April 2014, Vol. 69 No. 4
Features
Dealing With Confined Space A Complicated Challenge
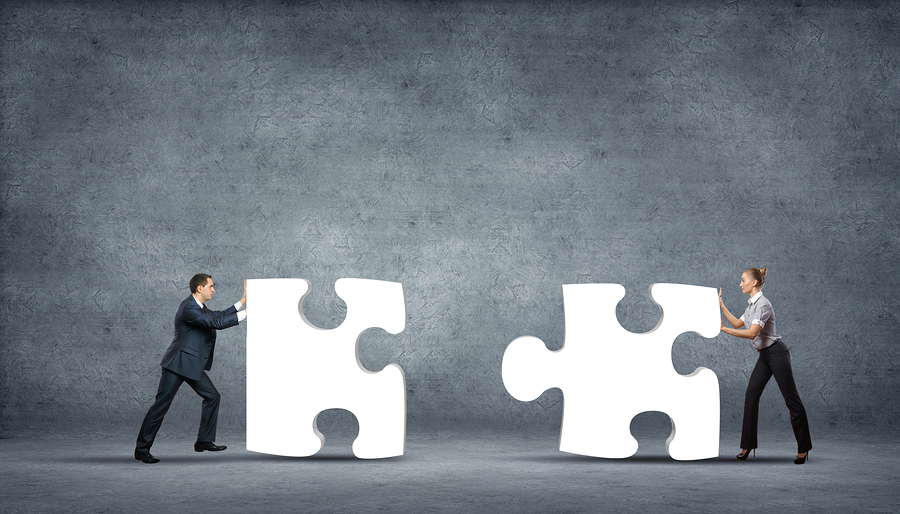
Working deep underground inside a large pipe or other enclosure requires specialized training, equipment, work procedures and safety practices.
In addition, it takes a special person who can be comfortable and productive inside confined, hazardous spaces – a task many could not or would not consider.
Utility and contractor personnel often must enter and work in confined spaces such as pipelines, sewers, tunnels, utility vaults and excavations of various depths and configurations.
Confined spaces represent one of the most challenging and potentially dangerous scenarios in construction, says Jackson Pettyjohn of the University of Texas at Arlington (UTA).
“Unlike excavation and fall scenarios where hazards usually are clearly visible and can be addressed with straightforward solutions,” Pettyjohn continues, “the atmospheric issues associated with confined spaces may not provide warnings to the senses. Typically workers cannot see, hear, or in many cases, even smell gases or fumes that may be present. They may not realize that they are in trouble until it is too late for them to recover and self-rescue. Fellow employees, who may see a victim collapse, rush to rescue, only to become victims themselves. The most distinctive and tragic statistic concerning confined spaces is that two out of three victims typically are would-be rescuers.”
Working safely under such conditions is a life-or-death challenge.
Pettyjohn, business development/program manager for UTA’s Division for Enterprise Development, said employers who set out to create effective confined space entry programs, are confronted with a mixed bag of guidance from regulatory and investigative agencies such as OSHA and ANSI. In a misguided attempt to save time, money and “bother,” historically there has been a reluctance to do more than meet the minimum requirements of regulations.
Tools available to safety professions for addressing confined space safety issues are an ANSI standard, an OSHA regulation and some trade and professional journal articles. Robert Spielvogel, director of safety for Clean Harbors, a leading provider of environmental, energy and industrial services, describes these tools as “…often informative, but seldom instructive.”
Impacts all
Pettyjohn says the critical first step for developing an effective confined space safety program is smashing through a “that-doesn’t-apply-to- me” attitude.
“Most of us who’ve taught in the public sector have experienced employees telling us they don’t have to do ‘that OSHA stuff’ because they are not under OSHA’s jurisdiction,” Pettyjohn explains. “Likewise, employees in the construction workplaces often state, complain or brag that the confined space standard applies to general industry, not construction, and OSHA doesn’t even call excavations – probably the most commonly entered space where hazardous atmospheres could easily accumulate – confined spaces, so they don’t have to put any real effort into confined space safety.
“My typical response has been to ask them if they really think the methane or hydrogen sulfide was going to tap them on the shoulder and ask them if they were public sector employees or working in a general industry scenario before it decided to kill them.”
Pettyjohn believes that when workers begin to understand that lethal atmospheres aren’t playing by the “rules” (regulations), they also begin to understand that their lethal opponent has to be understood and dealt with by using effective means and methods that may exceed minimum requirements of OSHA.
A good starting point is with definitions of confined spaces which will illustrate the problems with regulations.
The OSHA General Industry Standard of a confined space is one large enough and so configured that an employee can bodily enter and perform assigned work, which has limited or restricted means for entry or exit, and is not designed for continuous human occupancy. The OSHA Construction Standard defines a confined space as any space having limited means of egress which is subject to accumulation of toxic or flammable contaminants or has an oxygen deficient atmosphere.
“This is good as far as it goes,” says Pettyjohn, “but workers need to make sure they haven’t limited themselves to a strict reading and interpretation of a definition, but rather focus on whether the space – whatever it may be, however it may be configured and the activity being conducting – could result in the generation and containment of a hazardous atmosphere or an engulfment.”
As an example, consider the garage of a house, he added. The limited access/egress definitions certainly don’t apply, and folks who have installed a beer fridge, TV, stereo, pool table and dart board would defy the “not intended for continuous occupancy” definition.
“Still,” says Pettyjohn, “if someone were to be welding galvanized metal with the garage door down and the pedestrian door closed – this occurred to a friend of mine – they might discover their friendly garage to be as deadly as any vault or trench they ever entered.”
Developing a confined space safety program that is instructive and effective begins with regulations but grows past them, Pettyjohn emphasizes, especially those specifically written for a particular construction scenario, like excavations. “I believe it requires three steps: education, evaluation, and elimination,” he added.
Education
Clearly education, especially in the applicable standards in which there are legal obligations to comply with, but education in the nature of the hazardous atmospheres and environments in which engulfment may occur have to be included. Workers need to know how the various atmospheres will affect them and how to recognize them.
Pettyjohn advises employers to “shop” for standards that apply to the specific work their personnel does. OSHA standards to reference include:
• The General Industry Confined Space Standard for its comprehensiveness and the procedures it outlines to eliminate hazards;
• The Proposed Confined Space Standard for Construction, because the word on the street is that it will be enacted soon, and because it closely mirrors the General Industry Standard and knowledge of that standard will help in preparation for its enactment;
• The Excavation Standard because it is a vertical standard with specific requirement for the most commonly entered confined spaces in construction;
• The Tunneling Standard for guidance with ventilation and gas monitoring;
• Telecommunications and Underground Lines standards, also for ventilation requirements;
• Lock Out/Tag Out for controlling the unintended influx of water or other fluids or gases from pipes and other utilities; and
• Hazard Communication provides information about various kinds of exposures and treatments.
“A look at the excavation standard demonstrates why a single standard will typically not suffice,” says Pettyjohn. “OSHA requires that the designated competent person check any excavation over four feet deep. If the competent person believes a hazardous atmosphere might be present, he is to make sure there is at least 19.5 percent oxygen and no more than 20 percent of the LFL (lower flammable limit) of any flammable gases.
“An employee who knows no more than that knows only enough to get killed from a false sense of security created by the regulation.”
There are several fallacious assumptions involved. “The first is that the employee will do nothing that would cause their head to break the plane of the excavation and expose themselves to gases below natural grade. The second is that the gases will be heavier than air and not pressurized or stirred by wind to cause them to rise and overcome the employee. Insofar as gas distribution employees have been overcome and killed in excavations 12-inches deep, it is clear that the excavation standard leaves much to be desired where hazardous atmospheres are involved.
“Likewise, the failure to discuss UFL (upper flammable limit) and backdraft situations, which might be encountered from flammable liquids in excavations or from leaking containers in a storage shed that could lead to problems.
“Finally, workers who believe themselves safe with an oxygen level of 19.5 percent may not realize that the level may drop if they do something like ignite a cutting torch. Or it could be an indication of the infiltration of another gas that may create an asphyxiation situation, or a toxicity situation of a poisonous kind that the monitor cannot detect, particularly if the infiltration continues during the work.
“To understand the nature and generation of confined space scenarios and how to recognize and deal with them, employees should be educated via this shopping cart full of standards. Then deadly myths, such as “clean and dry means safe’ and others, can be dispelled.”
Evaluation
Armed with education and information, workers should be better able to recognize and evaluate potential hazards when working in confined spaces.
Prior to engaging in the work in a confined space, employees, particularly those designated as competent persons, supervisors or attendants should evaluate the site and ask themselves these questions:
• Where are the places a hazardous atmosphere could exist or an engulfment occur?
• How could the atmosphere be generated?
• Could the soil do it from previous contamination by spills or leaks?
• Could we be digging in a landfill? Are there underground utilities or storage tanks that could leak into the excavation?
• Have all valves controlling the influx of water or other liquids been locked and tagged out?
• Is nearby traffic generating carbon monoxide?
• Are we generating carbon monoxide with chop saws, tampers, or other equipment?
With the answers to these questions, it is possible to move on to further evaluation which would involve the correct use of gas monitors to determine atmospheric conditions before and during the conduct of the work. Employees must know to trust the monitors and exit the space if alarms sound.
Having evaluated the site, the employees should then undertake the appropriate measures to eliminate the hazards…the “Eliminate” step.
Eliminate
Some sites may be so hazardous or contaminated that specialty companies used to dealing with permit-required confined spaces and the use of advanced equipment such as air line supply respirators or self-contained breathing apparatus (SCBA) equipment may be required.
However, most sites, unless they contain contaminated soils, may be well within the capabilities of a typical construction crew, particularly when they involve excavations.
Once all potential sources of engulfment have been identified and locked out or found to be secure and free of leaks, the focus can shift to preventing the buildup of harmful gases. Carbon monoxide generation by equipment used in the excavation might occur, as may the infiltration of CO2 from passing traffic. An employee trained about the hazards of CO2 usually is receptive to wearing the appropriate respirator or helping ensure adequate ventilation occurs.
A knowledge of OSHA standards previously cited is helpful in a scenario such as this.
In the preamble to the General Industry Confined Space Standard, the telecommunications industry could demonstrate a record of more than 50,000 safe entries into manholes and vaults without one fatal incident. Most phone technicians say they seldom use gas monitors in ordinary circumstances, but a blower or ventilator is one piece of equipment they use with religious fervor.
“Simply stated,” Pettyjohn says “it’s tough to beat taking a safe atmosphere in with you. Understanding how to correctly position and use blowers to provide sufficient fresh air in a potential confined space could easily eliminate most confined space concerns, as well as provide cooling on hot summer days. Implementation of a blower on other construction sites easily could be as effective as it has proven to be for the telecommunications industry.”
Safe rescues
The OSHA Excavation Standard requires attention to rescue procedures be addressed. Therefore serious consideration must be given to effective means of performing rescue operations, and especially those that can be performed without entry to the danger zone by additional personnel.
A full body harness and lifeline system is the most commonly used method. Boat davit style winch systems that can mounted to trench boxes or trucks are available and easy to incorporate on job sites. Also viable are lifelines that can be secured outside the space or excavation, then hooked to a retrieval device. Whatever the rescue means selected, employers should carefully evaluate and discuss how they can be effectively used at the site.
“Finally,” concludes Pettyjohn, “it is necessary to recognize there are confined space scenarios that exceed the expertise levels of most construction workers and know when it’s time to ‘punt’ by calling in confined space experts.”
FOR MORE INFORMATION:
Jack Pettyjohn, (832) 922-5674; jcpetty@uta.edu
Comments