December 2014, Vol. 69, No. 12
Business
HERRENKNECHT Teamwork Ensures Swift Pipe Jacking Under Elbe.
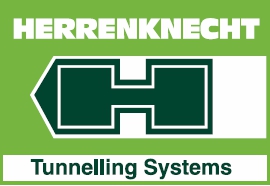
Breakthrough by a micro-tunnelling machine from Herrenknecht in a pipe-jacking project near Hamburg has closed a decisive gap in the construction of two new gas pipelines. The 1.5 kilometer route runs up to 35 meters under the Elbe through various, partially complex geological zones. This demanding technical challenge was competently mastered by the long-term Herrenknecht contractor A.Hak Drillcon on December 4, 2014 after a total of 112 days of tunnelling and in time for the feast day of Saint Barbara, the patron saint of tunnel builders and miners.
In northern Germany, the existing pipeline network is being modernized for regional gas supply. This major project also includes the “Elbedüker Hetlingen” where a Herrenknecht AVND machine (Ø 3,025 mm) crossed under the Elbe near Hamburg in the second half of 2014. The tunnel was driven in a pipe-jacking process from the peaceful town of Hetlingen to the target shaft on Lühesand Island on the Elbe – under high pressure in terms of both time and water. “Construction of the two new gas transit pipelines enables us to guarantee gas supplies for Northern Germany and Scandinavia also in the future”, claims Dr. Philipp v. Bergmann-Korn, Press Spokesman for the client Gasunie Deutschland Services GmbH.
Even before the project start, everyone involved was aware of the huge technical challenges associated with the construction. The diversified ground ranged from sandy gravel soil with stones through layers of boulder clay featuring larger rocks to layers of clay which tend to be very sticky. This was exacerbated by high water pressures of up to 4 bar as well as a route length of more than 1.5 kilometers, making the project one of the longest pipe-jacking jobs in the world. In its capacity as drilling company, A.Hak Drillcon relied on the expertise and support offered by Herrenknecht right from the start. Even during refurbishment and project-specific modification of the used AVND2400AB, collaboration was hand in hand and includeda videoscope examination of the main bearing as well as adaptation of the man lock and the main bearing sealing for water pressures of up to 4 bar.
Further collaboration on the jobsite proceeded particularly positively. Two Herrenknecht machine operators supported A.Hak Drillcon during the tunnelling process enabling efficient three-shift operations around the clock. At all times, experienced service technicians from Herrenknecht were also on hand to provide tunnelling support – on site so as not to waste any time. “On such a challenging project, continuous mutual exchanges of experience are simply advantageous. We appreciate that. Comprehensive service is as important as good technology.” summarized Peter Dennig, the responsible manager at A.Hak Drillcon.
For the purpose of increasing safety, the contractor ordered an entire range of navigation, survey and monitoring technology from Herrenknecht subsidiary VMT. Using IRIS.microtunnel – a web-based data management and monitoring system – it was, among other things, possible to permanently monitor all support pressures while comparing them in parallel with the fluctuating tides of the Elbe. Furthermore, the comprehensive HADES communication system featuring several modules such as video surveillance, fire alarm or RFID jobsite access control was used for the first time in Germany.
The machine encountered large boulders almost 200 meters into the route. But such geological conditions had in fact been anticipated and the jobsite team swiftly overcame these obstacles thanks to their experience and thorough preparations. Following the exchange of worn excavation tools, the AVND2400 picked up speed along the remaining route resulting in top values of up to 40 meters per day. Thereby, the entire tunnelling length could be handled directly by the main jacking station in the starting shaft without using any intermediate jacking stations. This top performance was attributable to the consistent application of AVND technology, automatic annular gap lubrication and the great teamwork displayed by everyone involved in the project.
A supplementary video on the project is available at allaround.herrenknecht.com.
Comments