,000 gallons, and we had pumps and multiple tankers ready to haul this displacement off to our disposal location.”
The pipeline is expected to be in service by the first quarter of 2019.
Successful completion of the project, Baker concluded, goes to Maxi Rig Division Manager Tom Forconi and the two Hard Rock crew leaders, Mario Diaz and J.R. Espinoza; general superintendent Leo Aguirre, as well as to the close coordination and cooperation with Fasken and Kingsley throughout planning and installation.
Based in San Antonio, Hard Rock provides HDD planning, engineering and construction services.
FOR MORE INFORMATION:
Hard Rock Directional Drilling,
(210) 403-2086, hardrockhdd.com
Vermeer Corp., (888) 837-6337, vermeer.com
Comments