November 2015 Vol. 70 No. 11
Features
Understanding Native Flowable Fill
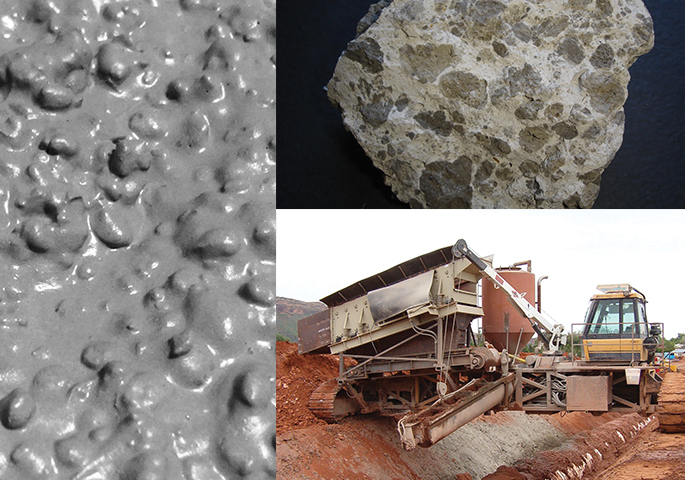
Some contractors are making native flowable fill using the existing soils excavated from the trench for pipeline embedment and backfill.
Native flowable fill can be both economical and environmentally friendly. The savings result from less excavation, material handling and labor costs. Reuse of soil excavated from the trench means no hauling in imported material and less spoil disposal.
Flowable fill is a mixture of soil, cementitious matter and water that hardens into a material stiffer than compacted soil. It is typically placed as a self-leveling slurry. Flowable fill is also known as CLSM and CDF, among other terms.
The soil used to make flowable fill can vary from standard ASTM or AASHTO aggregates to clay excavated from the trench. Based on the source and type of soil used, the slurry can be described as either:
- Imported flowable fill; or
- Native flowable fill.
Imported flowable fill uses off-site processed materials as the soil ingredient in the mixture.
Native flowable fill uses the existing materials that are excavated from the trench for the soil component. Native soils from the vicinity could also be used.
The main requirements for flowable fill are strength and flowability. For pipeline use, the compressive strength need only be 40 to 80 psi. This strength is appropriate because the hardened flowable fill needs to be easily excavated for pipe repairs and for new pipelines in the vicinity. The material should flow easily into all voids around and under the pipe making intimate contact with the existing soils.
Native soils that are sands or a mixture of sand and silt are ideal for flowable fill. The soil is easily processed and mixed. Clayey soils typically require more processing than sandy soils, but have successfully been used in pipeline construction. Clay soils require shredding so that the clay clods are about ½ inch to 1 inch in diameter.
Mixing
Different equipment set-ups have been used for mixing native flowable fill. Trench side mixing refers to using equipment that travels beside the trench to mix the soil, cement and water, and then discharge the flowable fill directly into the trench. Volumetric mixers have been used in trench side mixing. Portable batch plants are mobile and can be set up near the trench and moved along the alignment as the construction progresses. Soil from the trench is stockpiled next to the batch plant, screened if necessary, and batched on a weight basis similar to ready-mix concrete. Transit mix trucks transport the material to the trench site. Portable mixing plants, similar to volumetric mixers, have also been used.
A fresh mixture of native flowable fill containing clay clods is shown in Figure 1. A photo of hardened native flowable fill made using clay clods is shown in Figure 2.
Some contractors have developed trench side mixer operations. Typically, the equipment travels down the side of the trench, mixing and placing as it goes. One of these trench side mixers is shown in Figure 3. This is a volumetric mixing procedure. Soil from the hopper goes onto a conveyor belt to a mixing chamber at the beginning of a screw auger. Concurrently, cement and water are added to the mixing chamber. The material continues to mix as the screw auger moves the material down the chute. The flowable fill goes directly into the trench and around the pipe.
Volumetric concrete mixers are also used in a trench side operation. As the mixer moves alongside the trench, the spoil soil is being continuously fed into the soil hopper. The screw auger does the mixing. This procedure has been used successfully with sandy soils (SP, SP-SM, SP-SC, SM), some clayey soils (SC, CL), but is not effective with fat clays (CH).
Fat clays
One innovative operation is able to process and mix fat clay soils. These highly plastic clays are difficult to work with, but this equipment has successfully used the soil to make flowable fill. The soil from the hopper is fed into a pug mill via a conveyor belt. Cement is added to the soil on the belt with a vane feeder. Water is introduced at the beginning of the pug mill. The operation can successfully mix fat clay soils because of the action of the pug mill.
Another unique method for treating fat clay or other wet, sticky soils, is to modify the clay with lime to dry it out and to reduce the plasticity. After setting for a day or so, the modified material is ready to use to make flowable fill.
More about the procedure and the rigs are shown in the Technical Note Flowable Fill Using In-Situ Soils at www.pipeline-installation.com. On this same website, there are also some links to videos showing many of the trench side operations. There is also a bibliography of articles and papers regarding native flowable fill available on the download page.
The use of native flowable fill is growing and becoming more acceptable every day. Contractors are winning bids using the native flowable fill option. Using the soil excavated from the trench reduces spoil pile waste, spoil pile handling, importing aggregate materials and transit mixer truck traffic from ready-mix plants. Besides being economical, native flowable fill benefits the environment.
ABOUT THE AUTHOR: Amster Howard is a civil engineering consultant from Lakewood CO. This article is based on an excerpt from his book Pipeline Installation 2.0.
For more information go to
Pipeline-Installation.com
Comments