July 2011, Vol. 66 No. 7
Features
National Grid Up-Rates Low-Pressure System With Internal Seals
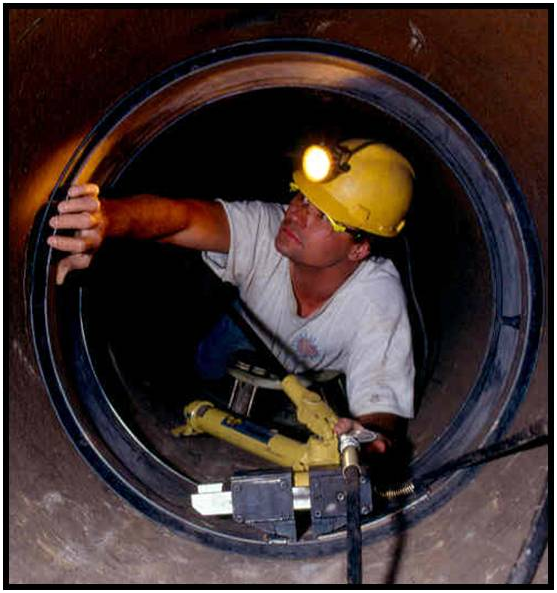
National Grid is an international energy delivery company that is the largest distributor of natural gas and electricity in the northeastern United States. It serves more than six million customers.
To meet its goal of providing safe, reliable service, National Grid has an ongoing program to improve and upgrade its transmission and delivery infrastructure, often using innovative construction technologies to limit disruption of street traffic and normal surface activities in busy urban areas.
For example, a recent project extended natural gas service to Boston University’s East Boiler Plant which was converted from No. 4 fuel oil.
Getting gas to the boiler plant involved several challenges. The source of the gas supply was from a 22 psig (pounds per square inch gauge) distribution main approximately 2,700 feet from the boiler plant. To get gas from the source of supply to the plant would require installation of a gas main along Commonwealth Avenue, a major city thoroughfare with typical urban infrastructure. In addition, Commonwealth Avenue crossed over the Massachusetts Turnpike and CSX railroad tracks — the bridge span was over 400 feet.
“A cost estimate for installing a new gas main within this urban environment proved to be prohibitive,” said Edward Wencis, National Grid project manager. “To install a new gas main across the bridge alone, including a bridge redesign, would cost several hundred thousand dollars.”
This led National Grid to consider other alternatives. “Fortunately,” said Wencis, “there was an existing 24-inch cast iron, low pressure (seven-inch water column) gas main under the north sidewalk of Commonwealth Avenue. This main provided gas service to the local distribution system as well as two university buildings. There was also an existing 36-inch, mechanically joined, steel, low-pressure gas main under the Commonwealth Avenue bridge deck which was also used to support the local distribution system.”
National Grid determined the best option was to take advantage of the existing low-pressure mains by up-rating them to the 22 psig supply pressure.
“In order to utilize these mains,” said Wencis, “a district regulator station was installed to support the local low pressure distribution system. The regulator station allowed the 24-inch cast iron and 36-inch steel mains to be converted to the 22 psig supply system. By using these mains, costs of excavating, installing and backfilling the main along challenging Commonwealth Avenue and costs associated with installing a main under the Commonwealth Avenue bridge deck were avoided.”
Right method
Because the existing 24-inch cast iron and 36-inch steel mains were mechanically joined, a reinforcement method had to be determined to allow the mains to safely operate at 22 psig. Internal joint seals are typically installed on larger diameter cast iron mains in metropolitan areas that can be taken out of service, Wencis said.
“Surface conditions are typically paved roadways or concrete sidewalks,” he explained. “Subsurface conditions typically include heavy infrastructure including sewer, water, drainage, steam, electric, communications and others. The cost for internally sealing cast iron joints, for these applications, is significantly less than conventionally installing joint seals externally. For an external joint seal, an excavation must be made over the joint, the joint cleaned and prepared, an external seal installed, excavation then backfilled and compacted and final restoration applied. In addition, traffic management must be employed.”
Wencis described the Commonwealth Avenue project as a perfect application for the internal joint sealing method. He said the Weko-Seal method was chosen because of its performance track record and competitive cost.
The project was under a stringent timeline driven by the university’s school year. “We could work only during summer break, and the university needed natural gas by early September.” Wencis said. “The Weko-Seal method was a significant contributor to meeting the aggressive time schedule.”
Weko-Seals are manufactured from a nitrile rubber for natural gas applications and EDM rubber for most other applications and are designed to internally and economically stop joint leakage through mitigation of infiltration and exfiltration. Flexible internal rubber leak clamps ensure a noncorrodible, bottle-tight seal around the full inside circumference of the pipe joint area.
Weko-Seal components include the internal joint seal, retaining bands and band shims, an assortment of band wedges, retaining band clips, pipe lubricant, hydraulic expander and air test assembly.
The Miller Pipeline Corp. installed the seals. Work came under a three-year contract to provide approximately 1,000 Weko-Seals annually in 20-, 24-, 30- 36- and 42-inch gas mains.
Installation process
Installation is a man-entry process, said Terry Bell, Weko-Seal product manager. After isolating pipe sections where seals will be installed and making sure the pipe was safe for entry, the steps for installing each seal were:
• Map each section of pipe, identifying the number of seals needed, and take measurements to accurately identify locations of the joints to be sealed;
• Clean the pipe as required and prepare the joint location for seal placement;
• Apply lubricant to the sealing surface;
• Position the nitrile seal over the joint with the test valve located at the 3 o’clock or 9 o’clock position;
• Place carbon steel retaining bands in designated band channel locations and ready the appropriate hardware for the initial expansion;
• An expander tool is used to hydraulically load the retaining bands to predetermined pressures;
• Install a wedge to provide an interference fit with the retaining band design and remove the hydraulic tool;
• Perform a second expansion a minimum of 30 minutes after the initial expansion to ensure the retaining bands received the intended pressure after the rubber seal has been allowed to relax;
• Pressurize the seal to 10 psi. Using a soapy solution, check the perimeter edges for leakage. If there is any indication of leakage, seals are removed and the process is repeated until passing results are achieved; and
• Depressurize the seal and seal the test port with a countersunk, hex-head completion screw.
On projects with a significant quantity of seals, these processes are completed in an assembly-line fashion.
Bell said the crew spent up to 10 hours per day inside the pipe performing sealing activities that included removing debris, cleaning the joints, installing the seal and testing.
“As with any project of this nature, safety for the technicians inside the pipe and the pedestrian traffic was a high priority,” said Bell.
Miller used a six-man crew to complete approximately 110 seals in a seven-day period. A total of four excavations were required with all work taking place at night.
“This exciting project was a ‘win-win’ since the university was able to reduce its energy cost and carbon footprint while National Grid added a customer that is a vital asset to the community,” said Wencis. “In addition, through the assistance of Miller Pipeline, any inconvenience to the city of Boston and the university due to the construction process was mitigated as a result of the accelerated work schedule.”
National Grid is an international energy delivery company. In the U.S., National Grid delivers electricity to approximately 3.3 million customers in Massachusetts, New Hampshire, New York and Rhode Island, and manages the electricity network on Long Island under an agreement with the Long Island Power Authority (LIPA). It is the largest distributor of natural gas in the northeastern U.S., serving approximately 3.4 million customers in Massachusetts, New Hampshire, New York and Rhode Island. National Grid also owns over 4,000 megawatts of contracted electricity generation that provides power to over one million LIPA customers.
For more than 50 years, Miller Pipeline has provided quality construction, maintenance and rehabilitation services and products to natural gas utilities, and the municipal and industrial infrastructure markets throughout North America. With headquarters in Indianapolis, Miller Pipeline employs more than 1,800 construction professionals working throughout 24 facilities throughout the United States.
FOR MORE INFO:
Weko-Seal, 800-428-3742, http://millerpipeline.com/95.html
Miller Pipeline Corp., (800) 428-3742, www.millerpipeline.com
Comments