April 2014, Vol. 69 No. 4
Features
Efficient, Economical Grout Solution For Downers Grove
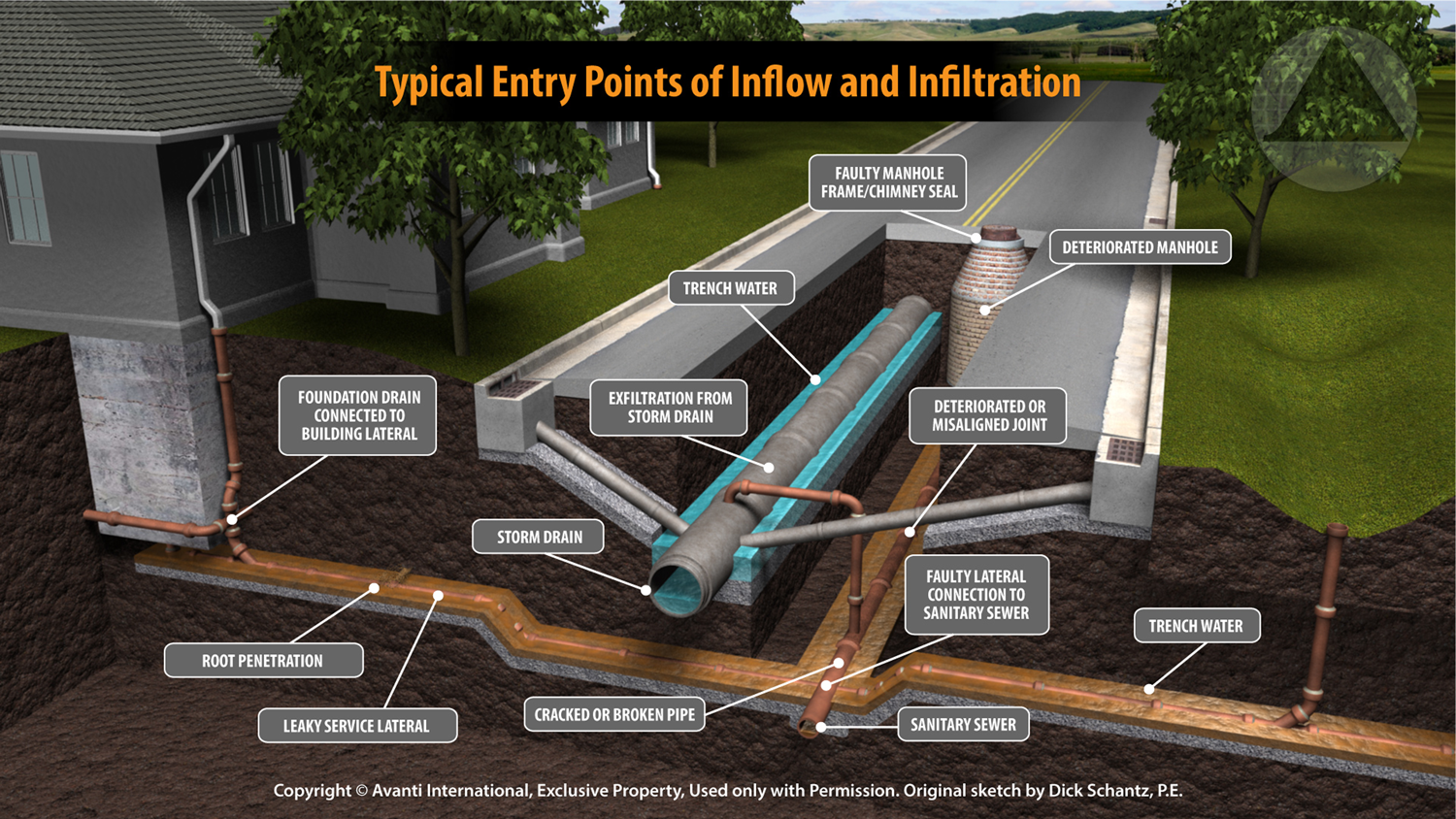
The Downers Grove Sanitary District (DGSD) is located in Downers Grove, IL, a community located 25 miles west of Chicago. The District serves 20,000 residential and business customers in Downers Grove and surrounding communities.
Like many Midwestern communities that were founded in the 1800s and grew over the succeeding century, its sewer system contains pipes of a wide variety of ages, from as old as 109 years to much more recent additions made as the service area grew. Replacements have been made as the existing infrastructure has aged. Today the DGSD system covers 20 square miles with 252 miles of sewer (consisting mainly of eight-inch vitrified clay pipe) and nine lift stations, and is designed to handle a peak flow rate of 110 million gallons per day.
When the American Recovery and Reinvestment Act of 2009 (ARRA) made funds available for “shovel-ready” infrastructure projects, the DGSD proposed a project to seal, by means of chemical grouting, a part of its system to reduce infiltration and inflows (I/I). The targeted 15 basins include 112,000 linear feet of eight- to 24-inch unlined pipe. The goal of the project was to seal 24,600 mainline joints, 3,100 lateral connections and 440 manholes. Work on the project began in December 2009 and was completed in August 2010.
Sewer stress
All parts of a sewer system – main sewers, laterals and manholes – are subject to the normal stresses of ageing and wear on materials and stresses on joints that lead to increasing I/I of storm water and ground water into the system. Materials carried into the sewer by the incoming water reduce the working diameter of the pipes at the same time that the I/I is increasing the volume of water that flows through the sewer. The result is increased stress on the capabilities of the sewer system and increased cost of treatment to system users.
Sewers are also subject to external, less predictable extreme stresses such as excessive flows during heavy storms that overload storm sewers. Overflows from storm sewers added to the increased pressure of ground water increase inflows into wastewater sewers, but also direct water into supporting trenches that erodes the supporting earth and gravel under sewer lines.
Supporting material is washed away, either into the sewer itself or along the supporting trench.
“Without proper support, pipes can then begin to shift,” states Frank Aguilar, vice president, customer service and operations of Avanti International, manufacturer of the grout used in the project, “causing gaps at joints and even failure of the pipes themselves.”
To counter these stresses, sanitary districts such as DGSD regularly inspect sewer systems and make repairs to replace damaged pipes and control I/I levels to enable the system to function as designed. DGSD, for example, annually cleans 25 percent of its sewer pipes and sets a goal of conducting televised inspection of 10 percent of the system. It has also conducted continuous flow-metering of the system since 1996.
Grouting decision
The three primary goals of the 2009 project were to reduce the I/I that in extreme cases increased the system’s flow to 10 times its average daily flows, to extend the life of its pipes and to reduce maintenance demands on the District’s crews. Of the various techniques of repairing sewer lines that were possible – open-cut replacement and repair, cured-in-place pipe (CIPP), various pipe lining methods and chemical grouting – the latter involves the newest technology and is perhaps the least well understood. DGSD, however, had used chemical grouting on previous rehabilitation projects with reasonable success in terms of I/I reduction. In addition, 96 percent of those grouted pipes that had been grouted were still passing inspection five years later.
“Our previous experience indicated to us that chemical grouting was a viable, cost-effective solution to reduce I/I,” says Bob Swirsky, DGSD’s sewer system maintenance supervisor. He points out that – in areas where it is an appropriate solution – using chemical grouting enables DGSD to avoid the dramatically more expensive repair options.
For this project, DGSD identified particular areas where pipe conditions were optimum for grouting – i.e. areas where its televised inspections had found no severe pipe misalignment or failure.
Chemical grouting is the pressure injection of a multiple-component chemical material into and through leaking pipe joints to seal the joint and prevent I/I. It also stabilizes the soil around the joint, helping to prevent future pipe movement and I/I.
Before chemical grouting begins, pipes are thoroughly inspected and cleaned of grit and root intrusions. If inspections show that pipes are leaking but stable, or are less stable but not yet to the point of failure, grouting is a viable solution. Beyond that, intrusive structural repair will be needed. The cost of those extreme measures can be as much as 10 times the cost of grouting.
Chemical grouting has several significant advantages over other technologies when the goal is to reduce ground and storm water infiltration. First, the more intrusive repair techniques are solely structural repairs, whereas chemical grouting is an addition to existing stable pipe and actually can also be used as a complementary technology when structural repairs are being done. Structural repairs also require a dry environment in order to be performed. Secondly, while these alternatives are valuable techniques to replace or repair damaged pipes, they do not stop infiltration. Chemical grouting, on the other hand, was specifically developed as a solution for leaking pipes, and being chemical in nature, can be successfully applied in a wet environment.
Another of the advantages of chemical grouting is that the material used can be varied in composition to match the specific requirements of the pipes being grouted. For example, since inspections of DGSD pipe had shown significant root intrusion, after the pipes had been cleaned and roots cut, a chemical growth inhibitor was added to the grout to curtail future root intrusion.
Selecting, grouting the basins
As noted, DGSD has conducted flow-metering of the 149 basins in its system for almost 20 years and has assembled GIS data on pipe condition, peak flows and I/I for each basin. Using this data, Derek Wold, vice president and manager of the Wastewater Group at Baxter Woodman Consulting Engineers, project engineers for the grouting project, and his team worked with DGSD to identify 15 basins that were candidates for grouting.
Using the 15 years of data, the basins were ranked in severity of I/I by assigning each a number representing the I/I in gallons per minute per lineal foot of sewer per inch of rainfall.
National Power Rodding Corporation (NPR), a Carylon Company, which pioneered the use of chemical grouting and is the nation’s largest chemical grouting group, won the contract to do the grouting of the identified basins. NPR grouted each basin in turn from north to south in the district, using three crews working in each of the basins. That procedure – using three crews in the same basin – allowed DGSD to assign only one inspector to the basin, freeing other personnel for District work.
All lines were cleaned and televised before grouting, allowing the crew to confirm that the lines were acceptable candidates. Before grouting, they removed all roots, mineral deposits and protruding taps from the pipes.
Of the 24,000 mainline joints tested, 25 percent failed. Each joint required an average of three gallons of grout to achieve a seal. Where inspections detected heavy root intrusion, a root-killing chemical was added to the grout. In one formerly swampy area, where joint failure was almost 100 percent, a diatomaceous earth additive was included to give the grout greater consistency.
Of the 2,100 lateral connections tested, 60 percent failed. Each of these also required an average of three gallons of grout to seal.
Composition, DGSD grouting procedure
The grout used in the DGSD project was an Acrylamide grout complying with ASTM F2304. The procedure used was to seal the joint or lateral being tested and grouted using inflatable socks that isolated it from the main sewer flow. For laterals, the four-foot sock sealed off the lateral joint at the main line and the first one or two joints within the lateral. Following testing, the grout was injected.
After each joint and lateral was grouted, it was retested and inspected to confirm that it was not leaking. Unique to this project, a three-year warranty test is to be conducted after three years of service to ensure that joints are still not leaking. That testing is scheduled to begin in the spring of 2014.
The project originally called for sealing 440 manholes by creating a grout curtain around each structure. After grouting 60 of the manholes, NPR determined that grouting would not be the most cost-effective solution because the backfill around the structures consisted of large rock, and required large amounts of grout to create an adequate curtain. NPR recommended that the manholes be sealed with concrete liners.
“We were originally hesitant to line the manholes, based on past negative experience with both cementitious and epoxy lining” says Swirsky. “In the past we found that unless the surface was cleaned thoroughly and the application carefully supervised, that the surface tended to flake off over time. But given the large amount of grout required to seal each manhole we felt we needed to explore an alternative.
“We asked NPR to complete a demonstration lining on one manhole as a test. They power-washed the surface and used coating much improved over those used in the past, including reinforcement with metal microfibers for added strength. The DGSD inspector on site found the result to be a solid lining and we approved moving forward with the lining procedure for the remaining manholes. In the months since, we have found it to be a satisfactory solution.”
In addition, pre-grouting review of the televised lines revealed that 6,200 feet of 24-inch concrete pipe had extensive damage from hydrogen sulfide (H2S). It was agreed by all parties that these pipes would be removed from the project and bid as a separate project in which they would be rehabilitated with CIPP rather than grouted.
“These decisions underline an important aspect of the success of a project such as this,” points out John Manijak, project manager with NPR, who directed the grouting operation. “On any project, the engineer, contractor and owner must work as one team with the single goal of producing the best result. That means being committed to doing what is right for the success of the project rather than what is specified in the contract.”
Funding
Funding for the project was provided by the ARRA through the state of Illinois Environmental Protection Agency (EPA), and consisted of an interest-free loan that included 25 percent loan forgiveness. The approximate total cost of the project was $3 million. However, as the project progressed, changes that were made from the original project description lowered the cost. Manholes that the project had planned to seal with grout curtains turned out not to be viable candidates for the technology and were removed. With that “saved” funding, DGSD and the contractor identified two additional basins that could be treated with chemical grouting, bringing the total number of basins grouted to 17.
“Post-grouting flow-metering of the sealed basins showed varying levels of reduction in individual basins,” says Derek Wold, “but an overall reduction of I/I in the system of 21 percent. In addition to reducing the stress on the treatment system, these reduced flows also help extend the life of the pipes.”
Also, he points out, removal of roots and the use of additives to inhibit future intrusion reduces the workload of the DGSD’s maintenance crews, freeing them for other work.
Finally, as to the $3 million cost of the grouting project, by reducing the added flow of I/I water in the system, eliminates the need to construct additional pumping capacity, and larger or relief sewers that would otherwise be needed to handle peak flows that were threatening acceptable operation during large storm events. It is estimated that the cost of the grouting project, $220 per gallon per minute (GPM) of I/I eliminated, saved DGSD an estimated $2,050 per GPM that would be needed to construct those additional facilities. There are additional savings in costs of handling these excessive I/I flows at the treatment plant.
“Not every sanitary district takes the time or has the capability to investigate the options that may enable them to do this kind of cost-effective maintenance,” DGSD’s Swirsky points out. “But the effort is well worth it. In addition to avoiding the necessity to build additional capacity, by using chemical grouting we were able to accomplish in less than one year what with more invasive repair technologies would have taken us multiple years to complete at a much greater cost.”
FOR MORE INFO:
Avanti International, (281) 486 5600 or (800) 877 2570, www.avantigrout.com
National Power Rodding Corp., (800) 621-4342, www.nationalpowerrodding.com
Carylon Corporation, (312) 666-7700, www.caryloncorp.com/
Baxter & Woodman Consulting Engineers, (815) 459-1260, www.baxterwoodman.com
Comments