September 2014, Vol. 69, No. 9
Features
Locating Systems: The Core Of Every Successful Bore
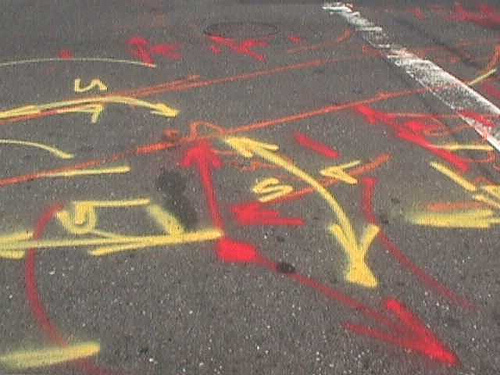
There’s no doubt that the success of any underground installation project depends on critical information provided drill operators by locating systems.
The ability of the operator to successfully navigate the planned drill path by knowing precisely where the drill bit is located – and where it is heading – is made possible by locators. HDD, in fact, owes part of its name and much of its distinction, to locating equipment. Since drill operators cannot see the position or heading of the tooling, without the assistance of locating systems a drill operator could only hope the machine’s tooling will reach the intended target destination accurately. Simply stated, without locators, there would be no directional in HDD and absent locating systems, HDD would simply not exist today.
“The development of a surface verification method was the catalyst for HDD’s amazing growth,” says John English, founder and president of Horizontal Technology, based in Hockley, TX. “Knowing precisely where a drill bit is located and where it is heading is the foundation for HDD’s success.”
Matching systems to jobs
As the world’s underground utility infrastructure has grown and become more crowded, documentation and accurate mapping of the location of individual water, sewer, gas and electrical lines has become even more critical. Yet, the distinctions between the various locating systems have blurred somewhat, especially for walkover units, due largely to technology improvements developed by locating system manufacturers since locating systems were first introduced.
It’s critical for HDD contractors to select a guidance system that will perform best given the variations of specific bores. Yet many of the industry’s most active HDD consultants are often not fully aware of the technical differences between various types of guidance systems.
Locating systems manufacturers typically offer three groups of systems: basic, standard and advanced. The basic system typically has a single frequency with modest depth and communication range. The standard system generally has two frequencies with better depth and communication range, while advanced systems have four or five frequencies, excellent depth and communication range, plus other specialty features such as data logging, interference rejection and other advanced features.
While the most common locating equipment used by contractors are walkover and wireline, some contractors are also utilizing gyro-based systems for projects where sufficient clearance is available – 600 feet or more – and where long distances (up to 1.5 miles) must be performed with only minor deviation, generally less than three feet of allowable positioning error. Using a gyro-based system is usually more costly, although effective in areas where a surface coil isn’t possible or economical. Some projects may also require a combination of a gyro and a magnetic steering tool.
Equipment components will vary by system depending on the operational functionality of the system. Walkover configurations include a sonde (or transmitter) behind the bore head that registers angle, direction, rotation and temperature data. This information is then encoded into an electro-magnetic signal which is transmitted through the ground to the surface. At the surface, a receiver is manually positioned over the sonde and the signal decoded and steering directions relayed to the operator of the bore machine.
Walk-over systems
“As a rule of thumb, walkover systems are best suited for installation’s where the bore path is clear to walk over and unobstructed,” says John Bieberdorf, senior product manager with Ditch Witch. “Bore depth is dependent on the environmental conditions and could be anywhere between 30 and 60 feet. Walkover systems also have the capability to log a two-dimensional profile of the bore depth and distance which is important since side-to-side, but do have a limited practical distance that the receiver can be positioning away from the tool head to work accurately. Wireline systems, on the other hand, can log a three-dimensional position of the drill tool (length, depth, side-to side) and can monitor the tool head from a much greater distance.”
Wireline systems use a wire to transmit various data up the inside of the drill pipe. At the surface, the data from the wire is decoded by a computer to provide depth, angle, rotation, direction and other information. When conditions do not allow a receiver to be positioned over the sonde or interference causes degradation of the signal, a downhole or wireline locating system will likely be employed.
“Walkover systems are very good,” says Jim Agnew, vice president of Inrock. “They’re accurate and efficient, especially for shallow, shorter bores and are also easy to get rigged up and set. The smaller rigs use this type of navigation system with great confidence. The only drawback would be limitations of the bore plan as far as depth, interference from swift moving rivers and wide lake crossings.”
All magnetic guidance tools utilize magnetometers and accelerometers to calculate a directional heading. These readings are recorded at specific intervals and the data is used to calculate the drill path’s location and direction. In some areas, drills can be very accurate with the calculated data. Yet in some locations, usually the more congested areas, magnetic interference can affect the readings and the calculations. By placing a thin wire on the ground, along the bore path, and creating a known magnetic field, the operator has the ability to know precisely where the magnetic steering tool is located.
“A locating system can represent a substantial investment, anywhere from $10,000 to $20,000 so contractors should consider a variety of factors,” says Siggi Finnsson, product manager with Digital Control, Kent, WA. “Size of drilling machine, types of projects, the flexibility or expansion capabilities of the system and availability of technical support are all important considerations. Once a locating system has been selected and purchased, it is potentially difficult and expensive to change or update the system at a later time. Limitations of the contractor’s current system should be considered as the types of projects they tackle become more involved and complex.”
According to Finnsson, contractors should also consider locating systems that are user-friendly, in addition to being accurate and fast. This leads to a shorter learning curve by locating personnel and allows locators to achieve operational proficiency more quickly.
“Contractors should consider a variety of factors when choosing a locating system that’s best- suited for specific jobs including soil condition formations, boring depth, any obstacles that will be encountered and signal interference,” English says. “Installation and product line specifications may exceed the capability of the contractor’s locating system, so additional options should be explored. If it is possible that a walkover system might be inadequate, it could be money well spent to plan ahead and include a wireline magnetic steering system in the project’s budget.”
Each type has inherent and distinct capabilities and advantages – and conversely – some notable limitations. Regardless of walkover, wireline or gyro-based, all systems are deemed reliable, accurate and dependable by HDD industry experts. Each type has a fitting place and serves an effective and important role by assisting contractors in achieving successful, incident-free bores.
“Obviously there’s a lot more underground infrastructure congestion in the city than a project where the jobsite is located in the country,” says Danny Crumpton, technical sales manager with Houston, TX-based Inrock Drilling Systems. “The more utility lines in the ground, the greater the likelihood of encountering signal interference. Depending on how deep the footings run into the ground, even office buildings can cause problems.
Technology, accuracy innovations
“Contractors should be aware that a single wire system is location specific,” Crumpton says. “Not all drill site locations can use single wire locators. We have done offsets of 1,000 feet and depths over 1,000 feet using the beacon tracking system. The system is location specific and serves as another secondary means of locating the bore and providing our ParaTrack locating system another alternative to using a surface coil.”
Recent technology innovations have also greatly enhanced the speed, accuracy, flexibility and functionality of locating systems. Additionally, locator design and capabilities enhancements, along with new electronic data recording information, gathering and communication technology, have allowed HDD contractors to complete bores faster, more accurately and with fewer underground incidents.
“I think the biggest advances has been with software that allows the operator to set up and make changes quicker,” English says. “Ready-to-print, real time ‘as-builts’ allow on-site decisions and improved payment time to contractors. The tools have also allowed more accurate stand-alone tracking of bores at greater depths.”
“One of the biggest advantages derived from recent locating system technology enhancements is speed,” says Crumpton. “Engineers can take three or four surveys in a matter of seconds versus minutes. The system is capable of working to depths in excess of 1,000 feet and is also extremely accurate which saves contractors time and money.”
Most walkover locating systems today have the capability to scan jobsites and recommend the best frequency and many have unmanned, real time remote guidance capabilities with actual and predicted depth capabilities. Multiple frequency capabilities are also common with most locating systems.
Inrock, for example, recently introduced a sophisticated HDD guidance tool component that accurately measure bit inclination and notifies guidance engineers of any deviation or deflection in the bore path.
“Fractured formations create unique challenges for drill operators because of the deflections they can cause to the drill’s tooling,” says Crumpton. “When drilling in formation containing boulders, fractured formations or formations that change from hard to soft and back to hard, it’s useful to know when inclination of the bit changes.”
“Since the introduction of our first product, we’ve continued to improve upon many components of early models,” says Finnsson. “An innovation that has been carried through in our designs from the Eclipse locator, introduced in 2000, is the ‘ball in the box’ concept. The Eclipse was the first locator to incorporate a screen showing the boring tool’s transmitter direction and location in real time relative to the locator. This allows the operator to easily determine the transmitter’s location below ground.”
Enhancements
Enhancements specific to transmitters and handheld devices have also continued to evolve. In addition to transmitting the pitch, roll and depth of a drill head, most transmitters on the market today are also capable of relaying temperature and fluid pressure readings, and many are equipped with remote displays that include wireless and Bluetooth connections. Intersect technology has also help make two bores originating from opposite directions come together and connect with pinpoint accuracy, while new technology in drill displays are providing better systems and more flexibility for contractors. Color touchscreen interfaces have been incorporated into locator displays which provide different options for displaying data so information can be delivered in forms of applications rather than forcing contractors to purchase a new device or having to completely upgrade the locating system’s software.
Additional notable locating system enhancements achieved over the years include:
• Multiple transmitter frequency options which help overcome jobsite interference;
• Streamlined graphic displays with intuitive icon-driven menus;
• Adjustable transmitter positioning to match the drill head;
• 3D antenna configurations;
• Increased depth ranges;
• Enhanced targeted steering capabilities with the ability to calculate distance and depth of the transmitter that allows operators to make up/down and left/right steering corrections more accurately; and
• Wire-line enhancements that are capable of transmitting data through the ground by an electro-magnetic signal to a stationary receiver and artificial electro-magnetic grids that compensate for potential magnetic interference.
While the locating systems and technology developed years ago are still extremely effective, accurate and reliable, we’re always working on improving locating systems with new features and enhancements,” Crumpton says. “That said, however, all the components of early locating systems were solid, built well and have a long and effective life-use span. I know of systems that are more than 10-years old and don’t even need to be recalibrated yet.”
On-site surveying, steering
Contractors with locating personnel who have limited experience can benefit from enlisting the professional services provided by most of the industry’s locating systems manufacturers. The majority of locating equipment from manufacturers offers a variety of customized surveying, locating and data documentation services including on-site guidance technicians, steering tools, on-site troubleshooting and related support. When in doubt, HDD contractors will be best served to employ the professional services of an experienced and knowledgeable locating consultant which can save valuable time and unnecessary expense.
Enlisting professional surveying, planning and onsite locating services offered by manufacturers can eliminate many of the costly mistakes often made on difficult or challenging bores. The many and varied guidance consulting services available to contractors ensures proper setup of equipment, matched to the jobsite, established clearances and drilling conditions. This is essential for accurately tracking the location of the drill bit’s path. Surveying and locating consulting services provided by a professional locating systems manufacturer often includes the review of existing data, resulting in a practical plan and increasing the odds of a successful project. When utilized, these consulting services save owners and contractors time and money.
Some contractors will find it beneficial to purchase either various components or a complete steering tool system. Another option is to subcontract locating services for specific jobs. With systems that are compatible, a contractor can buy a mixture of basic, standard and advanced equipment and know they can mix and match if needed, as well as upgrade a basic system when their operational needs advance.
Ask the right questions
Ultimately, what it all boils down to is three basic questions HDD contractors should ask:
• When to use with which system;
• What additional equipment will be needed; and
• How much will it cost? Factors to consider include the length of the bore and any obstacles being crossed, the soil profile and geological formation, drilling depths and signal interference. Installation and product line specifications may exceed a system’s capability. Contractors will be best served knowing the limitations of their guidance systems as well as the experience and instincts of locator and drill operators.
“While classroom and in-field training is required and recommended for locating personnel to become adept, both walkover and wireline locating systems are usually fairly easy to learn and use effectively,” says Bieberdorf. “Like all HDD equipment, the locator learning curve is more a factor of knowing the equipment and providing the operator the opportunity to attend factory or dealership training where locating personnel are properly trained and understand how to review operational manuals to better understand how different systems work. We also encourage them to call their locating manufacturer’s Tech Support personnel if and when they may get into a bind.”
“Locating systems are not all that difficult for locator personnel to learn,” says Richard Bond, director of operations with Sharewell HDD Services, headquartered in Spring, TX. “That said, there are certain individuals who just have the locating feel – sort of a sixth sense for visualizing what lies below the surface and an instinctual feel for anticipating challenges and underground obstacles, as well as the ability to anticipate and communicate any necessary drill steering corrections to the drill operator. Even with all the advancements in locating technology, the human component remains the most critical.”
FOR MORE INFO:
Horizontal Technology Inc., (713) 774-5594, www.horizontaltech.com
Sharewell HDD, (281) 288-2560, http://www.sharewellhdd.com/
Ditch Witch, (800) 654-6481, www.ditchwitch.com
Digital Control Inc., (800) 288-3610, www.digital-control.com
Inrock, (713) 690-5600, www.inrock.com
Preparing For The Purchase – What You Should Know
HDD contractors considering the purchase of a new or “improved” locating system should do their homework in advance. Armed with the right information and the right questions to ask, your locating system manufacturer will assure the system you select will be the best fit for the bulk of your work. Some important pre-purchase reminders:
• Know the location of the nearest dealer/service center:
• How many transmitter frequencies will be required?
• Is the locator capable of helping determine the best frequency to use?
• Can the system locator log bore path data?
• Can the locator be set ahead of the drill head un-manned and can it provide real time and projected depth? and
• Can repairs to transmitters be completed cost efficiently?
When purchasing a locating system and related professional services, make sure to consider the following:
• Steering tool and operator cost;
• Extra non-magnetic rental tool costs; and
• Consumable items (wire, crimps, etc.) and associated third-party costs including freight, airfare, lodging, etc.
Comments