January 2010 Vol. 65 No. 1
Features
Job Complications Lead To AXIS System Solution
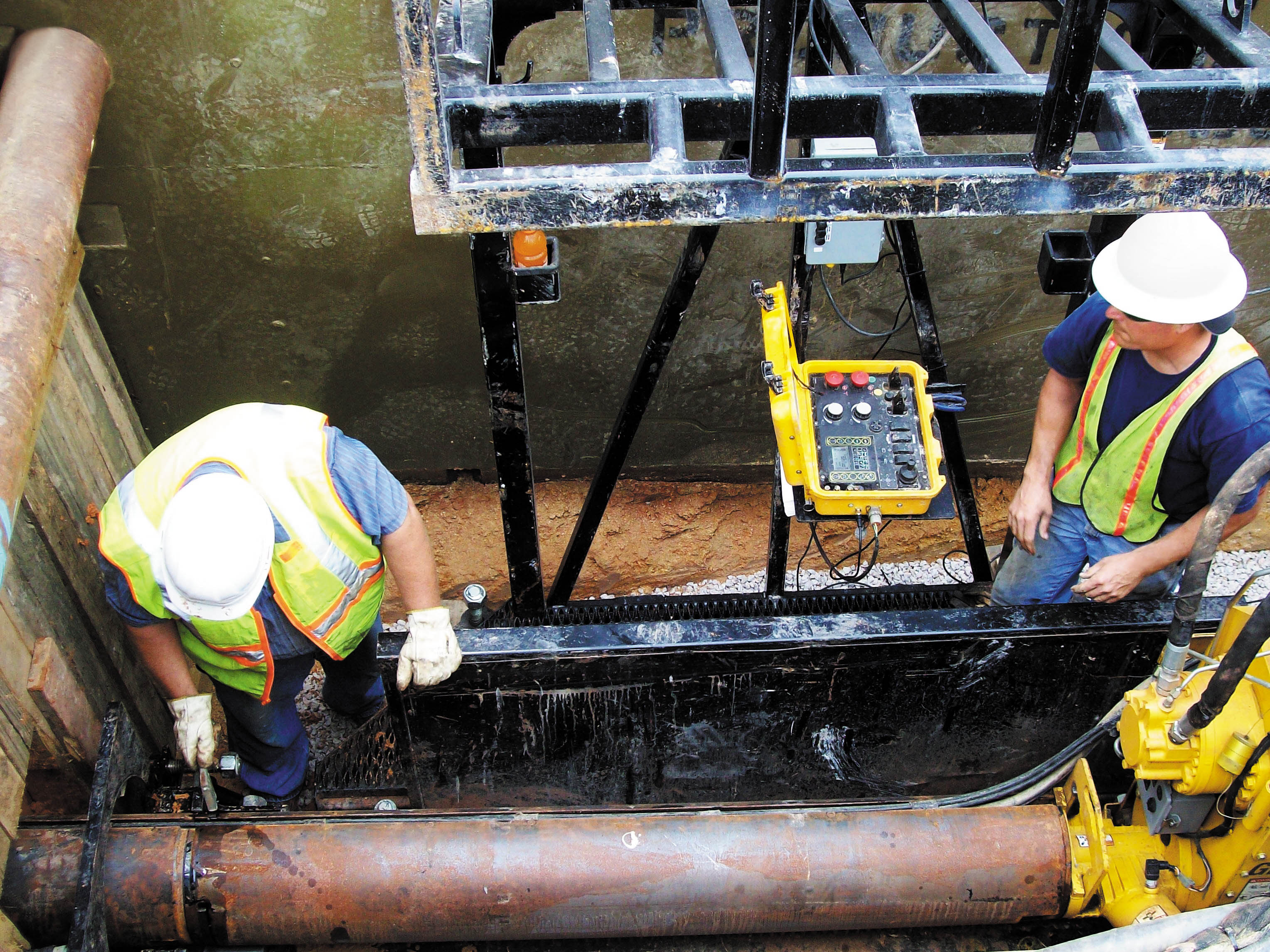
When Vermeer introduced the AXIS guided boring system earlier this year, it was presented as a new guided boring system capable of achieving pinpoint, on grade accuracy that eliminates many of the difficult procedures required by other underground installation methods.
The pit launched trenchless installation method often is described as similar to pilot tube boring, but with significant differences that set it apart from that process and other methods of trenchless construction. The AXIS system can maintain grades of less than 0.5 percent with pipes with diameters less than 24 inches (see box summarizing AXIS features).
Basic components of the system include power pack, rack, drill head, boring rod and vacuum and vacuum power pack and tank.
“At the beginning of the development process for the AXIS system, Vermeer established an ‘A’ team of engineering technicians designated for testing the system,” said John Milligan, AXIS project manager. “As the product development process evolved, the team was expanded and has assumed responsibility for demonstrations with customers, machine start-ups and training.”
One of the first projects in the U.S. completed with an AXIS system was the installation of a 160 foot on-grade segment of ductile iron sanitary sewer pipe in Kannapolis, NC. Project owner is the city of Kannapolis.
“The project was necessary to relocate a portion of a sewer line that went through school property and had to be moved because of construction at the school,” said Stephen Bissinger, P.S., City of Kannapolis Public Works Department. “Although the sewer line is the property of the city’s sewer infrastructure, the cost of the project was born by the school system.”
Primary Contractor was Hendrick Construction, Charlotte, NC. Cherokee Construction, Indian Trail, NC, was the subcontractor for the street and intersection bore.
Abundant challenges
“This segment of the project called for 160 feet of 8 inch ductile iron pipe to be placed seven feet deep under a road and extending it into the major intersection across the street from a school,” said Eric Mann, Cherokee Construction operations manager.
The work originally was specified as open cut; however, the city and department of transportation would not allow the intersection to be closed until a school holiday several months away.
“Various site conditions, including not being able to close the street, and the requirements of other trenchless procedures made it impossible to use other construction methods,” said Mann. “We considered microtunneling but the small exit manhole was too small to accommodate microtunneling pilot tubes.”
Mann began to investigate other trenchless options. Mann’s brother, Patrick Mann, chief operating officer of Magnum Tunneling in Houston, suggested the new Vermeer AXIS system should be evaluated and considered.
Eric Mann contacted Harry Eagle, general manager of Vermeer Mid Atlantic, for information about the system’s capabilities. Eagle contacted the Vermeer home office, and ultimately arrangements were made for an AXIS system and the A Team to come to Kannapolis and do the installation as a paid demonstration for Cherokee Construction.
After existing utilities were located and marked, Cherokee crew members closed one lane of traffic leading to the intersection, excavated a 10 by 12 foot launch pit, and cut a hole in the existing manhole that would serve as the exit pit.
The pipe laser then was set in the launch pit at depth and a 1.3 percent grade required by the project. Next, the leveling frame was set in place, the rack assembly lowered into the pit and positioned, and the drill head containing a camera was put in place. Images from the camera are viewed on a monitor at the operator’s console. The rack power unit contains the engine and hydraulic pumps and connects to the rack, powering thrust and pullback of the drill head and casing. AXIS casings are 6½- feet long.
During boring, the cutter bit at the front of the drill head rotates to cut through the soil. With the camera viewing the laser beam on the target, the operator can accurately monitor the target grade and make adjustments if the drill head moves off course.
Keeping the laser dot centered within the cross hairs indicates the drill head is on course with the target grade. Only the cutting bit and center drive shaft rotate as the drill head and casing travel through the bore; the outer section remains stationary as it is pushed through the hole opened by the cutting bit. As the drill head cuts through the soil, the cuttings are simultaneously removed by a high power vacuum system and diverted to a vacuum tank.
Additional sections of drill casing were coupled to the drill head until the head reached the exit pit.
Pipe installation
It took the AXIS system less than four hours to bore the 160 feet into the existing manhole. Once completed, the drill head and casing were pulled back into the entry pit and the head was uncoupled from the carriage assembly.
To install new pipe, the AXIS system typically uses one of two methods. For rigid pipes, after the drill head reaches the exit pit, sections of new pipe are substituted for drill casing, and the carriage assembly thrusts forward, jacking the pipe through the bore hole.
If job site conditions permit, it may be possible to pull pipe back through the bore hole. For this procedure, after the drill head reaches the exit pit, it is removed and replaced with a pulling head, which attaches to the product pipe, and it is pulled back through the bore hole. With the pullback method, it is possible to attach a reamer to the puller head to increase the diameter of the hole in order to install pipe that is larger than the pilot bore.
Because of site conditions in Kannapolis, Mann said a decision was made to push the new ductile iron pipe through the bole hole from the entry pit with an excavator using a nose cone and push cap to push the new pipe through one joint at a time. Grout was installed around the pipe through a tremmie line.
With new pipe in the ground, the launch pit was filled in and the street surface repaved. It took only two days from the time the launch pit was excavated until the project was completed.
The project was the first experience with the AXIS system method of installation for both Hendrick Construction and the city of Kannapolis.
“The method served the specific requirements of the job very well,” said the city’s Bissinger.
Vermeer’s Milligan said he believes that as more projects are completed and more people are exposed to the new technology, it will become an option on an increasing number of projects.
“The AXIS system provides several benefits that are not found in other trenchless installation methods,” Milligan emphasized. “Some methods can achieve accurate bores with less than a one to two percent grade, but they are time consuming. Other procedures can compete with open cut for speed of installation, but lack the ability to hold the tight grade tolerances mandated for gravity sewers. The AXIS system combines speed and accuracy into the same package, while adding the benefit of an environmentally friendly, non disruptive, trenchless installation.”
What Sets the AXIS System Apart?
Vermeer’s new AXIS guided boring system is designed to install a wide variety of pipe materials in 10 to 14 inch diameters from manhole to manhole in the 300 to 350 foot range. Depending on soil conditions, it may be possible to make longer runs or install larger diameter pipes.
Features include:
• The AXIS system can install many types of pipe, including fused HDPE and PVC, ductile iron, vitrified clay and steel pipe;
• The drill head can be retracted and changed in mid installation to adapt to changing soil conditions;
• A vacuum evacuates cuttings to keep job sites clean without the need to manually remove spoil from the boring shaft;
• The system can both push and pull in product pipe; and
• The system does not require walls of the launch pit to be structurally reinforced.
FOR MORE INFO:
Vermeer Corp., (888) 837-6337, www.vermeer.com
Comments