March 2011, Vol. 66 No. 3
Features
5,675-Foot x 72-Inch HDD Bore for 48-Inch Pipe Sets New Record
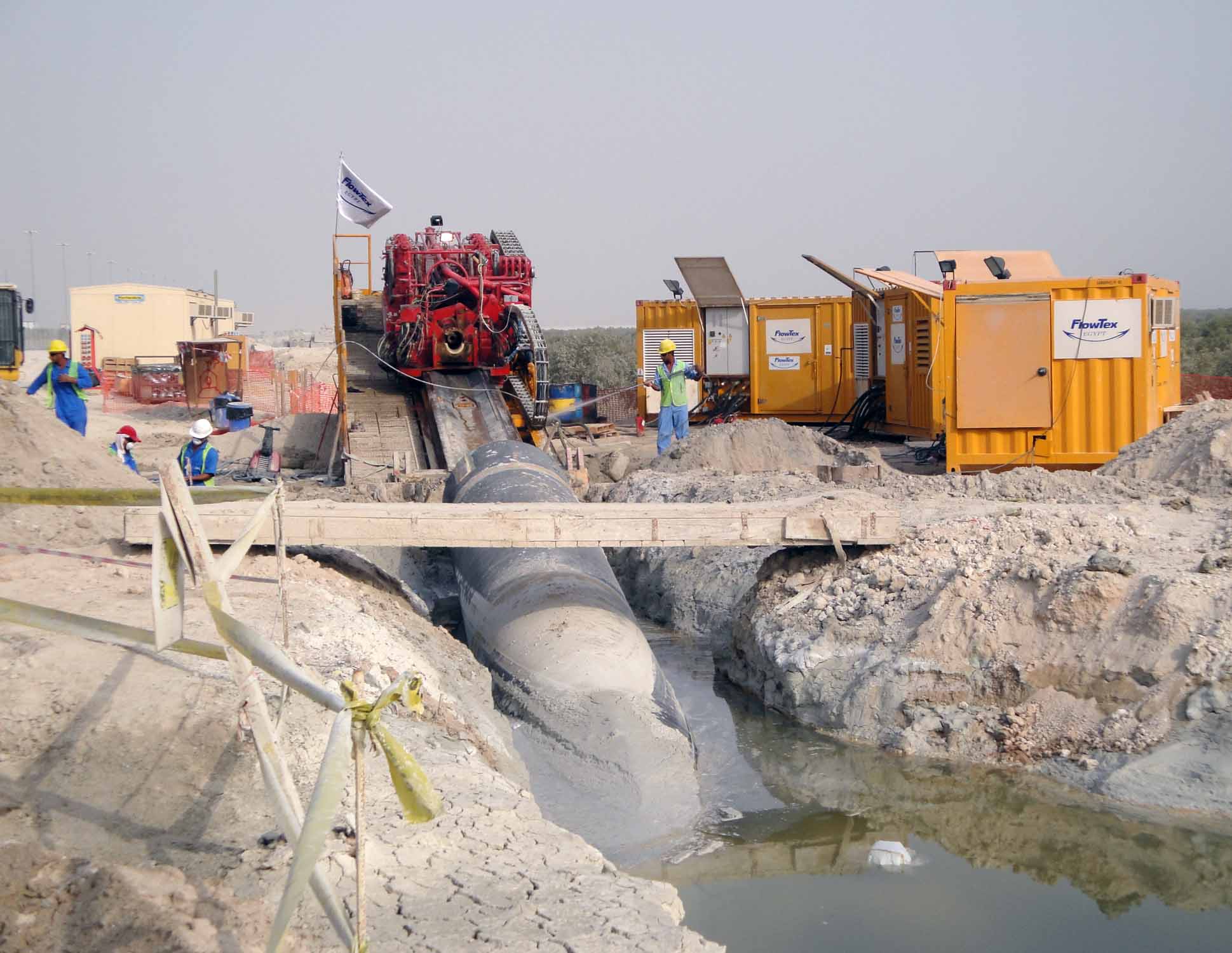
The Abu Dhabi Tourism Authority is developing a mixed commercial, residential and leisure project on a low-lying island just 500 meters off the coast of Abu Dhabi Island.
The Saadiyat Island development, which will cost US$27 billion, will eventually house about 150,000 residents. With a championship golf course, a New York University campus, a world class performing arts center and a 30,000 square meter Guggenheim Museum, Saadiyat Island is expected to become the cultural capital of Abu Dhabi.
Water infrastructure
Extensive infrastructure development, including storm water drainage, sewer systems, electrical grid stations and a water supply and reservoir system are all part of the development.
It was necessary to install two 48-inch diameter water pipes that cross the Abu Dhabi Channel and connect Saadiyat to the main water network in Al Nakheel Junction.
The original route chosen for the pipeline was rejected by landowners and the project was delayed about a year until an agreement was reached on an alternate corridor for the installation of the two parallel 48-inch steel pipelines and a six-inch conduit for fiber optic cable.
In August 2008, Lindenberg Water and Drainage (a division of Lindenberg Emirates LLC), awarded FlowTex Egypt a contract to drill the HDD bores and install the pipelines connecting Al Nakheel Junction with Saadiyat Island. The first 5,280 foot bore was started Sept. 21, 2009 and the product was pulled May 4, 2010. The second 5,675 foot bore started Oct 19, 2009 and was pulled on July 22, 2010. Drilling was accomplished with Herrenknecht 400 rigs. The bores were drilled concurrently with the same drilling tools used on the second bore after completing a pass on the first bore.
Drilling
Drilling the first 12 ¼-inch pilot hole was difficult due to the rapidly changing soil formations which varied from soft to hard to very hard, often within a few meters. The formation was primarily soft calcareous mudstone, siltstone and sandstone with streaks of crystalline gypsum and sections of hard calcarenite. The design radius of 5,250 feet was not achievable in some areas and radii of less than 3,300 feet had to be accepted. Because of the smaller radii it was decided to make the bores 72-inches rather than the 62-inches as originally planned.
Drilling the pilot hole was so difficult it was decided that the tooling ordered for the original corridor would not be suitable for the harder formation found in the present location.
FloTex had just completed a difficult HDD mountain crossing in Madagascar. Midway through that project they had switched to a barrel type hole opener and saw major improvements in penetration rate, tool life and hole condition. They were also aware that in 2008, a barrel type hole opener was used in a record setting 42-inch, 3,050 meter bore in Saudi Arabia in similar formation conditions.
As a result, a decision was made to use the barrel type hole openers with mill tooth cutters on this project. In consultation with the hole opener manufacturer, Transco Mfg. Australia, tools were ordered to open the holes in 26-, 36-, 44-, 58- and 72-inch stages.
The new tools were ordered at such a late stage in the project the pilot hole had almost been completed. This resulted in the reaming having to be started with barrel reamers with pick cutters. As was expected, reaming in the hard sections was extremely slow, and some joints of the drill pipe required two hours to complete.
When the first barrel hole opener arrived it was installed with barrel reamers in the front and at the back. The milled tooth cutters proved able to drill the hard sections much faster than the pick cutters and did not ball up in the soft sections. The rate of penetration was about 30 minutes per joint and could have been faster in some areas if the mud volume could have handled the cuttings. All the hole openers were run with barrel reamers before and after. This bottom hole assembly centralized and stabilized the hole opener and tended to straighten small deviations in the bore. Throughout the job the pull force varied from five to 50 tons, the rotations per minute ranged from 25 to 50 and the mud flow was from 475 to 660 gallons per minute. The sites were active 24 hours a day.
The standard design for the barrel hole openers worked very well up to 58 inches. At that point there was concern that the weight of the 72-inch hole opener would be too much for the softer sections of formation. FlowTex project manager, Ben Boere, along with a Transco sales technician suggested a lighter weight design for the 72-inch tool. In a few weeks time the new tool was produced and air freighted to the jobsite. The light-weight tool worked very well. The torque and pull values were low and the penetration rates were similar to those of the smaller hole openers.
Water problems
Throughout the project, the behaviour of the drilling fluid also caused problems. Since the bore was under water and between islands, salt water influx was a problem. Monitoring the drilling fluid showed that the viscosity was suffering because of the high gypsum content of the formation and the salt water influx entering the hole.
After several tests and remembering past experiences, the drilling fluid was changed to a mud that was based on salt water and salt resistant polymers. The use of available salt water also eliminated the need to haul fresh water to the site.
The pull operation for the last bore was completed on July 22. For both pulls the product pipes were filled with water to provide ballast, protect the cathodic protective coating and keep the pull forces at minimum. This and a very smooth and straight bore resulted in very low pull forces (60 to 70 tons) for this length and diameter of pipe. Each pull operation took about 16 hours, with the rate of the water pumped into the product pipe determining the pull speed.
FOR MORE INFORMATION:
Ben Boere, FlowTex Egypt, benboere@hotmail.com; info@flowtexegypt.com
George Fyfe or Chris True, Transco, 011-618-8326-5599, www.transco.com.au
Comments