September 2015 Vol. 70 No. 9
Features
HDD Units Updated To Match Customer Needs

The first compact horizontal directional drilling (HDD) machine developed specifically for utility applications carried the Ditch Witch® name.
The year was 1987 and this first model, introduced at an industry trade show, was mounted on skids and had to be lowered into a pit to begin drilling at the specified depth. The tethered power pack remained on the surface. Very soon it was replaced with a model on wheels, manually pushed into position; the power source remained separate, tracking electronics had not yet been developed and available utility locators were used to monitor location of the bore head.
With the Ditch Witch organization leading the way, HDD technology advanced quickly. Drill units became self-contained with onboard power sources. Drill pipe, downhole tools and electronic tracking systems were developed specifically for directional drilling.
Today there are Ditch Witch HDD models ranging from 5,000 to 100,000 pounds of pullback, with three All Terrain (AT) models with a mechanical drilling system for drilling through rock (see chart on page 4 listing models and basic specifications).
“The Ditch Witch HDD product focus remains on equipment for multiple markets, including communications, electrical power and natural gas distribution, water and wastewater, and energy pipelines, including gas transmission, and gathering lines at oil and gas well sites” said Product Manager Seth Matthesen. “HDD contractors today want HDD equipment with features that improve uptime and add to efficiency and productivity.”
Much of the utility work demands compact, powerful equipment used for broadband expansion in established neighborhoods and business districts, Matthesen explained. In fact, HDD is the preferred method of installation on many broadband deployments today. Small- to mid-size models also are installing electrical distribution cable and natural gas lines. HDD also is widely used to install water and sanitary sewer pipeline infrastructure.
“Our business philosophy always has been to develop products the market and our customers need,” Matthesen said. “If we help our customers succeed with the quality equipment we provide, our company’s success follows. Essentially, we and our customers are in business together.”
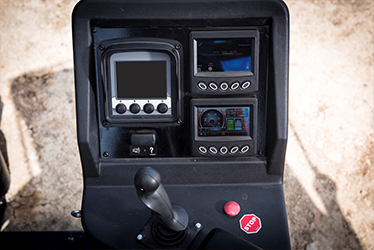
Updates
Among the most significant recent developments in the Ditch Witch® HDD lineup are heavy-duty anchor systems, open-top vise wrenches and an integrated remote display. Controls and operator interfaces are more intuitive. Downhole tools have steadily improved. The addition of the 66-horsepower JT9 provides a powerful compact model, not much larger than the JT5, but with more power.
Tier 4 engines are available for all drill models except the JT60 and JT100, and they will be ready the first of the year.
“This is an important step forward,” Matthesen said. “Adding Tier 4 is not just bolting in a different engine, but requires significant redesigns and many compatible components. Tier 4 engines are important because they improve the environment and in some areas equipment with non-compliant power sources will not be allowed on job sites.”
New Power Pipe® HD drill pipe is available in lined, unlined and forged versions. The SaverLok® System is the most advanced saver sub available providing the tightest connection and best protection against wear and tear on drill pipe and the drill unit’s drive system. A new line of heavy-duty reamers provide enhanced productivity and durability.
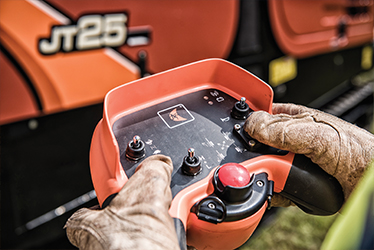
All Terrain offer the optional wireless ground drive control.
An optional wireless ground drive control has been introduced as an option on the JT25, JT30 and JT30 AT models, eliminating the tether needed for other handheld remote controls, improving visibility and operation.
CAN (Controller Area Network) systems that allow micro controllers to communicate with other components have been integrated into many models to control and monitor equipment performance.
ATs tackle rock
The proven Ditch Witch All Terrain (AT) system extends the ability of mid-size HDD equipment to effectively bore through rock without a mud motor, said Matthesen. AT systems use a mechanical, dual-pipe drilling system with an inner rod to drive a rock bit, and the outer pipe to steer the downhole tool while drilling the pilot holes and provide rotary torque for the hole opener during backreaming. They deliver maximum available power to the downhole tool and enable simultaneous drilling and steering through various mixed soil conditions and rock. AT equipment requires no more drilling fluid than conventional equipment.
In addition, said Matthesen, maintenance has been simplified across the line by making service points more accessible and, of course, the Ditch Witch dealer organization has a ready inventory of parts and provides unmatched repair service.
“Our company,” Matthesen concluded, “has a tradition of being first with new underground construction products: the world’s first compact trencher, first vibratory plow, and first with backhoe and combination trencher/vibratory plow attachments.
“We were the first, and still are the only company, to take a systems approach to design and manufacturing of directional drilling equipment – making not only the drill rig, but pipe, downhole tools and electronic guidance systems, providing reliable and productive equipment that meet the needs of the marketplace – some of the important ways that Ditch Witch products stand apart from other brands.”
Comments