September 2014, Vol. 69, No. 9
Features
Intersecting In The Florida Keys
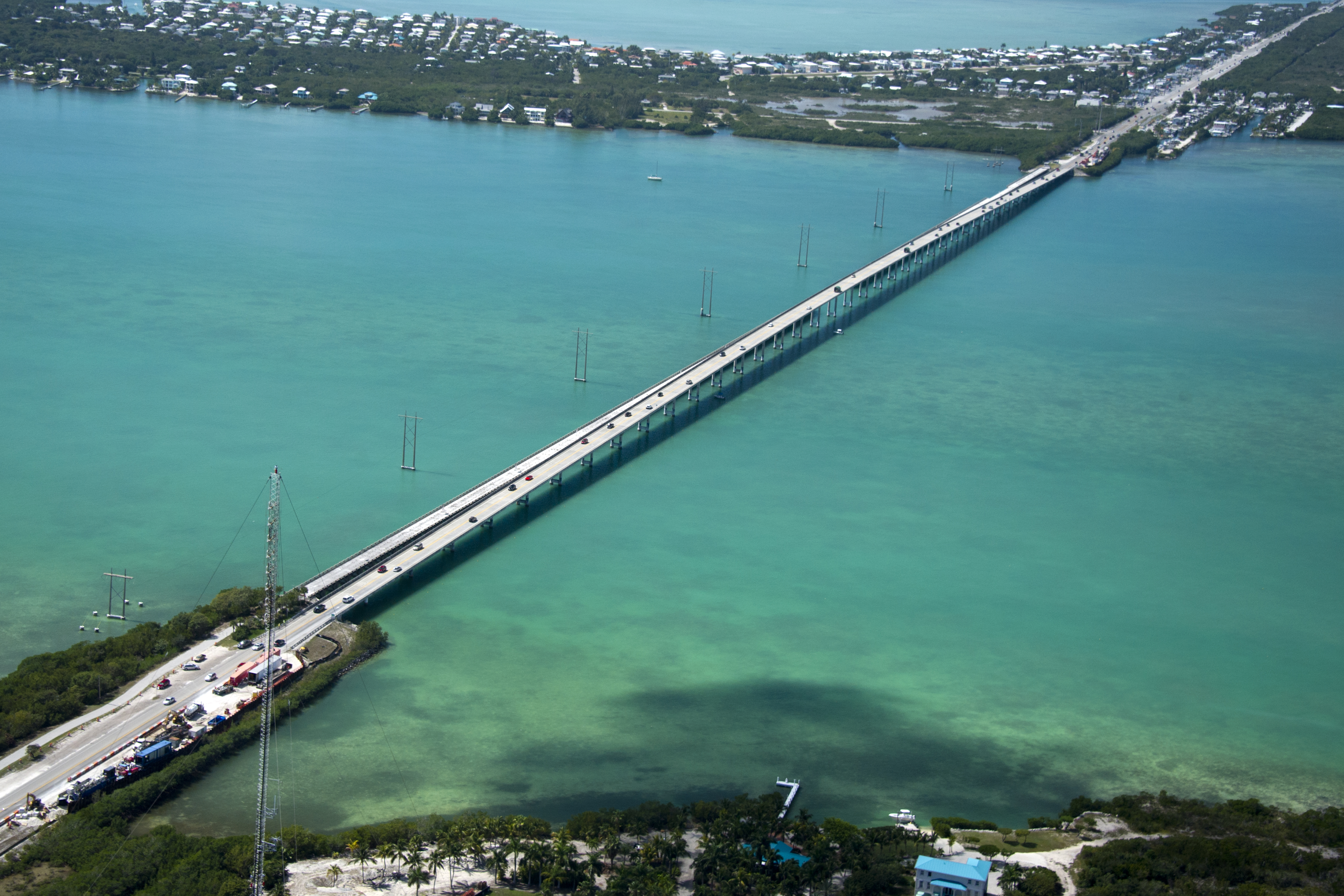
Advances in horizontal directional drilling (HDD) technologies and techniques are making it possible to make longer pilot bores and to install increasingly larger diameter product.
Complex projects considered impossible a dozen years ago are completed routinely today.
Of all the challenging HDD projects, perhaps none is more intriguing than a long intersection of two pilot bores under a body of water. That two drill rigs on opposite ends of a bore route can precisely meet and connect at a designated point still can amaze.
Earlier this year, Utility Services Authority LLC (USA) completed an intersect installation of 5,218 feet of 18-inch diameter HDPE pipe for a new wastewater line under Niles Channel between Ramrod Key and Summerland Key in Florida, approximately midway between Key West and Marathon. The new pipeline is an integral part of a larger project to replace aging sewer infrastructure, improve service for area residents and help preserve Florida waters.
Designated the Cudjoe Regional Wastewater Collection System, the project owner was the Florida Keys Aqueduct Authority. Engineers were Chen Moore & Associates and Eckler Engineering. Layne Heavy Civil (Layne), The Woodlands, TX, was the design/build general contractor. In conjunction with Layne, the crossing was constructed by Utility Services Authority (USA), Belleville, MI.
“This colossal task meant that to ensure success, every aspect of the project had to be engineered,” said Chris Lamb, USA manager of HDD operations. “Among critical considerations were calculations to determine loading, product pipe selection and thickness, the need for ballast water to offset pipe buoyancy, tensile strength and conformance to the owner’s requirements for performance. Considering these and other factors, 18-inch diameter HDPE DR7 pipe was selected.”
Lamb said the decision to intersect two pilot bores launched from opposite sides of Niles Channel was made to mitigate the risk of inadvertent drilling fluid returns into the channel.
The entry and exit pads for both drill rigs had limited footprints allotted for construction activities as both areas were sandwiched between mangroves and U.S. Highway 1, the only vehicular route to and from Key West.
“This meant drilling operations at both launch points had to use every available inch of the 40-foot wide easement,” said Lamb. “Prior to mobilization, Layne installed 450 linear feet of sheet wall on both sides of the channel crossing area to level the sloping right-of-way and to protect the sensitive mangrove areas. The sheet wall was driven 35 feet below the ground surface to support the drill rigs and additional equipment needed to accomplish a project of this size.”
Equipment
USA used an American Augers DD-625 for the lead drill rig with an American Augers DD-210 as the intersect rig. The DD-625 is powered by a 600-horsepower diesel engine. It develops 625,000 pounds of pullback, and 80,000 foot pounds spindle torque. The DD-210 has a 300-horsepower diesel engine. It has 210,000 pounds of pullback, and 60,000 foot pounds of spindle torque.
“The DD-625,” said Lamb “was the right fit for the type of drill rod and downhole tools selected because the equipment easily could accommodate the forces established in the design calculations. The DD-210 worked out perfectly as the intersect drill rig because there was a tighter footprint available since pipe had to be fused on that side of the drill shot.”
The pilot bore extended from Ramrod Key to Summerland Key at 80-feet below the existing ground surface (60-feet below the sea floor) in subsurface conditions of limestone and sand. Ten and five-eighth inch diameter TCI bits were used.
The DD-625 began its pilot bore a week before the smaller rig launched the intersect shot. The primary rig drilled out 3,618 feet and the DD-210 pilot shot was 1,600 feet. “The 3,600-plus feet with the primary rig was the longest we wanted to risk without the relief of the intersect,” Lamb explained.
After the two bores intersected, the DD-210 backed its drill string out of the hole as the DD-625 followed its path. Paths of the bores were guided by Inrock personnel using the company’s P2 guidance system
This is the Niles Channel pullback.
“To be certain accurate line and grade was maintained, USA installed a redundant grid wire guidance system on the Niles Channel Bridge crossing over the channel,” said Lamb. “Because of this, it was possible to cross check the accuracy of the steering tools in real time.”
Inrock also used the P2 system for the redundant grid.
Proper prep
While drilling proceeded, USA crews prepared the pipe for installation. “The availability of existing right-of-way allowed for the HDPE product to be fused in one continuous, nearly one-mile-long string,” Lamb said. “This minimized the exposure to problems during pullback by eliminating the possibility of fusion issues. The whole fusion process took a great deal of planning in order to install the necessary ballast line within the 18-inch product pipe without hindering the ability to fuse and pre-test the pipe.”
Meanwhile, the intersect was completed in 17 days without incident.
Once the pilot hole was enlarged with a 30-inch backreamer, the pipe was pulled in place in less than 24 hours with less than 80,000 pounds of pullback force – well below the engineered calculations established for the length of the bore hole and installation of HDPE DR7 product pipe. Pullback of pipe was completed 34 work days after the start of drilling operations.
There were numerous challenges involved in planning and executing the project.
“From trucking logistics to and from the Keys to running nearly a mile of subaqueous wire grid survey, every detail on this job had to be double checked given the magnitude, remoteness and sensitivity of the project,” said Lamb.
HDD lay-down pads were constructed between U.S.1 and mangrove habitats, leaving little space to construct functional work pads.
“U.S. Highway 1 is the only transportation route in and out of the Florida Keys,” Lamb said. “Couple this with particular weight restrictions, daytime exclusions on heavy loads and the seasonal influx of tourist traffic and we were forced to coordinate logistics in a whole new manner. Loads that came from states away from Florida had to be well-planned in order to arrive on time. Furthermore, this project called for the use of specialized equipment that was not readily available within the proximity of the project area.”
On one side of the work area, there was busy highway traffic and on the other side was the sensitive mangrove habitat.
“We had to strategically plan and place each piece of equipment within a 35-foot wide, 440-foot long drill pad,” Lamb continued. “With 23 semi loads of equipment and a half dozen other trucks needed to construct the project, the lay-down area proved to be most challenging.”
Finding space to fuse the 5,000-plus foot long pipeline string also was a major challenge. To accommodate pipe and equipment along the drill path required a work area more than two miles long.
Remote
All of these restrictions made it very difficult for vendors to support the project on-site. Every detail of the project had to be double checked before operations began.
“In addition,” Lamb continued, “there were zero big-rig vendors, tool manufacturers or specialized navigators readily available to service us if we experienced an equipment failure. It was like working in another part of the world. Because of this, we shipped redundant parts and tooling to the project to eliminate down time and the risk of delaying the job.”
Lamb said safety of individuals on the project and the general public always is the greatest concern.
After safety, Lamb said the greatest concern and crucial part of planning was protecting the pristine eco system of the Niles Channel waterway and its abundance of aquatic life.
“Prior to the start of the project,” Lamb explained, “soil borings were obtained from both the Ramrod and Summerland Keys. This information was used to plan the best vertical route for the drill path to take in order to mitigate the possibility of inadvertent returns into the waterway. Once the vertical depth was chosen, based on soil viability, calculations were run to select the right product material type and thickness capable of withstanding the depth and pullback forces calculated.”
Throughout the project, adherence to regulatory requirements established by National Oceanic and Atmospheric Administration, Army Corps of Engineers and the Florida Department of Transportation were essential for executing quality assurance and risk mitigation.
“Due to the efforts of all involved, the project was completed in full compliance and without incident,” concluded Lamb.
In addition to directional drilling, Utility Services Authority provides a variety of utility infrastructure and trenchless services, including civil engineering, cured-in-place pipe lining, pipe bursting, sliplining, hydro excavation, pipeline maintenance and rehab and land surveying.
FOR MORE INFO:
Utility Services Authority, (734) 481-0872, www.usallc.net
Layne Heavy Civil, (281) 475-2600, www.layne.com/en/divisions/heavy-civil.aspx
American Augers, (800) 324-4930, www.americanaugers.com
Inrock, (713) 690-5600, www.inrock.com
Comments