June 2014, Vol. 69, No. 6
Features
Joint DCA/AGA Workshop Bolsters Contractor/Operator Relationship
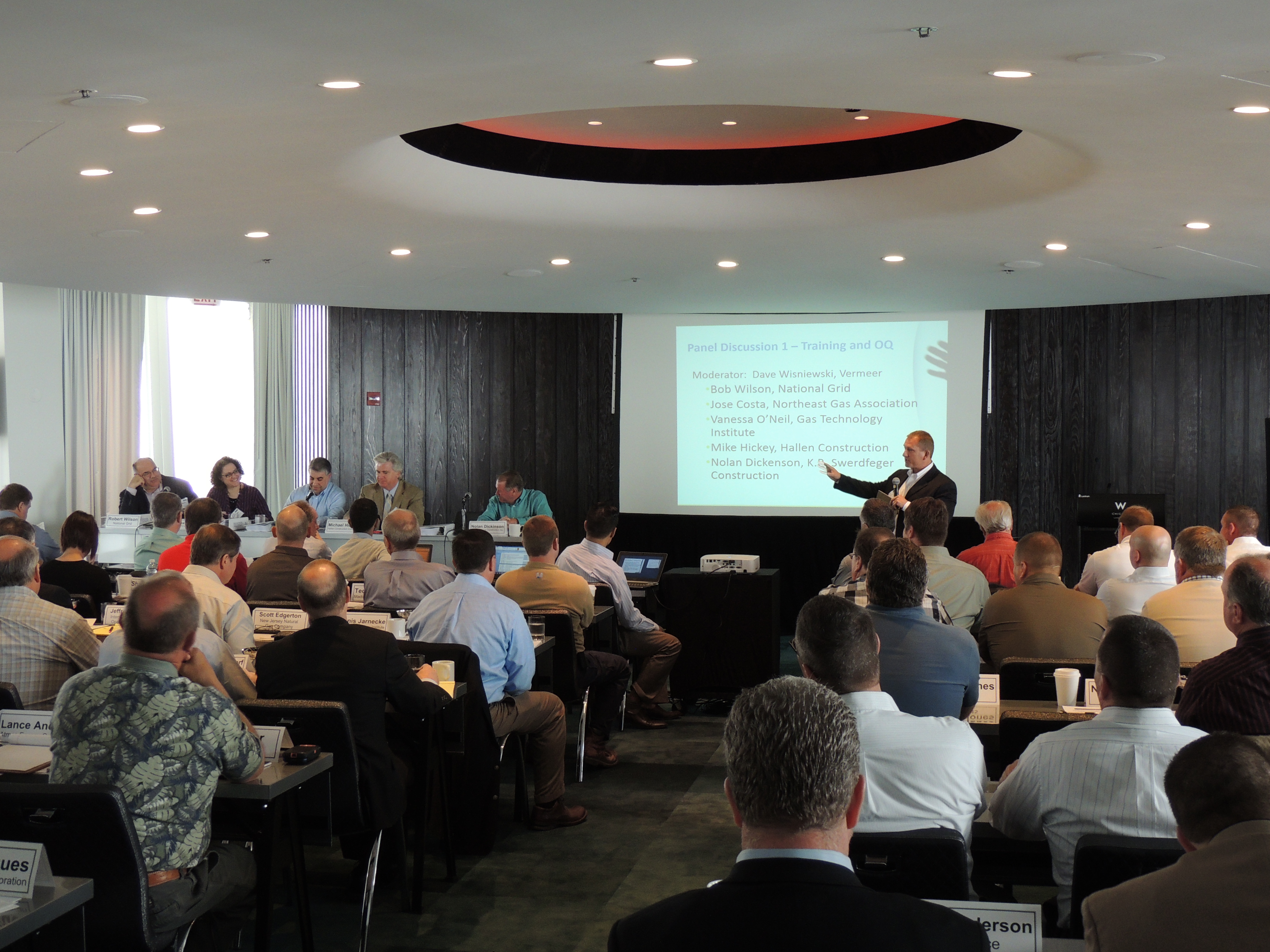
Gas utilities and the contractors that work for them, together build the infrastructure that delivers safe and reliable gas to countless American’s every day, in a cooperative process that requires experience, trust and continuous communication.
According to the American Gas Association (AGA), of the 71 million residential, commercial and industrial natural gas customers in the U.S., 92 percent, or 68 million customers, receive their gas from AGA members. Building the infrastructure needed to meet that capacity requires strong working relationships between operators and contractors alike. While these relationships currently exist in the gas distribution industry, improvements in communications and operations can always be made, thereby strengthening cooperation even further.
On April 29-30, the Distribution Contractors Association (DCA) held a Utility Contractor Workshop with the American Gas Association (AGA) in Chicago, for what turned out to be a packed day-and-a-half forum featuring speakers, moderated panels on a variety of subjects, breakout sessions and open discussion among some 130 representatives of gas utilities, contractors, manufacturers, labor unions, industry experts and the federal government. While a broad range of topics were discussed and progress was made on a host of issues, one thing was clear in the end: this forum is only the beginning of what will hopefully lead to a regular industry event.
Vast construction workload predicted
The workshop was kicked off by an informative presentation by Mark Bridgers of the Continuum Advisory Group, which provides management consulting to energy stakeholders involved with development and capital asset construction. The presentation focused on the past and expected investment in pipeline infrastructure from 2008 through 2031 and the drivers behind this investment. A geographic description was provided about the job creation and economic benefits that are resulting from the shale energy boom, including the current renaissance in American manufacturing, and how operators and contractors must be prepared to meet the rising demand.
Continuum expects three waves of pipeline spending over the next 20 years followed by a possible flattening of investment after distribution infrastructure is replaced. The continued shale energy phenomenon and anticipated replacement in steel, cast iron and plastic pipeline systems could mean hundreds of billions of dollars investment to expand the nation’s pipeline capacity. It was clear at the end of the presentation that strong relationships between operators and contractors are needed now more than ever, and the discussion served as an effective segue to the workshop’s panel discussions and breakout sessions.
OQ, portability
The first panel featured representatives from National Grid, Northeast Gas Association, Hallen Construction Company, K.R. Swerdfeger Construction Company and the Gas Technology Institute (GTI). The panel focused on effective training programs and how they relate to, and are distinguished from, programs and methods to comply with often varying operator qualification (OQ) programs maintained by gas operators. DCA members are continually frustrated by the lack of portability of their OQ programs, and believe that consistency is needed so they may carry them from operator to operator. Because of the high level of interest, this panel ran over and the discussion continued into the breakout sessions.
Utility commissions are beginning to require third party participation in the OQ process, and many expect those requirements to extend to other regions of the country. In the Northeast, stakeholders including GTI, the Northeast Gas Association, National Grid and several contractors have collaborated to develop a regional qualification pilot program that includes providing certified instructors who deliver standardized and condensed content on “consistent construction practices.” Panelists encouraged gas operators to stop thinking in terms of “compliance” with OQ requirements and adapt to the ever changing regulatory and business environment. This includes procedural and technical improvements, combining classroom with computer training before taking education to the field where use of various tablets (Android, IPhone, etc.) and industry practices must be continually updated.
While panelists understood that the specific model used in the Northeast may not work across the country, many in the audience agreed that conversation about the collaborative process should be taken to other areas where regional gas associations exist.
There was ample discussion about “training” versus “qualification.” There seems to be a substantial amount of pushback from operators when asked about standardization of covered tasks and the OQ requirements subject to them. Operators were encouraged to understand that “doing the right thing” includes a willingness to change and begin working more closely with their contractors on training and qualification programs.
Contractors generally agreed that more communication and cooperation is needed, and expressed that they don’t take their OQ responsibilities lightly. Contractors often keep workers in the field under observation until they are deemed prepared to undergo a qualification process. Then, classroom and computer-based training is combined with “real life” training scenarios. The underlying sentiment on the contractor side was that while classroom and computer training is key, there is no substitute for on-the-job training in the field.
At the same time, both operators and contractors are in need of more information from regulators about a variety of subjects, including whether contractors should be empowered to qualify their own people, whether requirements for a third-party role in the OQ process should be expected nationwide and what types of technologies will be needed in the future. Big concerns about liability related to transferal of OQ records from operator to operator remain in the contractor community.
One thing that operators and contractors were in complete agreement about is the need to reach out to the next generation of workers in the gas distribution industry. Because of misguided negative perceptions about the potential for success in the construction industry and the need for a four-year college degree, the industry has to break through these stereotypes and recruit talent in the next-generation workforce. Efforts to approach young people in technical and vocational schools, community colleges and other audiences are happening now and need to continue.
Changes in work procedures
A panel moderated by Continuum then discussed the drivers of work procedure changes and evaluated if the frequency of change is accelerating, decelerating or staying the same versus historical trends. Representatives from DCA’s Miller Pipeline and Hallen Construction joined panelists from NW Natural and Dominion East Ohio to share experiences on practices that have been implemented to help share updated work procedures and enhance communications between operators and contractors.
It was clear across this panel that significant work procedure changes are taking place more frequently today. The main driver of these changes is increased regulatory requirements, such as those from the Pipeline and Hazardous Materials Safety Administration’s (PHMSA) Distribution Integrity Management Program (DIMP) rule as well as ever-changing state and local regulations. Rising demands on municipalities and development of new and improved technologies can also dictate changes in construction company policies.
Both operators and contractors agreed that most changes in procedure are either forced through regulation or, if voluntary, are done so to preempt pending regulation. Changes in standard operating procedures (SOP) are passed down from operators to contractors and both sides have to work together to fully communicate expectations and what is needed to meet them at an affordable cost. Industry groups like DCA and AGA can play a role in facilitating this cooperation, but it is incumbent on individual operators and contractors to work in good faith to ensure that everything is on the discussion table.
The panel also talked about best practices in rolling out changes in work procedures and efficient ways to ensure that the information is implemented and retained. A variety of methods are used, including face-to-face meetings, teleconferences, training sessions, job-site communication, CDs, thumb drives and e-mail. Contractors on the panel indicated that roll-out approaches are usually e-mail driven and that often not enough information is provided for a contractor to effectively sort things out. It was expressed that as technology improves and we enter a “tablet” culture, changes in procedures will be increasingly sent directly to those in the field doing the work.
Finally, the Work Procedures Panel discussed approaches to ensure compliance with revised work procedures once they are rolled out. Operators usually depend on their inspectors to ensure compliance. If problems arise, communication with the contractor’s leadership and corrective action is employed as necessary. Gas operators commonly look for contractors who are fully qualified to perform all aspects of pipeline construction and back their work up with regular training for their personnel.
Gas operators said that once work procedure changes have been communicated, contractors are generally expected to comply with any and all changes in code, regulation or company policy. Contractor panelists agreed but said utilities sometimes need to do a better job in fully communicating changes in operation, personnel, and all peripheral expectations. In the end, increased partnership and cooperation was considered the best way to introduce, roll-out and ensure compliance with changes in work procedure.
PHMSA topics
Annmarie Robertson of the PHMSA then provided a broad description of the agency, the pipeline network under its jurisdiction, and the anticipated regulations on the horizon for the gas distribution industry. Many attendees were surprised to learn that distribution systems comprise of 81 percent of the some 2.6 million miles of pipeline regulated by PHMSA. Although the agency tries to employ a risk-based regulatory approach as well as inspection processes, the 2011 incident in San Bruno, CA, has brought increased scrutiny to the agency and the pipeline industry in general.
Regarding the regulatory climate in relation to the expected uptick in workload, PHMSA is encouraging state programs to plan for extensive pipeline infrastructure work. The agency believes that considerable repair, rehabilitation and replacement is needed for “high-risk” pipeline infrastructure, including cast iron mains, plastic pipe installed between 1960 and 1980, unprotected bare steel, copper and older pipe with inadequate records to verify integrity.
Robertson said PHMSA hopes to release a final rule on state damage prevention enforcement before the end of the year, and believes the rule will lead to necessary adjustments to state laws and damage prevention programs that currently include no or inadequate enforcement.
Tackling industry priorities
Three breakout sessions were held in the afternoon of the first day of the workshop, where all attendees were invited to weigh-in on key issues addressed by both utilities and contractors. Moderators oversaw discussions on the following areas:
Training and Qualification – Participants continued the discussion about effective approaches to training and operator qualification, emerging technologies that are enhancing the effectiveness of OQ programs maintained by operators and contractors alike, the need for more consistency in OQ compliance, and the overall effort to recruit the next generation of workers in the distribution construction industry.
Quality Assurance – This session focused on operator inspection and other quality assurance methods, both during and “post job.” Participants expressed the need to focus on the quality of inspector versus the percentage of total inspections, and how all information should be passed on from operator to contractor. In order to reduce inspector bias, third parties were reminded that investigation, root-cause analysis and corrective action should always be optimized. The ever-increasing problem of addressing cross bores was repeatedly cited as a main reason for effective quality assurance.
Worker Safety – This safety breakout focused on damage prevention, specifically on first and second party damages. Increased use of directional drilling and the general uptick in gas pipeline construction has led to an increase in first and second party hits. Contractors pointed out that a key issue surrounds who is performing the utility locate (contractor or contract locator). Participants also discussed issues related to billing, addressing ‘untonables,’ efforts to mitigate cross bores and other important topics.
Contractor oversight, management
DCA members Michels Corporation and ARB Inc. joined AGL Resources and Southwest Gas on a panel that evaluated practices gas utilities used to monitor the quality of work performed by their contractors, and how contractors feel utilities can improve quality assurance programs that would better meet their intended results. While several performance metrics were offered and thoroughly discussed, the general agreement was again that consistency, communication and cooperation between operators and their contractors win the day.
Depending on the size and experience of the contractor, gas operators try to maintain a centralized oversight program when possible. However, some factors call for state-specific requirements in certain areas. Operator reps on the panel said that when measuring contractor performance, everything should be on the table, from OQ records, work history to general consideration of their current working relationship. Risk-based analysis is commonly utilized, and it is imperative that when problems arise, operators communicate what went wrong and how to fix the problem. Specific metrics are used, but communication is everything.
When asked how gas utilities can help contractors with oversight, contractor panelists suggested that providing quality inspectors and employing a consistent inspection process is important. Focusing on the entire project rather than on specific inspections would also increase project effectiveness, as would ensuring enough inspectors working on a site to avoid project delays. Generally, if contractors know what is expected by the operator and that the operator will provide the people needed to mitigate possible conflicts and inconsistencies, they can get the job done effectively and comfortably. Once again, forging and enhancing working relationships is paramount to establishing this environment.
1st and 2nd party damages
In the final panel of the event, Duke Energy, Questar Gas, Mears Group/Infrasource and Michels Corp. discussed the recent increase in first and second party damages and how operators and contractors can work collectively to reduce these incidents. Directional drilling practices were a focus of the discussion, as was the often neglected issue of operators ensuring quality locates of their facilities.
Interestingly, gas operator panelists said they either did not track their first party damages, or had incomplete records of them. Contractors noted that although they may have facility hits, the vast majority are “third party,” or damages on an outside facility with an overwhelming percentage being unmarked or mismarked buried utilities. A very low percentage of contractor damages tend to be on the gas facilities they work on.
The issue of facility locates was a key discussion point in this panel. Although some contractors agree to locate the gas facility when bidding the project, most rely on the operator to locate and mark the facility as that is the operator’s primary responsibility in the damage prevention process. However, many contractors will verify the accuracy of these locates for safety reasons as it is usually the contractor who is closest to the hazard.
When asked what gas utilities are doing to ensure the accuracy of their utility locates, a variety of responses on the panel and in the audience revealed some very different approaches. Some operators employ extensive locator training and oversight. For example, one panelist described a process where locators are regularly audited and subsequent meetings held with the utility and even contractors to address problem areas. In other cases, operators provide no such assurances and address problems with inaccurate locates after the fact. Obviously this reflects varying philosophies and damage prevention priorities among gas utilities.
HDD practices were extensively discussed. After refuting common misperceptions about HDD and those engaged in it, contractors on the panel assured the audience that for the most part, those involved with HDD are experienced and put to work only after extensive training and preparation.
Long-term conversation
After lively discussion on a wide variety of important topics, DCA and AGA members left the Windy City with a lot to think about. Several issues were addressed that had not been openly talked about before, and progress was made on some longstanding issues between gas utilities and their contractors. While there was plenty of disagreement and lots of work left to be done in the future, it was clear that this forum worked and the conversation should continue.
“DCA applauds the AGA for reaching out and developing the structure and agenda of the workshop collectively with us,” said DCA Executive Vice President Rob Darden. “No doubt this cooperative approach was a main reason for the outstanding turnout at the event. We look forward to holding more of these workshops in the future – it’s this kind of open forum that leads to increased communication, cooperation and ultimately, a higher level of safety and effectiveness. “
FOR MORE INFORMATION
Distribution Contractors Association, (972) 680-0261, www.dca-online.org
American Gas Association, (202) 824-7000, www.aga.org
Comments