January 2016 Vol. 71 No. 1
New Products
Saginaw Sewer Excavation Proves Tricky

The challenge for American was the need to excavate and expose both pipes which run parallel but at slightly different grades,
then set up a system to support the concrete lines in order to dig out below the inverse of both pipes, and finally cast-in-place a new bypass junction chamber tying the two lines together. Of course, American needed to safely shore a pit that would encompass all of the above.
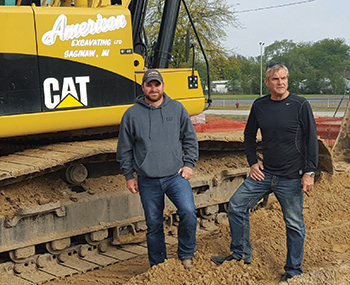
Selecting the correct shoring system is no easy task. “There were a couple of factors we needed to consider when looking for a shoring system,” said Zac Birnbaum, American Excavating’s project manager.
“We knew the excavation was going to be open for a while, so trench boxes would not be the best choice,” said Birnbaum. “Also, the excavation was in the middle of a road and according to the city (of Saginaw), needed to be ‘dirt tight’ so over-excavating the hole wasn’t a possibility.
“We considered sheeting, but that would require us to take out both the 60 and 90 inch sewers and use bypass pumps the whole time which would increase the cost of the project dramatically,” continued Birnbaum. “Instead we went with an Efficiency Production Slide Rail System because we could use panel guides and short lengths of KD-6 sheeting to tightly shore around both of the big pipes, without having to remove them.”
“Really, Efficiency’s Slide Rail System was just more cost effective than sheeting,” he concluded.
Perfect solution
Efficiency’s Universal Slide Rail is a component shoring system comprised of steel panels and vertical steel posts. The highly versatile system can be used in a variety of configurations. Efficiency’s Slide Rail System can be configured into small four-sided pits; an obstruction-free ClearSpan configuration; or in a Multi-Bay configuration to install large tanks and structures or lengths of pipe over 40 feet.
With the trench protection system decided, Birnbaum’s next call was to Efficiency Production’s Special Operations Shoring Division. Rod Austin, Efficiency’s senior slide rail installer and shoring specialist (now the company’s vice president of sales) took Birnbaum’s call. “Zac sent me the prints to figure out how we could shore the hole without shutting down the two sewer lines,” Austin explained. “I knew we could do it with Slide Rail by incorporating our Shore-Trak Panel Guides to shore around both pipes as they passed through the excavation.”
Slide Rail is installed by sliding the steel panels – similar to trench shield sidewalls – into integrated rails on the vertical posts, and then pushing the panels and posts incrementally down to grade as the pit is dug, a process commonly referred to as a “dig and push” shoring system. Efficiency’s Panel Guides replace the Slide Rail panels that slide down the open-faced inside rails on the posts. That allowed American to place short lengths of KD-6 sheeting and a few road plates through the 7-inch slot in the panel guides to tightly shore around the existing sewer lines on both ends. Panel guides are an exclusive feature of Efficiency Production’s Slide Rail System.
With equipment rented factory-direct from Efficiency Production’s manufacturing headquarters in Mason, MI, and with Tim Hurst, shoring specialist in Efficiency’s “Special Ops” Division on-site to offer installation assistance, American’s crew installed a two-bay, 4-Sided Multi-Bay configured Slide Rail System.
The total dimensions of the shoring system were 26-feet wide, 41-feet long and 24-feet deep. Multi-Bay utilizes Efficiency’s exclusive parallel beams that roll up and down the slotted rail on the inside face of the linear posts and have spreader collars which pin standard trench box spreaders for cross-trench support.
All told, it took American just two months to cast-in-place the approximately 30-foot long, 10-foot wide and 10-feet tall bypass junction chamber, plus two, 10-foot tall personnel-access chimneys.
American Excavating’s heavy equipment on the $280,000 project was a 345D CAT excavator, a 950G CAT front-end loader and a 320C CAT excavator with hoepack for compaction.
Saginaw-based American Excavating was founded in 1990 by Steve Birnbaum. In the construction business for more than 30 years, Steve got his start working for his father and uncle, Fritz and Al Birnbaum, at Valley Asphalt which is now part of Saginaw-Ace Paving. Steve’s son, Zac Birnbaum, joined American Excavating in 2004.
Efficiency Production, Inc., “America’s Trench Box Builder,” provides the widest selection of standard and custom trench shielding and shoring systems in the industry. Efficiency’s versatile products are designed specifically for safe and cost effective installation of utility systems and infrastructure improvements.
FOR MORE INFORMATION:
Efficiency Productions Inc.
800-552-8800, www.efficiencyproduction.com
Comments