June 2010 Vol. 65 No. 6
Features
Underground Electric Transmission Installations Gaining Traction
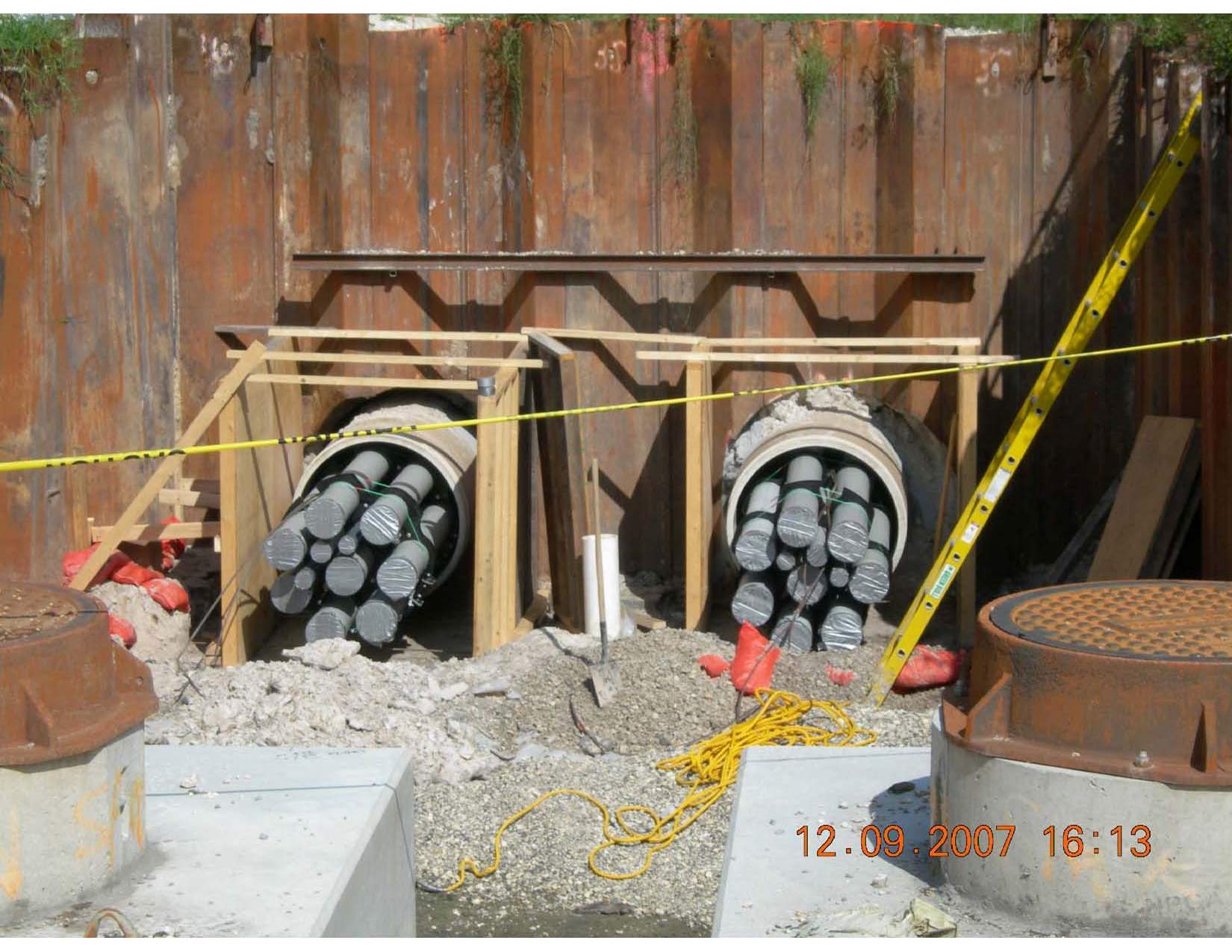
Electrical cable for power distribution systems has been placed underground for decades. In fact, it would be unusual today to even consider installing aerial power or communications cable in a new residential development, office park, government or institutional campus.
However, most power transmission lines remain overhead, suspended from steel towers. That’s because high-voltage power lines generate heat; being in open air allows that heat to dissipate. Being confined in underground spaces is not a good environment for high-voltage power cable. In addition, underground construction costs can be much greater than constructing aerial transmission lines.
Even so, there are areas, primarily in urban centers, where short segments of power transmission networks must be put underground. Today, advances in technology make it more feasible to bury high-voltage power cable.
A primary reason is the development of cable using plastic for insulation which has higher thermal tolerances than paper, oil-impregnated paper and fluid-filled pipes for insulating electric cable. With cable that can effectively and dependably carry high voltages underground, a narrowing gap between underground costs compared to overhead construction, and a growing list of successful underground transmission installations, utility providers, project planners, engineers, developers and communities are more open to considering underground segments of transmission projects.
Many factors
Ultimately, many factors influence consideration of installing transmission lines underground, says Brian Dorwart, P.E. PG, Brierley Associates, Bedford, NH.
“The reliability of underground infrastructure, along with regulatory issues and public demand, are factors,” Dorwart explains. “Cost ultimately may be the deciding factor, so it is important to note that the gap between underground and aerial construction costs has narrowed. The common rule of thumb once was that underground was 20 times more expensive than aerial. Today the difference generally used is that underground costs 10 times more.”
Aside from cost, it is generally accepted that underground cable is more secure than overhead cable.
“Acts of nature can cause outages, and these days the possibility of a terrorist strike can cause grid failure,” says Dorwart. “Aerial lines are exposed to hurricanes, ice and snow, wind and other natural disasters and overhead cables can be easily accessed for sabotage. Underground infrastructure is far less vulnerable to such risks and, thus, may be considered more reliable. For infrastructure serving military bases and other institutions of national importance, underground lines are more secure.”
There also are instances in which going underground simply is perceived as the “right” thing to do, Dorwart adds. Regulators are providing feedback from the public to power companies regarding overhead issues such as electromagnetic impact as a cause of cancer and improved aesthetics of landscapes without overhead cables.
Regardless of why a segment of transmission cable is being installed underground, a primary reason that option is available is development and evolution of high-voltage power cable using plastic for insulation.
Polyethylene plastic was first used to insulate power cables up to 5 kV in 1942, says Sara Susach, international account manager, energy division Southwire Company, Atlanta, a U.S. company that manufactures XLPE cable.
“By 1955, PE was used in cable up to 35 kV,” Susach continued. “In the 1950s, GE successfully crosslinked PE which helped its use as cable insulation gain widespread acceptance. In the 1980s, European and Japanese companies made great strides in development of XLPE with installations of 230 kV and even short 275 and 500 kV installations in Japan. Utilities liked XLPE cable for its absence of dielectric fluid and the inherent simplicity of the extruded cable systems, and the 1990s saw increasing numbers of 138 and 230 kV installations.
“Today XLPE cable is the dominating cable for HV and EHV underground power cable.”
Susach says to date, more than 4 million feet of Southwire HV XLPE cable has been installed in underground transmission systems in the U.S., and several other cable manufacturers also provide XLPE cable for U.S. projects.
Steady progress
Underground cable typically is installed in duct banks with splices made inside manholes. Terminations are made at substations or riser poles. There are single-point, cross-bonded and multi-point bonding options.
Black & Veatch, Overland Park, KS, a global engineering, consulting, construction and construction management company, has played a leading role in constructing power infrastructure containing underground transmission lines.
“The underground cable industry has seen the amount of high-voltage underground transmission lines increase as cable technology has advanced and reliability improved,” says John Rector, Black & Veatch associate vice president and project manager. “In the late 1980s, we were installing 115 kV underground transmission lines. In the early ’90s, Black & Veatch installed the first commercial 230 kV underground transmission project in Orlando, FL. In the years that followed as the number of underground installations grew and the reliability of these systems became evident, more power companies and planners became comfortable with the idea of placing 230 kV transmission lines underground.”
More 230 kV cable was installed, then came a short segment of 345 kV cable.
Additional short 345 kV projects followed and then came the 26-mile Middletown-Norwalk Project in Connecticut, a landmark projects demonstrating the viability of ever advancing high-voltage technology.
“Every time we increase the voltage level of these cable systems, we prove the reliability of this technology,” Rector says. “Europe and Asia for some time have been installing 400 kV and 500 kV systems. The U.S. utilities are a relatively conservative group which, I think, is a good thing. High-voltage cable technology is moving rapidly toward 500 kV in this country. Very soon we will see 500 kV underground transmission lines in the United States, probably in California or on the east coast.”
The need for added capacity in congested areas where overhead lines either are not permitted or are difficult to permit will spur more growth in underground transmission, Rector believes. And a strong indicator that underground transmission will continue to grow, he says, is that a second plant for manufacturing high-voltage dielectric cable opened in the U.S. late last year, making two such facilities to serve North America.
High-voltage underground construction is not for every utility contractor. The skill sets for installing underground transmission is quite specialized and demanding. The higher the voltage, the larger diameter of the cable, complicating logistics of transporting and handling of cable supplies. High voltages are unforgiving and there is little margin for error during installation.
Quanta Services has several companies with core competency in underground transmission engineering and construction, says John Wilson, president of the electric power division of Quanta Services, Houston. Quanta companies currently have several projects containing underground transmission lines under construction. One of those is EHV Power, Gormley, Ontario, Canada.
Trend to underground
EHV President Steve Burks, says the trend to place more power transmission lines underground is generally positive.
“There are many drivers,” Burks believes, “including improved cost factors and less challenging technology that can accommodate higher voltages and is easier to install. The current economy has imposed a temporary lull, but the envelope for opportunity is better than in the past for placing transmission lines underground. Most continue to be short, averaging about two miles with the longest about 20 miles.”
Obviously there are significant differences between constructing aerial and underground transmission infrastructure. Because it requires insulation, underground cable has much larger diameter than uninsulated aerial cable and is, therefore, more difficult to transport and handle.
“Size of dielectric cable is a function of load,” says Burks. “A 345 kV cable will be five to six inches in diameter. A reel containing one conductor typically will be 12 to 14 feet in diameter and weigh 40 tons. That’s one reel of cable containing one conductor, and a project will require three of them. Splices will be made every 1,200 to 1,800 feet, and they must be perfect. Obviously a lot of space is needed to handle and allow room for splices.”
Duct banks in which cable is placed must be insulated to dissipate heat.
“The duct banks must be of a thermal grade concrete to provide a thermal envelope to accommodate the load of the cable that will be placed in it,” says Burks. “Heat is the enemy of underground cable, and if the operating temperature becomes too hot, the insulation will break down.”
Placement of duct banks and construction of manholes and vaults requires extensive excavation in areas where traffic and normal activities would be disrupted.
“Excavation for ductwork will be at least three-to-four feet wide and four-feet deep,” Burks explains. “If the cable route must go deeper, the system has to be designed for the deepest part; the conductor must be designed to accommodate the deepest portion of the route, because heat dissipation lessens with depth.”
Often cable routes are in easement already containing other utilities which must somehow be avoided or relocated.
Manholes or vaults must be constructed along the cable route. Each section of cable is pulled into and out of vaults where connections are made and future maintenance will be performed.
“Civil construction costs — excavation, duct banks, restoration — often are 50 percent or more of project costs,” says Burks. “And from a contractor’s perspective, most of the risk of a project is on the civil side.”
Burks adds that because underground transmission work is highly specialized, only a few contractors are qualified for the work.
“However,” he adds, “the landscape of contractors is changing. Cable improvements are reducing the degree of specialization required.”
In conclusion, Dorwart believes the public and government will be demanding more underground transmission to create a backbone grid that will be hardened to acts of God and terrorists threats; to provide reliable power delivery to lifeline service nodes; and to improve quality of life by removing unsightly overhead transmission systems, especially for new “green” energy production facilities.
“Based on this public pressure,” he concludes, “I believe that the outlook for underground power transmission construction will be strong in urban areas and in areas of alternative energy production for connection to the grid.”
Brian Dorwart has extensive experience designing trenchless projects that include underground transmission segments, and he currently is designing shore landings for cable runs crossing the Hudson River between New Jersey and New York, and directional drilling river crossings for power transmission installations in Jacksonville, Fla., and Malden, Mass.
Black & Veatch is a leading global engineering, consulting and construction company specializing in infrastructure development in energy, water, telecommunications, management consulting, federal and environmental Black & Veatch has completed several landmark underground power transmission projects.
Quanta Services provides a full range of services for the electric power, natural gas, pipeline, telecommunications and cable television industries, including designing, installing, repairing and maintaining network infrastructure nationwide. Quanta company EHV Power specializes in underground power transmission.
Southwire is a leading manufacturer of wire and cable used for transmission and distribution of electricity for commercial, residential, industrial, institutional and OEM applications.
FOR MORE INFORMATION:
Brierley Associates, (603) 206-5775, www.brierleyassociates.com
Quanta Services Inc., (713) 629-7600, www.quantaservices.com
EHV Power, (905)-888-7266, www.ehvpower.com
Southwire, (770) 832-4242, www.southwire.com
Black & Veach, (913) 458-2000, www.bv.com
Comments