September 2014, Vol. 69, No. 9
Features
Common Controls Cut Learning Curve For HDD Operators
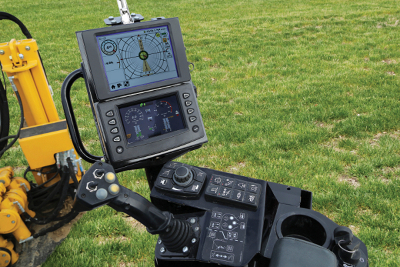
Regardless of brand and model, the basic functions of horizontal directional drilling (HDD) rig are the same.
However, on early directional drill models, controls of different models – even made by the same company – often were arranged differently on different machines.
As new automated features such as pipe make-up and breakout systems were introduced, the array of controls could be confusing, often making it difficult for an operator to move from one model or brand to another in an organization’s equipment fleet.
Ease of operation is an important sales point for any type of construction equipment, and it made sense to HDD manufacturers to make operation of their equipment as simple as possible. Arranging controls in a similar pattern on all models was a step in that direction and today drill rig manufacturers embrace commonality of controls in equipment designs.
Underground Construction asked three primary drill rig manufacturers to share their views on this topic.
What is your definition of “common” controls?
Vermeer, Jon Kuyers, global underground product manager: We define common controls as having the same basic control system grouped by function. The only caveat would be that with the smaller models that do not have rod loading systems, those controls will not be included. On some of the larger drills, the keypads may also have different functionality based on a different features like a crane or rod stager which the smaller drills would not have. The D36x50DR Rock drill has a slightly different joystick switch for the makeup and breakout of the dual rod system’s third vise; otherwise it is like our standard D36x50 Series II drill.
Ditch Witch, Seth Matthesen, senior product manager: Our goal for common controls is to allow users to be able to operate various sizes of machines without having to adjust to controls moving around on a console panel or joystick. They would be positioned the same on all models.
American Augers, Brian Hollis, director of engineering: Our definition is: controls grouped by function.
Is directional drilling equipment well suited for the common control concept?
Vermeer: Yes, because there is not a significant amount of variation among many of the machine sizes. For instance, a 20,000-pound pullback drill has the same joystick controls as a 60,000-pound pullback drill. While these drills are designed for totally different types of work, an operator can quickly learn how to operate the machine and how the machine reacts and performs in differing types of ground conditions.
Ditch Witch: Yes. When going from small drills to All Terrain-capable drills, there are a few additional controls that are needed to operate the inner rotation functions, but these should be minimal.
American Augers: For fundamental machine controls, yes. However some machines we build are very specific or unique, and it is more challenging to make those machines common.
What are the benefits to drill operators of having common controls?
Vermeer: There are many benefits. Obviously when operating different sizes of machinery, the learning curve is drastically reduced. The thrust and rotation levers are always consistent – the mud pump, throttle and rod loader controls all are located on the joysticks. This is common throughout the Vermeer drill line.
Ditch Witch: Common controls among equipment gives the driller the ability to go from one machine to another without taking the risk of damaging the drill or product by hitting the wrong function or slowing performance due to re-adjusting his or her operation.
American Augers: The learning curve for an operator to learn the machine controls of one drill compared to another drill is much less. Operators can jump from a 100,000-pound class rig into a 220,000-pound class rig and feel comfortable much sooner if the controls are similar or common.
How are common controls related to ergonomics?
Vermeer: Common controls were developed in direct relationship with operator ergonomics. We looked at how our machines were operated, collected feedback from operators – what they liked and disliked – and grouped the controls according to the operations that were used the most, then developed the logic that made the operation consistent and easy to operate.
Ditch Witch: Common controls contribute to optimizing the ergonomic operation of a product. With the consistent operation of various drills, optimizing the ergonomics of a drill family will lead to a common control layout.
American Augers: We try to make all our controls ergonomic and accessible to make work comfortable for the operator.
Are there controls that do not apply to all models across your line?
Vermeer: Rod loader controls are not available on our smallest machines and as mentioned, the D36x50DR has an additional toggle for the third vise.
Ditch Witch: Yes, we have two control variations. The first one is the difference between a Jet Trac drill and an All Terrain model. The second one would be the addition of a pipe box handling system. Generally the pipe box handling system requires an independent control.
American Augers: Yes. For example, some machines have mud pumps on board and some machines do not. There are also machines that have pipe loaders. Obviously, each machine’s controls accommodate such differences.
Are you satisfied with the status of your program to achieve common controls across your HDD line?
Vermeer: Yes, we are very pleased with the implementation of our controls across our product lineup and believe it has helped operators and companies in the industry to expand their operational abilities.
Ditch Witch: We have made great strides to improve the common controls of our drill line. However, we are not done.
American Augers: Yes, although we are always looking at new controls technologies and trying to find opportunities to incorporate them into our standard product offerings. With the large number of HDD models we have, there is always room for improvement.
Are there steps are still to be implemented?
Vermeer: While we believe we have made great strides in developing common controls across our lineup, we also know that we are never finished. Vermeer always will be looking to find a better way to adapt and improve our controls with the advancement of new technologies. This can only help our customers be able to become more productive and profitable.
Ditch Witch: Yes.
American Augers: Absolutely. In addition to new technologies, we are monitoring and working to comply with forthcoming regulatory standards as they apply to our equipment, specifically the European standard EN16228-3.
Has there been an effort among manufacturers to make controls common to all brands of equipment? Is such a goal achievable?
Vermeer: I would not say there has been a concerted effort among the various manufacturers domestic and foreign to communize controls.
Ditch Witch: Due to the established customer bases of Ditch Witch and other manufactures, customers drive preferences of choice based on controls.
American Augers: EN16228, a European standard to go in effect at the end of the year, has a specific section that applies to HDD controls. Much of it is directed toward safe operation and commonality of machine signage, but there is a subsection that will require changing a method of controls, specifically the “hold to run” controls. In addition, the Association of Equipment Manufacturers (AEM) is active in standardizing safety symbols and for identifying controls.
FOR MORE INFORMATION:
Vermeer Corp., (888) 837-6337, www.vermeer.com
Ditch Witch, (800) 654-6481, www.ditchwitch.com
American Augers, (800) 324-4930, www.americanaugers.com
Comments