July 2016, Vol. 71 No. 7
Features
2nd In A Series: Building A Culture Of Construction Safety
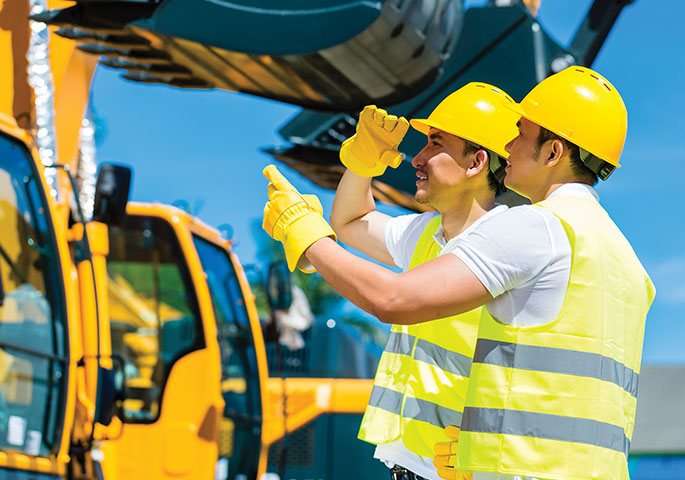
by Jeff Griffin Senior Editor
Working in construction carries potential dangers, and the level of danger varies with the type of work being performed – certainly underground construction poses risks specific to that industry.
No one wants to get hurt, and owners and managers of construction firms want to keep their workers from harm. Yet, safety records clearly show that some organizations do a better job than others when it comes to implementing safety efforts that significantly reduce accidents.
Establishing safety practices, training, and rewards for accident- free work are a few basic steps most companies use. So why do employees of some companies post better safety records than others?
The answer seems to be that the safest construction organizations have developed a culture of safety.
What is a safety culture? How is it developed? Why is it essential?
This second in a series of articles on the topic shares input from representatives of two underground construction companies with enviable records of safety: Matt Ory, director, safety and health, ElectriCom Inc.; and Butch Magers, safety director, Kenneth G. Myers Construction (KGM). (See first installment: DCA Safety Award, Buiding a Culture of Safety)
How do you define “safety culture” as it applies to your organization?
Ory, ElectriCom Inc.– A safety culture represents a company-wide effort to help reduce workplace incidents and injuries. Participation is needed from every employee at every level – top to bottom – within the company to accomplish this. Every employee must know his or her role and what’s expected regarding safety and health. Accountability is a big key to achieving a culture of safety excellence.
Magers, KGM, Magers – Safety culture is the attitude and awareness shared among all employees – from the company president, to the equipment operator with 40 years of experience and newest laborer – that, just like the stickers on the company vehicles proclaim, “Safety is First.”
What is the first step in creating such a culture?
Ory, ElectriCom – The senior management team must take the first step. A commitment to the cause must be demonstrated. The president of our organization has developed a Safety & Health Mission Statement. This statement demonstrates his commitment and his role in the safety and health process within our organization. It states that: “It is my responsibility as president to promote and ensure the safety of our workplace…”
Magers, KGM – New employees begin their career with safety orientation; an introduction of industry hazards; and discussion and training in identifying work hazards, eliminating hazards, and safe procedures and practices in dealing with hazards. During this orientation, the seed for the Safety First culture is planted and fertilized with the knowledge that although each employee is primarily responsible for his own safety, the entire company stands beside him or her in safe work practices. From the beginning, every employee is encouraged to speak up and never look the other way when dealing with safety.
Can a small- or medium-sized organization create and implement a safety program, or do outside experts need to be involved?
Ory, ElectriCom – Any organization can create and implement a safety program. However, I strongly believe that a true safety professional is needed to create, implement and
facilitate an effective safety process.
Magers, KGM – Yes, with today’s deep well of information available through the internet in text, pictures and video, it is very possible. There are tons of useful websites to choose from. We recently completely revised and overhauled our safety manual which originated in 1994. We did this completely in house and are proud of the finished product. That said, we are always open to any outside influence or expert who can help us perform our work safely.
How does a formalized safety program fit into building a safety culture?
Ory, ElectriCom – A successful safety program will detail the operations, guidelines, policies, best practices and expectations for employees at all levels. It’s important that the safety program within any organization is not viewed solely as a binder that sits on the safety director’s desk. It should be viewed more as a process. It must be developed, reviewed and amended as needed. Employees should be able to participate in this process.
Magers, KGM – In many ways, the safety program and the safety culture build each other. They feed each other and grow together. The program involves 6 a.m. safety meetings, and the culture grows from these meetings when new employees see the company president right beside them at 6 in the morning, talking about safety. The culture feeds the program when employees are empowered to bring new products and ideas forward, and introduce them to the safety program.
What part does training play? How important is continuing, regular training?
Ory, ElectriCom – Training is one of the most important elements of any safety and health program. Training enables employees to learn their jobs properly and reinforces safety policies and procedures. Safety training also provides an opportunity to effectively communicate safety principles and management’s commitment to safety. Progress through various craft and technical job levels depends largely on the safety training that the employee receives on the job. It is necessary to instruct employees in doing all phases of their jobs in a safe manner to enable them to advance within their profession. Employees found deficient in the necessary skills to perform their job safely must be recognized, re-trained, reclassified or released.
Magers, KGM – After safety orientation comes on the job training, which begins when a new worker is introduced to a veteran foreman. The foreman is given specific instructions to show the new employee the right way to do the work. This practice puts a lot of responsibility on the foremen and veteran crew members, but company management is right there aiding the training process and monitoring it with onsite inspections and consultations. Regular and refresher training is important, and is executed with monthly safety meetings, weekly safety handouts along with quizzes, and daily job briefings. We also take advantage of Ohio BWC safety training classes, and local safety council meetings and seminars.
How does management “sell” safety to its employees?
Ory, ElectriCom – Within our organization, it’s important that management “walk the walk.” Our management teams are just as involved – if not more so – in the company safety process as any employee. Besides allocating time, money and resources, they also are involved in the day-to-day operations. Our management team members attend regular safety meetings, conduct field safety observations, participate in accident investigations, and develop regular safety and health related communications for employee distribution. This sends a very important message that the responsibility for safety is not limited to the safety department.
Magers, KGM – The company president and top management standing in front of the employees on a Monday morning at 6 a.m. and reinforcing the Safety First ideal sells the safety program very well. Management backing up a crew after the crew refuses to complete or start a project due to safety issues beyond company control puts these words into action. These are the actions that sell the safety program and culture.
Does recognition of safety achievements encourage safety?
Ory, ElectriCom – We believe it does encourage and promote safety. It also provides transparency. I produce a monthly Safety Performance Report which provides a “snapshot” of all things relating to safety at our company. It details several categories, including number of safety observations conducted by the safety department, number of safety observations conducted by management, average score of the safety observations out in the field, number of recordable incidents, safety statistics, short-term goals, long-term goals, breakdown of monthly safety observations (non-compliant findings), and a summary of the monthly safety committee meeting. It is important that everyone is on the same page when it comes to safety and health. We need to know where we are and where we’re going, and this report serves as a safety scorecard for the company.
Magers, KGM – Safety performance is recognized verbally at monthly safety meetings. Any injuries or near misses are documented and discussed so they might be avoided in the future. As of now, awards are not part of the program, in order to avoid non-reporting of incidents.
How can employees at every level be encouraged to be responsible for safety?
Ory, ElectriCom – Buy-in is critical to any successful safety and health process. Employees should feel motivated and empowered to participate in that process. Employee-run safety committees are a great starting point and a great tool for safety communication. Most of the discussion is centered around field-related safety issues. The committee also is a liaison between the field and management. Employees at all levels have the ability to provide insight on field safety issues, recommend policy changes, attend safety and health training sessions, and interact frequently with the safety department and members of the management team.
Magers, KGM – From the first orientation, it is instilled into employees that they are Number One. That is, they are the primary person responsible for their own safety. The safety director, company president, even their foreman, will not be with them every moment of every day; only the employee can control each movement, each action and each thought. Employees are directed to speak up and be part of the safety solution, and never look the other way. The first hand-signal taught to new employees is the all stop signal and this empowers even the newest employee to bring a stop to a bad situation.
How can a safety program evolve with changing needs?
Ory, ElectriCom – After implementing any safety and health initiative, there must be a review process. Is it working? If so, what can we do to ensure continuing success? If not, what can we do to achieve the desired results? A main function of a safety professional is to stay current with all federal, state, and industry rules and regulations. Communication and transparency are important to ensure the successful evolution of any safety and health policy. Never forget the employees. There is a wealth of internal knowledge just waiting to be tapped.
Magers, KGM – Communication. Crews need to communicate to safety management about things they are seeing in the field. Maybe they have noticed another company using a new product or a new procedure. Conversely, safety management needs to keep the crews advised of any developments in safety and any changes in safety standards.
What are the most common mistakes management makes in attempting to develop a culture
of safety?
Ory, ElectriCom – Common mistakes are:
- Not realizing that it all starts inside the company and must come from the top down.
- Setting unrealistic safety and health goals.
- Too much focus on Safety Statistical Results (Incident rate, DART rate, EMR).
- Too much emphasis on lagging indicators versus leading
indicators. - Dangerous safety incentive programs. For example, incentive programs based on a single measure, such as number of accidents, can create a culture of under reporting which can become potentially dangerous.
Magers, KGM – There are times when we do not pay enough attention to the newer employee. Younger crew members sometimes can feel ignored by management. Sometimes, only the foreman’s point of view is taken into consideration. It’s very possible to miss out on some great fresh ideas from younger
employees.
How would you describe your organization’s safety culture? How is it being sustained?
Ory, ElectriCom – ElectriCom’s safety culture is built on the principals of participation, knowledge, transparency and accountability. Employees at all levels are encouraged to participate in the safety and health process. Our employee-run safety committee is a great vehicle for involvement. Training is one of the most important elements to building and sustaining our safety culture. As previously mentioned, training is designed to enable employees to learn their jobs properly, and reinforce safety policies and procedures. Transparency is vital. The Safety & Health Process at ElectriCom belongs to all involved. If a policy change needs to be made, everyone must be included in the process, from the draft to implementation. Lastly, but certainly not the least important, is accountability. Failing to hold ourselves and others accountable for safety and health related issues sends the message that safety is not important.
Magers, KGM – Like the fiber optic cables we install, our safety culture is bidirectional. That is, our safety culture is sustained through communications from both directions – from the company president to the newest employee, and from the newest employee to the company president – with all of our employees representing a point of information scattered throughout our safety communication path.
FOR MORE INFORMATION:
ElectriCom
800-483-5941, www.electricominc.com
Kenneth G. Meyers Construction
419-639-2051, www.kgmyers.com
Comments