October 2016 Vol. 71 No. 10
Rehabilitation
Pre-Chlorinated Pipe Bursting Gives Historical Community New Water
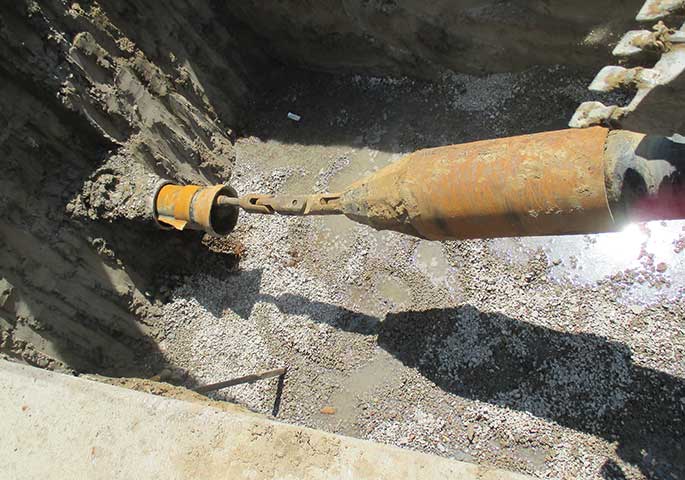
About a 30-minute drive northwest of bustling Detroit lies Bloomfield Village, a distinctively beautiful, nonpolitical entity within Bloomfield Township in Oakland County, MI. Although in size Bloomfield Village covers only about one square mile, its tree-lined streets, lanes and cul-de-sacs provide access to nearly a thousand homes.
The village’s quaint aesthetics are the design of Judson Bradway. When Bradway first established Bloomfield Village in 1924, he wanted to protect its appealing features, controlling its architectural plans and all village maintenance for over 40 years. The suburb’s own residents played a role, forming the Bloomfield Village Protective Association, forerunner of the Bloomfield Village Association, a nonprofit corporation continuing to oversee village maintenance and provide guidance to its residents.
Such devotion toward protecting Bloomfield Village’s charm leaves little wonder why an open-cut technique was ruled out when it came time to replace water mains. Olivia Olsztyn-Budry, Bloomfield Township engineer, said plans for the village’s four- to five-year water service upgrade specified pre-chlorinated pipe bursting replacement.
Some of the mains were the original 6- and 8-inch cast iron pipes laid in the 1920s. Olsztyn-Budry said other underground trenchless replacement methods were considered, such as horizontal drilling, but the pipe bursting technique was most conducive to the limited space available along the street right of ways in the Village. The mains could be accessed and then opened with comparatively minor excavation.
With no rig to position as in the horizontal drilling technique, and working to and from comparatively small access pits, pipe bursting presented the least amount of disruption to residential traffic. Nor would residents’ water service be interrupted except for the single day that work was performed in front of their homes.
Design-bid
The city engaged Hubbell, Roth and Clark to design, bid and administer a plan to replace 44,000 feet of water main. The company is a full-service engineering consulting firm that has served municipal, industrial and private clients for more than 100 years. The firm is recognized for its implementation of industry-leading innovations such as pre-chlorinated pipe bursting. In 2006 the firm designed and administrated the replacement of 23,000 feet of water main and introduced the pre-chlorinated pipe bursting technique to this region with (at that time) the largest project of its kind in the country.
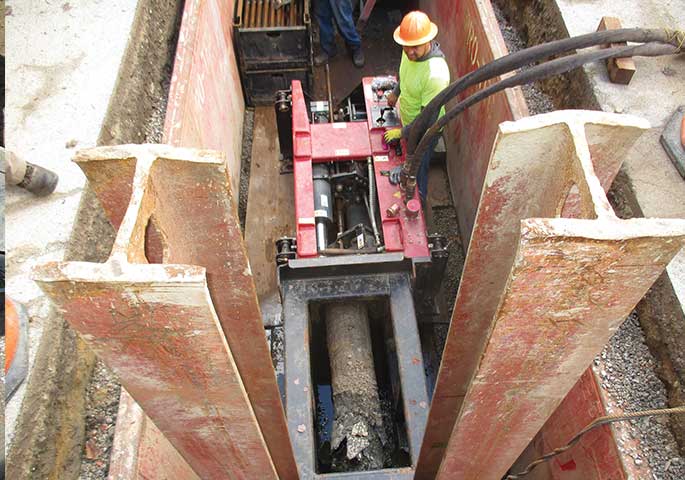
The resulting Hubbell, Roth and Clark project specified pre-chlorinated pipe bursting technique in a four-phase, multi-year replacement schedule to upgrade the existing mains with 8 inch and 12-inch high-density polyethylene pipe (HDPE).
The pre-chlorinated pipe bursting begins on the surface by fusing sections of HDPE pipe to the full length required to complete a run. The fused pipe is pressure tested, chlorinated and tested for bacteria by a state-certified lab. Then it is sealed at both ends, one with an 8-inch pulling head fused onto it in this case, and the other with a fused cap.
The pre-chlorination process can take up to two days of project time prior to installation. Once sealed, the sterilized pipe can remain this way for up to two weeks prior to use in the replacement process, which allows for staging treated pipe in advance of a series of bursts and eliminates the purification process required after reinstatement.
Installation of the pre-chlorinated pipe is based on the static pipe bursting method. Pull rod is fed from a pulling unit through the pipe to the other end, where a bursting assembly is attached. The pre-chlorinated replacement pipe is attached behind the bursting assembly. As the bursting assembly is pulled through the pipe, it will simultaneously fragment the pipe and temporarily enlarge the diameter of the pipe path while drawing the pre-chlorinated pipe into place behind it.
The pre-chlorinated pipe bursting technique significantly reduces the shut-off period and generally eliminates the need for a substitute water supply. In most cases, water customers lose service for less than one workday shift. Residents can expect to have water service while preparing to leave their homes for the day and return home to service that has already been restored.
Pros and cons
James Surhigh, P.E., of Hubbell, Roth and Clark, said that open cut does present some efficiency advantages due to its “production-run style” workflow, compared to the multiple short runs of a pre-chlorinated pipe bursting replacement method. However, those efficiencies are quickly offset by the extensive demolition and restoration that trenching entails. The larger workforce required and greater time spent during the project restoring drives, walkways and landscaping along the entire length of a replaced water main, can make the open cut technique costlier.
“In some cases,” Surhigh said, “there really is no comparison, especially if the replacement run involves historic trees, paver paths, and drives and landscapes of long-established communities like Bloomfield Village.”

While conventional pipe bursting is an improvement, like open cut it also requires the provision of a temporary water supply, an additional cost. The temporary water supply is unappealing to residents for several reasons. Unsightly hoses that lie above the ground must be bridged where they cross drives and landscaping. Traffic also drives over the lines. Since the lines lie exposed to the sun, residents complain of warm water from their taps and are concerned by its “funny smell and taste,” having come from warm, plastic hosing. These conditions last from several days to over a week in some cases until the reinstatement and sterilization processes are completed, tested and approved for use.
In comparison, municipalities have actually remarked to Surhigh how few residents call in during pre-chlorinated pipe bursting projects.
Surhigh said he believes choice of contractor is at least as important as project design. “We have a number of competent contractors we can entrust with our projects. They not only know the technique but run a clean, efficient operation. Contractors we use generally have yards cleaned up and sodded within a week of the installation. Residents do not complain when they see the diligence and professionalism of the installers.”
One trusted installer is pipe bursting specialist Bidigare Contractors Inc. of Northville, MI, chosen for the Bloomfield Village job. Due to the size of the project, Bidigare expanded its workforce in a joint venture with D’Angelo Bros Utilities of Farmington Hills, MI.
Bursting begins
For bursting operations, Bidigare used its own hydraulic pipe bursting machine from the HammerHead Trenchless Hydroburst line of equipment. Although the machine was capable of up to 100 tons of pulling force, John Bidigare, vice president of Bidigare Contractors, said the average burst required only about 20 tons.
The Bloomfield Village project launched with three primary objectives: replace undersized and historic water mains, replace and upgrade fire hydrants to improve coverage, and replace and add water system valves for more reliable water system operation. It was designed to take place in four phases.
The various sections of Bloomfield Village’s legacy water system ranged in age from 46 to 89 years old. The newest additions to the 11 miles of ductile iron pipe, valves and hydrants, were installed in 1968.
Most bursting involved 8 on-8-inch replacement of ductile iron pipe with HDPE, with some sections of 6-inch ductile iron to be upgraded to 8-inch HDPE.
Prior to each burst, Bloomfield Village utilities were located and flagged. Residents received 24-hour notification of when they would lose water service, which usually lasted 8 to 12 hours.
Each evening prior to bursting operations, the crew prepared two 5 by-10-foot access pits, 5 to 6 feet deep. One would serve as a working pit with the pulling machine in it, and the other as the replacement pipe entry pit where the bursting run would begin.
During a typical 10- to 12-hour shift that included a pipe bursting run, the burst itself took between two and three hours to perform.
Pull rod was paid out from the HydroBurst through the existing pipe to the entry pit. There, a flex joint connected the pull rod to a pulling head nestled inside a hollow body expander. Typically 25 percent larger than a pipe’s nominal diameter, an expander’s function is to fracture the existing pipe and press it away from the pipe path, leaving sufficient room for the pulling head and replacement pipe. For the 8-inch HDPE in this application, the expander was 10 inches in diameter. The replacement pipe, which was fused directly to the pulling head, was drawn along behind the pulling head as the assembly progressed.
Once in place, crews flushed the pipe, re-attached the residential service to the main and activated the water system. Other than the access pits, the only other landscape affected was a 3- by 3-foot pit to access the water service shutoff valve. Although pipes had been sterilized, residents were advised by the city to boil drinking water during the next day or two, waiting for a certified laboratory to confirm the water was within regulatory guidelines.
Bidigare Contractors replaced between 200 and 500 feet of pipe a day using this method, and began replacing the 17,000 feet of Phase I pipe in October 2013, completing the first 3,000 feet, as scheduled, before shutting down for winter in November. The number of lines included as part of Phase I were increased, since pipe bursting operations were running ahead of schedule. Phase I replacement work was completed in 2014, Phase II in 2015 and Phase III in 2016.
Bidigare is on schedule for completion of the project in 2017.
FOR MORE INFORMATION:
Bidigare Contractors
(248) 735-1113, bidigarecontractors.com
HammerHead
(800) 331-6653, www.hammerheadmole.com
Hubbell, Roth and Clark
(248) 454-6300, hrc-engr.com
Comments