March 2012, Vol. 67 No. 3
Features
Science Of Mud, Systems In HDD Ops
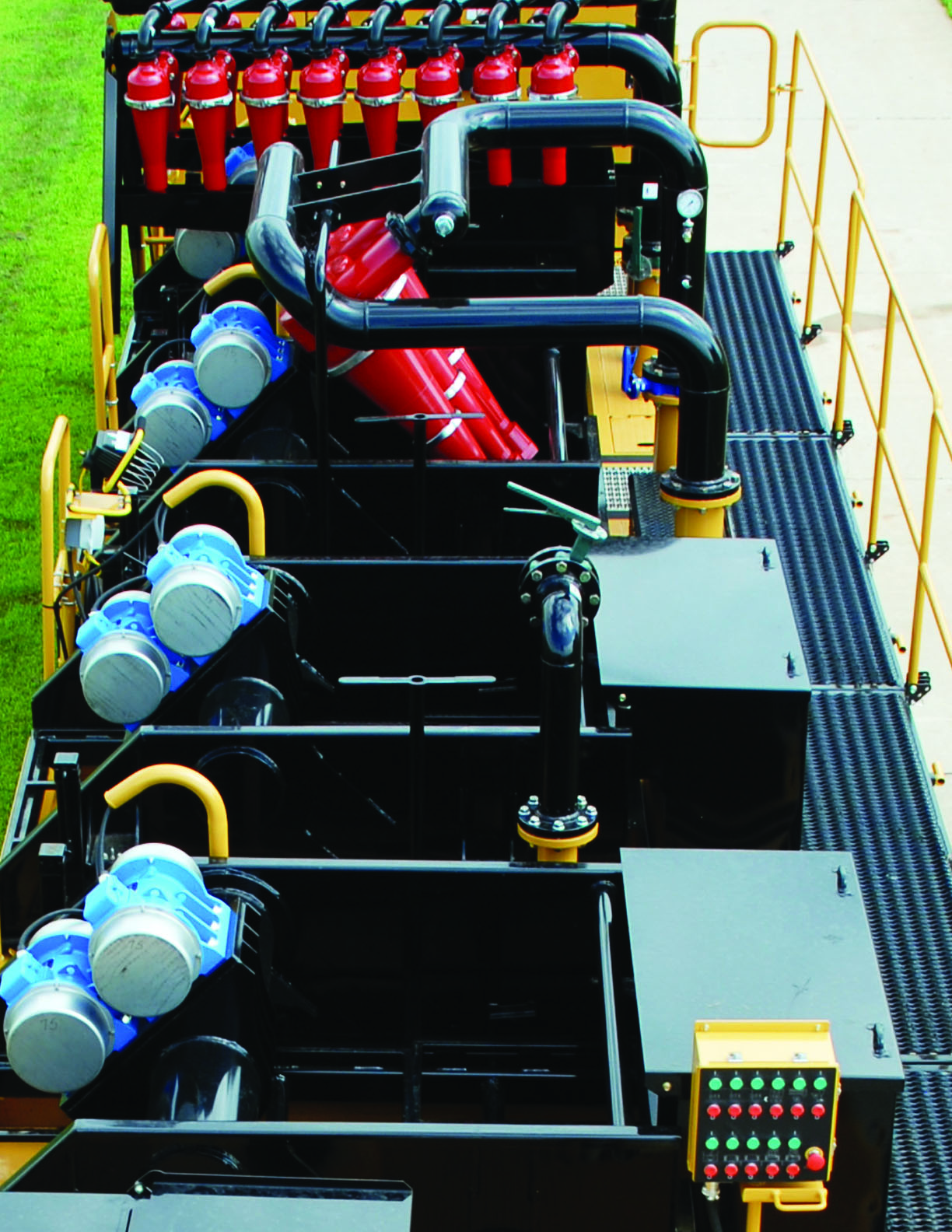
The old adage “don’t muddy the water” doesn’t apply to horizontal directional drilling (HDD) where the water is supposed to be muddy. Drilling fluid (mud) extracts particles and cuttings from the bore hole, as well as stabilizes the hole itself. Mud has always been an essential element to a successful drilling operation.
Along with the drilling fluid, a reliable method of delivery to the drill is needed. This is called a mixing system or mud system. The mud system delivers the fluid to an onboard pump (on smaller horizontal directional drills) or a standalone pump that feeds into a larger rig (generally 100,000-pound capacity or larger.) With the rise of mud recycling in drilling, reclaimers are becoming more prominent on jobsites. These are a type of mud system that “cleans” the used mud and recirculates it back into the mixing system to be reused. An HDD contractor needs to make sure to use the right kind of mud and the proper equipment to effectively supply the correct amount of fluid into the pump and downhole.
“The mud system is the device on the jobsite that is married to a particular drill rig,” says Jon Heinen, pipeline segment manager for Vermeer Corporation. “Its job is to provide that rig with the appropriate amount of drilling fluid, so it has to be a good match. A large pipeline project with a maxi rig is going to have a significantly different system than that of a smaller 9,000-pound (thrust/pullback) machine. Either way, all HDD machines need a mud system of some kind.”
There is a method to the “mudness,” and strict adherence to procedures needs to be followed. The key factors are proper planning, ensuring the use of proper equipment and consistent drilling fluid maintenance during drilling operations.
Drilling fluid, mud, slurry — it’s all the same
“Mud” is the common reference to drilling fluid used in all types of drilling operations. “Slurry” is another term that is an interchangeable reference to drilling fluid. Mud serves multiple purposes such as: provide coolant for down hole electronics; suspend and displace cuttings from the bore hole; reduce wear on downhole tooling; and aid building a stable bore hole by reinforcing and maintaining the walls of the bore or tunnel. Given the importance of mud, achieving the right mix is another science.
“There is no universal formula,” says Heinen. “There’s no perfect recipe for a fluid mix. It just depends on what you’re doing, where you are and how each soil encountered reacts, since soils react differently.”
The key to maintaining the integrity of the walls of the bore is bentonite, the primary component to mud mixes. Bentonite is a mineral found in clay beds. Its properties are such that when it’s mixed with water, it forms a filter cake much like the layers of a biscuit. This filter cake helps seal the walls of the bore tunnel allowing the drilling fluid to remain in the hole, which helps mechanically support the structure of the bore hole.
Water is one of the critical elements to the mud mix. Water can vary depending on its source, whether it is extracted from a creek or river or sourced from the city. Water with a high concentration of sand or clay will weaken the binders in the mix and compromise the effectiveness of the drilling fluid. Contaminates in the water could also damage, or at the very least shorten, the life of your mud pump, says Heinen.
Other elements and additives in the mix help with fluid viscosity and gel strength, which determine how the fluid can suspend particles and cuttings and carry them out of the tunnel. The ground conditions and type of soil you are drilling into will affect the viscosity and gel strength of the drilling fluid. That is why HDD contractors are constantly tweaking the formula, especially when soil conditions change as the bore progresses.
Rise of mud recycling
Rising costs of mud disposal and the limited availability of disposal sites are driving some HDD contractors to reuse their drilling fluid, which requires a reclaimer.
“Environmental concerns are also a factor so we are seeing more reclaimers required in drilling specs,” says Heinen. “Also mud disposal is cost prohibitive and we are seeing an increase in mud recycling requirements on job sites.”
Cost factors in mud disposal include hauling of used fluid, whether it is trucking or rail cars, sometimes out of state. Dumping costs are expensive; certain situations may require additional additives to be mixed with the used fluid that have come into contact with hazardous materials underground.
It is estimated that about 20 percent of what comes out of the exit pit is solids and cuttings. Mud recycling is simply using a reclaimer instead of a standard mixing system — it’s a combination of a mixing system and a system to clean dirty fluid, and then recirculate the cleaned fluid.
A standard mixing system employs a mixing hopper, an agitation system and a pump to deliver to the drill. These components are standard no matter the size and capacity of the system. The hopper is where bentonite is introduced into the clean water or clean mud. The agitation system continuously circulates the fluid to keep the components in suspension, and the pump creates the flow to deliver the fluid into the drill.
A reclaimer is generally used on drill projects when you are using a large volume of fluid. Smaller projects can utilize an excavation system and dispose of mud in a cost effective manner. A reclaimer utilizes a series of shakers, cones and screens to filter out solids from the fluid, leaving the bentonite and other additives in the solution and recirculating the cleaned fluid.
The reclaimer is generally configured with multiple tanks which can include a clean mud tank, a dirty fluid tank and a desander and/or desilter tank. Dirty fluid is drawn from the return pit and pumped across the first cut shaker(s), which sift out all the larger particles of sand and debris. Then the fluid is pumped through the desander cones where a cyclonic motion is used to eliminate even smaller particles, and again across a shaker screen equipped with a finer mesh screen to further the cleaning process. The fluid finally passes through desilter cones and again across a final set of shakers and screens, which separate out the smallest micron particles from the drilling fluid completing the cleaning process. Each deck on the reclaimer uses progressively smaller screens to remove micron-sized elements from the fluid. Once through, the fluid is stored in the clean mud tank ready to be recirculated back down hole.
“You won’t get 100 percent return on your fluid due to several scenarios,” says Heinen. “There is typically some circulation loss either due to soil absorption, formation instability or the drilling process. When using a reclaimer, you should use a mud test kit to test the clean fluid being held in the clean mud tank. This test will verify both information on the cleanliness of the mud and be an indicator of how well your cleaning system is performing.”
The mathematics of mud
As mentioned earlier, bores can fail due to a poor quality fluid mix, but also bores fail when the standard procedures and accepted formulas for fluid-to-soil ratio are not followed. There is a formula that must be followed to determine the amount of mud needed for effectively maintaining the bore path, which figures in the bore diameter, soil conditions and process.
“You start with determining the size of bore you’re going to be building in the ground,” explains Heinen. “This is not the diameter of the product, but the diameter of the actual hole.”
Hole diameter in inches squared divided by 25 gives you the gallons per foot. Next figure the fluid-to-soil ratio, which is based on the soil type and is where the expertise in your ground conditions comes into play.
“The type of ground will have a bearing on how much fluid you need to pump downhole. If you’re in sand, gravel, cobble or rock, typically your fluid ratio to gallons per foot is about 1-to-1,” says Heinen. “If you’re drilling in clay, the ratio can range anywhere from 2-to-1 up to 6-to-1 depending on the soil, and reactive shale is anywhere from 10-to-1 or 20-to-1.”
The last parts of the calculation are the rod length and pump output. So the formula is Gallons per Foot x Fluid Ratio x Rod Length ÷ Pump Output.
“This is the generally accepted formula in the HDD industry. Not following it is like not having Generally Accepted Accounting Practices in accounting,” says Heinen. “It will help the contractor estimate how much fluid will be needed and how much time it may take on the job.”
Sizing equipment, proper maintenance
As stated before, mud systems are married to particular HDD machines, but systems need to be sized according to the hole diameter rather than the capacity of the drill.
“The mud cleaning system is a function of the hole diameter,” says Heinen. “The rule of thumb is the pump should provide 1 liter per minute per millimeter in diameter (6 gallons per minute per inch in diameter). Your annular velocity should be between 3 to 6 feet per minute to maintain a clean hole.”
As an example, 132 gallons (500 L) per minute would be needed for a 20-inch (508 mm) bore. As for fluid supply, there should be enough clean fluid in the mixing hopper to pump a minimum of 10 minutes of fluid at the maximum pump capacity. An example here would be 4,000 gallons (15,152 L) of clean mud to supply a 400 gpm (1514 L) pump. The mixing capacity, which is how much mud the system can create at a given time, should be three times the capacity of the pump. If we are still working with a 20-inch (508 mm) hole and a 400 gpm (1514 L) pump, the mixing capacity should be 12,000 gallons (45,452 L).
Mud systems and reclaimers typically have similar structure no matter the manufacturer. The engine needs fluids checked daily. “Just like any machine, the engine is a daily maintenance check,” says Heinen.
Maintenance includes weekly greasing of pump bearing packs and general cleaning of the unit. The cones and screens on the reclaimer need continuous on the job maintenance, according to Heinen.
“For Vermeer systems and reclaimers, make sure the shaker screens are consistently wet. And as soon as you see blinding or blocking, use a power sprayer to make sure that those screens are functioning properly. Desander and desilter cones are wear items. You can visually see if they’re working properly. If the discharge isn’t consistent across all of the cones, or if fluid comes out like soft serve ice cream, something is not working properly and the system requires attention.”
These maintenance tips are generally universal for any HDD and mud system, regardless of manufacturer, capacity or size. However, you should always refer to the manufacturer’s maintenance manual for proper instructions. Proper planning before an HDD job and vigilance during the operation will help to ensure a successful bore.
FOR MORE INFORMATION:
Vermeer Corp., (888) 837-6337, www.vermeer.com
Comments