July 2016, Vol. 71 No. 7
Rehabilitation
Team Of Experts, Equipment Needed For Pump Station Rehab
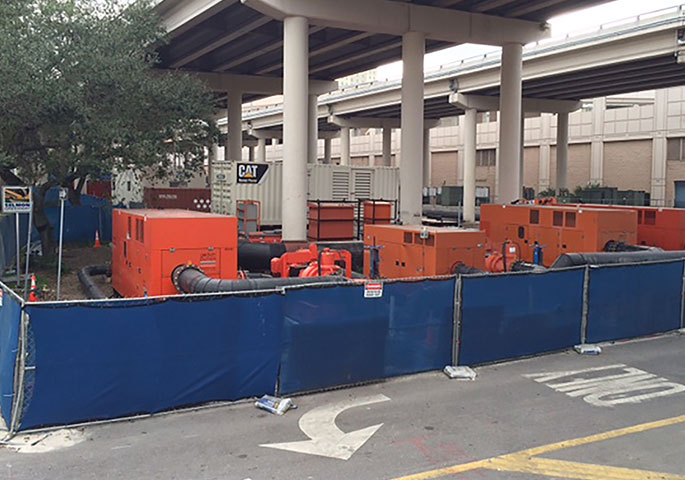
Bypass At Its Best
By Hunter Powell Senior Applications Engineer, Southeast Region, Xylem Dewatering
The Wastewater Department of the city of Tampa, FL, is responsible for the collection, treatment and disposal of more than 55 million gallons of wastewater per day (mgd) from more than 100,000 customers in Tampa and the surrounding suburbs. Central to the operation is an advanced wastewater treatment plant with a capacity of 96 mgd. The department also operates and maintains the complex maze of sophisticated infrastructure that feeds into the plant, including about 1,800 miles of gravity and force main sewer lines, 225 pumping stations, 30,000 manholes and 667 air release valves.
As part of the Wastewater Department’s proactive maintenance program, it was determined that the Krause Pump Station (built almost 40 years ago) had exceeded its designed life expectancy and was in need of rehabilitation. The local contractor, Vogel Bros. Building Co. and the pump experts at Xylem, were brought in to assess the project, design a robust bypass plan and implement the bypass while the station was being rebuilt.
“We were thrilled to get the pump station project as our experience with wastewater and industrial projects aligned perfectly,” said Darren Vogel, PE, project manager at Vogel Bros. “And we knew our relationship with Xylem would pay off, as they are pump rental and dewatering experts.”
No room for error
The average daily flow at the Krause Pump Station is 20 mgd. But over the years, there had been wet weather spikes to greater than 50 mgd. To ensure that the bypass was robust and could handle any amount of anticipated flow rate, the specifications and design plan called for a system capable of handling a 100-year storm event, or 64 mgd.
To implement the bypass, the design incorporated the use of four manholes: two of them in the middle of downtown Tampa under the expressway, and two of them along the Hillsborough River. These locations had very little room for the bypass equipment. To complicate the project further, a request to the city for a complete road closure was denied, so the placement of the pumps and bypass equipment had to be done in such a way that traffic would not be hindered.
In order to ensure that the bypass would be operable and could handle the flow, redundancies were put in place as part of the plan.
“The last thing we wanted to do,” continued Vogel, “was to have a sanitary sewer overflow event at some point while the bypass was in place. We took every precaution and incorporated back-up equipment into the system, just in case.”
As primary equipment for the bypass, the plan called for three Godwin electric CD400M Dri-Prime pumps, one Godwin electric DPC300 pump and a Godwin electric CD150M pump. The electric pumps were all tied in to a generator, as a back-up in case of a power outage. A bank of seven Godwin diesel pumps, equipped with fuel cubes, was also put in place for complete redundancy of the bypass.
Getting it done right
A typical solution to moving pumps and oversized equipment into place on a job site is with a crane. But since the primary location was under the expressway and a crane couldn’t fit in the work space, Xylem used a rotator extender truck with a telescoping boom to place the equipment where it needed to be on site.
Once in place, each of the primary electric pumps was installed with a Godwin Variable Frequency Drive (VFD), to adjust pump speed for optimal efficiency and to save energy costs. The pumps were integrated together to work sequentially, with each pump activated only as increased levels in the wet well – identified by Godwin level transducers – called for additional pump activity.
Since the bypass was situated in a busy traffic area under an expressway, space had to be optimized as much as possible. With the city not eager to close a busy road for an extended period of time, the plan also called for the use of tapping saddles on the main trunk bypass line. This saved enough room to be able to keep one lane of traffic open for the duration of the bypass project.
“The team at Xylem pulled together a terrific bypass solution. It was efficient, redundant and they brought in the right rental pumps for the job,” Said Vogel. “The City of Tampa was very happy with the outcome. The bypass put their mind at ease, and allowed them to focus on getting the Krause Pump Station rehab completed in a timely manner. It was a win-win for everyone.”
ABOUT THE AUTHOR: Hunter Powell is the senior applications engineer for the Southeast region for Xylem Dewatering. He can be reached at hunter.powell@xyleminc.com.
FOR MORE INFORMATION:
Xylem,
914-323-5700, www.xylem.com
Godwin Pumps,
(856) 467-3636, www.godwinpumps.com
Comments