March 2011, Vol. 66 No. 3
Features
GSW Goes Small To Conquer Rock
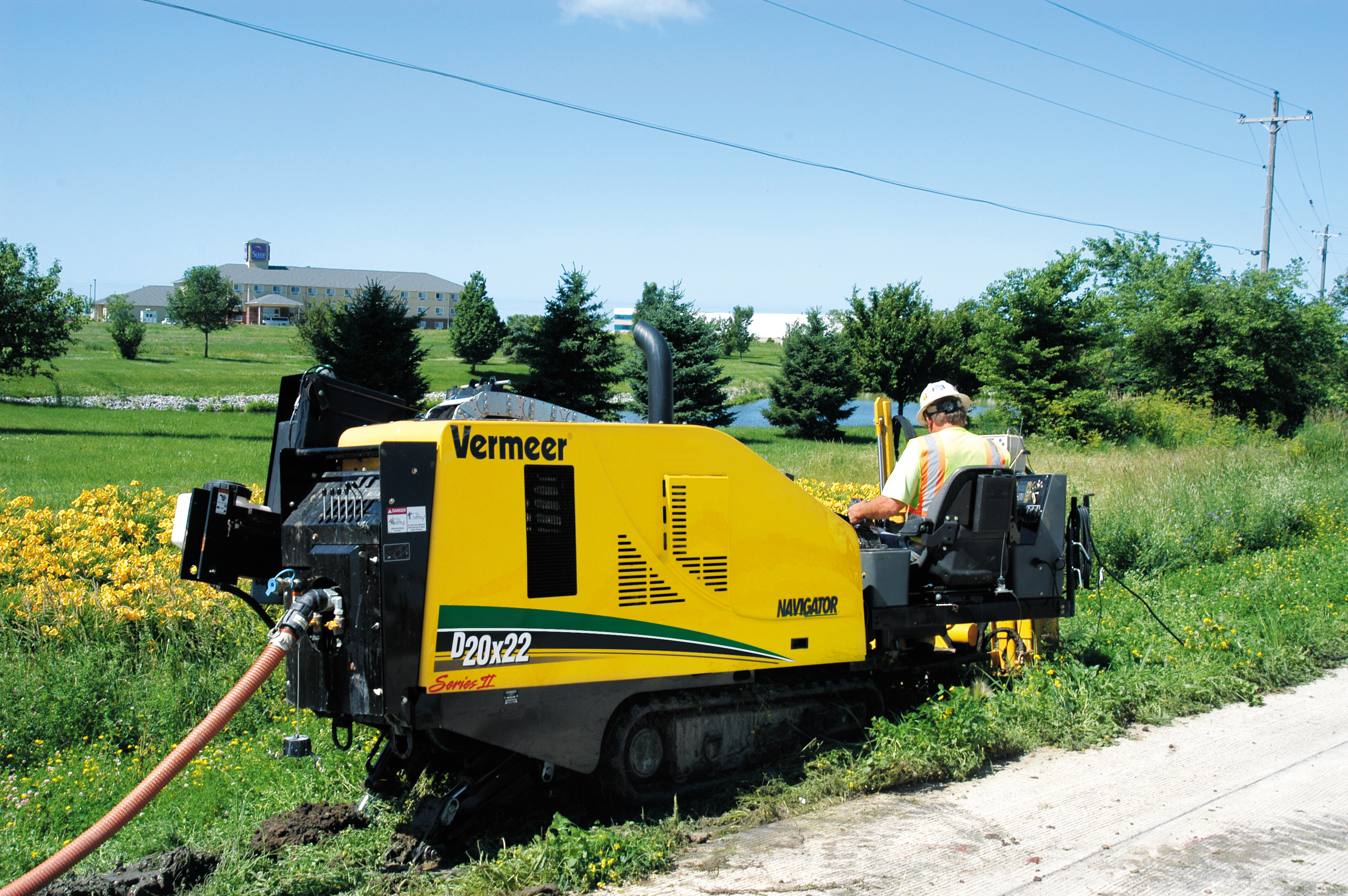
GSW Contracting has found a niche — and in doing so, has uncovered what most would consider an unlikely approach for directional drilling through rock.
Any contractor who has ever encountered a rock formation during an installation project knows all too well that boring through rock is a time-consuming and often costly process; especially if the right equipment isn’t being used. Further complicating matters is the fact that every rock formation is different. Conquering the hard stuff requires an approach that is effective in each unique formation and often involves changing and experimenting with different rigs, attachments, mud mixtures, etc.
But thanks to the resourcefulness, knowledge and experience of Gregg Wilder and his team of installation experts, GSW Contracting, based in Canton, GA., is utilizing an approach that has helped alleviate much of the guesswork of experimenting with various-sized horizontal directional drill (HDD) rigs and attachments for effectively drilling through rock.
“We don’t have to walk away or get our tails handed to us when it gets tough,” says Wilder who ventured out on his own and started GSW Contracting nearly a decade ago. “As utilities have grown and finding installation routes become more challenging, it [drilling through rock] is one of the last areas where installations are now possible. Often times, there is nowhere else to go. GSW has the specialization in drilling through rock formations that allows us to bid and compete for more jobs. This history and our track record of successes have really made a difference. We’ve grown steadily as a result and it’s all been by word of mouth.”
Small is big
The solution Wilder and his team of rock drilling experts have uncovered flies in the face of the long-held conventional wisdom that bigger is better — that to win the boring battle against rock it takes a drill with more power than smaller, more economical equipment. According to Wilder, it’s more about the attachment, the methodology and the approach; not the size of the drill. He cites a telecom installation project GSW Contracting recently completed successfully in Pennsylvania to document his contention.
“We got involved in the early phase of a telecom installation job just as the previous contractor had progressed into an area of solid rock,” Wilder recalls. “We were one of the first contractors to adopt the hammer attachment for boring through rock, especially for smaller-size drills and used the Vermeer D20x22 Series II model drill with a Pioneer One hammer. We were able to set up a lot smaller, shorter shots and because of the size drill we were running and the size hammer, we could operate with a much smaller setup — something that can be a key factor in being able to take on a job.”
Wilder had worked in the past with the engineer who developed the Pioneer One hammer attachment and liked what he had done (compared to other systems) with the control unit and the capability of the hammer. “He’s the only one I knew that really understood that it isn’t necessarily the power behind the drill that’s needed to bore through rock but rather how you approach it and the design of the hammer attachment. The design of the Vermeer D20x22 drill allows for good air flow and hammers are just better tools in tackling rock. It’s very difficult to beat a well-designed hammer, especially when you are battling those really hard formations — those above 10,000 psi. The smaller drill certainly has the power to guide the hammer; plus a smaller drill is more economical to operate.”
The fiber project that Wilder and his crew completed successfully — not to mention likely salvaged for project owner Infrasource, involved installing a 3½ -inch conduit through some 5,000 feet of solid rock, composed primarily of limestone that in some places exceeded 30,000 psi.
“It was some pretty hard stuff,” Wilder says, “and that is where the hammer systems set themselves apart. Some of the formations were more difficult than others due to collapsing rock, but the instincts and experience of our crew using various methods proved successful. We’d been there before.”
Cavalry
After the rock formations had defeated previous invasions initiated by another contractor using a larger drill and experimenting with various drill bits, Infrasource turned to GSW Contracting for assistance. After completing a site evaluation, Wilder’s clean-up crew put their experience to work and took the rock challenge head-on by employing a strategy they had used successfully in similar contests with varying rock formations in the past. After repeated, hard-hitting assaults, ranging from 200 to 500 feet per shot, the rock succumbed. After completing 20 shorter-range bores, Wilder’s crew had prevailed — void of the muscle most felt was necessary to emerge victorious in similar contests against rock.
“We were drilling on average of 150 feet a day,” Wilder says. “There were times when we had to put on a reamer and pre-ream some of the bores and this slowed our production rates accordingly. But in conditions where we could use the hammer exclusively we were drilling close to 40 feet an hour. That’s not too shabby considering it was solid rock that we were boring through.”
The smaller D20x22 Series II Vermeer drill GSW Contracting used to complete the job had several competitive advantages over the larger rigs that had failed previously; including the ability to use a much smaller compressor to clear the bore of spoil. Wilder’s crew used a 375 cfm/ 200 psi compressor that not only used less fuel to operate than compressors often needed to accommodate larger drills, but by weighing in at only 7,000 pounds, it was also a unit that could be transported on site with a more economical towing vehicle, helping reduce operational costs.
In instances where back-reaming was required, Wilder’s crew used a 6-inch reamer to secure unstable formations resulting from occasional mini cave-ins. As Wilder explains, there isn’t much that equipment, attachment or operator can do to control every bore response in the various rock formations that can result in an unstable bore wall. While unpreventable, these situations still affect overall productivity — something Wilder encourages other contractors to recognize as part of the rock contest.
“Do the best you can do with the experience of the operator and the capabilities of the drill but recognize that when drilling through rock some things are simply unavoidable,” Wilder says. “The key is to be aware of the variables up front and account for them when preparing the bore approach and most importantly, the bid. Account for what cannot be controlled and tackle the rest in the most efficient way.”
Know your rock
As Wilder can confirm from having encountered a host of different rock formations, knowing the differences is what is paramount to winning the battle. “Rock varies greatly by geography,” Wilder says. “In the southeastern part of the country the rock is much more solid. You can bore a hole and use much less water, so access to a water source isn’t as much of a factor. In other areas of the U.S., rock formations vary a great deal, so access to water becomes more of an issue because more will be needed to secure a bore.”
The biggest challenge facing contractors who take on projects in areas already clogged with existing utility and fiber service lines is identifying a route to place a new installation. Sometimes drilling through rock is the only option and Wilder appreciates being able to use a smaller drill with a hammer attachment. “The ability to use a smaller setup with a smaller drill and not needing to swap out attachments, all the time really works to your advantage,” he says, “especially in crowded urban areas or spaces already clogged with lines. That’s why we went with a smaller set-up on this job. This was one of those instances where a larger drill just couldn’t have been set up and we were able to complete the job using smaller equipment.”
In the end, the Pennsylvania telecom installation — spanning 400 miles from east to west — was completed successfully. But Wilder contends the overall success of the project can justifiably be attributed to his company’s experience and knowledge navigating pesky rock. “You don’t need a lot of muscle to win the David versus Goliath rock battle,” he says. “You just have to be smarter than Goliath. It’s not about muscle; it’s about strategy. GSW will gladly accept that challenge any day.”
FOR MORE INFORMATION:
Vermeer Corp., (888) 837-6337, www.vermeer.com
GSW Contracting, (404) 925-3499
Comments