January 2014, Vol. 69 No. 1
Features
For Miller Pipeline, Damage Prevention & Safety Tops Core Values
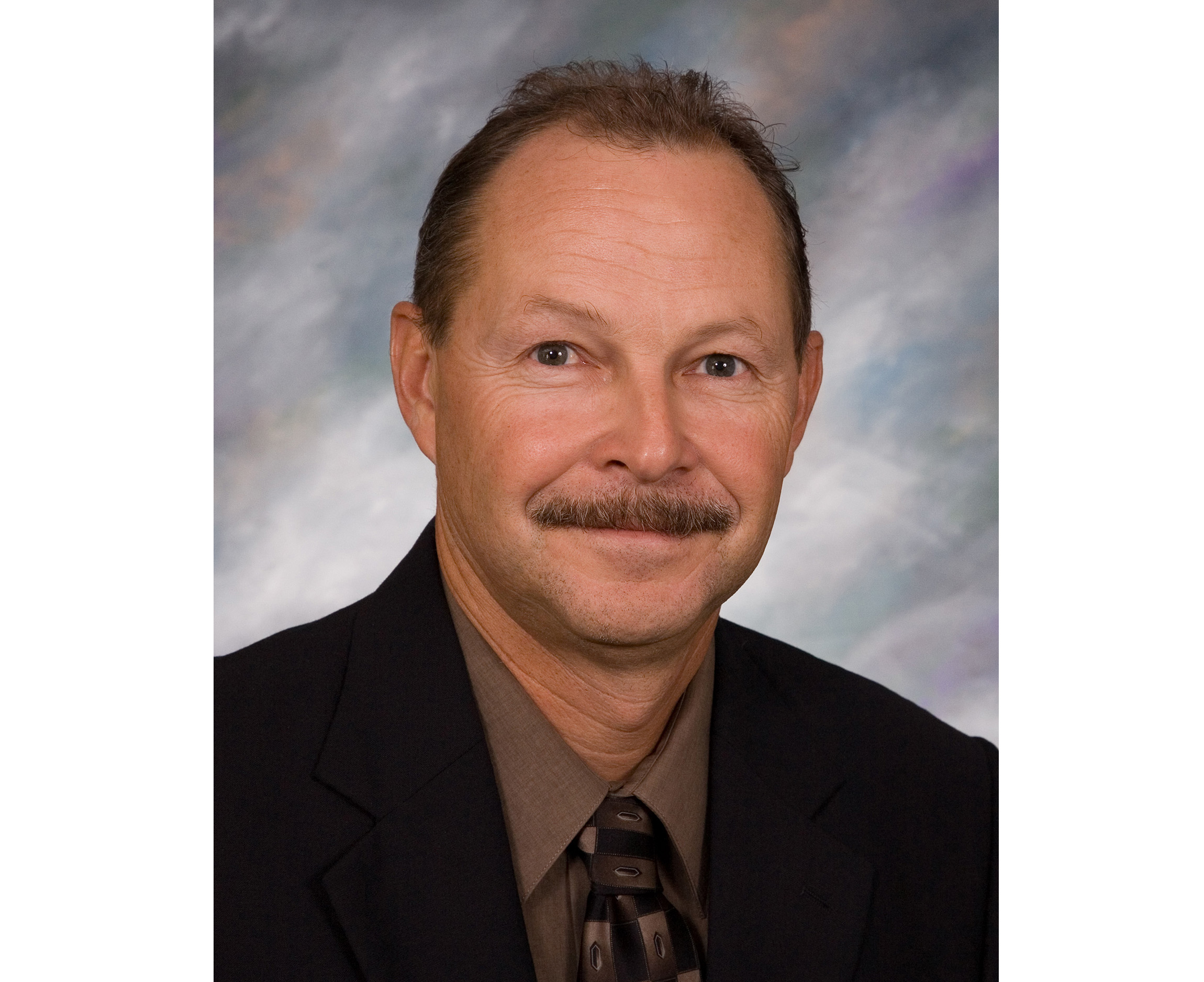
Kevin Miller, president of Miller Pipeline, stressed that “damage prevention and safety occupies a unique position in our company. The management of Miller Pipeline not only has identified employee safety as one of the company’s core values, but placed it at the top of the list. This has not just been done in writing, but more importantly it is clearly visible through the company’s actions.
“As do most top-performing companies,” he continued, “Miller Pipeline complies with all federal and state safety regulations, e.g. maintaining written programs, ensuring that all required training is completed, providing necessary safety equipment, facilitating safety meetings, conducting job-site inspections, maintaining equipment in safe working condition and other proactive steps. One important element in our program extends to preventing damage to other utilities and property on every project. Our safety department and quality assurance program monitors incidents which do not always pose a safety issue – for example, cutting a water line or communications cable that might disrupt service to utility customers.
“We believe the things we do beyond government requirements clearly shows how committed we truly are to providing a safe workplace for our employees.”
Basic elements of Miller’s damage prevention and safety programs include:
• Management commitment;
• Employee participation;
• Training and education;
• Hazard identification; and
• Employee recognition.
“Miller Pipeline’s safety and damage prevention programs are managed by a full staff of SQC (Safety, Quality and Compliance) specialists in the field,” Miller continued. “In each region, these specialists perform audits which include safe boring and digging procedures. They also lead the way on root cause investigations of significant utility damage incidents. Lessons learned from each incident are reviewed with all employees company-wide. Utility hits are tracked and reported as part of a quality assurance program reviewed by the executive group on a monthly basis. As president, I am notified of every safety and damage related incident through a web-based application.
Huddles
“On every project, daily “Planning Huddles” are held to identify the plan for the day and any potential risks. Monthly crew meetings are held to review the contents of our safety newsletter. Quarterly safety meetings address corporate and regional safety concerns. All scheduled meetings are required to begin with a safety message. In addition, leadership and task training are provided to potential foremen. OSHA 10 to 30-hour training is provided to all executives, managers and superintendents,” Miller pointed out.
“Employees are encouraged to report near-miss incidents as part of their safety bonus. An ‘Injury Hotline’ has been established for all injuries to be reported immediately. All accidents are thoroughly investigated and preventative measures are identified and implemented. Leading causes of injury become focal points of the Job Site Safety Observations and are shared throughout the company. All foremen are evaluated on Job Site Safety Observation scores as part of their safety bonuses.
“Miller crews operate many different types of equipment on our projects and receive training for using specialized equipment on various projects,” he continued. “New hire orientation has been modified to include using the national 811 One-Call number, the tolerance zone, protecting other utilities when digging, surveying job sites for other utilities before excavation and spotting utilities by hand digging or with vacuum excavation.
“Training for all foremen and supervisors includes proper use of line locators and damage prevention/risk management. Financial resources are committed towards purchasing special equipment to help eliminate identified risks. We utilize a fleet of more than 100 vacuum excavators to help our crews identify buried utility lines. We use small trailer-mount units that operate on air or water, medium sized truck-mount vac rigs and large hydro-excavators.
“Each construction crew is supplied with a line locator to help validate utilities that have been marked, as well as privately-owned facilities. In addition to regular training, operators of horizontal directional drilling (HDD) equipment receive annual training, usually conducted by the manufacturer that includes safe operation and identifying existing utilities. A large portion of HDD operator training relates to the elimination of sewer lateral crossbores,” Miller said.
High consequence
“Last year, we implemented a new procedure related to crossing “high consequence” utilities when installing pipe by directional drilling. Slots must be opened over these utilities two feet on either side of the located line and the hole must be left open during the bore and pull back process, with observers left at the hole. We also have set minimum required distances to maintain between our new installations when we are parallel boring adjacent to existing high consequence utilities. Before we start boring, supervisors are also required to walk the path of the drill with our operators, looking for any points of conflict before we start boring,” he explained.
“No matter how excellent the plan, it’s up to personnel in the field to execute it,” Miller emphasized. “Daily huddles allow crew members the opportunity to discuss any special situations related to crossing high consequence utilities and planning for safe boring or digging. Employees who achieve “Excellent” scores on Job Site Safety Observations receive recognition. Promotional items are given away during peak times of the year to raise awareness. Raffles are held quarterly in each area to recognize positive safety performance and a “Safety Excellence Award” is given to the top three performing areas each year.”
FOR MORE INFORMATION:
Miller Pipeline Corp., (800) 428-3742, www.millerpipeline.com
Comments