June 2010 Vol. 65 No. 6
Features
Rigonomics: With Low Rates, HDD Rig Selection Is Critical
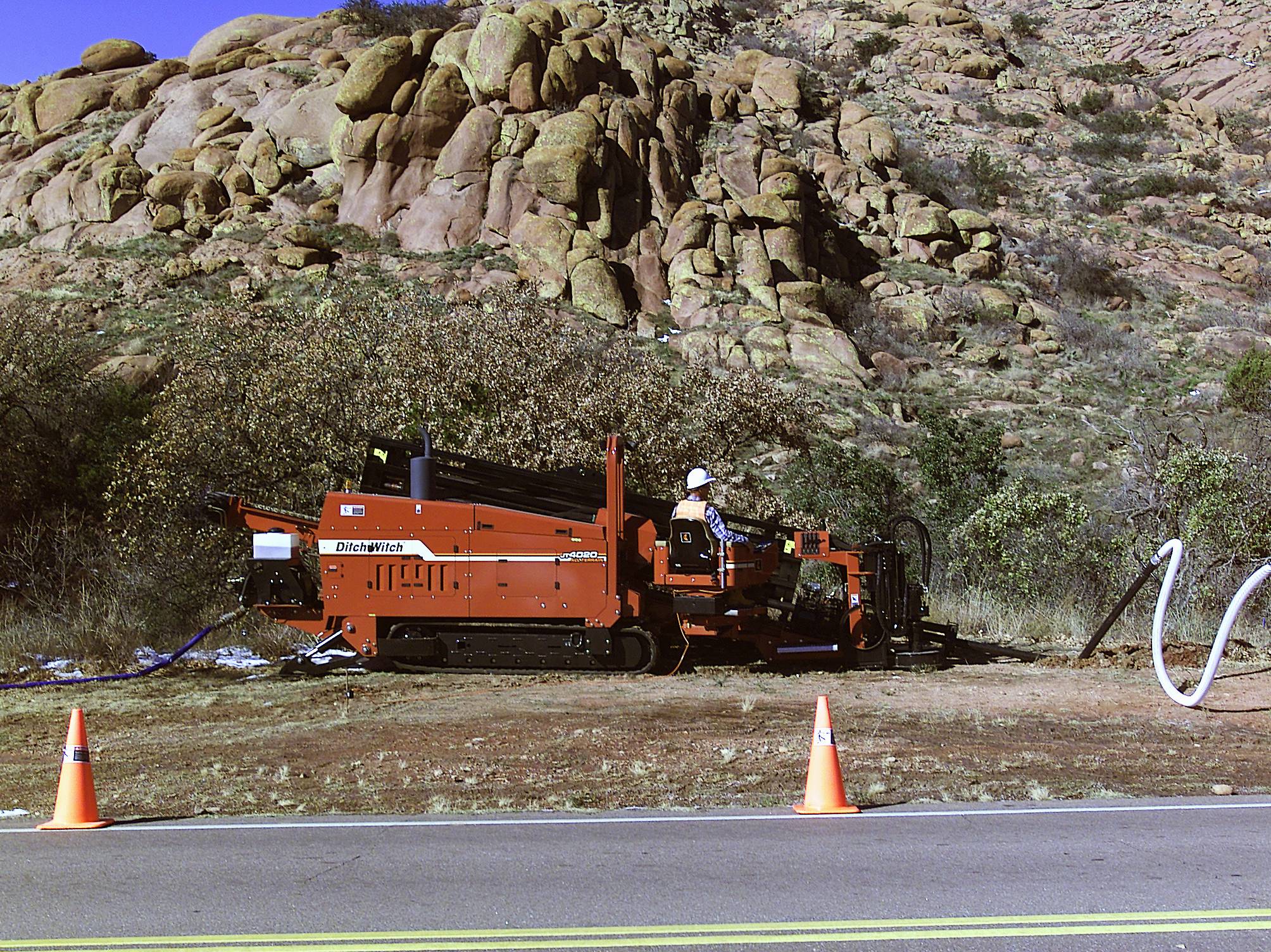
Rigonomics: [n.] efficiently and effectively conducting HDD operations to ensure maximum profits
Plan the work, work the plan — good advice no matter what the job. On construction projects, failure to properly follow that simple advice can result in lost and wasted time, costly errors and accidents.
Several months ago, Jim Agnew and Danny Crumpton of Houston-based Inrock, were discussing the range of problems they have encountered in serving their clients on horizontal directional drilling projects. Many were the result of lack of planning or deviating from the project plan after construction was under way.
The Inrock group thought the topic could be a worthwhile session at the annual UCT Show (Underground Construction Technology International Conference & Exposition). With input and encouragement from customers, Crumpton and Agnew began development of a program that ultimately became the “Rigonomics” session at the 2010 UCT show in Tampa.
“We recognized the key to making the program interesting and beneficial was interaction among those attending,” said Crumpton. “We decided not to use a PowerPoint presentation, but to develop content that would stimulate interest and allow maximum interaction for sharing the knowledge and experience of all participants.”
The concept worked. “We went three hours with three breaks,” Crumpton said. “We felt a high level of interest was sustained throughout and received very favorable comments from those attending.”
In discussing on-the-job problems, it was clear many problems were the result of shortcuts to save time which ended up causing delays. Delays equal lost time which results in lost revenue.
As directional drilling has matured and drill operators have gained experience, it can be tempting to skip or alter basic steps.
No shortcuts
“The value of knowledge and experience is diminished when personnel convince themselves they know enough to take shortcuts,” Crumpton observed.
“An example is a failure to maintain redundancy in a basic tool such as a crossover sub,” he said. “If a crossover sub is damaged and another one is not available, the rig is down until another sub can be brought to the job site. How costly was a $395 or even a $1,200 sub compared to a day of down time? For a rig costing $5,000 per day, that is not good economics.”
Rigonomics topics included selecting the right size drill rig for each job, drilling the pilot hole, backreaming, proper drilling fluid properties, operations of mud motors, transportation of equipment, downtime and dealing with unforeseen problems.
To share Rigomonics information with those unable to attend the UCT sessions, Underground Construction magazine will publish a series of reports on key topics covering HDD operations. The first is about selecting the right drill for the job.
“Once a drilling company is awarded a project, most of the time there will be several weeks to plan how to best execute it,” said Crumpton. “At this stage, you’re ahead of the game — bid work should have provided information needed to make the installation.”
Selecting the right drill rig is an essential early step. Considering project specifications, such as pilot hole size, bore length, type of soil formation, size and type of product line to be pulled back and numerous other factors affect the decision of selecting the right machine for the job.
Important questions
Among questions that should be answered when selecting equipment for a job:
• Does the drill unit have sufficient push/pull and torque capability?
• Is the capacity of the mud pump enough to clean the hole and offer effective hydraulic horsepower?
• Is the drill pipe able to withstand the torsional and tensile forces that might occur on the job?
“The rig’s pumps must be able to handle the volume needed for the final reaming size,” said Crumpton. “If cuttings can’t be removed from the hole, there are going to be problems. Pressure is not the issue, volume is what is important. If necessary volume can only be achieved by running the pumps wide open, larger-capacity pumps should be used. Mud pumps cannot pump to engineering specifications because they are designed for actual efficiency ratings. For example: duplex pumps are rated at 85 percent efficiency. Triplex pumps have 90- to 95-percent efficiency ratings. If the pumps must be operated at maximum RPM, the efficiency is reduced. Either triplex or duplex pumps are very good to use in the HDD industry.”
Postponing starting a job because the right-size rig is not available is never an attractive option. A solution often used is to drill the pilot hole with a drill unit that may be too small to complete the installation.
“A smaller model can be transported to the job site, moved into position, rigged up and start the pilot hole faster and at less cost than a bigger machine,” Crumpton said. “Smaller rigs use less fluid, have smaller engines that burn less fuel and require fewer personnel on the job site.”
A common practice, said Crumpton, is to “leap frog” two machines, completing the pilot hole with the small machine, moving it off to the next bore down the line, and bringing a larger unit for the reaming and pullback.
“The leap-frog method can save time and money if done correctly for particular formation types.” Crumpton explained. “It is practical in many soft rock and soil formations. Other factors to consider in the leap-frog process are the length of the bore, the rock type and the hardness.”
A subcontractor is another possible solution. “If the job consists of only one bore,” Crumpton said, “using only one rig that can complete the bore is the best method. On most rock bores, a large rig has to do the complete bore.”
FOR MORE INFORMATION:
InRock, (713) 690-5600, www.inrock.com
Editor’s Note: In the September issue of Underground Construction, Rigonomics will cover drilling the pilot hole.
Comments