September 2014, Vol. 69, No. 9
Features
HDD, Fusible PVC Solve City’s Immediate Growth Needs
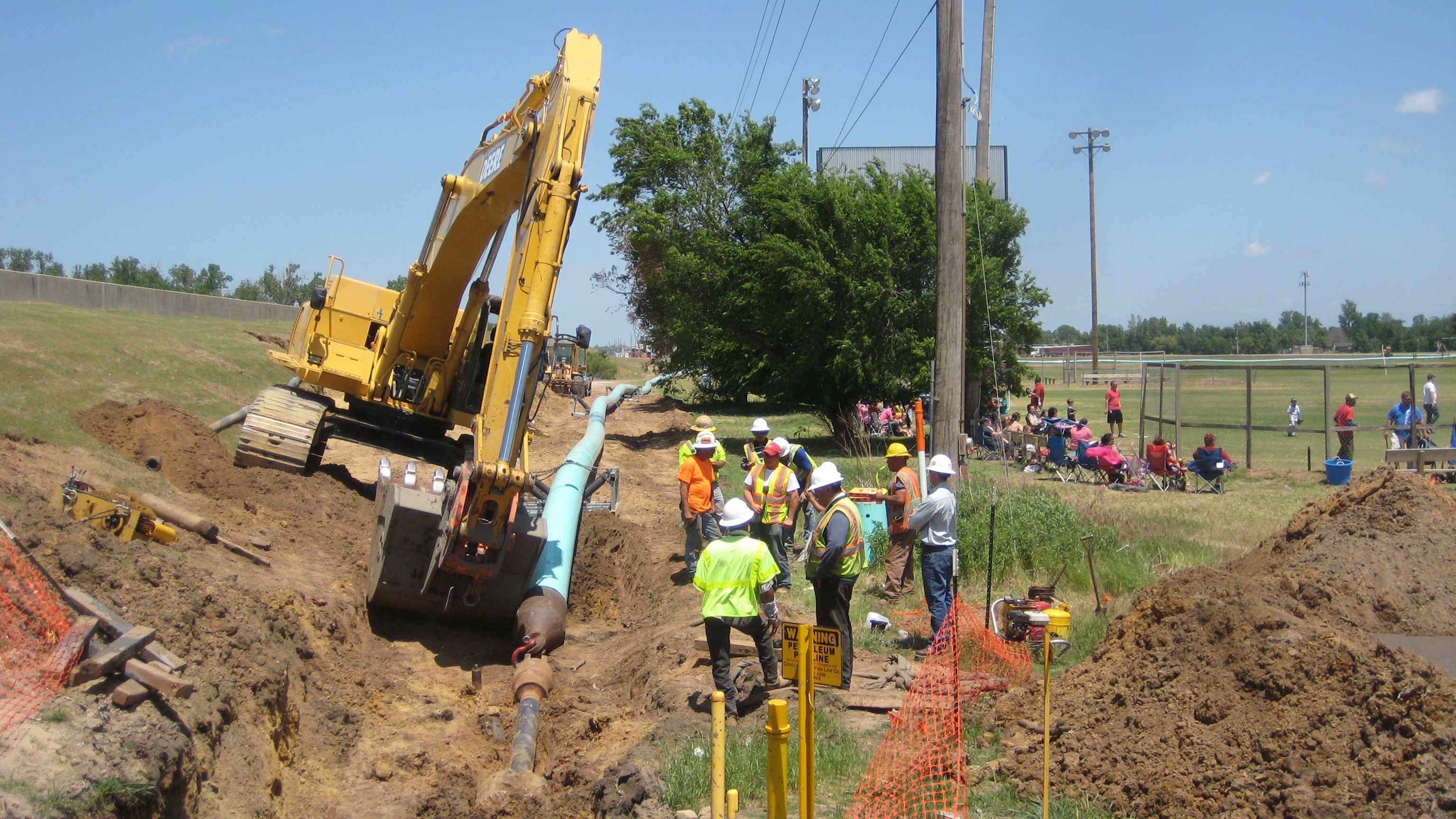
Fast-growing cities like suburban Bixby, OK, are continually tasked with building infrastructure that will sustain the influx of new residents.
The city’s overtaxed sewage system is just one example of needed improvements as more and more homes are built north of the Arkansas River in what was once a gap between Bixby and Tulsa. A state-issued consent order will not be lifted until the city increases its short-term wastewater treatment capacity to serve some 16,000 to 17,000 residents in this area and completes a long-term compliance plan for the entire city. A new wastewater transfer line is part of the $2.5 million short-term improvement project that must be complete by Jan. 1, 2015. The long-term compliance plan will provide for continued population growth, accommodating 40,000 to 50,000 future residents.
Currently, Bixby has two lagoon treatment facilities on the north and south sides of the river. The solution to the city’s short-term treatment needs is a pipeline that will transfer excess flow from the lagoons on the north side of the river to the lagoons on the south side of the river where there is more capacity until a new plant is constructed or it is connected to a regional wastewater facility.
In the past, the procedure has been to actually excavate and divert the river channel when new utilities were installed. The city is avoiding that at this time by using horizontal directional drilling (HDD) technologies to carefully control the location and depth of the crossing.
“To avoid construction and excavation operations within the river channel and variable nature of the flow conditions, directional drilling was selected to ensure that the force main was placed within a stable formation (shale) that was well below the reach of any surface conditions that could interrupt service,” said Jared Cottle, Bixby city engineer.
Pipe material
The city selected fusible PVC, supplied by Underground Solutions Inc., for the bored portion of the force main. McGuire Brothers Construction is the general contractor with Holloway, Updike and Bellen engineers and Nebraska-based Thunderstone Construction as the driller.
Fusible PVC is joined through a patented heat fusion process which creates one continuous length of leak-free pipe, eliminating the need for gaskets. UGSI provided fusion expertise on-site, operating a TracStar 900 fusion machine made by Tulsa-based McElroy Manufacturing. The machine was especially well-suited for the application because of its rugged, self-propelled track system.
“The biggest advantage to using a tracked fusion machine is the ability to make critical adjustments during the fusion process without having to utilize additional equipment,” said Eric Davis, UGSI’s vice president of operations.
David Reuter, UGSI regional sales manager, said they were able to fuse the entire 18-inch, 2,350-foot length of pipe prior to the drill. Once complete, the fused pipe curled and twisted alongside a sod farm and baseball fields. Thunderstone then drilled the bore under the river at depths of 30 to 60 feet and pulled the fused pipe to the south side of the river. Sand formations dominate the area, so Thunderstone drilled into more stable layers of shale. Their equipment included an American Augers DD440T Drill and MCR-10,000 Recycler.
It’s been an interesting project that required a few accommodations along the way because of its location adjacent to a city park. “Bixby was having its BBQ & Blues Festival and we had to prepare for that,” Madden said.
Hundreds of people would need to park in and around the jobsite, but there was one problem – the fused pipe that was staged in the area was blocking their way. Madden said they resolved the issue by inserting the Fusible PVC into a steel pipe that was buried so people could drive across it.
UGSI used a McElroy TracStar 900 to fuse DR 18-inch Fusible PVC near the bridge crossing in a tent to protect the fusion joint from the elements.
Rodney Madden, project manager for McGuire Brothers Construction, said the next phase of work involves laying a 140-foot stretch of 16-inch, high-density polyethylene (HDPE) pipe that will discharge into the south lagoons. McGuire will do the fusion work on that portion of the project with McElroy’s Certified Rental machines. Because of the flexibility of HDPE, they will be able to wind it through a manhole and anchor it on the bottom of the lagoon.
Madden said that they are on target to finish up the project by Nov. 1.
FOR MORE INFO:
McElroy Manufacturing, (918) 836-8611, www.mcelroy.com
Underground Solutions, (858) 679-9551, www.undergroundsolutions.com
American Augers, (800) 324-4930, www.americanaugers.com
Thunderstone Construction, (402) 786-2270, http://dev.thunderstoneconstruction.com
McGuire Brothers Construction, (918) 224-2764
Holloway, Updike and Bellen Inc., (918) 682.7811, www.hubengrs.com
Comments