February 2016, Vol. 71 No. 2
Features
Culvert Replacement Project Beneath Famed Pacific Coast Highway
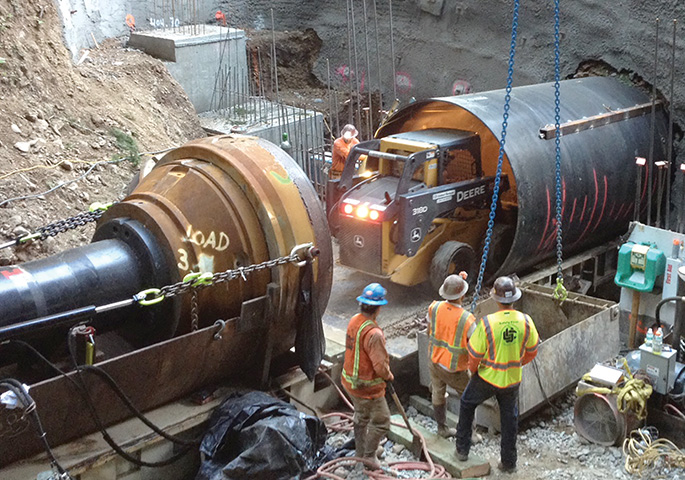
Pipe Ramming Tool ‘Swallows’ 48” Culvert Beneath Highway in Jenner, CA
A failed 48-inch-diameter culvert at mile marker 29.9 north of Jenner, CA, had been causing periodic flooding from rain water runoff. Jenner lies on the heavily trafficked, 147-mile-long thoroughfare along the scenic California coastline known as the Pacific Coast Highway. In addition to heavy traffic to and from large metropolitan areas along the route to the south such as San Francisco and Los Angeles, the road is a popular tourist route due to its coastal views and seaside attractions.
Laid in a creek channel over shale rock prior to construction of the roadway overlying it, the existing four-foot-wide culvert had been overdue for replacement for perhaps decades. Age and years of logs and debris washing down the hillside, repeatedly battering against its mouth and continual exposure to flooding had taken a heavy toll. Much of its invert had eroded away.
To ensure a replacement culvert would not face the same abuse, the California Department of Transportation (Caltrans) opted to widen the culvert’s diameter to 9 feet, which would allow almost anything washing down the hill to pass through it. The Caltrans project plan specified pipe ramming technique.
The culvert replacement project design was a joint effort between Caltrans Districts 6 and 4 in consultation with WRECO and Bennett Trenchless Engineers. The pipe ramming portion of this project was the job of Drill Tech Drilling & Shoring Inc. Having a northern office in Antioch, CA, and southern office in Corona, Drill Tech Drilling & Shoring specializes in geotechnical construction such as earth retention, foundation support, tunneling, shaft construction, ground treatment, dewatering and architectural shotcrete.
Bigger better
Although pipe diameters over 120 inches have been successfully rammed with smaller ramming tools, Drill Tech chose this project as a test of the world’s largest pipe ramming tool, a 34-inch hammer by HammerHead Trenchless Equipment of Lake Mills, WI, due to concerns posed by the shale rock under the invert.
Desmond Blake, Drill Tech’s professional engineer, calculated ramming requirements with consultation from HammerHead’s Brian Cowles, southeastern and western U.S. sales manager. Cowles explained the requirements: “The jobsite was dense, California redwood forest. The outfall immediately terminates in the Pacific Ocean at one of the most pristine, protected abalone-filled coastline sites in the state. Trees, soils, rocks and moss-covered stumps had to be carefully protected during the project. Precise planning and execution were critical.”
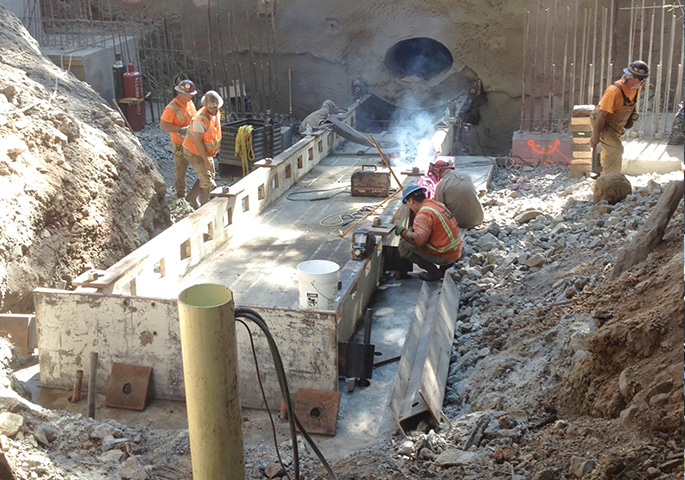
Work space was limited to the road right-of-way and the construction easement’s small footprint. Upstream encroachment was not permissible, and working from the outfall side was not possible due to topography. Materials could not be staged at the site due to these space limitations. Every piece of equipment and each section of pipe were trucked to the site as they were needed. A timed stoplight limited interruptions to traffic to no longer than 10 minutes, which required precisely coordinated movement of machines and equipment each time one was off-loaded or moved.
It took a full week of excavation, building a dam to divert the creek and installing a 25-foot-tall shoring system to retain the road embankment and install a headwall footing before pouring the concrete slab for ramming operations. The 40-foot-long by 12-foot-wide concrete slab was designed to support a 45,000-pound jacking sled, each 28,000-pound section of pipe and the 27,500-pound ramming tool. It was allowed to cure four days prior to installing the hydraulic jack, jacking frame and anchors, as well as the pipe ramming support rails. Since the creek provided no room to build a proper backstop for the hydraulic jack, the pad design included tie-backs in the face and micropile anchors in the sides and back to prevent the pad from shifting during the ram.
The 34-inch ramming tool chosen for the job is rated for maximum operation at 4,700 cfm of compressed air at 110 psi. On this job, three 1,600 cfm compressors were linked through a common manifold to provide air capacity up to 4,800 cfm for the ramming tool.
Additional tooling consisted of a 34-inch rammer and a 48-inch collet with 72-inch and 96-inch drive cones and split rings to attach to the 108-inch-diameter pipe.
Custom equipment
In addition to the 34-inch ramming tool, a custom-built pipe jacking system provided up to 500,000 force pounds of static thrust to counter swim. The jack applied force through a semi-circular thrusting plate contacting the bottom half of the pipe through the ramming cone assembly.
Nine people were on hand during the ramming operation. The crew included a project supervisor, crane operator, safety person, jack operator, ramming tool operator, four welders and at times additional laborers. Robert Hordyk, project superintendent, said “the hammer worked beautifully. Between the hydraulics and that hammer, we were going to go through anything.”
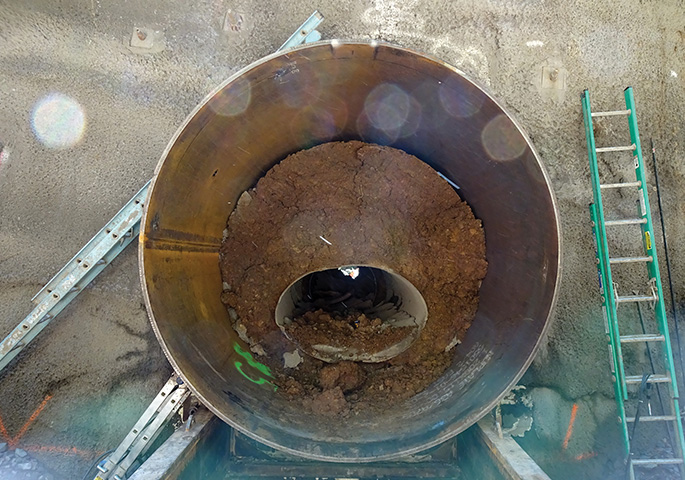
Maximum static thrust provided during the ram by the hydraulic jack was never more than 400,000 pounds. Drill Tech observed that the jacking system alone was nearly sufficient to install the first stick in the saturated embankment. Installation of the first piece had taken just 45 minutes. Ramming operations paused for spoil cleanout after the third piece was in place to reduce wear and tear on the jacking sled system and pipe.
Joint-welding after each section was installed took four welders 10½ to 12 hours each after pulling the ramming tool back, removing the collets and setting and aligning new section of pipe. The last of the five sections took only 90 minutes to ram in place, completing the
88-foot run.
In spite of rains that caused interruptions of the project, ramming operations took about two weeks and were completed by Sept. 26. At least one lane of traffic was kept open at all times, with minimal delays to traffic.
The finished pipe run was within a half percent – or 6 inches – of the 9½ percent grade specified in the plan, well inside the 1 percent tolerance of 12 inches.
Since the successful demonstration of the pipe swallowing technique at this difficult and environmentally sensitive location, Caltrans may now be considering other projects for use of the 34-inch HammerHead pipe ramming tool.
FOR MORE INFORMATION:
HammerHead Trenchless Equipment
(800) 331-6653, www.hammerheadmole.com
Drill Tech Drilling & Shoring Inc.
(925) 978-2060/(951) 277-9700,
www.drilltechdrilling.com
Comments