January 2010 Vol. 65 No. 1
Features
Mega-Size Sewer Lift Station Construction Requires Unique Shoring System
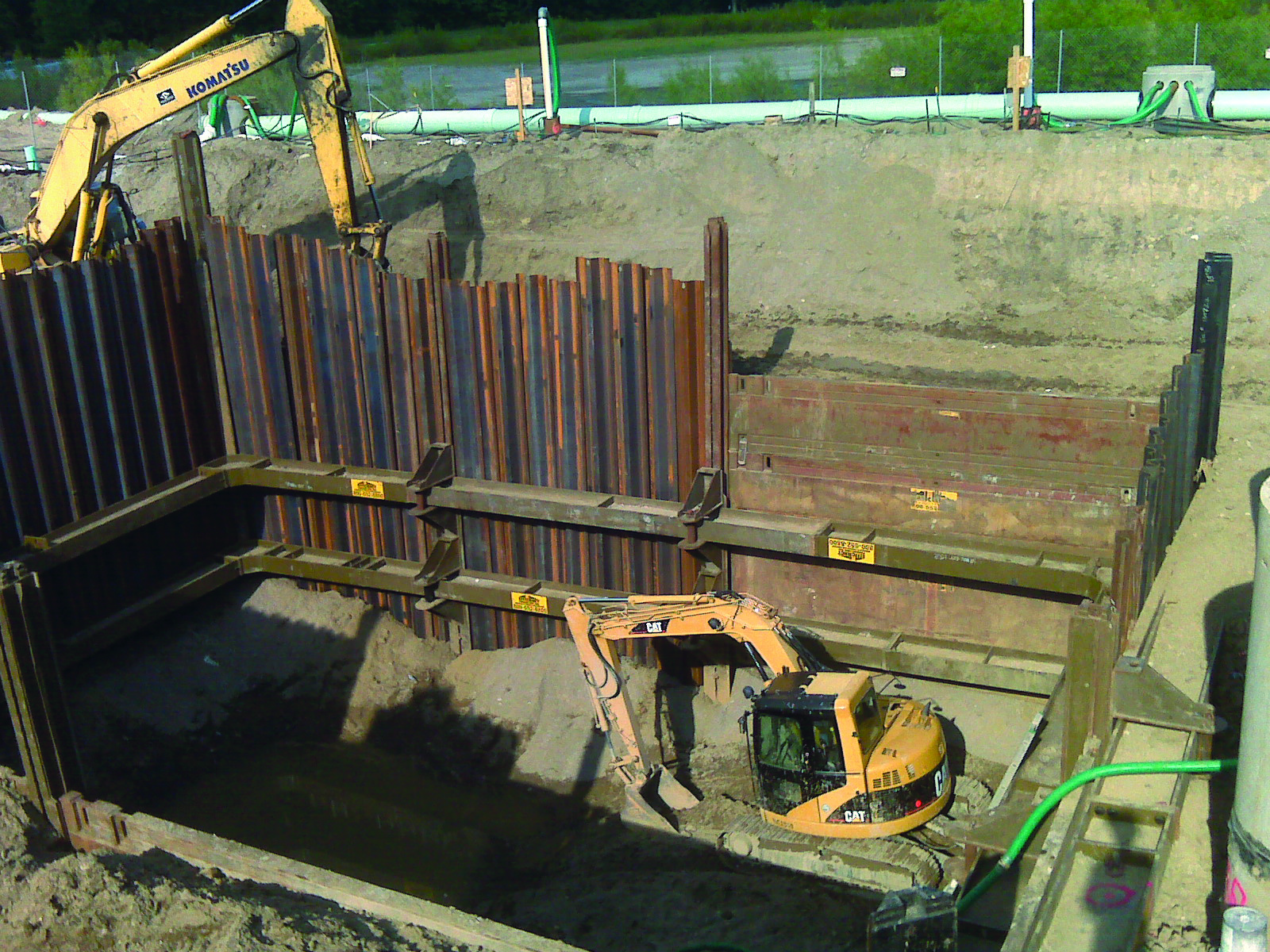
Like many other communities across the country, Fishers, IN, a suburb of Indianapolis, is in the process of upgrading their aging sewer infrastructure to keep pace with growth and new development. This means replacing miles of sewer lines and manholes, and installing new lift stations. One recent lift station installation project let by the Hamilton Southeastern Utilities Company was unusual due to the sheer enormity and shape of the structure: a poured in place behemoth measuring 52 by 29 feet, with height ranging from 14 to 40-feet.
Weihe Construction of Noblesville, IN, won the job as low bidder by working closely with local trench shielding and shoring distributor, Excavation Safety International (ESI), to design a shoring system that used Efficiency Production’s Universal slide rail system in the exclusive ClearSpan configuration.
Because one side of the structure needed to be poured at a depth so much deeper than the other, the shoring challenges were immense. Working with engineers at Efficiency Production to custom design a shoring system, Weihe and ESI were able to come up with a modified ClearSpan slide rail system measuring 41 by 56-feet square, 20-feet deep, but with the addition of sheeting on the deep-end to reach the 40 foot grade.
“We’ve always said that in theory, ClearSpan can have unlimited size, and this excavation proves that a 50 foot wide pit is not just theory,” said Efficiency Production Vice President of Engineering, Mike West. “That’s possible because we are not encumbered by cross members at any time.”
Dig and push
Efficiency’s Universal slide rail is a component shoring system comprised of steel panels (similar to trench shield sidewalls) and vertical steel posts. The versatile system can be used in a variety of configurations in addition to ClearSpan, such as small four sided pits, or in a linear multi bay configuration to install lengths of pipe over 40 feet.
Slide rail is installed simultaneously as the trench or pit is excavated by sliding the panels into integrated rails on the posts – either double or triple rails depending on needed depth – then pushing the panels and posts incrementally down to grade as the pit is dug, a process commonly referred to as a “dig and push” system.
The size of this slide rail system was most ambitious for a contractor who was using it for the first time, but they had no problems. “At first, there was some trial and error in finding the best technique to install the slide rail parts in the hard clay, but so far it’s been wonderful,” said Mike Matlock, Weihe’s project superintendent. “We got the system in the ground in good time. The waler beams have been critical, in that they move up and down, which makes it easy to extract when we start to pull the sheet out as we backfill on that deep end.”
To assist Weihe with the initial slide rail installation, Efficiency Production sent on site their Slide Rail Systems Manager Greg Ross. “It’s always interesting to see the reaction of contractors the first time they use slide rail,” explained Ross. “The first day, they usually are intrigued on how and if it’s going to work; the second day, there is usually a bit of consternation as they have to overcome unexpected ground conditions as they are trying to put the system in one piece at a time; but by the third day, they really get the hang of it, and they really start to figure out that this is a great system.”
Efficiency Production’s slide rail is unique in that it is installed and removed incrementally, which allows the trench to be properly shored throughout the entire installation or removal process, always protecting workers from a trench wall collapse.
Before actually digging the pit, the excavation was benched down the first five feet. A CAT 311 mini excavator was then set in the hole to complete the excavating. The lift station was formed with two-foot thick walls, in two chambers.
Additionally, Weihe installed two 20-foot tall precast manholes; one that had an eight-foot outside diameter, and the other a five-foot outside diameter. The lift station was completely formed up in only three months. Because the excavation was open for that duration, Weihe utilized the system’s integrated slide rail barrier posts and adjustable length hand rails which provided fall protection.
Weihe Construction Inc. is a general site work and excavation contractor specializing in residential and commercial developments, including earthwork, sanitary sewer, storm sewer and waterlines.
FOR MORE INFO:
Weihe Construction: (317) 776-2966, http://weiheconstruction.com
Efficiency Productions, Inc., (800) 552-8800, www.epi-shields.com
Excavation Safety International, (317) 841-0185, www.excavationsafetyint.com
Comments