February 2015, Vol. 70, No. 2
Features
Innovative Geopolymer Lining Process Saves Severely Corroded South Texas Stormwater System
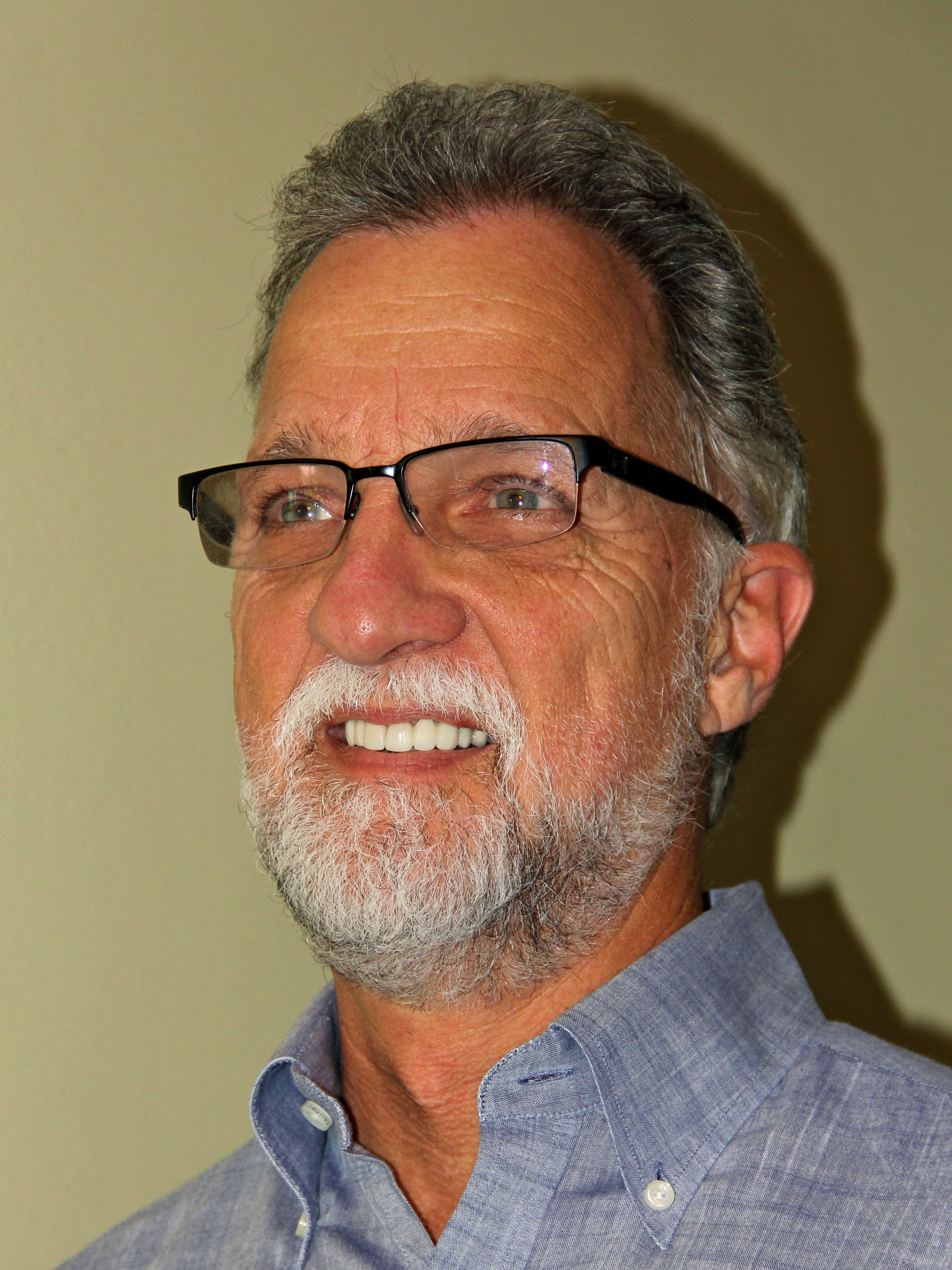
After an extended period of severe drought during 2013, the skies above the south Texas town of McAllen opened up.
Subsequently, the soil became saturated, inflicting continuous groundwater infiltration on nearly a half-mile side-by-side section (4,420 linear feet) of 114-inch storm water corrugated metal pipes (CMP). No longer able to sustain the long-term exposure to the excessive groundwater flows, the damaged CMP located beneath a residential area of McAllen finally caved – literally. Severe deterioration including several offset joints and partial collapse of the pipes in numerous places had resulted in too much damage and the quickly deteriorating storm water line had fallen into dire need of repair.
To complicate matters for officials with Hidalgo County Drainage District 1 (HCDD1) charged with finding an effective rehabilitation solution, a sinkhole had formed directly above the afflicted pipes – the result of an unprecedented event of abnormally wet weather in 2013 – creating additional challenges for repairing the affected pipes that were positioned well beneath the narrow streets and pristine yards of this upscale residential neighborhood.
HCDD1 then contacted Fred Kurth, project consultant engineer with Melden & Hunt Inc., a south Texas Civil Engineering firm, to evaluate the condition of the corroded storm water line. After a thorough inspection of the damage and extenuating environmental repair challenges, Kurth turned to Inland Pipe Rehabilitation (IPR), based in Houston, for a possible repair solution.
“IPR immediately identified serious issues with the pipe, specifically with its joints,” said Kurth. “Based on the large diameter CMP, the overall condition of the damaged pipe and the confined space jobsite limitations, IPR recommended its EcoCast Advanced Geopolymer Lining System as a possible solution. After detailing how the EcoCast system works and its advantages, and submitting a thorough work plan for tackling the complicated and challenging project, we were able to convince HCDD1 officials that EcoCast was the right approach.”
Introduced by IPR in 2010, the EcoCast Advanced Geopolymer Lining System is the first “green” geopolymer rehabilitation process discovered. The process is considered by rehabilitation experts as a technological breakthrough in the ongoing evolutional development of structural geopolymer products available to the traditional pipeline rehabilitation market. Historically, the industry has focused on four critical performance physical characteristics for the successful application of geopolymer rehabilitation lining systems: excellent bond strength, low permeability, high compressive strength and efficient constructability. Yet, as Steve Henning, technical director with IPR explains, what sets the EcoCast technology apart from other geopolymer lining system methods is that EcoCast is also sustainable.
Sustainability
“IPR, along with our development partner, Milliken, were able to add a fifth crucial element – sustainability – to the traditional mix with the EcoCast Lining System methodology,” Henning says. “The proprietary system combines the most advanced application equipment with a custom formulated geopolymer specifically designed for consistent application and long-term strength. The process employs a geopolymer liner that is precision sprayed or spun onto existing host structures such as culverts, manholes, wet wells, etc. EcoCast combines the most advanced application equipment with a custom formulated geopolymer designed specifically for achieving consistent application and long-term strength and performance.”
The high-strength, fiber-reinforced EcoCast approach – applied by mechanical pumping, spraying, trowel application or combinations thereof – forms a crystalline structural liner that halts further water infiltration, rebuilds the surface and offers higher resistance to acids resulting in greater long-term surface durability. The system is exceptionally resistant to environmental factors like heat and cold, and allows for extended application environments through batch temperature controls. It also cures quickly, providing shortened storm water by-pass time.
“EcoCast is ideal for a variety of applications and is especially effective for storm water and sewer line repairs similar to the McAllen project,” Henning says. “There were several challenges and extenuating circumstances including many sections that required extensive prep, patch and sealing work. The collapsed section, more than 400 feet, was completely removed and replaced with CMP, then lined with EcoCast. Another shorter 10-foot section had deflection in the top of the pipe and was also removed, replaced and lined. Most of the damaged pipe joints were in really bad condition so we applied carbon fiber grid reinforcements to stabilize, strengthen and seal the area between the joints. This step in the process was somewhat unique to the McAllen project and was deemed necessary because of the severely compromised condition of the joints.”
According to Henning, EcoCast is designed specifically for large diameter projects, and effective for materials that have separated, dropped or have curves, making it an ideal rehabilitation option for the severely corroded and structurally compromised McAllen job. The vast majority of pipes ranging in sizes from 36 inches to more than 10 feet in diameter can be rehabilitated by the EcoCast method. With less installation risks than other lining rehabilitation methods, and given the confined space jobsite restrictions of this residential area of McAllen, project owner HCDD1 was convinced Kurth and IPR had recommended a solid, effective solution.
Detailed plan
Work on the project got underway in April 2014. “The condition of the pipe was a big issue,” says Henning. “There are always specific safety concerns we must take into consideration for entering the pipe, such as imminent collapse or the inability to control water from entering the pipe.”
Henning explained that flow control was also an issue, necessitating a plan to bypass underground infiltration and storm water flow to the affected length of pipe. Both ends of the pipe were evaluated to determine how best to remove any standing water present during the rehabilitation process. It was also necessary to make sure the bypass system was set up so the pump inlet was positioned below the level of the deepest part of the section of pipe that needed to be rehabilitated.
In addition to the bypass pumping system, temporary dams were constructed to halt and divert the nonstop groundwater infiltration IPR encountered during duration of the rehabilitation process. Since the McAllen storm water system was installed with two pipes side-by-side, IPR was able to divert water to one pipe while repairing the other, and vice versa.
Location, with the damaged pipe located beneath a prominent residential area of McAllen, as well as the city located in close proximity to the Mexico border, also factored into the work plan equation.
“The EcoCast method was developed specifically for projects where working in confined space is a concern,” says Henning. “We were also sensitive to completing the repairs using equipment and a process that would be minimally invasive to residents in the affected residential area. Security was also an issue as the presence of federal agents monitoring illegal border activity was ongoing.”
“Unlike many other repair systems, EcoCast is best suited for use in damp and humid environments,” says Collis Parrish, business development manager with IPR.
Process
The EcoCast process began with thorough cleaning of the inside of the severely corroded CMP. “To assure that proper adhesion occurred, the interior of the pipe was thoroughly cleaned using a high-pressure washer ranging from 3,500 to 5,000 psi and water temperatures ranging from cold to over 100 degrees,” Henning said. “This process was effective in removing any film, dirt or other deleterious materials. Ideally, the wall of the pipe should be damp but not wet with running water for the EcoCast system to be most effective.”
A fast setting hydraulic geopolymer applied directly to the damaged sections of the CMP was necessary to stop flowing water and repair leaks. Chemical grouts were also applied at several junctures to stop larger amounts of infiltration.
Once cleaned, it was necessary for IPR to prep the joints, which were a major failure point of the existing pipe structure. The soil surrounding the pipe was very fine, sugar-like sand which aided in exacerbating joint issues during infiltration. Any joint within the pipe that showed signs of failure, infiltration or separation was subsequently grouted, sealed and reinforced with a carbon fiber mesh. The chemical composition of the geopolymer used in the EcoCast process allows for a fully structural and monolithic rehabilitation, which eliminates joints all together.
IPR then employed the process for applying the EcoCast geopolymer liner, as determined by findings of the engineers reports outlining the thickness the liner needed to be to effectively repair the structure of the pipe. In this case, minimum thickness of 1½ inches was required, using the proprietary IPR GeoSpray material mixed with appropriate amounts of clean water. The EcoCast geopolymer liner was then applied to the inside of the pipe using a spin casting process.
“Beginning at the downstream side of the pipe, the oscillating EcoCast spin cast assembly was placed inside the pipe, along with the product delivery hose, retraction chain, air hose and electric power line,” Parrish explains. “A direct-drive electric motor moves the entire assembly at a predetermined speed, depending on the thickness of liner required for various sections. The application process is monitored continuously and adjusted accordingly, based on engineer design calculations. The pump delivers material at a consistent rate and pressure, and has multiple built-in alarms that detect whether too much or too little material is being delivered. The water ratio is also carefully monitored and must be maintained on a consistent basis.”
According to Henning, another advantage of the EcoCast system is the curing properties of the material. “Extreme heat or cold can affect curing with other technologies,” he says. “The conditions must be monitored closely and adjustments made accordingly to achieve proper curing. The mechanically mixed EcoCast geopolymer liner begins to set very quickly.”
Because of the extreme groundwater infiltration, the lining material was spin cast using a top down versus the usual bottom up approach for the McAllen project. There were also occasions where hand trowels were used to compact the geopolymer material into all the voids to achieve a level, smooth surface.
Once the liner achieves initial curing – only a matter of hours for the various sections of the McAllen job – full storm water flow was released within 24 hours.
“We were able to complete the CMP rehabilitation completely, successfully and cost effectively with only minimal disruption to the neighborhood above,” Henning says. “We were able to overcome a variety of challenging conditions and save HCDD1 a lot of aggravation using the EcoCast system. It turned out to be the ideal solution for repairing this severely deteriorated section of storm water pipe. We were most appreciative that Fred (Kurth) was acquainted with the EcoCast System and recommended the proprietary IPR approach for the project.”
FOR MORE INFO:
Inland Pipe Rehabilitation (IPR), (281) 362-1131, www.teamipr.com
Melden & Hunt Inc., (956) 381-0981, www.meldenandhunt.com
Comments