January 2014, Vol. 69 No. 1
Features
Establishing A Comprehensive Safety/Damage Prevention Culture
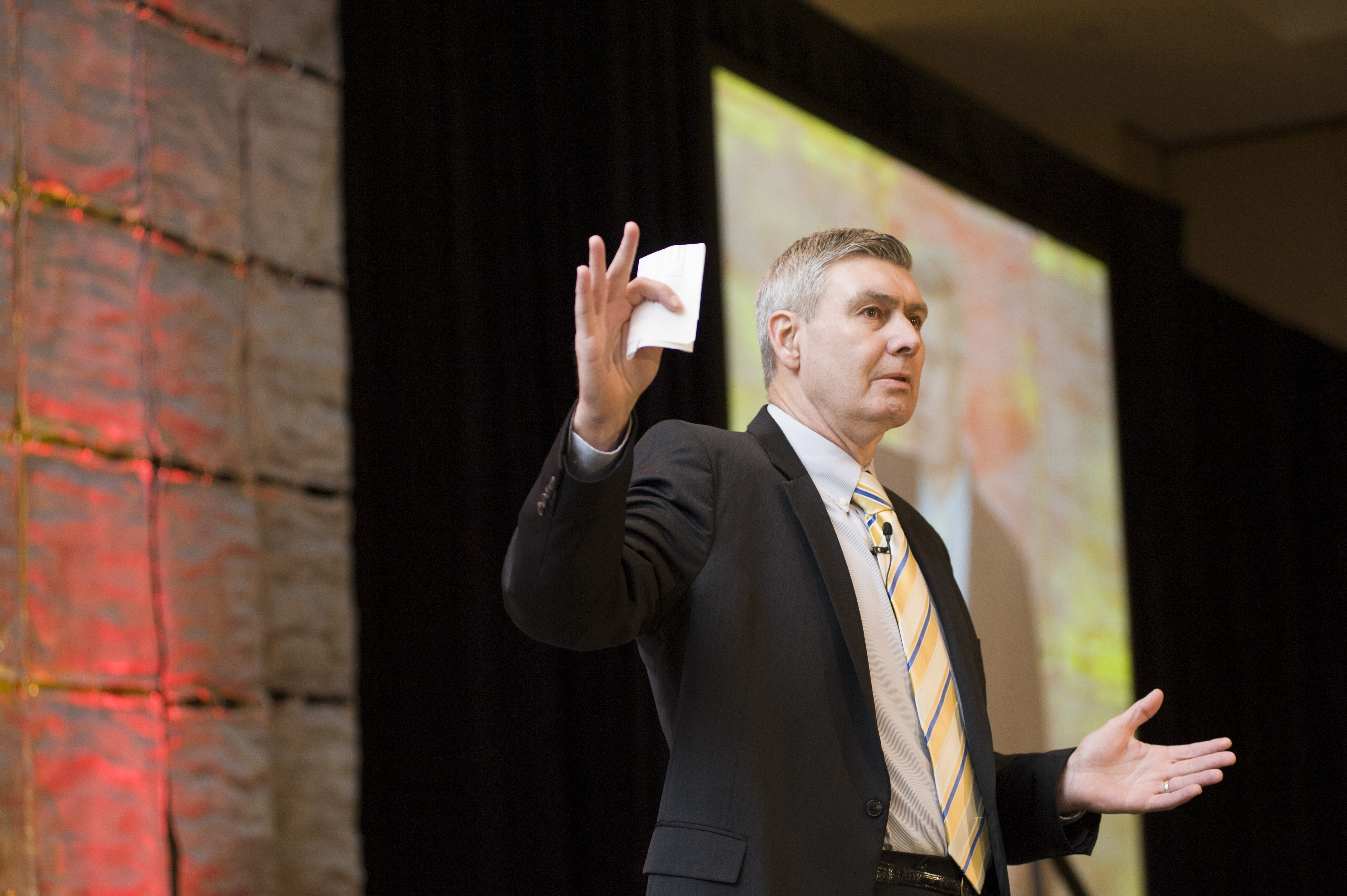
Developing and implementing an effective safety and damage prevention program for a construction company of any size is a critical and challenging task. However, the larger the organization, the more complex it is.
That said, consider the task of developing a safety program and implementing it with multiple companies scattered across North America and abroad that represent varied construction specialties.
That’s the job tasked to Wilson Yancey, vice president of health, safety and environment at Houston-based Quanta Services. Quanta is a S&P 500 company that is a leading provider of specialized contracting services for the electric power, natural gas and pipeline industries through more than 40 operating units.
“At Quanta, safety takes precedence over all business pursuits and practices,” said Yancey.
The success of Quanta’s approach to safety along with the development and implementation of the successful program are documented by an enviable safety record.
“Going back to 1999, Quanta was a young organization that had begun to expand with the acquisition of successful power and telecom contracting companies,” he explained. “At that time, I was given the responsibility for safety and that is my job today. We were a decentralized company then, as we are now, and we found some of our operating companies had safety programs, others did not. Some had people in ‘safety director’ positions that had no concept of what that meant. Many of the companies – even those that had safety programs on paper – placed no priority on safety.”
Patience
It took several years to develop the company’s vision of safety and a template that could apply to all Quanta companies, Yancey continued. Safety procedures were developed and safety personnel were hired to get operating companies moving in the right direction with safety processes.
“In 2004, we brought in a consulting group to evaluate our safety processes,” Yancey added. “In short, they found we had the processes, but not the necessary management philosophy.
“The turning point came when our chief executive officer, chief operating officer and chief financial officer made the management commitment and took responsibility for safety. They, along with the company’s management team, have made safety a top priority and our most important value ever since. Today, every board and management meeting begins with a safety moment. Presidents of our operating companies actively direct safety processes. Quanta no longer acquires companies that do not have a strong commitment to safety.”
From the top through every level of Quanta Services and its operating companies, the organization is committed to the health and safety of its employees, customers, contractors, and communities. Providing and maintaining a safe work environment is a top priority. Today, Quanta has more than 250 safety officers in the field.
To be effective, a safety program requires continuing training, education and compliance.
“Hands-on training involves executives and key management people who deliver messages downward with formal training sessions for groups and often one to one,” he said. “We provide all employees what they need to be proactive, but also how to be reactive when an incident does happen. A software program tracks all educational programs and monitors efficiency.”
Although most often referenced as “safety” processes, the program also incorporates damage prevention.
“Damage prevention is a very important part of what we do,” Yancey said. “I believe we do a very good job of hazard analysis. We want to make sure crews on every job have an understanding of underground and overhead issues to ensure that no incident occurs. Incident prevention is a key part of our program and what drives it, and we want all our employees to take ownership of the program and safety for each other.”
Records
Another essential part of Quanta’s safety program is keeping a record of every incident involving damage or injury. In each case, investigations seek the root causes of incidents. Reports go to top management and safety personnel who disseminate it down the chain of employees. Incident information – positive and negative – is shared during daily safety meetings, conference calls or during safety stand-down meetings.
“All aspects of our safety processes are monitored constantly to keep our employees aware of challenges and changes needed to keep us proactive,” Yancey said.
In an outline format, primary goals of Quanta’s safety and damage prevention processes are to make all employees:
• Commit to taking ownership of safety;
• Maintain a focus of zero accidents in all work activity;
• Make safety a 24/7 activity at work and at home;
• Reinforce the companywide, principle-based safety code of conduct;
• Comply with all federal, state, and local regulatory requirements; and
• Demonstrate a caring attitude for the safety of all fellow employees.
Effective safety and damage prevention programs are not static, but must be dynamic, changing to meet changing technologies and industry advances.
“Safety programs can be written and in place, but if they are not alive, they are just something on a shelf,” Yancey said. “Our continuing processes are to make safety as simple and possible for all employees, not to damage equipment or facilities and to prevent people from getting hurt.”
A measure of any program is results and Yancey said Quanta’s Total Injury and Illness Rate decline each year and remains significantly below the industry average.
“Quanta Services is dedicated to building on this achievement by continuously improving our safety practices and policies,” he concluded.
Safety Leadership
Along with other dedicated organizations, Quanta Services safety efforts extend beyond its own company.
Quanta, along with the Occupational Safety and Health Administration (OSHA), other electrical construction contractors, the International Brotherhood of Electrical Workers (IBEW), National Association of Electrical Contractors (NECA), and Edison Electric Institute (EEI), formed the Electrical Transmission and Distribution Partnership. The organization’s goal is to reduce the number of injuries and fatalities in the industry through implementation of best practices and collaborative training programs.
FOR MORE INFO:
Quanta Services Inc., (713) 629-7600, www.quantaservices.com
Comments