June 2011 Vol. 66 No. 6
Features
Rigonomics: Modern HDD Contractor Tools For Drilling Rock
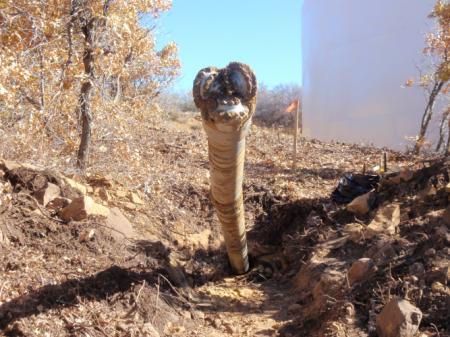
At one time or another, rock is a challenge to most contractors who do horizontal directional drilling (HDD). The degree of difficulty and the efficiency with which rock is penetrated involves many factors, including the size of the drill unit, method of drilling, downhole tools and the experience and capability of drilling crews.
Rock hardness is defined by the compressive force per square inch to crush a core sample of rock. Reports citing the hardness of rock on a project very often are based on estimates, rather than tests of samples. For directional drilling purposes, “soft” rock would be about 5,000 psi and “hard” rock 25,000 psi and higher.
Some contractors are specialists in rock drilling, called in to make difficult installations others don’t want to attempt. They take pride in doing the “impossible.”
Other drilling firms make long bores to install large-diameter pipes and have the equipment and experience to handle most rock bores they encounter, but do projects in a wide range of soil conditions, including rock.
Typically contractors in these two categories operate big, powerful HDD units with 300,000 pounds of pullback and higher that are equipped with mud motors which require fluid recycling equipment for the large volume of “mud” needed to operate the motor. Terrain conditions and depths drilled often mean wireline guidance systems and True Tracker grids must be used.
Depending on site conditions and job requirements, there are options when using mud motors. Contractors who do utility work with equipment of 100,000 pounds or less may encounter rock beyond their capabilities, but downhole bits and reamers and air tools allow 30,000 to 40,000-pound pullback machines to work through surprisingly difficult conditions.
Four contractors representing each of these categories shared rock drilling knowledge and experience for this report.
H&H Enterprises
H&H Enterprises, Andover, OH, and Bemus Point, NY, is a rock specialist working primarily in the Northeastern United States.
“Ninety-five percent of our work is in rock,” said Jason Hockran, vice-president/owner. “We seek out and complete projects in rock and other complex installations that standard HDD contractors are not interested in or are unable to complete. Rock drilling is always difficult and requires a significant amount of planning and communication to meet the project expectations. “Through years of experience in rock drilling and excellent communications with customers, H&H has successfully completed thousands of rock drills.”
One project near Pittsburgh, PA, required drilling 2,200 feet of approximately 18,000-pound psi rock to install 24-inch diameter steel casing for multiple HDPE gas transmission and water lines. An American Augers DD220 was used for the pilot hole and first reaming pass that was equipped with a 6 ¾-inch Adtech mud motor with an 8 1/2-inch sealed bearing tri-cone bit and multiple low-torque Sharewell hole openers of 22 to 36 inches to complete the opening of the hole. An AA DD440 was used for the final reaming pass and pulling in the pipe.
“Most of our projects are more complex and not ordinary in overall scope,” said Hockran. “Recently we completed a project in Pennsylvania in a moderate-hard shale formation that required an innovative approach to fluid management. A frac-out created the need to drill a vertical intersect to our drilled hole and provide a controlled path for the drilling fluids. This was successfully achieved and provided significant advantages for both the drilling process and most importantly, the environmental impact to a nearby stream.”
Laney Directional Drilling
For more the 21 years, Laney Directional Drilling, Humble, TX, has been completing long, difficult horizontal directional drilling installations, many in rock.
About 20 percent of the company’s projects involve rock, estimates Grady Bell, Laney vice president of business development. Many of the company’s rock projects have been notable (see page ?? of this issue for a report about mountain HDD installations through rock that Laney recently completed in Colorado’s Mesa Verde National Park).
Indeed, Laney is equipped to take on any rock projects that come along with 11 Laney-designed and built drill rigs, the smallest with 300,000 pounds of pullback, plus recycling systems, mud motors and all the support equipment necessary.
Alan Snider, P.E., Laney vice president of engineering, said most HDD projects containing rock that are put out for bids typically have rock under 25,000 psi unconfined compressive strength. However, he added, there have been crossings designed and successfully constructed with unconfined compressive strengths in excess of 40,000 psi.
“Planning is critical for drilling through rock,” said Snider. “Accurate geotechnical information is needed to properly plan and prepare for a project.”
Last month, Laney transported equipment, including the company’s 1.7 million-pound pullback drill rig, to West Virginia to start four crossings ranging from 1,500 to 3,300 feet to install segments of a 24-inch steel gas pipeline.
Southern Diversified Technologies
Southern Diversified Technologies (SDT), Brookhaven, MS, specializes in telecommunications construction. The largest of its HDD units has 30,000-pounds of pullback.
“For rock, we use an air hammer and Railhead bit with diamond teeth,” said Jack Freeman, division manager of outside plant construction. “We don’t use mud motors.
“With the air hammer, not as much equipment is needed, and there is much less clean up than when a mud motor is used. Anything we can’t get through, we have subcontractors running 80,000 and 100,000-pound equipment who can bring in mud motors if necessary.”
Freeman said it is rare that the company crews run into unexpected rock.
“We’ve been drilling a long time and have worked in most areas of the country, and we know what to expect when we bid a job, so normally we are aware of rock,” Freeman said. “Engineers that plan projects do a good job identifying soil conditions and anticipating rock so we are very close on our estimates.”
Freeman said SDT crews always are prepared for rock, typically having air hammers and specialty air compressors ready.
One of the toughest rock jobs Freeman recalls was in Leeds in north central Alabama on a fiber optic project. Soil conditions included a granite mix and solid granite for 15 miles. “It was very slow going,” he said, “about 200 feet per day.”
SDT keeps from 18 to 25 drill rigs working most weeks, six are Vermeer and Universal company-owned machines with crews while the balance are subcontractors.
Woods Construction
Woods Construction, Colorado Springs, CO, operates 30,000 and 40,000-pound HDD units working mostly in rock in Colorado, Arizona, Missouri and Wyoming. Most projects are gas, but also includes some water, telecommunications and on-grade sewer installations, said Ed Libby, Woods president.
“We don’t do large-diameter installations,” said Libby, “but much of our work is in rock, and our approach has been to use Ditch Witch All Terrain equipment with dual-pipe mechanical counter bore drilling systems. In the conditions we work in, we believe this is a better choice than using machines with mud motors.”
For a new gas distribution system in Branson, MO, Woods Construction crews installed more than 100,000 feet of HDPE main line pipe with a diameter mix of two, four and six inches. Most services were 3/4, 1 1/4 and 2 inches.
“The rock in Branson was extremely hard,” he added. “We did test breaks at various locations through the project and more than half the rock was more than 20,000 psi. In some areas rock was 31,000 psi on the hardness scale. With our equipment, we drill quickly through rock of 5,000 to 6,000 psi. As it gets harder, production is reduced.
“Our goal going in was to achieve a shot a day with the two JT3020s and one every two days with the JT4020, and on most days we were able to meet those goals. Production would have been double that in good conditions.”
Three hundred bores were made, ranging in length from 80 to approximately 1,320 feet. The average bore was approximately 330 feet.
“The mechanical system uses much less drilling fluid than mud motors would require,” said Libby. “Frac outs were reduced, and we believe there is less downtime with this equipment.”
FOR MORE INFO:
Universal HDD, (847)955 0050, http://unihdd.com/
Ditch Witch, (800) 654-6481, www.ditchwitch.com
Vermeer Corp., (888) 837-6337, www.vermeer.com
H & H Enterprises Inc., (440) 293-8911, www.handhent.com
Laney Directional Drilling, (281) 540-6615, www.laneydrilling.com
Southern Diversified Technologies, (770) 554-4011, www.sdt-1.com
Woods Construction Company, (719) 213-2098, www.woodsconstructionco.com
American Directional Technology (Adtech), 405-449-3362, http://patriotpdm.com
Sharewell, (800) 637-6461 or (713) 983-9818, www.sharewell.com
Comments