January 2014, Vol. 69 No. 1
Features
Maine Moves Ahead On CSO Projects
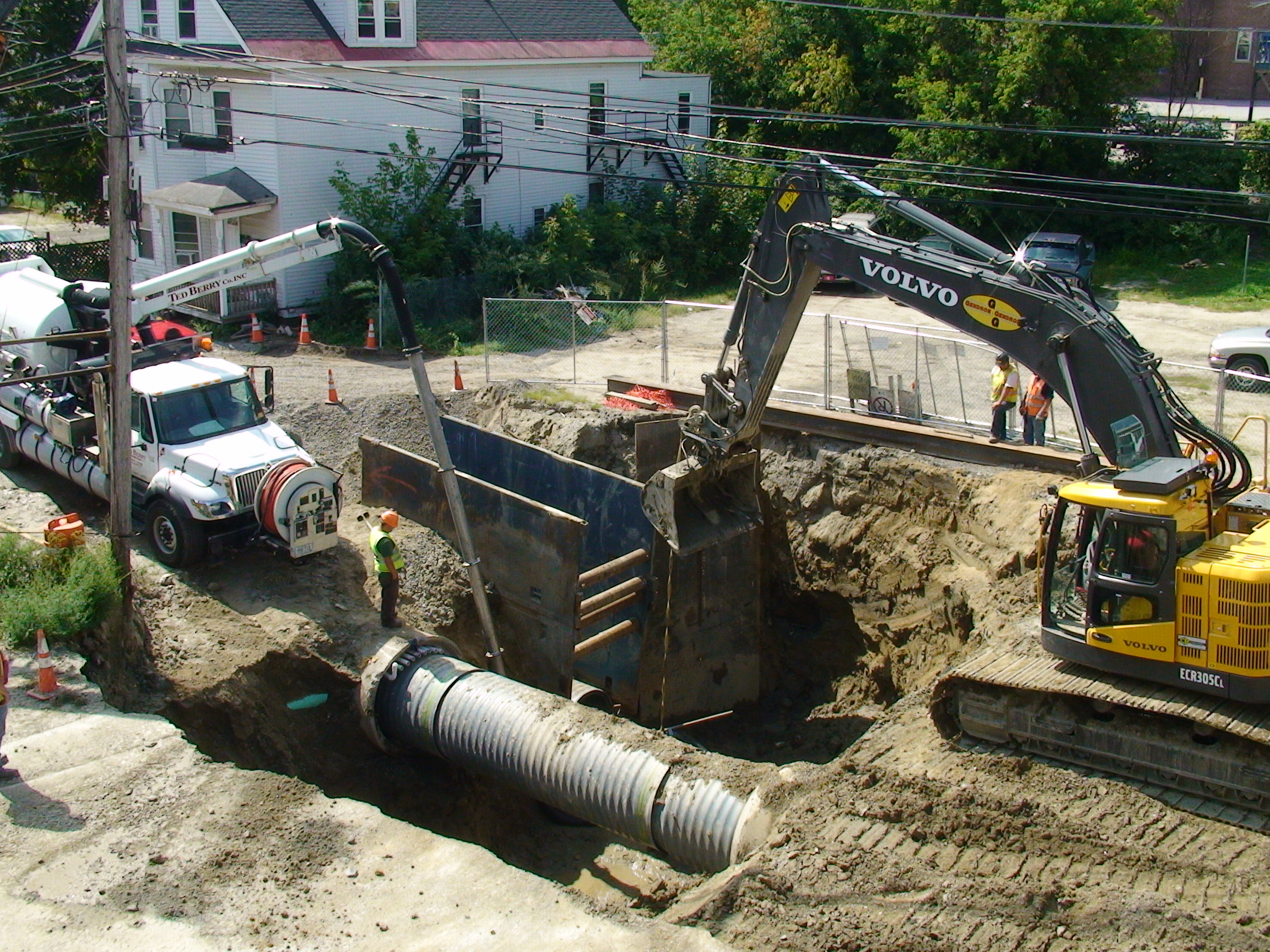
A trenching project for a new, combined sewer overflow (CSO) separation pipeline in Lewiston, ME, led to an unexpected, emergency sliplining of a sanitary sewer line. The job also had other challenges which included a massive rock ledge, old buildings virtually on the edge of the trench along with the existing sewer that was found to be leaking effluent.
The Oak Street – Phase III Project is the third part of the city’s CSO master plan. This new piping separates storm water from the existing sanitary sewer system in order to relieve capacity stress on the treatment plant and meet Maine Department of Environmental Protection requirements. With a population of 37,000, Lewiston is the second largest city in Maine and is part of the Portland-Lewiston-South Portland combined statistical area.
“There are five phases to our CSO work,” stated Jeffrey D. Beaule, P.E., project engineer for the city of Lewiston. “We just finished Phase IV, but the Oak Street – Phase III portion was probably the most challenging. This is because of the location of the pipeline, the unexpected sewer rehabilitation and the geological make-up of the area.
“One of the biggest problems we had on this job,” Beaule explained, “was the rock ledge we had to go through. The buildings were right at the back of the sidewalk plus we had a gas main right next to that old sewer so we couldn’t blast. They had to manually hammer 370 cubic yards of rock ledge out of there. All of that and the added sewer interceptor sliplining put a lot of pressure on the projects construction schedule.”
During the course of installing the new pipe, an old 60-inch diameter concrete sewer line was found to be leaking and needed to be replaced. As an alternative to replacing the sewer pipe, it was sliplined using the same type of pipe being used for the new storm water line — SaniTite HP pipe from Advanced Drainage Systems Inc. (ADS). Additionally, the company’s N-12 corrugated high-density polyethylene (HDPE) pipe was used for some other sections of the storm drain pipeline and smaller diameter SaniTite HP was used for new sanitary sewer piping.
“Originally this project went out to bid with concrete pipe for the projects storm drainage piping and SDR-35 for the new sanitary sewer piping,” Beaule continued. “ADS came to the pre-bid meeting and educated us on the benefits of utilizing the SaniTite HP after the great results Portland, ME, has had plus an economic advantage and installation benefits. With this, SaniTite HP was allowed as an alternate and we ended up going with it for the project as the contractor bids came in. It turned out to be a really versatile pipe because it could be ordered pretty much any way we needed it, including lengths and fittings at virtually any angle.”
Neighborly advice
A CSO Separation project in nearby Portland helped Lewiston gain comfort with the SaniTite HP pipe. The project used the 60-inch diameter, high performance polypropylene pipe to increase conveyance capacity, replacing a smaller 100-year old vitrified clay line. The new line separated a parallel 10-foot diameter combined sewer, which now solely conveys storm water. Completed in October 2010 after just five months of construction, the Portland CSO abatement project used some 5,600 feet of 60-inch SaniTite HP pipe. The $4-million project resulted in a single larger diameter pipeline to eliminate combined sewer overflows at Capisic Pond Dam and stop untreated wastewater from flowing into the Fore River Estuary.
“The common thread is that both the Portland and Lewiston CSO projects were difficult jobs,” said Bob Pelletier of E. J. Prescott (Gardner, Maine), which provided the materials for both. “Basically, the Portland water/sewer separation and the project here in Lewiston found the ease of handling and assembling of the products made a big difference as far as cost savings in installation as opposed to concrete pipe.
SaniTite HP pipe available in 30- to 60-inch (750-1500mm) diameters with triple-wall profile construction meets ASTM F2764 specification requirements. It also provides a watertight joint, exceeding the requirements of ASTM D3212 with a dual-gasketed spigot design, and banded reinforced bells. The smaller SaniTite HP diameters, 15 to 18-inches, that were used for new sanitary sewer applications, meet ASTM F2736 specification requirements and are made with dual-wall construction to provide performance ratings that exceed all of today’s industry standards for gravity flow sanitary sewers.
“This particular Lewiston job had some deep, deep cuts. They were down 25 to 30 feet in certain areas.” Pelletier continued. “It was very challenging, especially for the maneuvering of the pipe because they were down so deep and one city block was only 40 to 50 feet across. You also have to haul off a lot of materials as in a city you don’t have a location to store it. Line up the dump trucks, load the material and send it off. Once they had the installation completed and compacted, they were able to haul all the material back in to reconstruct the roadway.”
Rock solid
For the overall project, the city contracted with Gendron & Gendron of Lewiston, a local construction company with a 42-year history in working with the city. “They usually save the ‘best’ for us,” said Todd Gendron with a smile. “The Oak Street job was the middle part of the city’s separation initiative and we had to match up with the elevation with what had been done a few years before. They stopped when they hit the rock ledge.
“That’s where we started – in the ledge. We couldn’t blast. There was a 60-inch concrete sewer two-foot away from where we had to put in this 42-inch and 48-inch SaniTite pipe and it was three-feet deeper than the bottom of the concrete sewer. We also had other utility lines. We brought in a drilling company to drill holes eight inches on center in an area 20-feet wide by 300-feet long and then we hammered out rock with a hydraulic hammer. When we first started it was just to put in 200-feet of pipe, and we hit solid rock which was nine-feet higher than the invert of the pipe, so we had to hammer out nine-feet deep and 55-inches wide.”
The ground conditions in Maine can vary literally from block to block. “About three years ago we did a storm water job about 18-feet deep but it was in clay on College Street – one street up from Oak,” stated Gendron.
Big job, little room
“On Oak Street the buildings were right on the edge of the hole, but we only lost one front porch,” he continued. “We were in a high-visibility, high-traffic area and had a dead-end street to contend with as well as dealing with gas mains, telephone lines and conduit, water mains and the 60-inch concrete sewer main that takes care of half the city. That is one of the main trunks for the city. If we broke that and it rained and we were at the wrong place at the wrong time, we would have gotten flooded. We really had to plan ahead and try to make it work, and if it didn’t you had to hurry up and figure what you had to do. ADS helped us a lot with unique fittings and excellent service in terms of product availability and fabrication,” Gendron said.
“We had to buy a special excavator – a Volvo 305. There are only three in Maine with no counterweight on the back so we could get by the buildings. We dug down three feet in the street so we could sit down in the hole and reach everything. If we opened the roof on the excavator, we’d hit the overhead wires. Another obstacle we had to overcome was the rock ledge and also the diameter and the weight of the structures plus going under that 60-inch concrete sewer.”
It took the Gendron six-member crew from April until November 2012 to install 800-feet of pipe. Typically, a ‘normal’ project of this size would take just a few days.
“The length of the pipe helped us a lot, however,” explained Gendron. “We used different lengths of pipe, 13 and 20-feet and some others. The 13-foot pipe gave me the reach so I didn’t have to have such a big excavator and we could use a 20-foot trench box instead of a 24-foot box. ADS also helped by making all the specialty fittings and the T-Bases. The job was originally designed for concrete pipe and structures but for all the things that had to be done, if we were trying to do it with concrete, there would be no way to complete the project.
“When we designed the T-bases, elbows were made specifically for the holes on the top and we just poured around them. It was much faster than it would have taken with concrete and actually I don’t think it would have been possible to do the job. If you had to do those in concrete the weight would have been so much that you would have needed 100-ton cranes to set them, plus we didn’t have the room. Ductile iron would have been too big and heavy.”
The SaniTite pipe used was 15 and 18-inch diameter sanitary sewer, 42 and 48-inch diameter for the storm drainage along with another 400-feet of 48-inch for the sanitary sewer sliplining of the old RCP pipe. Additionally, the project used 12, 15 and 18-inch diameter ADS N-12 corrugated HDPE pipe for storm drainage collector piping. The company also helped with the design of the T-Base manholes that included pre-manufactured tees. “It was a doghouse structure with a six-foot diameter manhole around it and encased in concrete that worked out really well,” stated Beaule.
Angles and manhole
After all the connections were made, the trenches were backfilled with regular sand and gravel and rock that was brought back.
“We put in an 8-foot by 12-foot concrete manhole in the middle of one of the busiest streets in Lewiston,” Gendron continued. “They had to actually close down the street to make the connections – we had many different angles and turns. We had 90-degree and 45-degree connections and even 22-degree bends. We had to have pipe made so we could come up at a 45-degree angle and back at a 45-deree angle. It was like a big slide in the hole and how we did it was very intricate.”
“The CSO project was very challenging and very time consuming. When Todd and his crew got near an old 60-inch concrete transmission sewer main, they found the joints were leaking. They ended up having to install 400-feet of the 48-inch pipe to segmentally slipline and rehabilitate the sewer pipe,” explained Beaule.
“As the crew was digging alongside that old concrete pipe, the effluent was just pouring out of all the joints because there were no gaskets in the concrete pipe – it was a 50-year-old RCP pipe. With the effluent pouring out into the trench it was decided that we needed to do something quickly and sliplining seemed to be the best option since we already had a big hole opened. Matt Timberlake of the Ted Berry Company headed up that operation. Gendron helped them out with the excavation that was needed. Since we were installing a second storm drain for the CSO, we didn’t need the full 60-inch capacity of the old sewer, so the 48-inch pipe that we already had onsite worked perfectly. They just slipped it right through and it worked out great.”
The Gendron crew had to go under the 60-inch sewer with the new 48-inch pipe but the old pipe was leaking badly and they didn’t want to dig underneath it until it was rehabilitated. “What I saw was not one of the things that I wanted to be playing with,” emphasized Gendron. “The city called in the Ted Berry Company to slipline the 60-inch sewer. We worked with them, cutting through the concrete and later doing the laterals with InsertaTee connectors.”
The unexpected repair to the old concrete pipe sewer line was declared an emergency. “Within 72-hours from the time it was discovered we got the call, we were putting pipe in,” said Matt Timberlake of the Ted Berry Company, Livermore, ME. “Everything had to happen quickly. We’ve done a lot of work with the city with similar jobs and so they had a high level of comfort that we could design/build the project on the fly with some unknowns, yet go in confident that we would be able to stick to a budget, stick to a timeline and give them what they were looking for. They could have dug it up and replaced it. Or do a cured-in-place liner which is not something that you’re going to turn around in 72-hours.”
Process
A total of 400-feet of SaniTite HP, 48-inch diameter pipe was sliplined into the old concrete pipe with connections to 10 service laterals, including two 18-inch service lines using Inserta-Tee connections. Its triple-wall profile design reduces friction and along with its engineered bell and spigot joint allows for longer, uninterrupted pushing distances with lighter construction equipment.
“We saw an area where it would be reasonable to put in an insertion pit,” explained Timberlake. “We would insert the pipe upstream and terminate into a manhole that was in the middle of a very busy street and then slipline downstream and we connected in the middle.
“We were able to insert in two different directions from one pit and then bring those pipe sections together with a final connection in that pit. We essentially lined upstream into a manhole and then downstream into a manhole. The pit was about 30-feet long by about 12-feet wide at the bottom so that we could use the 20-foot SaniTite HP pipe to minimize joints.”
The upstream manhole was in the middle of one of the busiest streets in the city with a number of pipes that came together into that up-steam structure that could not be disturbed. The Ted Berry Company crew pushed the pipe into that manhole and under the busy street.
“Generally, a city can’t get everything it wants,” offered Timberlake. “They want it done quickly, they want it done correctly, and in a cost effective manner. It’s very hard to get all three. In this case, however, Lewiston got it done right with a very quick turn around and from an economic standpoint, they ended up with a new pipeline. And I know, all things considered, the city is very happy with the final install cost.”
According to Lewiston’s Beaule, “We have to complete all the projects for our CSO master plan by the end of 2014 in order to stay in compliance with our permit from the Maine DEP. We expect to be installing at least 10,000-feet of SaniTite HP pipe this year, and perhaps more.”
FOR MORE INFORMATION:
Gendron & Gendron, (207) 782-7372, http://gendroncorp.com
Ted Berry Company, (207) 897-3348, www.tedberrycompany.com
Advanced Drainage Systems Inc., (419) 424-8275, www.ads-pipe.com
Comments