April 2011 Vol. 66 No. 4
Newsline
Duoline Expands Texas Manufacturing Plant, Examines Corrosion Risks
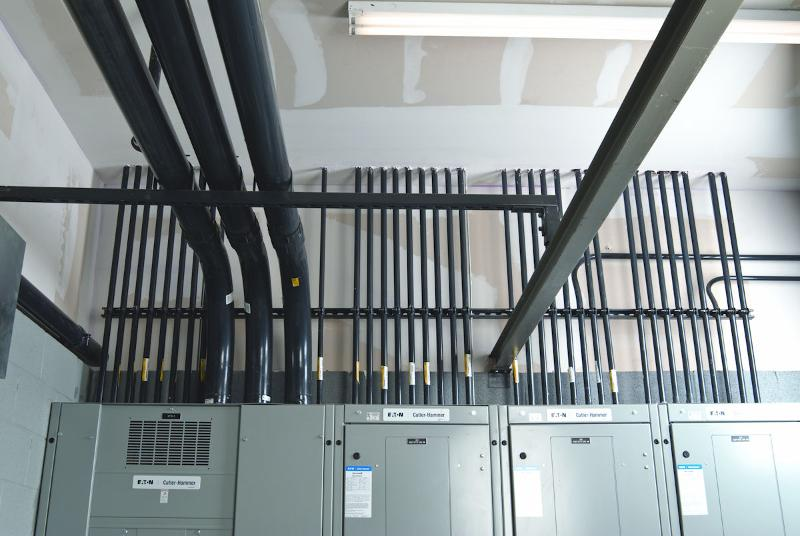
Duoline Technologies recently expanded its manufacturing facility in Gilmer, TX. The company now produces Duoline from an ultramodern, ISO9001:2008 certified, 130,000 square foot plant using a highly efficient manufacturing system supported by advanced process controls and automation designed to provide repeatability and precision.
According to Oscar Zapata, product engineering manager for Duoline Technologies: “In order to accomplish our manufacturing objectives we evaluated every critical building product, including conduit options to protect our electrical wiring systems. This is especially critical in applications, such as ours, where the presence of corrosive factors constitute an ever-present and costly threat for damage to equipment as well as potentially catastrophic compromise of vital systems.”
Zapata points out that proper corrosion management, built upon proper product specification, depends on a comprehensive understanding of regulations and documented product performance. Proven product life predictions are essential for knowing what, within a manufacturing operation, can be relied upon over the course of time for fighting the high cost of corrosion.
“Choosing the wrong material can result in frustrating or even dangerous situations,” states Zapata. He further observes that defining the corroding agents and determining their concentration can be a complex but necessary process. Usually several corrosive elements are present and interactions are not always well documented. Water is the most common corrosive element and is usually present to some extent in every application. Adjacent processing operations or other intermittent activities such as industrial cleaning and the general plant environment may expose the sensitive process equipment to a variety of corrosive agents and temperatures. Each environment is unique and all possible corrosive agents should be identified for the intended application.
According to Zapata: “Should the decision be made to use one material over another without in-depth investigation into potential corrosive media, users may be looking at a very short life span for their most vital systems. For example, before we specified the conduit used for our new plant, we learned how manufacturers of Plasti-Bond rigid PVC-coated conduit went one step beyond their UL listing to ensure customers that they are producing a top quality product . . . if you want to avoid the potentially high cost of failure from corrosion damage, the conduit you buy must carry the ETL-Verification label.”
Comments