March 2015, Vol. 70, No. 3
Features
HDD Rigs: More Power In A Small Footprint
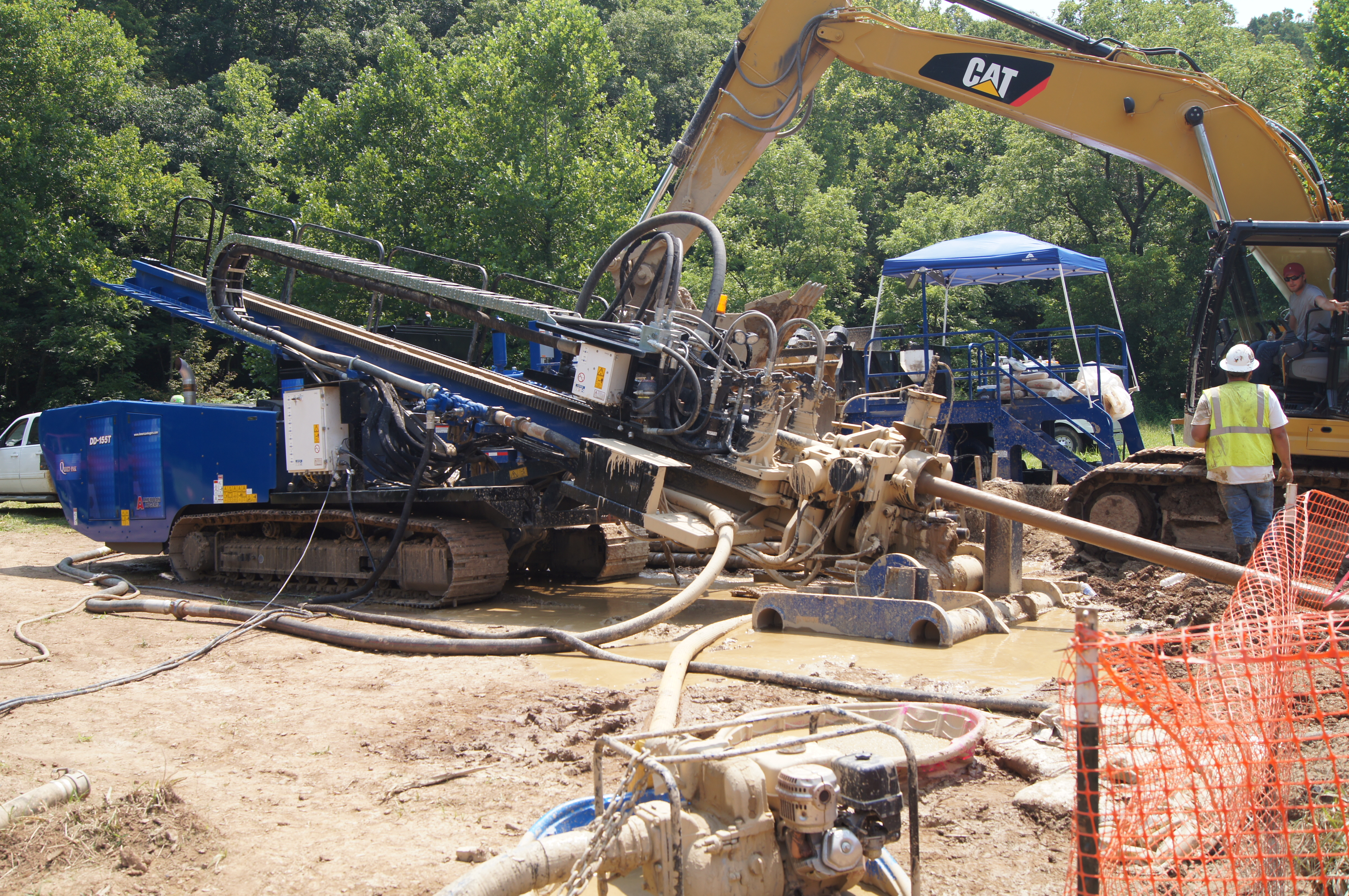
With construction equipment, sometimes big can be better by bringing more power and more productivity.
However, for some projects big can be too big. If a machine is too large to fit in available work space, benefits of more power and increased productivity are lost.
An ideal solution is to pack big power in smaller packages and that’s an ongoing trend that applies to horizontal directional drilling (HDD) equipment, as well as trenchers, excavators and other equipment used for underground construction.
Underground Construction magazine invited several manufacturers to comment about HDD downsizing:
Is there a trend toward downsizing directional drills?
American Augers, Richard Levings, director of product management: Power density has been a goal of manufacturers for a number of years now. This was primarily driven by the smaller utility drilling packages needing to work in more confined residential spaces.
Barbco, Anthony Barbera, vice president product development, technical service, and product control: Yes, there is a trend toward downsizing.
Ditch Witch, Seth Matthesen, HDD product manager: HDD size requirements for utility projects have been fairly constant since the inception of HDD.
Vermeer, Tod Michael, product manager for trenchless core products: I agree that there is a desire to minimize equipment footprint on most HDD construction job sites. However, I would not necessarily say that HDD manufacturers have been able to meet the desire of a reducing footprint or weight on all models across the manufacturer’s product line. This transition has been a continual process over many years and I would not consider it a new trend. It’s just been an evolution of the industry to meet the growing needs of the market.
Does downsizing apply not only to big rigs, but to mid-size and compact models, too?
American Augers: Work space efficiency is practiced in all size drilling units today. Even the maxi systems are finding some job-site size restrictions driven by right-of-ways and environmental concerns. This does not always mean the size of the equipment has to be downsized but rather reconfigured on the site. As the HDD industry progresses, all classes of contractors will see pressure to increase efficiency of their operations. Finding the balance of having the ability to complete projects on time and on budget with systems that fit their business plan will drive how equipment is shaped and packaged.
Barbco: Downsizing seems to start around the 100,000-pound rig size.
Ditch Witch: Both.
Vermeer: Reducing equipment footprint is desired not only on large equipment, it also is very important on midsize and compact equipment, as well. In fact, it may be more important on smaller HDD equipment than with HDD rigs larger than 200,000 pounds.
What factors are driving downsizing?
American Augers: The location of projects and how tightly they are regulated.
Barbco: Much of the drilling in shale is being done for wet gas in areas such as southern Ohio, West Virginia and Pennsylvania in mountainous terrain for long shots on steep grades.
Ditch Witch: On the utility side, it is driven by weight for transport and for the smallest system packing just as much power as possible.
Vermeer: I believe the trend and/or desire to have a minimal equipment footprint on a job site comes from an increase in HDD work that is occurring in urban areas. As pipeline work continues to encroach on urban areas, contractors want to have a minimal impact on traffic flow, existing landscape and the general public who are working and living in these areas. These have been driving factors for the move to downsized equipment for years.
Have technical advances contributed to downsizing?
American Augers: Yes and no. Certainly hydraulic components have advanced in efficiency which helps use more of the horsepower available. But when the overall power consumption required to perform a project is considered, it is necessary to look at all the inputs to know what it takes to be successful on each project day after day. Downsizing and combining power components sounds great in theory but often leads to project failures if not done properly. This is true up and down the equipment classes.
Barbco: Not really. Hydraulic and electrical components continue to improve but that does not bring much benefit to downsizing.
Ditch Witch: For utility size units, we have taken advantage of the increases of horsepower in smaller block engines to reduce weight and size. Higher-efficiency hydraulic components also have contributed to sustaining or increasing performance specifications in a given-size drill unit.
Vermeer: For the most part, there have not been recent technology contributions that have led to the downsizing of Vermeer HDD equipment. In fact, new engine emissions requirements, as well as low noise level requirements have negatively impacted most equipment footprint designs. The power-to-footprint ratios have improved due to the creative work of engineering teams that are continuously working to select and configure components that provide a minimal weight impact on the machine and help reduce equipment footprint.
What are the primary benefits downsizing brings to HDD users?
American Augers: Smaller machines that fit in tighter spaces can be packaged for hauling and often reduce towing, trailering and sometimes licensing requirements. However, the product being installed, coupled with bore length and ground conditions do more to drive the size of the equipment than the available space. When the job requires working in the street, in a back yard, on a sidewalk, etc., space may be so limited that a very small unit is needed. When a project is such that the product size and length are large, but the space is too small for the size system needed to complete the project successfully, the bore often will be broken up into segments so smaller equipment can complete each segment.
Barbco: Smaller equipment is easier to mobilize and downsized equipment can bring more productivity in areas where larger equipment can’t work.
Ditch Witch: Smaller work spaces such as backyards, street access, or highly- landscaped areas require smaller equipment; and smaller equipment can reduce transport requirements and, in some instances, eliminates the need for a transport driver to have a CDL. On occasion, keeping a replacement model in a certain weight class keeps the owner from having to upsize transport equipment.
Vermeer: There are a number of benefits from using a small foot print machine. The smaller the machine looks on a job site, the fewer complaints operators receive from area homeowners and businesses. Lighter weight machines are less expensive to transport to the job site.
Smaller and lighter machines are less destructive to the terrain, which reduces rehabilitation expenses to the existing landscape.
Productivity has not necessarily been improved by footprint reduction, but we have concentrated on reduced set-up time and cycle times of specific drill functions. This can help enhance overall productivity. There have been some productivity improvements where contractors can utilize a newer HDD machine with a smaller footprint that may feature more power than an older and larger model HDD machine. Again the productivity advantages come from reduced damage and rehabilitation of the environment and landscape, as well as cycle time improvements on specific machine functions.
What are examples of downsized models in your company’s product line?
American Augers: The American Augers DD-110 and DD110S, DD-220 20-foot version and MPR-6000 fluid cleaner and pumping system. All of our equipment can be configured in line to meet tight or narrow right-of-way requirements. All HDD equipment can be transported under height, width and length requirements.
Barbco: Our 80,000 pound and 100,000 rigs are on a smaller footprint than our old 50,000-pound rig. Our new 200,000 and 250,000 pound models have the same as the old 100,000-pound footprint. We put the most power in the smallest footprint. Our 250,000-pound rig has 45,000 foot pounds of torque with excellent speed on a 20-foot rod machine.
Ditch Witch: The J9 has increased horsepower in the same size as its predecessor; the JT25 has increased power specifications with lower weight and horsepower than its predecessor; the JT60 weight and size is relatively the same as its 40,000-pound class predecessor.
Vermeer: It is difficult to cite examples where Vermeer has reduced the size and weight of a particular model. In fact, most models have increased in weight and footprint over time. It is necessary to look deeper at the size/power relationship. At Vermeer, we work hard to maintain weight and footprint, while increasing power specifications that allows a customer to choose a smaller model to do the same work previously done with a larger machine.
One of the latest examples is the D20x22 S3 drill built off the D16x20 Series II platform. Improvements were made to the engine horsepower and hydraulic circuits allowing the new D20x22 S3 model to maintain nearly the same footprint as the D16x20 Series II model while taking on heavier and larger work with improve efficiency.
FOR MORE INFO:
American Augers, (800) 324-4930, www.americanaugers.com
Vermeer Corp., (888) 837-6337, www.vermeer.com
Ditch Witch, (800) 654-6481, www.ditchwitch.com
Barbco, (800) 448-8934, www.barbco.com
Comments