November 2010, Vol. 65 No. 11
Features
Michigan UP Excavation Challenges
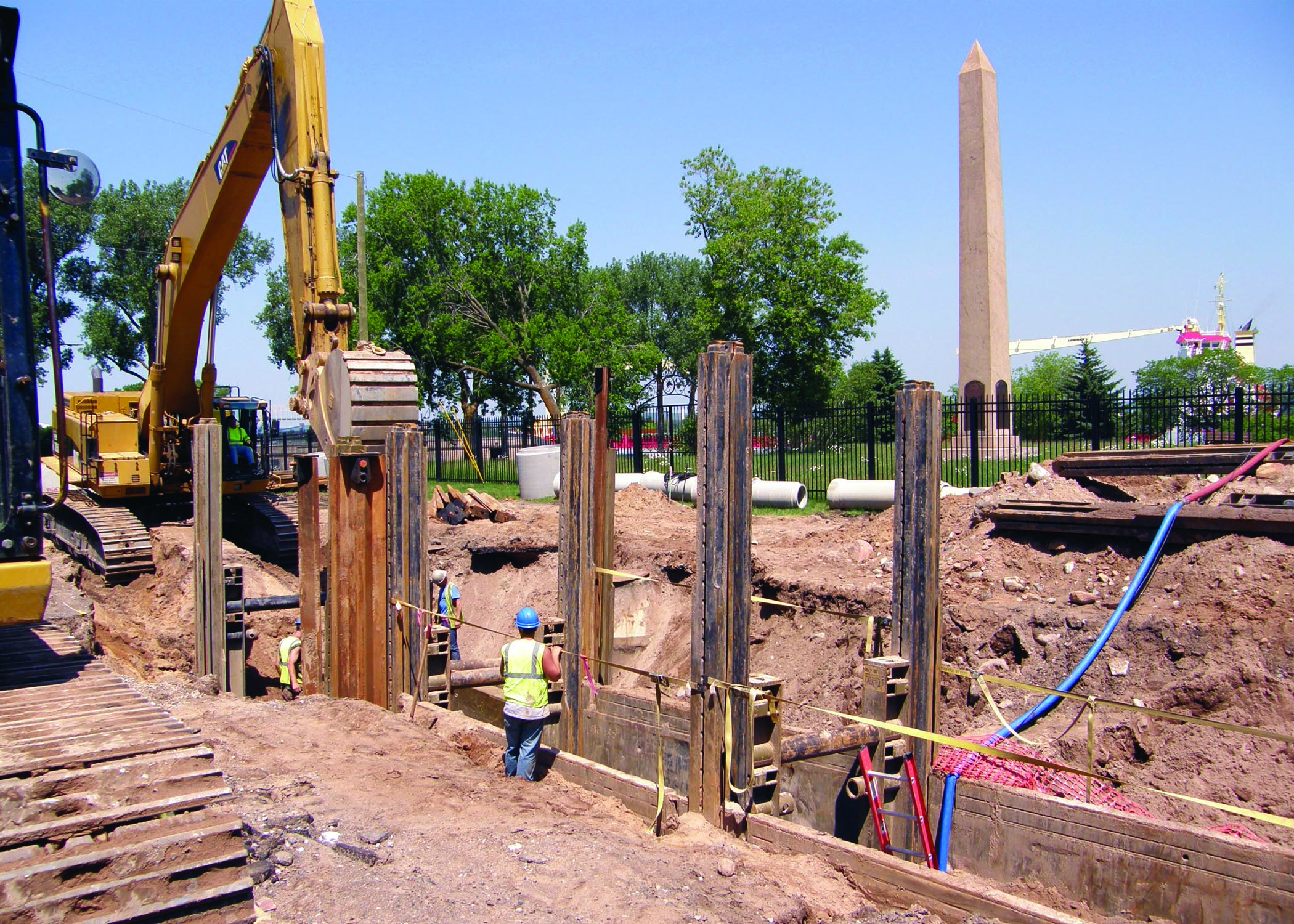
Sault Ste. Marie, MI, like so many other communities, is in the midst of storm-sewer separation upgrades. For many cities, that can mean miles of new pipe or upgraded utilities. Sault Ste. Marie has a unique challenge in that its historic downtown area is essentially an island, with the famous Soo Locks closely adjacent to the excavation area.
Taking on a part of this very unique and difficult project is Bacco Construction Company, headquarter in Iron Mountain, MI, in the center of Michigan’s Upper Peninsula. The $9.5 million CSO Control C-1 C-2 Div A project entails installing 2,000 linear feet of new sanitary sewer pipe as deep as 28 feet, with an average depth of 22-24 feet.
Ironically, it was not Sault Ste. Marie’s adjacent historic buildings and Indian Burial Park that were the biggest excavation challenges for Bacco. Certainly, maintaining the surrounding buildings and structures was important. First and foremost was the safety of the workers due to the depth of the excavation. The other major factor came down to cost and economics.
“Sault Ste. Marie requires Class 3 sand as backfill which is very expensive, especially in the Eastern Upper Peninsula,” said Chris Wentland, Bacco’s project superintendent. “It was very important that we excavate out as little dirt as possible, but also move as quickly as possible.”
Given this consideration, it left Bacco with very few excavation and shoring options. Bacco contacted Efficiency Production Inc., a leading manufacturer of trench shielding and shoring equipment, for consultation and solutions.
Slide rail meets safety requirements
“We knew that Efficiency had a slide rail (shoring) system that seemed like it would work great, but we had never used slide rail or even seen it used,” continued Wentland. “Efficiency sent us out to Salt Lake City, Utah, to see the system in use.”
Explained Mike West, Efficiency Production’s vice president of engineering: “There are a couple of contractors in Salt Lake City using hundreds of feet of slide rail to install the big aqueduct system there,” he said. “One contractor has been using our system for several years, so it was a great example for Bacco to see how slide rail would work on their project.”
Efficiency’s Universal Slide Rail is a component shoring system comprised of steel panels (similar to trench shield sidewalls) and vertical steel posts. The versatile system can be used in a variety of configurations, such as small four-sided pits; large unobstructed working pits as big as 50 by 50 feet with Efficiency’s ClearSpan System; or in a linear Multi-Bay configuration to install pipe lengths of more than 40 feet.
After returning from Utah, Bacco rented a slide rail ystem configured in a 6-bay, Linear Multi-Bay application.
A slide rail systems is installed simultaneously as the trench or pit is excavated by sliding the panels into integrated rails on the posts – either double or triple rails depending on needed depth – then pushing the panels and posts incrementally down to grade as the pit is dug; a process commonly referred to as a “dig and push” system.
Cost savings
After an initial learning curve, Wentland said that they were typically getting in 80 to 100 linear feet of eight-foot long, 18-inch diameter reinforced concrete pipe per day at an average depth of 22 feet. “This (slide rail) really is the perfect shoring system for this type of soil,” explained Wentland. “The heavy clay we were encountering is always moving, flowing. With this system, the panels seal off the trench from the dirt that’s constantly shearing in. It can withstand a lot of soil pressure,” he said.
Bacco is moving east to west, along E. Water Street and East Park Place, across from the opening to the Lake Huron or “downriver” locks. Parts of the new sanitary sewer line was installed just below the old line which runs down the center of the two concurrent roads. Here again, slide rail shows its advantages and versatility. “Just consider, if we used double stacked trench shields, we would still need to cut outside the box. This slide rail systems allows us to keep the trench as narrow as possible — not even eight-feet wide — and that means less expensive backfill and more profit for us,” Wentland concluded.
Bacco is using a CAT 385 Excavator on the front end of the trench to excavate and install the slide rail components. They are using a CAT 345 Excavator on the back end to backfill and remove the system, plus a CAT 966 Front Loader.
Bacco Construction Company’s founder, Medio Bacco, was awarded the company’s first contract in 1915. On April 9, 1930, Bacco Construction Company was incorporated and has been prequalified with the Michigan Department of Transportation (MDOT) for over 70 years. Today, they handle a wide array of jobs including DOT projects and private-market work. Bacco is a member of the Michigan Infrastructure and Transportation Association (MITA), as well as other state and national construction and road builder organizations.
FOR MORE INFORMATION:
Efficiency Productions, Inc., (800) 552-8800, www.epi-shields.com
Caterpillar, (309) 675-1000, catrequests@cat.com
Comments