November 2010, Vol. 65 No. 11
Rehabilitation
Fused PVC Pipe The Answer For Pipebursting Projects Across The Country
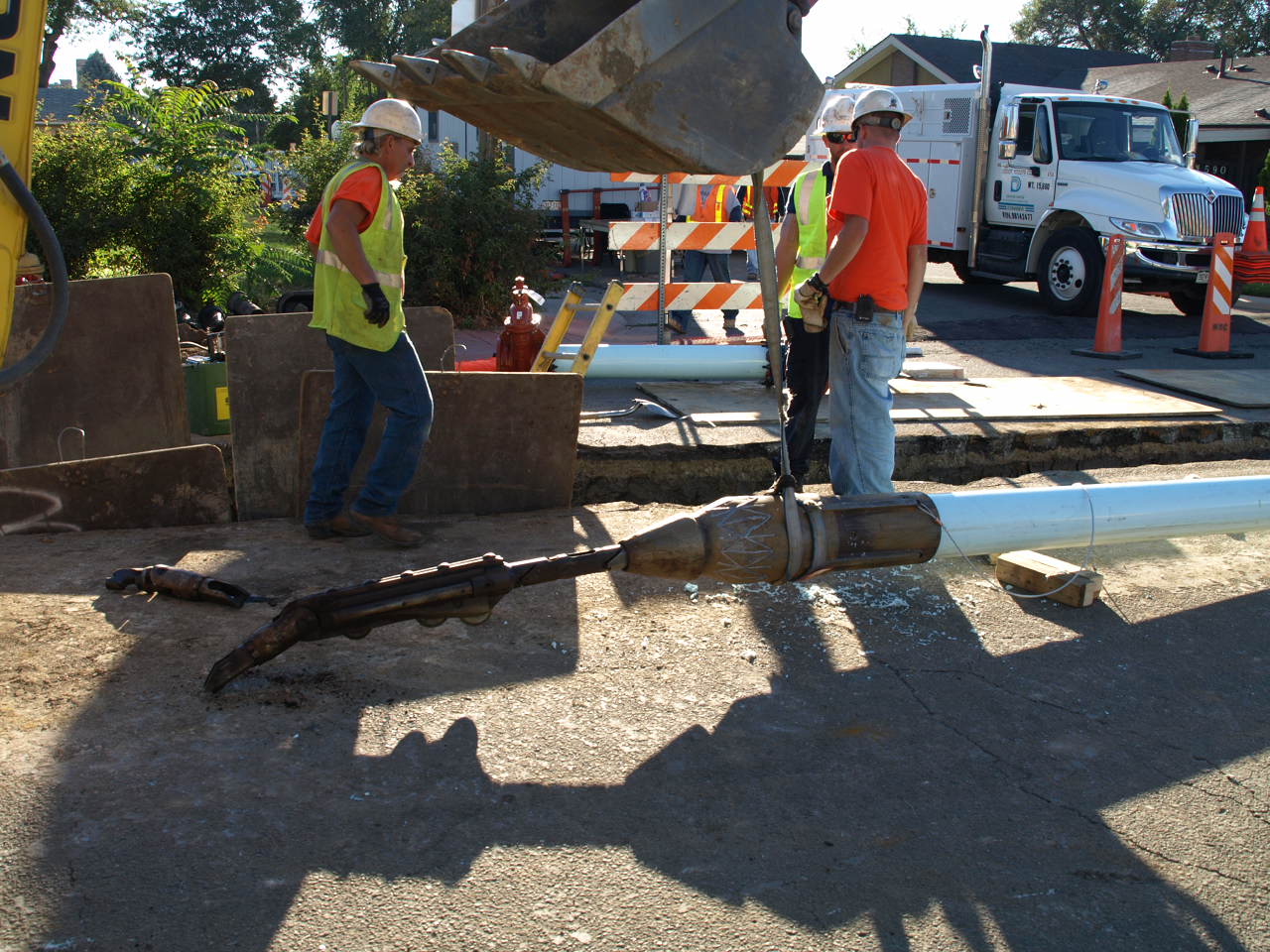
“Quick and quiet,” is how John Riera, Water Resources manager for St. Petersburg, FL, describes a recent pipe bursting project using fused PVC piping in a residential area of his city. “Homeowners appreciated the speed and minimal disruption of the project,” he says. “We didn’t have a single complaint.”
Speed of installation and reduced surface disruption and damage are among the main reasons communities across North America are shifting to fused PVC piping in pipe bursting projects. Ease of upsizing and the ability to use standard fittings and compatible materials are other key factors.
St. Petersburg used fused PVC in a pipe burst of 1,200 linear feet of eight-inch cast iron pipe located just a few feet below manicured lawns and driveways. Disruption of the surface in this expensive residential area was not an option.
Billings, MT, burst an aging water main and chose to replace it with fused PVC pipe which had both a higher safe pull force and a higher inside diameter (ID) to outside diameter (OD) ratio than alternative piping materials.
And in California, several communities are using fused PVC for pipe bursting, including the city of St. Helena which rehabilitated and upsized a failing water line tucked between a highway, rail line and historic vineyards.
The developer and provider of Fusible PVC piping systems is Underground Solutions Inc. (UGSI) of Poway, CA. The company’s Bo Botteicher explains that the most common difficulty with pipe bursting projects is the increase in pipe diameter, or upsizing, of the replacement pipe compared to the existing pipe.
Fusible PVC pipe has a reduced wall thickness and hence a smaller OD due to the hydrostatic design basis for PVC, in general. These features result in higher flow rates and smaller bore hole requirements, important considerations in pipe bursting applications where enlarging the piping channel could lead to surface disruption, interference with other utility lines, or other issues.
“Eliminating or reducing the degree of upsizing in pipe bursting reduces the risk that soil displacement from the operation will disturb adjacent underground utilities or cause surface heave,” Botteicher says. “In the past, PVC pipe required gasketed or solvent cement mechanical joints, and these joining techniques often limited or prevented its use in trenchless applications.”
Now, however, UGSI technology is enabling customers to install continuous, monolithic, gasket-free PVC pipe – with high-strength fused joints – and take advantage of the hydraulic efficiency, stiffness, ease of repair and lower cost of PVC over alternative piping materials.
In addition, Botteicher points out that both fracturable pipe (cast iron, clay, ac pipe), as well as non-fracturable pipe (steel, ductile iron) are being burst using fused PVC pipe.
The St. Pete story
Pipe bursting with fused PVC pipe was a logical choice for the St. Petersburg project. The 40-year old cast iron water main had become corroded from tidal influenced groundwater and needed repair or replacement. But it was situated just three feet below the surface and ran beneath upscale landscapes that the city did not want to dig up or disturb.
By deciding to use fused PVC pipe from UGSI, the city was able to replace the 8-inch diameter, 1,200 linear foot line along Snell Isle Blvd. and attain the desired ID without having to increase the diameter of the pipe channel. The risk of heaving the ground surface and possibly cracking driveways and sidewalks was avoided.
WRS Compass of Tampa, FL, performed the pipe burst. USGI provided the pipe and fusion services.
City crews performed all of the related construction, excavation, restoration and tie-in work. Just three pits were required – a “jacking pit” at each end of the line, and a common pit in the middle. The contractor fed the 8-inch Fusible C-900 DR18 pipe from either end and joined the lines in the middle. Small potholes allowed reconnection of 29 residential taps and hydrant connections to the new water main. City personnel were able to execute all the tie-ins themselves, because working with PVC eliminated the need for electrofusion saddles.
According to Riera, “The job was completed under budget, and homeowners were pleased with the speed and minimal disruption.”
Riera said his department held meetings with the property owners and distributed literature on the technology prior to the project. That, plus the minimal disruption in the yards and driveways, led to a complaint-free project.
Bursting in Billings
In Billings, MT, water pipes were similarly deteriorated, but the city wanted to upsize the 8-inch diameter to 12 inches. The city originally had planned to fuse HDPE pipe and install it using static bursting methods. But, after a few trials with HDPE and other pipe materials, the project managers decided to try bursting using fused PVC.
The city owns its own fusion machine and bursting system to slit and burst the cast iron pipe, and a number of city employees received UGSI training to become licensed in pipe fusing.
The city’s first project, 520 linear feet beneath Third Avenue North, was completed in November 2008, and Billings has elected to continue using pipe bursting technology with fused PVC pipe throughout its long-term water main replacement program.
The adoption of fused PVC pipe for its pipe bursting application was driven by several factors. For one thing, the city was familiar with PVC piping, having used bell-and-spigot PVC pipe throughout its system. It also stocks standard fittings, and has crews familiar with tapping and working with PVC pipe.
Another factor was pull-strength. For the Third Avenue project, the fused PVC pipe had a safe pull force of 101,600 pounds. By comparison, other piping materials under consideration had lower safe pull forces, especially around bends.
But the biggest reason was upsizing. The difficulty of a pipe burst project relates directly to the increase in size (upsizing) of the new replacement pipe relative to the existing pipe. Using 12-inch DR14 Fusible C-900 pipe, the city was able to expand the 8-inch ID lines to the desired 12-inch ID. If HDPE pipe had been used, it would have had to be upsized to 16 inches to provide an equivalent ID.
The pipe was fused, pulled and pressure tested in early November 2008. Kent Lustig, project manager for the city, commented: “Overall the project went well. Fusible PVC pipe looks like the way to go on future water main burst projects.”
Billings maintains over 400 miles of water mains throughout the city, much of it cast iron pipe and some of it nearly 100 years old. Going one block at a time, the city has replaced and upsized about 3,000 feet of water main thus far, with another 27,000 feet in line for future replacement.
Tight quarters in St. Helena
Upsizing and difficult installation conditions were the reasons behind the choice of fused PVC in the pipe bursting project in St. Helena, FL.
In April 2010, Team Ghilotti of Petaluma, CA, began rehabilitation of a 10-inch welded steel water line running approximately 3,000 feet south from the downtown area.
The pipe needed to be upsized to 12-inches in diameter, and the installation conditions were very tight. The line ran between a major highway and the historic Napa area vineyards, and alongside a main rail line.
Comments