June 2014, Vol. 69, No. 6
New Products
Centrifuges Greatly Enhance Fluid Recycling
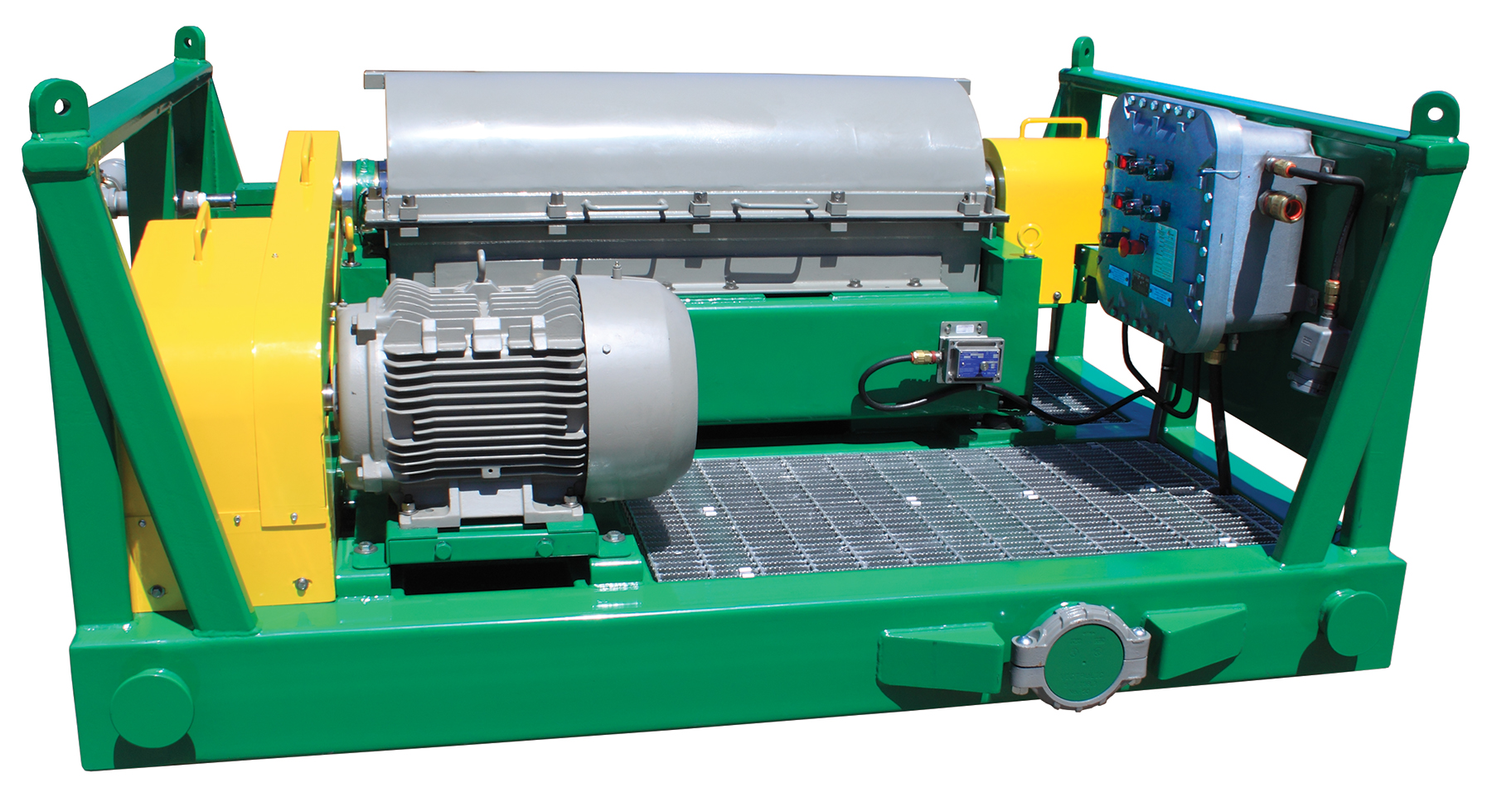
Drilling fluid additives and the water that contains them are an essential part and expense of successfully completing a horizontal directional drilling (HDD) installation, and the longer the bore and larger the product being installed, the more drilling fluids cost.
Therefore, it makes economic sense to recycle drilling fluids by removing cuttings and recirculating the cleaned fluids.
HDD fluid recycling technology has been adapted from the oil and gas drilling industry where it has been used for several decades. Today, projects employing midsize and even small drill rigs use separate fluid mixing and recycling systems. Most big projects use recycling packages that mix, pump, clean and recycle drilling fluids with equipment using a combination of screens, centrifugal pumps and hydrocyclones to remove the cuttings from the fluid.
Many drillers now are adding a new component to drilling fluid cleaning and recycling systems – a centrifuge.
“Integrating a high-speed decanter centrifuge with a conventional drilling fluid cleaning system removes ultra-fine solids that traditional shakers and hydrocyclones can’t remove,” said Michael Rai Anderson, P.E., president and chief executive officer of Kemtron Technologies. “This allows the driller to better manage drilling fluid weight. In theory, properly integrated centrifuge technology allows for the indefinite recirculation of drilling fluids.”
Kemtron is a leading manufacturer of drilling fluid cleaning and circulation systems, including centrifuges.
Anderson said with conventional mud cleaning systems, drilling fluid initially passes through the linear motion shale shaker capable of handling 100 percent of the mud pump, typically removing coarse-sized solid particles greater than 100 microns. The drilling fluid then passes through desander and/or desilter hydrocyclones for further removal of fine and silt-sized solid particles, ranging in size between 250 to 100 microns.
Centrifuge boost
Adding a high-speed, solids control decanter centrifuge removes ultra-fine drill solids of greater than 2 to 5 microns at an average process rate of approximately 20 percent of the mud pump flow rate, Anderson continued.
“Centrifuges can improve the cut point by a factor of six times when compared to a prototypical shaker/hydrocyclone system and can dramatically increase drilling fluid life,” he said. “Kemtron has experienced applications utilizing centrifuges in cooperation with the standard solids control equipment in which drilling fluid life was increased by a factor of 10.”
A centrifuge also can be used as a barite recovery system or dewatering system, a practice widely used in the oil and gas industry. The dewatering process, said Anderson, allows up to 100 percent removal of all suspended solids from the drilling fluid. The reclaimed water can be used to make up new mud for another job or as rig wash-down water.
However, the use of a centrifuge is not appropriate for every HDD project.
“It comes down to drilling fluid volume and the complexity of the drilling fluid additives used,” said Anderson. “Small jobs might use 100 to 300 gallons per minute of circulating drilling fluid. Consequently, Kentron’s experience has been that the break-even point for a centrifuge-enabled system is for longer, wider-diameter bores requiring at least 400 gallons per minute of recirculation.”
Drilling fluid “life,” he added, is dependent on the particle size distribution of the
solids generated and the degradation life cycle of the solids within the drilling fluid.
Anderson said that incorporating a centrifuge into a recycling system has benefits in addition to fluid savings, such as increased production.
“Studies have shown,” Anderson continued, “that the lower the colloidal solids content in a water-based drilling fluid with particulates in sizes less than 2 microns, the faster the rate of penetration. Minimizing colloidal solids lowers the plastic viscosity of drilling fluid, contributing to greater horsepower at the bit.”
More benefits
In addition, he explained, cleaner fluids reduce wear on pumps and wear seals, contributing to longer equipment life.
“Oil and gas drillers utilize the centrifuge to minimize waste and to manage the weight of the mud prior to recirculation,” said Anderson. “It has only been over the last decade that HDD companies have been adopting such systems into the HDD drilling operations.”
Kemtron currently manufactures three centrifuge models for HDD applications. Several companies offer centrifuges for HDD work, some are available for rent.
“However,” Anderson said, “of all the HDD mud reclaimer manufacturers, Kemtron is one of the only companies that manufactures both packaged mud systems and centrifuges. Contractors routinely shop multiple companies to put together packages that we already offer – Kemtron has a product line that incorporates conventional drilling fluid recycling equipment and centrifuges into one integrated package.”
Anderson foresees continuing growth in the use of centrifuges on HDD projects.
“We continue to see new records for long HDD bores, exactly the type of project which can realize maximum benefits from including centrifuges in cleaning and recycling systems,” Anderson concluded. “For many jobs, a simple mud system is not enough. Adding a centrifuge is a step in the evolution of mud systems to meet changing demands. Environmental issues also are a factor as regulations become more stringent regarding disposal of drilling fluids.”
Kemtron Technologies is based in Stafford, TX and since 1990 has been providing solids control and dewatering equipment to a global market. Kemtron products include mud mixing, recycling, dewatering, and closed-loop water reclamation systems for HDD, oil and gas, geothermal, water-well, environmental remediation and mining industries.
FOR MORE INFORMATION:
Kemtron Technologies, (888) 536-8766, http://kemtron.com
Comments