January 2010 Vol. 65 No. 1
Web Exclusive
Day 2: New Rehabilitation Technologies
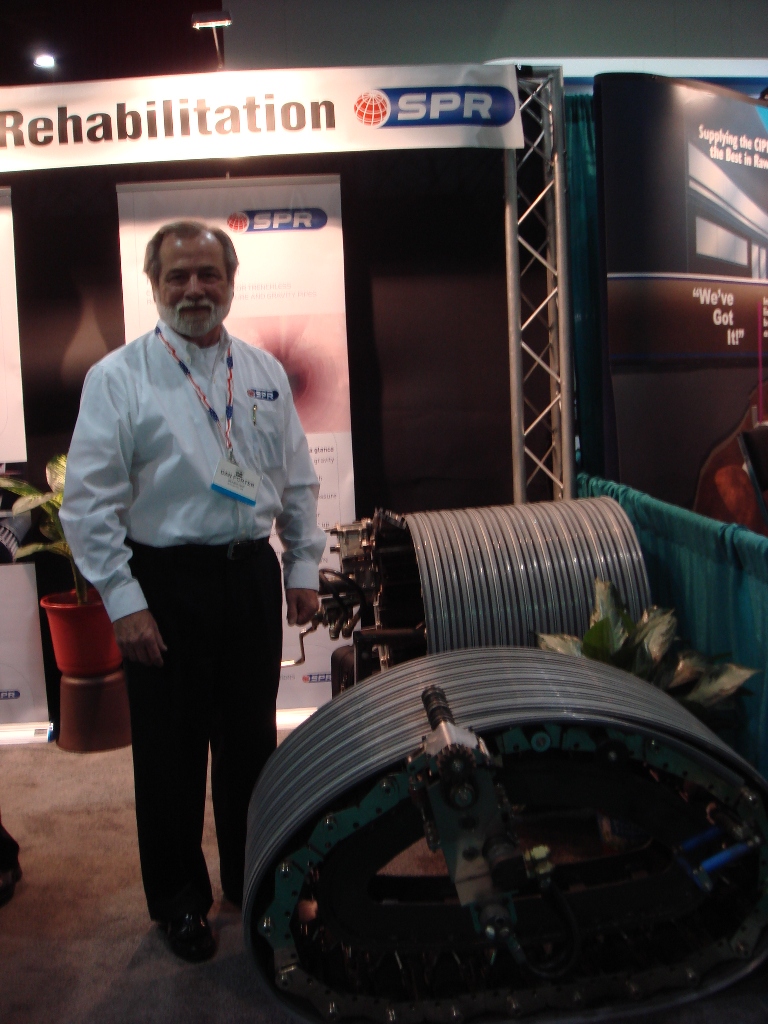
Several of the exhibitors at UCT this year were new to the show and, in some cases, the industry itself. But new acts in rehabilitation were easy to come by on Day 2.
Kanaflex, exhibiting to promote its metal reinforced pipe rehab and storm drain solutions, was garnering plenty of traffic to its impressive installation anchoring a corner of the exhibition hall. The booth features a 48-inch diameter demo pipe and a hypnotic display of flexible pipe rotating through the mechanism at the front of the booth. The company is international in reach and based in Japan, but has only recently entered the domestic market with a labor-saving product line advertised as a competitor to concrete with watertight joints and lighter weight.
LightStream is another newcomer to the sewer/water market, with a U.S.-made light train for UV pipe curing and a corresponding UV liner reinforced with fiberglass. The liner is certified for 1.7 million PSI and according to the company studies have shown the technology to maintain strength equivalent to 1.16 million PSI for at least 50 years. The built-in video connection in the light train permits an operator to examine the liner for flaws before curing.
The Japanese company Sekisui SPR has been working a small number of rehabilitation projects in the United States since 2005, more or less through the machinations of the city of Los Angeles. According to regional sales manager Dan Porter, Los Angeles learned about the technology and told Tokyo-based Sekisui SPR that Tokyo and Los Angeles had several things in common: “We both have a lot of earthquakes, we both have hand-dug sewers with lots of curves and we both hate to stop traffic.”
The SPR technology is particularly effective for sewer and water systems which are oddly shaped, such as Los Angeles’ arch-shaped tunnels. Horseshoes, squares and arches were popular designs for hand-dug sewers built in the 1920s and 30s—graceful architecture that leaves cities with aging systems facing complex problems as they come due for rehabilitation. The rehabilitation process involves a caterpillar track machine that can enter a sewer or water system through a manhole, spool winding material automatically from a reel on a truck on the street above, and create a new pipe by spiraling together a combination of plastic, steel and grout. As another benefit to the built-up cities that hand-dug water systems, it’s fully trenchless and maintains a small footprint.
Not all new innovations were coming in the water side of the business. Arkema’s Rilsan offers the first plastic pipe approved by the Department of Transportation, and the company is aiming it at steel natural gas mains in need of rehabilitation. After 14 years of development, the pipe can withstand 200 PSI at diameters up to four inches, needs no corrosion-resistant coatings, resists both temperature and abrasion, and offers a 25% savings over steel insulation. After approval in December 2008, the pipe has just been deployed on a 6000-foot project in Texas, with a 56,000-foot project waiting in the wings and several large utilities interested.
The Cosmic TopHat CS100 Navigator Lateral Cutter, on the other hand, is so new that there is only one unit currently in the United States. Scheduled for a debut at the Rehab Zone this afternoon, the little lateral cutter instead went to Phoenix on New Year’s Eve for a rescue mission: a liner on a main line into a casino collapsed, requiring an emergency intervention that included four to six feet of liner cut out and three hours of operation for the navigator, which uses a 2HP electric motor and can fit into pipe as small as 3.5 inches in diameter. The untrained operator damaged the prototype, however, and although New Year’s Eve was saved the demonstration was called off.
Though not strictly rehab, ICS Blount’s Power Grit Utility Saw Chain is faring well at the exhibition, and seems to be attracting attention from contractors of all stripes. The diamond-coated saw chain is designed to fit on a regular chain saw, either hydraulic or gas-powered, and can cut through ductile iron, cast iron, PVC, HDPE and, with some modifications, concrete pipe. The saw increases operator safety and vastly increases the ease and speed of the operation, since it needs only to get to shovel depth before it can cut pipe.
With more new technology waiting to be uncovered tomorrow, the rehabilitation of America’s infrastructure is definitely looking up at UCT.
Comments