May 2014, Vol. 69 No. 5
Editor's Log
Labor = Video Games & Automation?
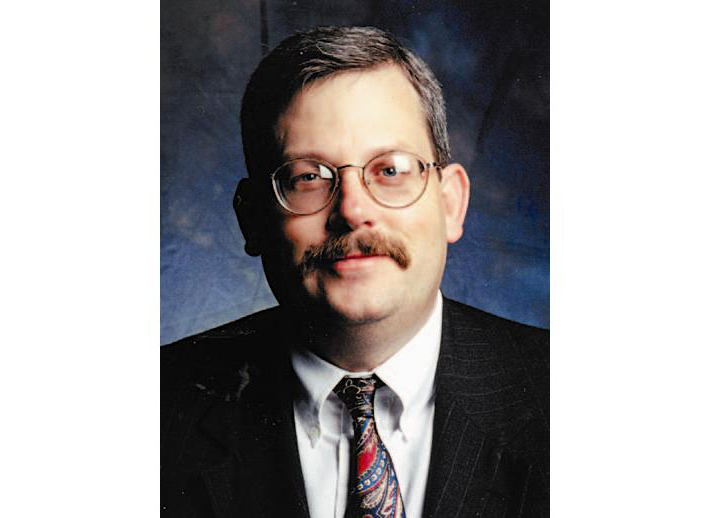
I’ve received a variety of interesting comments and reactions regarding my March 2014 Editor’s Log entitled “Labor: Inhibitor To Growth?” That column discussed the ongoing shortage of skilled labor in the underground utilities/pipelines construction and rehabilitation industries. It created an interesting dialogue.
At a time when so many Americans are still seeking good jobs and careers, it is almost criminal that opportunities in the utility and pipeline industry go unrealized. One of the more frequent comments I’ve received is that too many young people today have the perception that working in these fields are low-class, blue-collar jobs. They feel entitled to a perceived high-class, white-collar career. As my father, and others, have said throughout the years, any job that pays the bills, puts food on the table and supports your family is a good job.
The truth is that not everyone is cut out for office work though the perception is that such a path is a better career choice. The underground infrastructure industry must get past these misconceptions and ill-conceived attitudes. A satisfying, solid career with good wages and benefits is desirable whether in the dirt or in a sky scraper. And for many parts of the country (the rust belt comes to mind), those kinds of jobs are worth their weight in gold. Of course, there are also a tremendous number of management and engineering careers available in our market.
Regardless, the struggle continues to attract and retain qualified personnel. Underground Construction will continue to address this issue.
One of the common complaints we hear as parents and grandparents is how our children have become too engrossed in the home and on-line video gaming world. Indeed, such video adventures permeate our society at every level. My four-year-old granddaughter can (and has) downloaded and filled my tablet with her games from all sources. She even knows the ones that require payment. She gets everything set-up and then asks grandpa for his password, hoping to sucker me with her sweet ways! My two-year-old grandson is not far behind. It is indeed a bold new, digital world for the young.
My grandchildren are natives to the new digital reality of our culture while older generations remain as immigrants to new technology, having to learn from scratch when needed, but rarely comprehending the digital technology to the degree of our younger counterparts.
This situation, combined with labor shortages, has not been lost on machine manufacturers. One effective solution in addressing our industry’s dearth of qualified labor is with an aggressive automation program for traditional, big iron equipment.
At recent equipment introductions, I sensed a largely unspoken, yet obvious trend as improvements were announced: new equipment is more sophisticated yet easier to adapt for younger people who are adept of hand-eye coordination (via modern video games, etc.). The equipment is designed to make intuitive decisions. Modern telematics allow an employee to monitor all kinds of data while sitting behind a computer across the country. Such innovation dramatically reduces learning curves, error margins and broadens the scope of qualified job candidates.
Additionally, big iron today is designed to a very high degree of ergonomic comfort which makes operating heavy equipment much more tolerable. Combine that with the comfort zone of operating equipment in a manner not unlike what many have been doing for years with digital equipment, and you’ve got a much more attractive career for potential employees.
Automation has another beneficial component as well – safety. Anything manufacturers can do to put workers out of harm’s way is always a positive. For example, Vermeer now has track trenchers that can be operated by remote control, effectively removing operators from their traditional over-the-trench cab position. Similarly, Sharewell HDD’s Cleat system securely and quickly locks a drilling rig in place, avoiding unforeseen and sudden movement of the rig during drilling/pullback operations, increasing the safety factor for the operator dramatically. Time will tell if these innovations are as effective as traditional operations and gain wide-spread industry acceptance and support, but they are definitely a step in the right direction.
I’ve no doubt that the future of both equipment and the workforce will rely heavily on the ability of manufacturers to automate machinery and expedite the training curve.
Comments