August 2010 Vol. 65 No. 8
Features
New Tool Helps Colorado Contractor Tackle Tough Ground Conditions
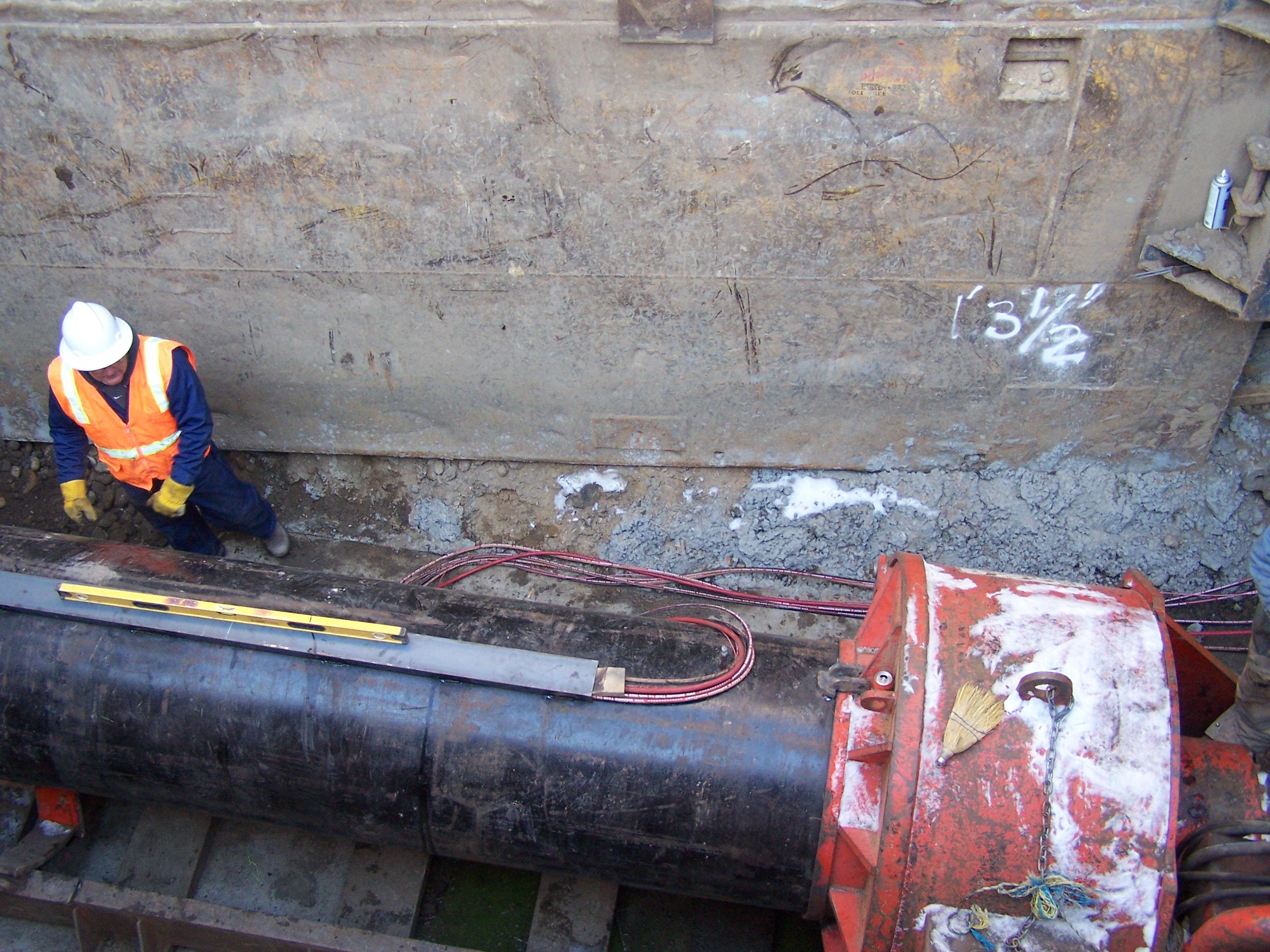
Brighton, CO, has a successful formula for growth. The community of 30,000 just outside of the Denver metropolitan area has added 750 new businesses since 1990 and is home to a wind turbine and nacelle manufacturing plant that will eventually employ 1,350 people. Part of the formula is a sound infrastructure that provides businesses with access to up-to-date facilities and services.
The city has taken steps to upgrade and expand its infrastructure as a means to attract new businesses to the area. One recent project involved the expansion of a 24-inch water distribution line in a quadrant bordered by Colorado Highway 85 and E-470 located within the metropolitan Denver area with close proximity to Denver International Airport. This area has the potential for residential and commercial growth that will ultimately create jobs.
Extending the water line required passing under Highway 85 and a Burlington Northern railway. This portion of the project required some planning as the highway and railway were adjacent to each other, and the area included an existing array of telecom, fiber, gas, sewer and water lines, not to mention the ground conditions, which consisted of sand, gravel and clay.
When the project went out to bid, Northern Colorado Constructors knew they had the equipment and expertise for the job. The company was formed in 1979 and specializes in utility construction utilizing open cut and auger boring methods.
“We introduced auger boring to our customers in the 1980s,” says Chris Zadel, who is the construction manager for Northern Colorado Constructors (NCC). “Now we have one entire crew dedicated to this installation method, and we’re one of few utility contractors in the area with auger boring capabilities.”
Planning pays dividends
The project called for a 36-inch casing, which would house a 24-inch water main, to be installed under Highway 85 and the Burlington Northern Railway. The total length of the bore was approximately 700 lineal feet. As Zadel and his team reviewed the project, they decided trying to complete the full bore in one shot would be difficult considering the soil conditions. Additionally, the project required precision placement of the casing both vertically and horizontally to avoid the existing infrastructure and a house that sat within 20 feet of one of the receiving pits.
“We took our time with the planning stage, but we wanted to be proactive due to the tight requirements and traffic flows in the area,” says Zadel. “We had to hit on both sides within a couple of feet horizontally, so we made sure to get it right the first time.”
After taking into account the ground conditions and precision placement, NCC decided to place the bore pit in between the highway and railway and complete two bores – one 340-foot bore under the highway and then turned the auger boring machine around and complete a second 340-foot bore under the railway.
“We were concerned that the ground conditions may limit our ability to effectively complete a 700-foot bore and we had a slight deflection into the receiving pit on the far side of the railway,” says Zadel. “We figured the chances of losing material in front of the head were high and that could potentially affect the structure of the highway; plus, hitting that mark in the receiving pit would be easier with a shorter bore.”
New tech
Due to the ground conditions and precision needed to hit the receiving pits, Zadel decided to try a new steering head. He recently received a mailing touting the On-Target steering head from McLaughlin. The new steering head allows contractors to not only control horizontal on-grade (up and down) changes, but also allows for lateral (left to right) direction changes. The system provides contractors with more control of the auger boring steering head leading to higher accuracy for difficult on-grade bores.
The cutting path — grade and lateral movement — of the steering head is controlled by hydraulic actuated panels that open and close to keep the head on the intended path. A control station features a hydraulic power pack to control the movement of the steering head, and a built-in water level helps monitor grade throughout the bore. Two halogen lights in the control station indicate lateral (left and right) steering head movements.
“We felt the On-Target steering head offered us the steering capabilities we needed to keep the material tight in the front of the steering head, so we wouldn’t lose the material as we were boring,” says Zadel. “We had to shoot in an area where, if we didn’t make our points on the both sides, we’d be on private property within 20 feet of a house or into existing utilities, and that would have made it quite difficult to try to excavate and install the water main. We really had a two-foot-square window to hit, so a conventional steering head wasn’t an option.”
The bore pit was placed in between the highway and railway at a depth of 16 feet to provide the necessary cover requirements. The auger boring machine was placed in the pit and Zadel and his crew began working on the 340-foot shot heading west that passed under the highway while pushing the 36-inch casing into place.
The On-Target steering head uses a built-in vertical alignment sensor that provides continuous monitoring of grade using two projection halogen lights enclosed in the steering head. Because of this, a 20-inch auger was used to ensure the crew could see the lights and maintain line throughout the bore.
On the eastbound bore passing under the railway, the crew had to deflect the bore into the receiving pit located in the eastbound lane of 124th Avenue in order to bore out of the flow of traffic and not require the closure of this busy street. In addition, the receiving pit was bordered by existing utilities to the north and a private septic system to the south.
“The steering head worked great and we hit our marks with no issues,” says Zadel. “At one point in the bore under the highway we hit hard clay and our pushing pressures went up tremendously. However, the machine and head didn’t have any issues, but the clay did affect our daily production.”
Overall, the project took six weeks to complete. In the better materials, Zadel states they were getting about 40 feet a day, but in the clay soils they were lucky to get 20 feet a day.
“I think very seldom do contractors complete one bore in two separate sections like we did on this project,” says Zadel. “I don’t think the bore could have been completed in one shot with the accuracy needed considering the existing ground conditions and other unknown factors. Overall the On-Target steering head worked well and is a cost-effective option for tight bores.”
FOR MORE INFORMATION:
McLaughlin, (800) 435-9340, www.mightymole.com
Northern Colorado Constructors, (303) 857-1754
Comments