October 2014, Vol. 69, No. 10
Editor's Log
When Research Dollars Return
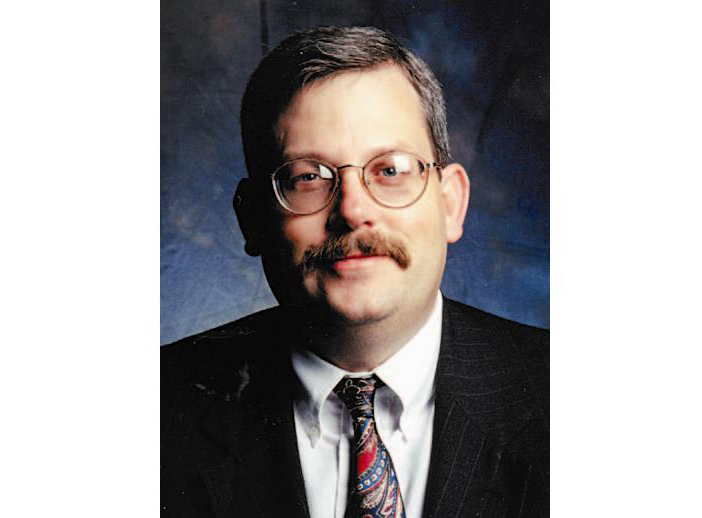
Federal standards for off-road diesel engines were first adopted in 1994 for engines over 50 horsepower and called Tier 1.
Further developments led to the 1998 EPA final rule that introduced Tier 1 standards for equipment under 50 horsepower and increasingly more stringent Tier 2 and Tier 3 standards for all equipment with a phased-in schedule from 2000 to 2008. On May 11, 2004, EPA signed the final rule introducing Tier 4 emission standards, which started phased acceptance in 2008.
T-4 work continues to wrap up but should be completed in 2015. However, as any manufacturer will tell you, it wasn’t a simple process and there is still a lot to do. Tier 4 didn’t require just development of new engine emission systems; rather the added size forced companies who purchased their engines from OEMs to redesign their equipment as well to accommodate size differences and new widgets. Often this required a major equipment overhaul. Equipment of all sizes, little or large, was impacted and manufacturers have spent years reinventing their products. Equipment ranging from compact excavators and directional drills and all the way in size up to massive excavators or track trenchers, had to be redesigned to fit Tier 4 engines.
The good news is that work is winding down. By now, manufacturers have systems in place to match their engineering philosophies and preferences, as well as what works most effectively and affordably for their budgets. If a company hasn’t embraced Tier 4 yet, they are currently racing to do so or they’ll be out of business soon – the EPA doesn’t mess around.
Also, from the consumer point of view, customers have had a few years now to understand that the result of Tier 4 doesn’t just mean improved fuel emissions, but also that equipment prices have necessarily had to climb. Fortunately for manufacturers, sticker shock is beginning to fade.
Tier 4 is potentially a big win for the environment. But besides increased equipment prices, what are the other costs of Tier 4? Getting to Tier 4 final for both engines and equipment has carried a tremendous research and development cost for manufactures. In fact, R&D budgets have largely been consumed by solving first Tier 1 and then Tier 2 through Tier 4 Final design equations. Engine and equipment manufacturers have done a magnificent job of finding a variety of workable, effective and, as affordable as possible, solutions for industry. Steadily working on meeting the benchmark EPA standards for 20 years could quite possibly be the costliest mandated compliance problem ever solved by the construction industry.
With the volumes of R&D budgets dedicated to meeting the various engine emission tiers, monies that would have been sunk into new project or technology development has often had to take a back seat. The result is that much innovation has been stifled.
That’s not to say that new products and technological development has been totally throttled over the last 20 years. There have been remarkable jumps and exciting new directions for all kinds of equipment. For example, hybrid and electric equipment is now becoming more practical. Telematics is finally reaching critical mass. Other areas will develop and follow.
It will be very interesting to see what develops over the next 10 years now that those crucial R&D dollars can now be poured into technology to improve and innovate not only the equipment itself, but in making that equipment work more efficiently, productively, safely – even more environmentally friendly.
Just think where we would have been if the billions dedicated to the tier programs had been invested differently. Hopefully, it was money well-spent but history will have to judge that. I do believe that we now stand on the precipice of a technological renaissance that hasn’t been seen in the construction industry for . . . well, 20 years.
Comments