September 2010 Vol. 65 No. 9
Features
Rigonomics: Steering Tools Continue To Lead HDD Revolution
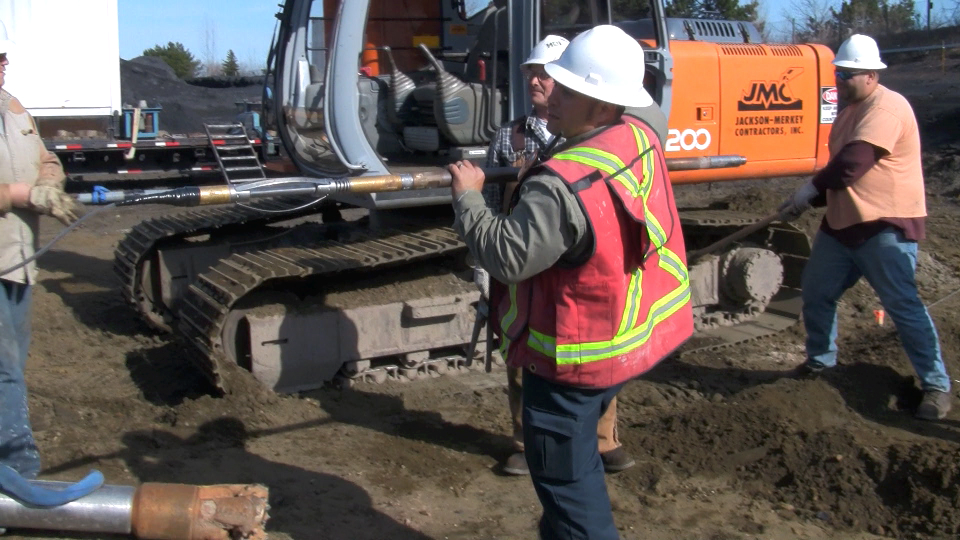
For horizontal directional drilling, the first “D” in the acronym HDD is the key to the success of this versatile trenchless technology — without the directional capability, HDD could never have achieved the impact in utility construction that it has over the last 20-plus years.
Drilling equipment has advanced rapidly since the first compact HDD models developed specifically for utility work became commercially available in the late 1980s. But perhaps no component of the HDD system has changed as dramatically as the equipment to track a drill unit’s drill head and provide information to adjust the path of the pilot hole as it is drilled.
From walkover electronics to wireline and now gyro steering technology, HDD installations can be more accurate and capable of longer distances and greater depths to install larger diameter product.
Today’s walkover systems are more accurate than earlier models, and increased depth capabilities of newer products allows walkovers to be used instead of wireline systems for some installations.
Depending on job requirements, most utility projects with small- and medium-size drilling equipment (generally those with 5,000 to 90,000 pounds of pullback) use the basic steering technology of early drill units: the orientation of a slant-face drill head is monitored by a crew member with a hand-held, walkover receiver that provides information about the location and orientation of the drill head, and that information is used to make steering corrections.
Walkover improvements
The first tracking receivers were modified locators that provided audible signals when the face of the drilling head was in the 12 o’clock position or deviated from 12 o’clock. Crew members often marked each length of drill string to visually indicate when the face was at 12 o’clock.
“The accuracy of today’s walkover tracker equipment is superior to previous units,” said Mike Dvorak, electronics account manager at Ditch Witch. “Equipment improvements have made various applications easier because of improved accuracy, offset tracking and drill through abilities.”
Siggi Finnsson, Directional Control Inc. (DCI) sales and marketing manager, said the ease of use of today’s walkover equipment helps contractors train people faster.
“A focus for walkover systems is to improve productivity,” said Finnsson. “More operating frequencies have also been introduced to help deal with interference.”
Manufacturers continue to make improvements to enable walkover models to effectively make on-grade installations.
“Locating systems capable of gravity-flow installations have been around since the late 90s, and the increase in the number of gravity sewer installations using HDD can be attributed to more accurate locating systems,” said Finnsson.
Ditch Witch’s Dvorak said on-grade installations are the most recent of new applications for directional drilling.
“New and improved technology offers more precision and accuracy that is needed for on-grade drilling,” he added.
Wireline
When walkover guidance systems are not practical or job conditions make their use impossible, wireline steering tools are the most widely used alternative. Wireline systems often require the use of a Tensor TruTracker grid system to eliminate or reduce the effects of magnetic interference.
Steve Cornwall, vice president of Sharewell HDD sales and services, said the most important advance for the magnetic guidance wireline steering tool has been the improvement of the software used with wireline systems.
“This has lead to the use of ‘micro-coil’ and other faster, more accurate capabilities,” Cornwall explained. “A micro-coil is a compact circle of surface wire placed in an uncongested area, like a grassy median on a busy interstate highway. This allows the operator the ability to ‘true-track’ without laying wire across the road.”
Cornwall said that probably the best example of steering accuracy for HDD is an intersect project in which two pilot bores meet and intersect.
“This type of project,” he said, “is attainable with several different types of steering systems and has expanded the ability of contractors to successfully complete jobs that previously were thought to be too difficult to achieve.”
Every locating system — whether walkover, wireline or gyro — has its applications and limitations. The challenge of contractors and suppliers is to match the right system to the project in order to maximize success.
Danny Crumpton, Inrock’s technical sales guidance manager, observes there has been an increase in applications where using surface coils are not possible, usually on deep water crossings where environmental concerns are an issue. New developments eliminate the need for wire grids on the surface.
“The beacon tracking system (BTS) allows engineers to reach out by 300 feet past the edge of where the coils would have to be stopped, giving greater range and tracking capabilities,” said Crumpton. “Equipment can be placed in a specific location and surrounding areas are not disturbed. It is much quicker to setup and is environmentally friendly.”
John English, president of Horizontal Technology Inc., believes misinformation about available steering tools is a by-product of the rapid growth of the HDD industry.
“In order to compare steering systems and select the right one for a job, it is necessary to ask questions,” he said. “Any magnetic steering system is comprised of four components: the steering tool, guidance software, secondary verification system and the guidance technician, who will set up and operate the first three.”
Owners and contractors must select the equipment best suited for each project.
Growth driver
English said the growth of HDD is directly related to the development of a secondary (tracking) verification system.
“The advent of surface tracking allowed HDD to move into more congested areas where the vast majority of construction takes place,” said English. “This is accomplished by creating a precise magnetic field on the surface and using the algorithms of the steering software to locate the steering tool’s position below the artificial magnetic field. The more precise the surface set up and the higher the intensity of the field the more accurate the readings. The most accurate system requires the use of a DC current through a surface wire precisely placed along each side of the drill path. Whichever steering tool or software system is used, the DC surface tracking system is the most flexible and accurate.”
English emphasized that perhaps the most important component of a magnetic steering tool system is its operator.
“There is no alternative for training and experience,” he said.
Jim Cloud Jr., president of Slimdril International, said gyroscopic guidance tool systems (GST) are an option to magnetometer wireline systems. GST systems use highly-accurate gyroscopic sensors to establish measurements relative to the earth’s true north and are not affected by natural or man-made magnetic anomalies,
“Gyro systems have been in use for many years, but most applications have been to locate existing pipelines,” said Cloud. “Slimdril introduced the HDD gyro steering tool to the United States and currently is the only company in the industry offering this technology.”
Cloud said an important benefit of GST steering equipment is the stability of sensors during drilling and rotating, providing highly-accurate (plus or minus 0.04 degrees) measurements relative to the earth’s true north and are unaffected by magnetic anomalies.
“I believe,” said Cloud, “we will see HDD projects that were not feasible or possible prior to recent steering tool advances.”
What Suppliers Say About Their Products, Services
Digital Control Inc., Siggi Finnsson, sales and marketing manager: DCI offers a range of products, with the basic model being a walkover tracking model up to the top-of-the line model which includes wireline and magnetic guidance capabilities. All systems have walkover capabilities. Ease of use and increased productivity has been a particular focus for DCI as well as more locating frequencies and more advanced locating methods such as real time locating and target steering.
DCI has offered gravity-flow installation since the late nineties and this is a standard capability for all but the most basic systems. We anticipate there to be an increase in gravity-flow installations and have made that capability inherent to most DCI systems.
DCI’s entire product line consists of three-dimensional field view locating systems, commonly referred to as “ball in the box” locating in the industry. This is the closest thing available to seeing the drill head moving through the ground. The locating systems are intuitive and easy to operate with ions or menus. They feature real-time locating which improves productivity and makes for more accurate bores. Newer systems have a common user interface and design language so that a transition from one system to another requires very little adaptation. Transmitters are available in different frequencies and depth ranges which should meet most of the requirements of today’s typical HDD bores.
DCI continues to develop ancillary technologies such as the TensiTrak Pullback and Pressure Monitoring System which is used to monitor product pull force and annular drilling fluid pressure.
Ditch Witch, Mike Dvorak, electronics account manager: The 8500 tracking system has features that are not available on other walkover systems. The ability to locate the beacon without finding the front and rear “ghost” signals is a key to quick and accurate locates. Another key feature is the 8500’s “drill through” mode that allows the driller to drill not only to the tracker, but also beyond the tracker. This feature is very important when crossing busy streets and highways, and when there are obstacles in the bore path. The offset locating feature also can be used to track the beacon when obstacles are in the bore path.
The accuracy of the tracking electronics is key to making grade bores. The Ditch Witch 8500TK is superior in its accuracy for use in on-grade installations. In addition, Ditch Witch manufactures downhole tools that are specifically designed for on-grade applications.
Horizontal Technology Inc., John English, president: We are a global horizontal directional drilling (HDD) company and supplier of a comprehensive range of HDD machines, drilling tools and equipment. We also provide HDD guidance services, HDD inspection and monitoring services, magnetic steering tools, wireless steering tools, down-hole pressure tools, high torque motors, tri-cone drill bits, rock reamers, PDC rock reamers, hole openers, PDC hole openers, under reamers, split bit reamers, drill pipe, non-magnetic collars, jetting assemblies and pipe rollers.
“What sets us apart,” said English, “is that we are not promoting one system over another. Our goal is to provide the best steering service available because that is what is most beneficial to the HDD industry. There is no alternative for training and experience, and we consider our professional guidance technicians the industry’s best.”
Inrock, Danny Crumpton, technical sales guidance manager: Inrock is recognized as a global leader in providing HDD performance drilling tools, equipment and services solely dedicated to the development of dynamic HDD. Inrock is a pioneer in HDD rock-drilling projects.
The ParaTrack 2 Steering System has many advantages, underground track, intersect technology, single wire and the ability to lay coil configurations out that previously were unthinkable. Operating cost is reduced because there is no need for welding machines and personnel. It also allows for deeper depths with better accuracy.
ParaTrack 2 allows the field engineer to lay surface coils out that are offset from the bore path, and having a return leg of the coil far away. Single-wire applications in specific job sites allow the engineer to lay out a coil quickly. The ParaTrack 2 system has successfully tracked bores to depths greater than 1,000 feet.
Sharewell, Steve Cornwall, vice president HDD sales and services: The cold truth about MGS wireline steering tools is they all have the same accuracy. What sets Sharewell apart from others is our personnel in the field operating steering systems for our customers. Experience is the key to any successful job, and we have some of the most experienced field people in the industry.
As HDD projects become more complicated and difficult, we will find ways to overcome the limitations of any steering system. Challenging projects force us to expand our abilities to meet the needs of our clients.
SlimDril International Inc., Jim Cloud, president: SlimDril offers both magnetic steering tools with magnetic tracking and the Drillguide gyro steering tool (GST).
At this time Slimdril International is the only company in the industry offering gyro steering tools. Drillguide GST sensors provide nearly continuous communication from downhole to the surface The GST accurately measures the azimuth and inclination which provides the drilling crew a real-time survey of the drilling progress and facilitates corrective steering actions when needed.
Drillguide software incorporates a bore planning component that works off of established GPS coordinates to enable the drilling crew to more precisely follow the designed bore-hole curvatures, especially important in congested rights-of-way and other sensitive locations where other technologies have difficulty achieving the required accuracy. SlimDril will continue to advance this technology, and make it the most accurate and feasible tool in the industry.
FOR MORE INFORMATION:
Digital Control Inc., (800) 288-3610, www.digital-control.com
Ditch Witch, (800) 654-6481, www.ditchwitch.com
Horizontal Technologies, (713) 774-5594, www.horizontaltech.com
Inrock, (713) 690-5600, www.inrock.com
Sharewell, (800) 637-6461 or (713) 983-9818, www.sharewell.com
SlimDril International, (281) 391-5800, www.slimdril.com
Comments