October 2014, Vol. 69, No. 10
Features
Pipe Burst A “Walk In The Park” For No-Dig Tec
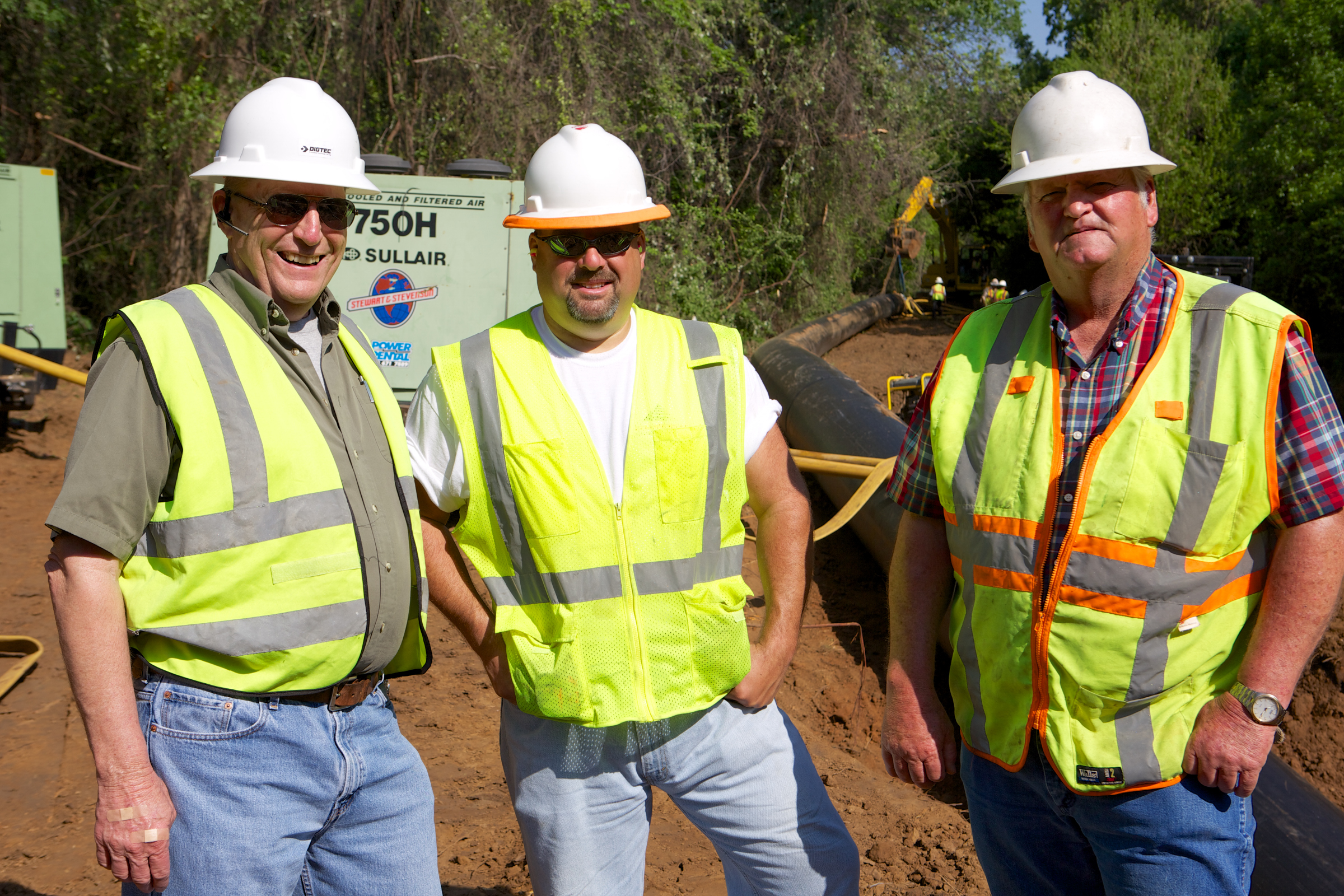
Summing up the largest diameter pipe burst performed by his company to date, John Newell, general manager of No-Dig Tec of Dallas, quipped, “It was just a walk in the park.”
No-Dig Tec completed all six runs of a pipe bursting upsize from 24-inch diameter pipe to 32 and 34-inches in spite of daily rains and special requirements of working in a Trinity River recreation area this past April. The job was part of a larger Arlington and Fort Worth, TX, wastewater sewer upgrade project undertaken by general contractor, Mountain Cascade.
Newell added that “I’d say it ranks as one of the more difficult jobs we’ve done. It certainly demonstrates what pipe bursting can do, where it can be used.”
The six runs totaled more than 1,800 linear feet. Five of the runs replaced 24-inch-diameter pipe with 32-inch HDPE. A sixth pull of 300 feet replaced the 24-inch RC pipe with 34-inch HDPE – a five-step upsize. This feat was the largest diameter pipe burst and upsizing by No-Dig Tec using HammerHead Trenchless Equipment’s tooling to date.
Mike Walk, the HammerHead ram and burst specialist who had come down from the company’s Oconomowoc, WI, headquarters to observe the burst, said, “I knew our bursting tools would go the distance. But the speed No-Dig was getting? They were moving an expander head of nearly 38 inches through 24-inch-diameter reinforced concrete at a foot a minute. I’m very happy with how the equipment performed for them.”
For five 200- to 325-foot bursts, No-Dig Tec placed the 38-inch expanding head fabricated by HammerHead specifically for this job ahead of a 26-inch pneumatic bursting tool. The tool was guided by a 20-ton HydroGuide HG20 cable winch pulling from the exit pit. The string was backed up with a 20-inch pneumatic tool on the pipe’s trailing end as a “kicker.”
No-Dig Tec teamed two 1,600 cfm compressors guaranteeing at least 2,200 cfm at 110 psi to drive the 26-inch hammer at 122 beats per minute. A third, 750 cfm compressor powered the 20-inch kicker pushing from behind.
The guiding cable will be kept at a steady 16 tons during the pull. It runs through the 24-inch pilot with splitting blades and 38-inch burst head to the pneumatic hammer inside the burst head. The 32-inch pipe connected to the burst head trails along behind, receiving a push from a 20-inch “kicker” hammer placed at its tail end.
Newell calculated that the 32-inch HDPE weighed 4,500 pounds per joint. On the longer pulls, he said, “the total weight of pipe and tooling being moved through the pipe was 60,000 pounds – and that’s not counting the force to overcome the existing pipe’s resistance.”
The pipe lay at a depth of about 15 feet. Entrance pits were excavated to 60-feet long by 10-feet wide and 15-feet deep. The extraction pits were 36-feet long by 10-feet wide and 15-feet deep.
Complicating factors
Though the equipment had no trouble making the pulls, half of the replacement job ran through a Trinity River park in Arlington. The jobsite’s nearby residential properties, highly valued trees and natural landscape required great care during the pull. Narrow pathways were created to allow equipment access. They were covered with lumber and a minimum of 5 inches of wood chips with temporary fencing along the sides.
Select trees were protected with picket shielding banded around the trunks. Then they were fenced off. Deflection posts were installed where there was any potential that machinery or pipe might come in contact with them during burst preparation or the burst itself.
A 38-inch bursting head is more than half the height of most crew members. Replacing 24-inch reinforced concrete pipe with 32- and 34-inch HDPE is the largest diameter burst and largest upsize No-Dig Tec has performed to date.
Forty-years ago the 24-inch RC pipe had been installed in trenches that meandered sharply around the trees. At the RC pipe offsets, which were made to form curves in the sewer line, installers had poured cement over the joints. Some of the cement intruded into the pipe.
Newell said that although digging was not permitted to identify these joints, he could tell when the expanding head encountered each one because the pipe bursting operation would suddenly slow to a fraction of its progression rate. As soon as the tooling had fractured and compressed the broken pipe away to the sides, the pull resumed its pace.
In places where the bends were judged to be too sharp to “push the limits,” Newell said, the runs were terminated. At these points Mountain Cascade created manholes to form junctions for the runs.
Careful orchestration
Newell emphasized just how well this project demonstrated the confines in which a burst this size can take place. The lengths of 32-inch pipe had to be fused offsite and then towed to the park’s limited work area, a pathway not more than 10 to 12-feet wide in most places.
Newell said that although each burst took only one day, each required at least a week of site and pit preparation. “Dirt had to be moved off site as we went, and then brought back when we were done. I had hoped to use 300 and 350-series excavators, but due to the access limitations, we had to shift down to 200-series in size.” Newell said the equipment consisted of two of the 200-series track excavators, two rubber-tire back hoes, one rubber-tire front-end loader and two 145 mini-excavators. “And even then it was a tight fit.”
Orchestration of equipment prior to conducting the pull was critical. “Due to logistics here, if you screw up the order, you’ve basically just lost a day’s work,” Newell said. If any one part of the lineup went in out of turn – pumps, compressors, tools, excavators, backhoe and pipe – all of it would have to be removed one at a time and the piece-by-piece lineup would have to start over.
Newell trusted organization of the pulls to 25-year veteran pipe burster Allan Woodruff. Walk, had worked with Woodruff before and said that he was one of the best pipe bursters in the business. “His retention, his procedural expertise and his attention to detail are second to none. He knows what he’s doing.”
Project owners requiring trenchless pipe replacement often limit bidding to those companies who meet specific experience requirements. No-Dig Tec’s expertise in this niche service makes it one of the few companies qualified to bid on jobs like this one, which was completed in April.
FOR MORE INFO:
No-Dig Tec, (972) 488-9910, http://texaspipebursting.com
Hammerhead (Earth Tool Corp.), (800) 331-6653, www.hammerheadmole.com
Comments