July 2010 Vol. 65 No. 7
Features
Sustainable, Long-Term Solution For MIC/SRB Corrosion In Hydrocarbon, Other Pipeline Systems
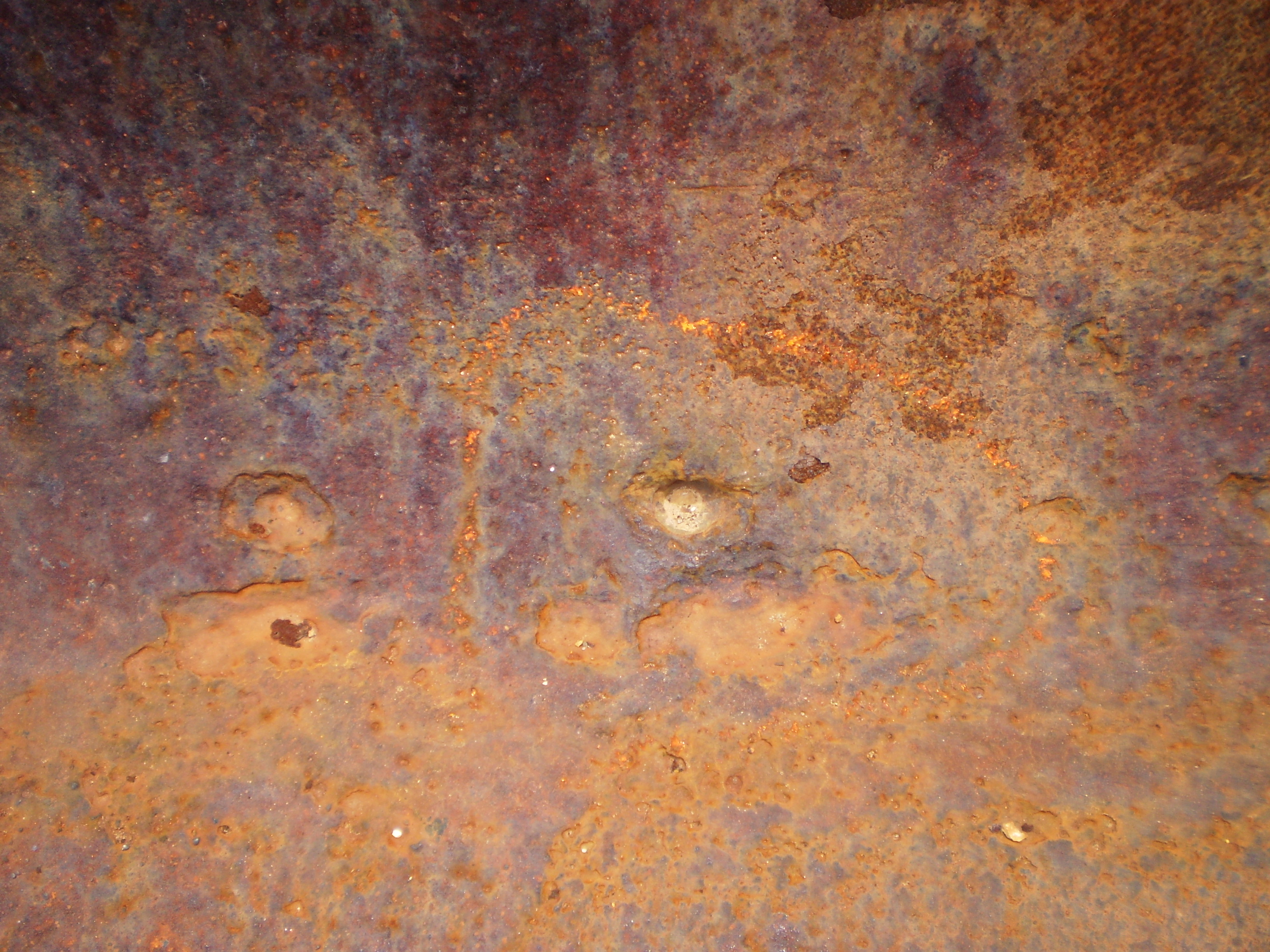
In the spring of 2008, a reliability engineer at a major oil refinery contacted Inspar Robotic Technologies Inc., regarding concerns about the continual microbial corrosion problems they were encountering. The facility was experiencing multiple perforations in a progressive sequence from the effluent source in their hydrocarbon pipelines.
As a matter of internal protocol, the plant’s operations was continually installing exterior clamps to arrest leakage from perforations, some as large as 3/4 inch, due to microbial activity. Because governing authorities consider exterior clamps a temporary solution, the client had attempted a permanent solution by replacing sections of the system with stainless steel pipe. The client almost immediately discovered that this changeover did not solve the corrosion problem and in effect, it actually increased the veracity and propagation of the microbial agent.
An Inspar crew conducting their rehabilitation work on the industrial pipeline.
The pipeline system consisted of six-inch carbon steel pipe with multiple convolutions, ells and earthen penetrations through tank farm containment berms. The effluent composition contained hydrocarbons, acids and miscellaneous organic compounds. The pipeline’s design pressure was 180 psi, with an operating pressure of 120 psi linear to production requirements. Effluent design temperature was approximately 350 degrees F, and the soil load was approximately 12 feet to invert at all berm penetrations.
The problem
Inspection of the sump line revealed significant microbiological induced corrosion (MIC) and/or sulfate reducing bacteria (SRB), resulting in profound cavities, craters and large perforations in the pipeline. Determining specific full circumferential wall thickness measurements along the axis of the subject pipeline required long range ultrasonic testing (LRUT). Inspar performed this testing and subsequently advocated a ‘worst case’ approach due to the sporadic nature of the corrosion. This protocol determined the diameter, depth and quantity of detailed deteriorations in a specific segment of the pipeline.
MICs are an aerobic species (requiring oxygen for survival) such as slime-forming bacteria, also referred to as a biofilm, which colonize the layer. Once the biofilm has reached a certain thickness, SRBs colonize beneath the biofilm and locate themselves at the interface between the biofilm and the metal substrate. SRBs are anaerobic (thriving in oxygen-deficient environments) and therefore locate themselves at the interface, where they are protected from the aerated water of the biofilm. The MICs use the available oxygen within the biofilm; the base of the biofilm is anaerobic.
The Inspar process.
It is essential to note that the survival of both types of bacteria requires the presence of water. They therefore cannot be active in non-aqueous media or environments.
Due to the difficulty of removing SRBs once they have become established, simply injecting biocides into the slurry is ineffective because the bacteria is located beneath the tubercles. To expose the bacteria, the scale and tubercles must be removed, which Inspar achieved by using helically-wound wire pigs, followed by rotational water jetting.
As a pre-treat to the prepared carbon steel, Inspar used a proprietary chemical compound developed by Planet Resource Recovery Inc. This compound can render the cavernous pits of metal impervious to oxygen and biological penetration within surface bonding. It forms ionic bonds with metal at the nano scale level and fills the micro crevices on metal surfaces, rendering a smoother coefficient that is impervious to bacterial and oxygen threats. Inspar utilizes this method because it is not simply an ‘additive’ to attempt to kill the microbial agents, but is actually a catalyst for changing the molecular structure of the metal.
The basic issue with most of today’s simple ‘additive’ treatments has been the lack of permanency. One of the primary attributes of the Inspar polyurea-based lining systems is the extreme durability and performance expectations of their lining products. It is difficult to justify applying a product or system that will last over half a lifetime and then improving the system with anti-microbial characteristics that might last only a year at best. Most ‘anti’ additives contain heavy metals that impair microbe viability. These additives tend to migrate to the surface of the coatings and are then washed or abraded away after a relatively short period of use, therefore requiring a continuous replenishment program.
New type of additives
In the last several years, specific additives containing more permanent ammonium salts that become permanently polymerized within polymer-based systems were developed by Inspar formulators. This polymerization process is greatly enhanced within the Inspar polyurea systems, resulting in a matrix of ‘lance-like’ salt structures throughout the entire thickness of the high-build linings. These nano-sized structures pierce the cellular walls of microbes, resulting in the complete and effective death of the bio-organisms.
It is important to note that these salt structures are bio-compatible with sensitive applications such as drinking water, food contact and other health uses. Additionally, no heavy metals are used, and no arsenic is present in Inspar’s BioLine ‘anti-microbial’ formulations.
Lining Application
Inspar reviewed all design factors and data in calculating the required thickness of the liner. The analysis was first based on determining the safety factor pursuant to the wall loss of the schedule 40 carbon steel pipe in conjunction with the existing pressures in the system. The subsequent calculation also required the liner to span 3/4-inch perforations with a safety factor of three. The result, when combined with the linear mathematical expression formulated from prior burst testing, was the determination of a liner thickness of approximately 4 mm.
In this instance, the effluent bypass utilized an adjacent ballast pipeline. The pipeline was accessed from the existing flange breaks provided by the client. The Inspar lining systems require only one access to the pipe interior, a minimal lay-down area, and no impact on the surrounding area. Additionally, with umbilical-controlled robotics, the requirement for close proximity to the pipe access is unnecessary.
The lining product Inspar utilized for this project was StructrLine SS, a highly chemical- resistant, heat-resistant, semi-structural polyurea with Inspar’s BioLine additive. The use of StructrLine SS resulted in a tenacious bond to the host pipe and a liner that was cohesive with the substrate.
Eliminating annular space
Because of the liner’s full cohesiveness with the existing profiles in the pipe, there was no resulting annular space, as with other remediation methods the client had investigated. More importantly, the absence of this annulus prohibited the aqueous environment that the bacteria require for survival.
The completion of the project was both on schedule and effective. The client’s initial solicitation for Inspar services followed 19 progressive perforations over a nine-month period. Since the installation of the Inspar lining, there have been zero reported pipeline incidents in this system. Inspar has since been issued a global master service agreement, completed the second phase of this project with the same success, and is expected to complete the third phase in 2011.
These continual innovations in apparatuses, methods, and lining products allow Inspar to offer state of the art, permanent anti-microbial protection. With the ability to pre-treat and change the metals’ molecular structure and to utilize BioLine in all Inspar’s polyurea formulations, MICs and SRBs no longer need to be a continual and costly threat to pipeline environments.
ABOUT THE AUTHOR:
Kent Weisenberg is the founder, president and CEO of Inspar Robotic Technologies.
FOR MORE INFORMATION:
Inspar, (941) 483 3000, www.inspar.com
Comments