May 2011, Vol. 66 No. 5
Rehabilitation
Aussie technology goes global with joint venture
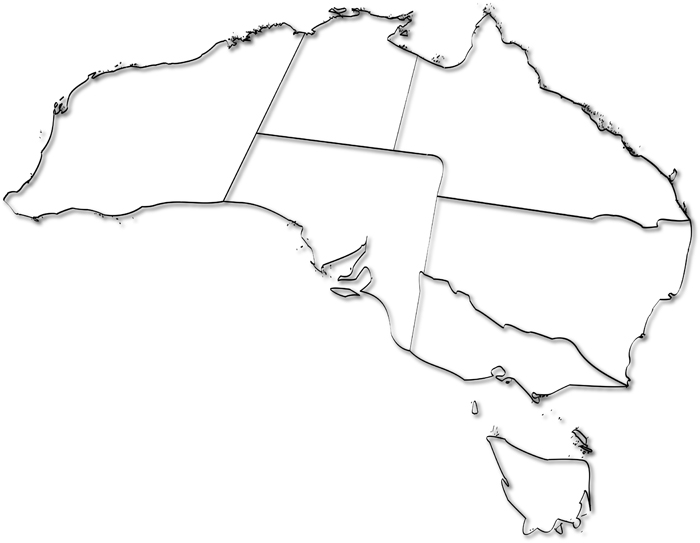
Interflow Pty Limited, a company with some 75 years experience in the pipeline industry, has since 1991 been a leading provider in Australia and New Zealand of repair, rehabilitation and renewal services for deteriorated underground non-pressure pipelines.
More recently, the company has been instrumental in developing technologies including the Interfit system for lateral connection sealing.
Established just four years ago, Germany-based Fluvius provides an extensive range of services for pipe and sewer renovation. Now these two major industry names have joined forces to bring Interflow’s Interfit lateral connection sealing system to the broader global market.
Approved for use in Australia since 2001, the Interfit system has been used to complete over 40,000 lateral connection repairs and seals to date. The system is designed to effectively seal lateral connections subsequent to lining the main to establish a fully sealed renovated pipe network. Investigations have shown that the system provides installations with a very low failure rate.
The Interfit system is applicable to main pipelines from 150 mm (6 inches) to 300 mm (12 inches) in diameter, with lateral connections of 100 mm (4 inches) and 150 mm (6 inches0 diameter where it can provide strong and robust structural seals that are installed from inside the main pipe without the need for surface excavation. As the majority of the world’s lateral connections fall into this size range, the system can be utilized on a very high percentage of junctions.
Based on a patented sock design, the Interfit process uses a proprietary resin ensuring that installation are simple and fast while being very effective. The sealing sock can be designed to accommodate lateral connections with incident angles to the main pipeline from zero to 90 degrees, covering most commonly encountered circumstances.
The patented sock design comprises a PVC coated glass fiber flat sheet that is shaped and stitched lengthwise according to the requirements of the lateral connection being sealed.
The resin used for the installation of the sealing sock is a two-part silicate resin, which has a long pot life (20 minutes) while offering a short cure time (30 minutes) without the need for heating or UV curing. This allows time for operators to properly prepare the seal before installation and yet ensure high productivity with the short cure time allowing several installations per day if required. Application of the resin to the sock also uses innovative technology to ensure an efficient impregnation operation on site.
Once prepared, the seal is fitted to a small, lightweight, low friction, flow-through and low cost installation packer that is easy to use and has no moving parts or electrical requirements. The packer design is available as a ‘short’ or ‘long’ lateral arm version depending on the length of installation required into the lateral connection. The integrated flow function means that installations can be performed without the need to fully seal off the main pipe flows.
With the seal fitted, the loaded packer is pushed (or pulled, depending on access requirements) into position along the cleaned mainline pipe to the lateral to be sealed. The seal is placed into the lateral during this positioning operation. Once in place the packer is inflated with compressed air pushing the impregnated seal against the inner walls of both the mainline pipe and the lateral. While cure time is just 20 minutes, to ensure that local ambient conditions are taken fully into account it is good practice to hold the packer inflated for 30 minutes which ensures a robust seal is achieved before the packer is deflated and removed from the main pipe.
The installation process ensures that, as the packer is inflated and the sock pushed against the host pipe walls, three-dimensional expansion of the seal into position is achieved.
Comments