April 2011 Vol. 66 No. 4
Features
Cincinnati Seven
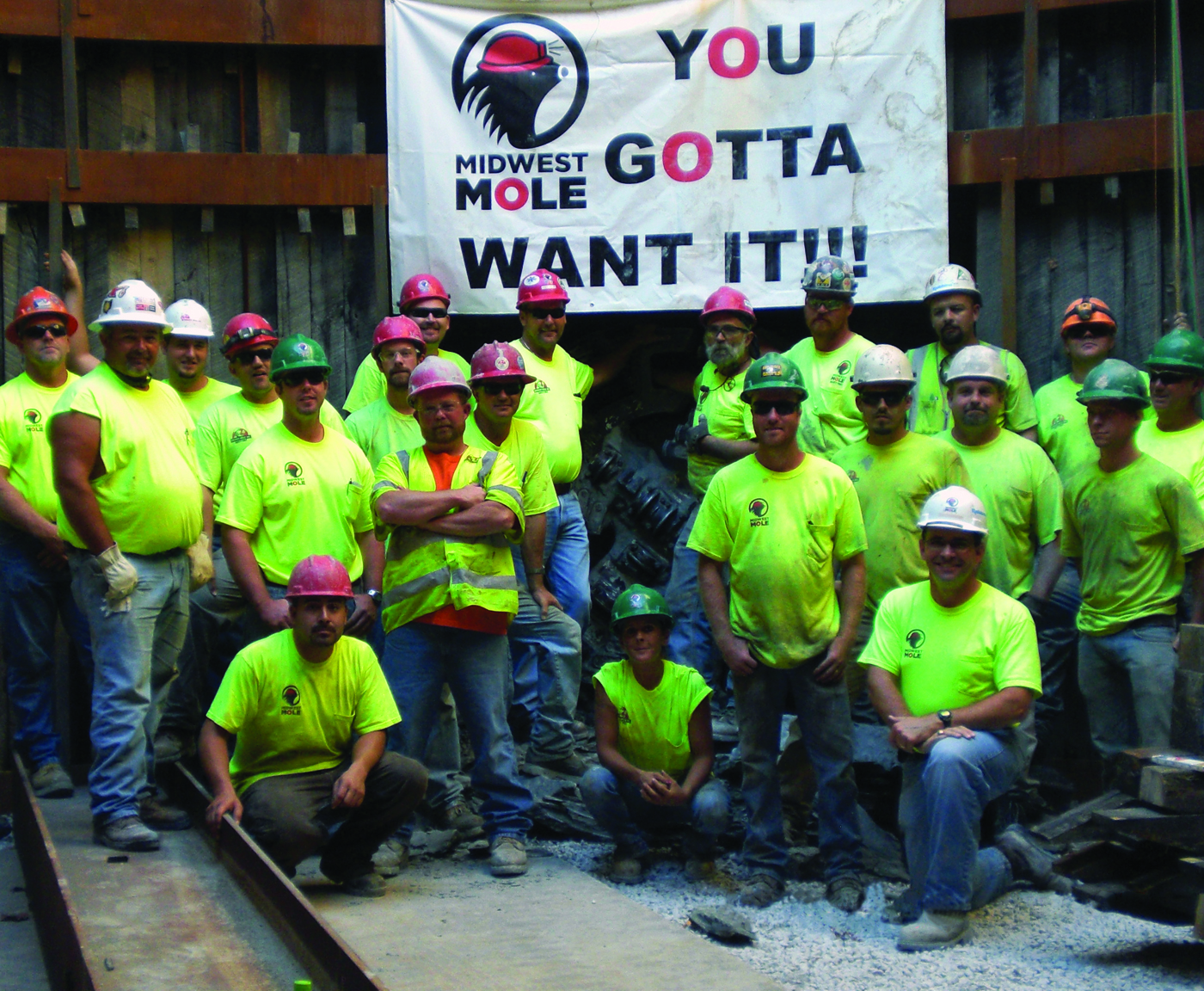
Legend has it that Cincinnati, like Rome, was built on seven hills. Contractor Midwest Mole Inc., Indianapolis, IN, is continuing the local history by constructing seven sewer tunnels in a landmark project that is challenging common trenchless methods for long bores.
Cincinnati’s rolling topography is a key component of the challenging project, resulting in tunnel alignments that range in grade. Ground conditions are correspondingly varied, consisting of interbedded layers of shale and limestone from dry consistency to sticky and wet. Despite the highly changeable conditions, Midwest Mole chose a single machine solution for the pipeline — a small diameter, self-propelled tunneling machine with disc cutters.
The contractor is utilizing a 72-inch diameter Robbins Double Shield Rockhead, to excavate 9,430 feet of tunnel in total, with individual bores ranging from 816 to 2,014-feet long. The entire pipeline is being constructed for the Shayler Run Segment C Sewer Replacement Project in Clermont County, OH. Once complete, the $15 million project will upgrade an exposed sewer system and protect an area surrounding environmentally-sensitive Shayler Creek.
Cleaning up Clermont
The Shayler Run Segment C project is a priority for the project owner, the Clermont County Ohio Water Resources Department, because of severe pipeline erosion in the creek bed. “The existing sewer pipe was installed in 1978 directly into the creek. Since then, the creek has eroded, exposing the pipe to the environment and putting certain sections at high risk of failure. The exposed pipe has now dumped raw sewage into the creek on several occasions,” said Lyle Bloom, sanitation engineer for the Clermont County Ohio Water Resources Department.
The new pipeline is being installed well below the creek bed, crossing the creek multiple times. Cover ranges from 10 to 100 feet, with the majority of the pipeline running some distance from the waterway.
Final carrier pipe will consist of 42-inch diameter Hobas Reline, and will be much larger than the current 24-inch sewer line. “The larger pipe was decided on mainly to allow trenchless construction, though it has the added benefit of providing a larger capacity for future needs in the area,” said Bloom.
Midwest Mole is responsible for pipeline construction, which consists of seven tunnels crisscrossing the creek. Each crossing is connected by a 32-foot diameter launch and receiving shaft, with a total of eight shafts in all. The shafts will eventually become fiberglass manhole structures to access the new pipeline.
Original plans called for 11 shafts and 10 tunnels, but Midwest Mole worked with the project owner to change the alignment and reduce the number of bores. “If there is one thing we would like to emphasize, it would be how willing the contractor has been to work with us throughout the project. They planned value engineering that resulted in substantial cost savings. Midwest Mole proposed to eliminate three shafts from the original bid. They obtained easement rights to alter the project alignment, and shortened the project schedule with their new plan,” said Bloom. All seven of the tunnels and the eight manhole shafts are expected to be complete by May 2012.
Midwest Mole has achieved rates of up to 70-feet per 12-hour shift, with average ranges of 40 to 60 feet per shift.
Adaptable setup
Due to the gravity sewer construction, each tunnel is at a slightly different grade to maintain specified slope. “We needed a machine that could hit the specified manhole locations within a foot of line at one to 2 percent grade,” said Steve Abernathy, vice president of operations at Midwest Mole. The variance results in a change of 177 vertical feet over the course of the project. As a result of the elevation change, the tunnels were predicted to travel through different strata consisting of softer shale and limestone for the first 3,000 feet, changing to harder, drier shale and limestone for the later tunnels. To effectively excavate in the conditions, Midwest Mole needed a solution to excavate mixed ground as well as hard rock up to 24,000 psi UCS.
“The Rockhead was the best suited to the project conditions based on our previous experience with similar Robbins machines. Two-pass tunneling with a Double Shield Rockhead was also more cost effective than microtunneling when we prepared our estimates,” said Abernathy. The original contract permitted either microtunneling or two-pass tunneling, which allows for installation of a primary liner before placing the carrier pipe.
The Double Shield Rockhead was designed with a mixed ground cutter head that can be changed out for a hard rock cutter head later on. The mixed ground cutter head features 6.5-inch single disc cutters and carbide bits, combined with large openings in the cutter head to ingest mixed ground and to allow for cutter changes. The hard rock cutter head is dressed with 11.5-inch diameter single disc cutters and abrasion-resistant muck scrapers, as well as a cutter head opening for cutter changes. Crews can switch out the cutter head between crossings in one of the launch/receiving shafts, based on the ground conditions encountered while tunneling.
Tunnel design called for a primary liner of ring beams and lagging, which is set every 5-feet following each machine push. After each ring is built, a muck train consisting of a battery-operated locomotive and three muck cars removes spoils from the tunnel. The muck will be used as back-fill around some of the shaft sites after project completion, and potentially as fill on private property in the area.
Tunnels 1 and 2
Excavation of the first tunnel began on May 19, 2010, from a 36-foot deep shaft. The Robbins Rockhead completed its first 1,589-foot long drive in three months, holing through on Aug. 18 into a shaft site. “The mixed ground cutter head is ideal for the ground. After the drive there is almost no perceptible wear of the teeth or disc cutters. The machine also drives very smoothly and has plenty of power for these conditions,” said Abernathy.
Crews reported advance rates averaging six-inches per minute in low strength shale using the mixed ground cutter head. Production rates have been as high as 70-feet in one 12-hour shift, and are consistently in the range of 40 to 60-feet per shift, thus producing 80 to 120-feet per day. The swift advance comes despite some unforeseen difficulties — the crew tunneled just four feet below a creek bed into highly saturated ground, requiring temporary diversion of the waterway. Crews cleaned the machine several times and carefully monitored gripper slippage in the soft, wet ground during machine pushes.
The machine was launched from its receiving shaft to bore a second 1,889-foot long tunnel on Aug. 30, following some maintenance and modifications. Changes included modifying the hydraulic system for increased gripper and roll correction cylinder pressure. The increases allow the machine to grip and roll correct in the extremely soft, often wet rock. Other modifications were made to the muck haulage system. “We worked very closely with Robbins to add volume to the muck car boxes. Having a little bit greater capacity in our three muck cars has allowed the machine to be ready to mine after one ring set is completely built. The result has been even greater production with not a lot of wait time,” said Abernathy.
Tunnels 3 and up
Tunnels 3 and 4 were excavated in December 2010 and January 2011 during a bitterly cold winter in the Midwest, including regular single digit lows and highs in the teens. In order to keep tunneling during the adverse weather conditions, the contractor had to heat the machine’s cooling water overnight to keep it from freezing. Cooling water was recycled and filtered, then stored in 2,000 gallon tanks with heaters.
The subsequent drives on tunnels 3 and 4 were successfully excavated through fairly wet ground, as well as some drier material. “We’ve been very happy with the mixed ground head, and are currently planning to use it for all of the tunnels. The rock isn’t very hard and cutter wear has been minimal. We have more risk of a hard rock head getting plugged up and having to stop and clean it than we do using the mixed ground head and experiencing possibly slower production rates or accelerated wear in hard rock — which we haven’t seen at all at this point,” said Abernathy.
Line and grade on all four tunnels has been within limits — a high grade of 1.8 to 2 percent was required in order to maintain the desired slope of the gravity sewer. During tunneling, operators continuously steer the Rockhead using a combination of hydraulic stabilizer pads in each quadrant of the machine’s shield and articulation cylinders.
After tunneling crossing 4, the machine exited into a drop manhole shaft, consisting of a 15-foot change in elevation from outlet to inlet in order to maintain pipe grade. The machine was then removed from the shaft in January while installation of the carrier pipe and the lower 15-foot portion of the manhole was installed. As of early March 2011, a steel plate was being installed to cover the manhole, and the Rockhead was being prepared for launch on its fifth and longest bore of 2,014 feet in April.
Ground in tunnel 5 is predicted to consist of majority limestone with some shale. The route will undercut Shayler Creek with about 20 feet of cover. The final two tunnels needed to finish the job are expected to be much the same, and will measure 1,046 and 816-feet in length. Tunneling is expected to be complete in mid-2012.
Work on the launch/receiving shafts is ongoing; five shafts are now complete using a combination of drill and blast techniques and manual excavation. Some open-cut pipe jacking operations are also connecting existing, peripheral lines to the new sewer line. Midwest Mole recently utilized a 30-inch diameter Robbins SBU-A for a 150-foot long crossing of the creek, which will connect an 18-inch diameter PVC sewer to the main line.
Midwest Mole plans to use the Rockhead machine on future projects in the region after tunneling is complete. The contractor sees few limitations for the machine to excavate long bores. “One of the only limitations on distance is ventilation inside the tunnel. Our ventilation has a limited duct diameter due to the small diameter of the tunnel. We can adequately ventilate 2,000 foot tunnels, but we would need larger size fans for longer tunnels,” said Abernathy.
Overall, he feels that the method has worked well for the long tunnels at Shayler Run: “We have become very efficient at setup, launch, and conveyor installation during the start of each tunnel, as well as removal of the machine after it breaks through each shaft. We have gotten great production and are currently right on schedule.”
FOR MORE INFORMATION:
Midwest Mole Inc., (800) 274-MOLE, www.midwestmole.com
Robbins, (440) 248-3303, www.therobbinscompany.com
Comments