March 2011, Vol. 66 No. 3
Features
Two Methods Of Culvert Repair Successful In Indiana
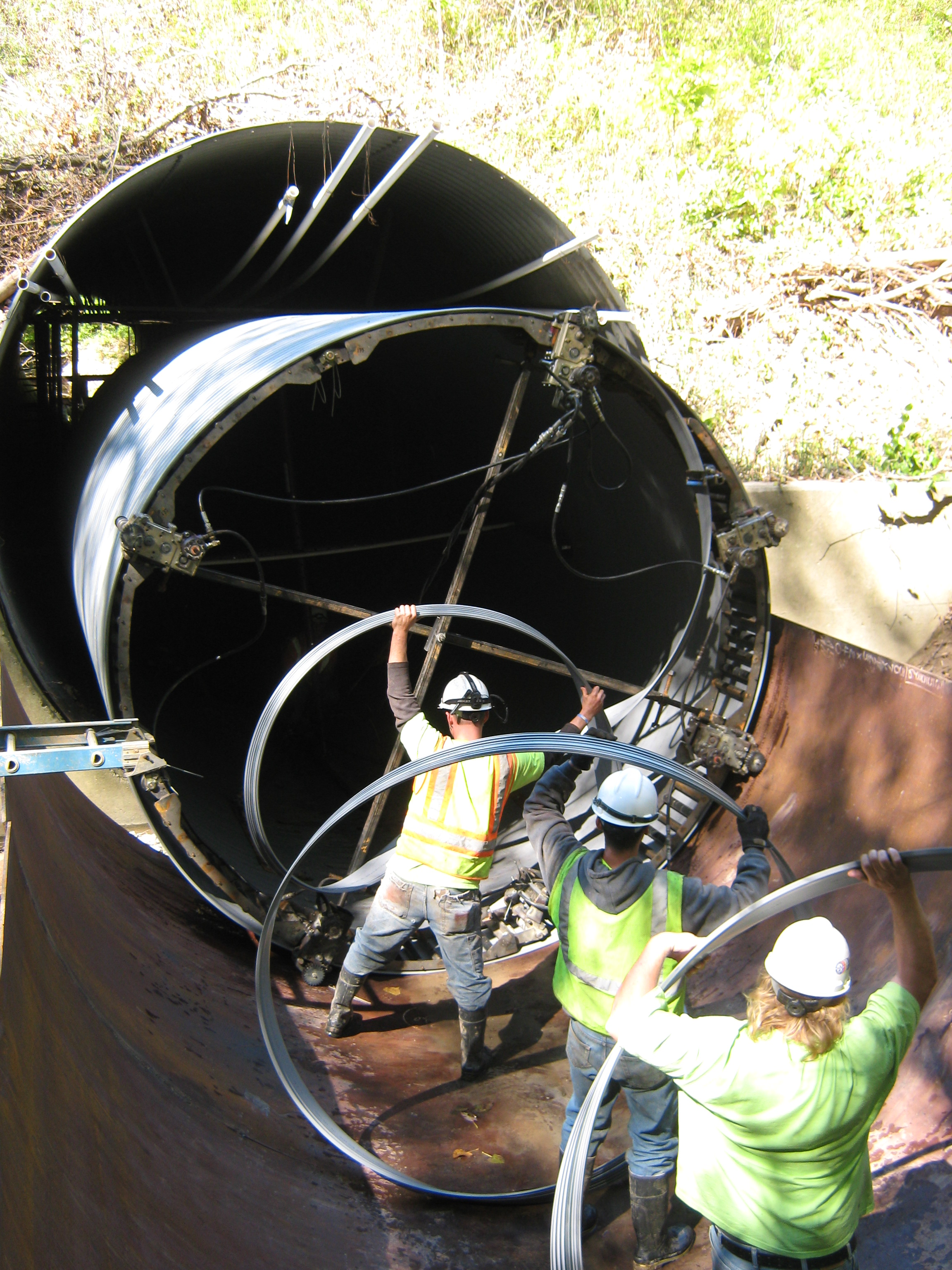
Trenchless rehabilitation of failing underground sewer infrastructure is covered extensively by the industry trade press and even consumer media, but the importance of deteriorated culverts beneath roads and highways typically receives less attention.
Failing culverts can provide costly and dangerous collapses to streets and highways, making culvert maintenance a critical issue for federal, state and local transportation departments. Whenever possible, culverts are rehabilitated, rather than costly and disruptive replacement.
Contractor Indiana Reline Inc. recently rehabilitated two culverts for the Ohio Department of Transportation that illustrates the benefits of two types of sliplining technologies: spiral wound pipe and conventional sliplining.
Indiana Reline Project Manager/Estimator Karl Bates said the spiral pipe project represented the largest Sekisui SPR PVC spiral wound pipe every installed in the United States. The other project, Bates said, used ISCO Snap-Tite culvert pipe liner and included the world’s first hydro-bell structure to provide a larger, wider intake at the culvert entrance.
The SPR liner project was with 132-inch spiral pipe lining installed in a 180-inch multi-plate culvert which had been installed in the 1950s to carry the flow of a creek under two-lane State Road 101 outside Tiffin, OH.
Bates said the project originally called for the culvert to be relined with 132-inch HDPE liner, but ODOT District 2 issued an addendum that allowed 132-inch machine spiral wound PVC liner in addition to HDPE.
Experience counts
Taking into consideration 10 successful projects installing 90-inch machine-wound spiral pipe the previous year, Bates said Indiana Reline was the successful bidder using spiral wound pipe, coming $45,000 lower than other bids.
SPR is a spiral wound liner utilizing steel reinforced, monolithic, interlocking PVC profile strip that is grouted in place with specified cementitious grout. SPR has the capability to negotiate bends and rehabilitate odd shaped pipelines because of the adaptability of the profile.
The basic installation process is to position a winding machine at the base of an access point of the host pipe and spirally wind monolithic panels of PVC into the host pipe to form a continuous, low-weight, watertight liner with high stiffness.
“The area is heavily forested, and we had to cut roads on both sides of SR 101 to bring the materials and equipment to the location of the culvert,” he explained. “Because of the large size of the structure, we built a cofferdam to slow the flow and accommodate flow during rain events when we were typically unable to work for one to two days.
“Originally we intended on using a crane to lower material to the culvert via a closed road. After discussing with ODOT and adjacent property owners, we actually constructed two dirt paths to bring materials down slopes with a Caterpillar 320 excavator and a Cat 277 track skid-steer loader.”
Indiana Reline personnel cleaned the host culvert, installed bracing and blocking between the liner and the host to prevent displacement during grouting, and the SPR liner was installed. No pits were required. In addition, Indiana Reline built two 14-cubic-yard bulkheads, installed internal bracing and pumped 620 cubic yards of 350 psi light-weight cellular grout in the annular space between the host and liner pipes per the project specifications.
The project began in September of 2010 and was completed in November 2010.
Sliplining
The sliplining project with the Hydro-Bell inlet was to rehabilitate 317 linear feet of corrugated metal pipe (CMP) culvert in Wooster, OH, with 63-inch solid-wall Snap-Tite HDPE liner and replacing 30 feet of fill. The culvert was under U.S. Highway 250, a divided, four-lane highway.
The pavement above was already beginning to fail due to culvert deterioration and backfill material loss, said Bates.
First the host pipe was cleaned and runners were installed for liner to slide on. “The existing culvert had deformed from a 72-inch culvert down to 61 inches in several spots, which required hand-mining portions of the old CMP as the 63-inch liner was installed,” Bates said. “Some clearing was necessary, and a bench was cut on the slope above the outlet end as a perch for the CAT 330 excavator used to insert the liner.”
After successful installation and bulkhead construction, light-weight cellular grout was pumped into the annulus between the host pipe and new HDPE liner.
“The deterioration of the host culvert and subsequent loss of backfill material surrounding the culvert resulted in 25 percent more grout being installed than calculated,” Bates said.
ODOT District 3 design personnel’s hydraulic analysis showed that an improved inlet was required to lower the proposed headwater and meet ODOT’s drainage design criteria, and Indiana Reline proposed the use of the world’s first solid wall HDPE Hydro-Bell inlet.
Bates said ODOT District 3 engineers reviewed the proposed solution and accepted the use of the improved inlet based on the fact that the design of the Hydro-Bell allowed for approximately an 18 percent increase in the HDPE liner pipe capacity and also corresponded to a lower outlet velocity.
The project required approximately two weeks to complete and included construction of an inlet end bulkhead.
“Installing a liner in the existing pipe was a great option for several reasons,” said Timothy Farley, PE, ODOT District 3 highway management administrator. “The work
was done without disruption to traffic which given the alternative, to open-cut the site, a road closure and detour would have been needed.
“The project was completed independent of the weather conditions since earthwork, backfilling and asphalt were not necessary. The site was left relatively undisturbed with minimal impact to the ground-side vegetation. A project of this magnitude, installing a liner within the existing 72-inch culvert more than 300 feet long under 35 feet of fill beneath a four-lane divided, limited access highway, proved to be a very cost-effective solution to rehabilitate a failing culvert. This wasn’t a do it yourself project and Indiana Reline demonstrated that through their prompt professional service.”
Based in Sulphur Springs, IN, Indiana Reline was incorporated in 2000 with an initial focus of specializing in sliplining and cellular grouting. Over the past 10 years, Bates said the company has rehabilitated more than 55 miles of culvert and sewer pipes throughout the U.S. and today is one of the largest sliplining contractors in the Midwest, providing design services, construction and on-site technical support.
In addition to sliplining and grouting, the company offers pipebursting and pipe ramming services, HDPE fabrication, hand-mine tunneling and lake and spillway rehabilitation.
FOR MORE INFO:
Indiana Reline, (877) 533-5040, www.indianareline.com
Sekisui SPR Americas, (678) 510-1820, www.sekisui spr.com
Comments