August 2009 Vol. 64 No. 8
Features
Slide Rail System Keeps Lift Station Project On Time, Budget
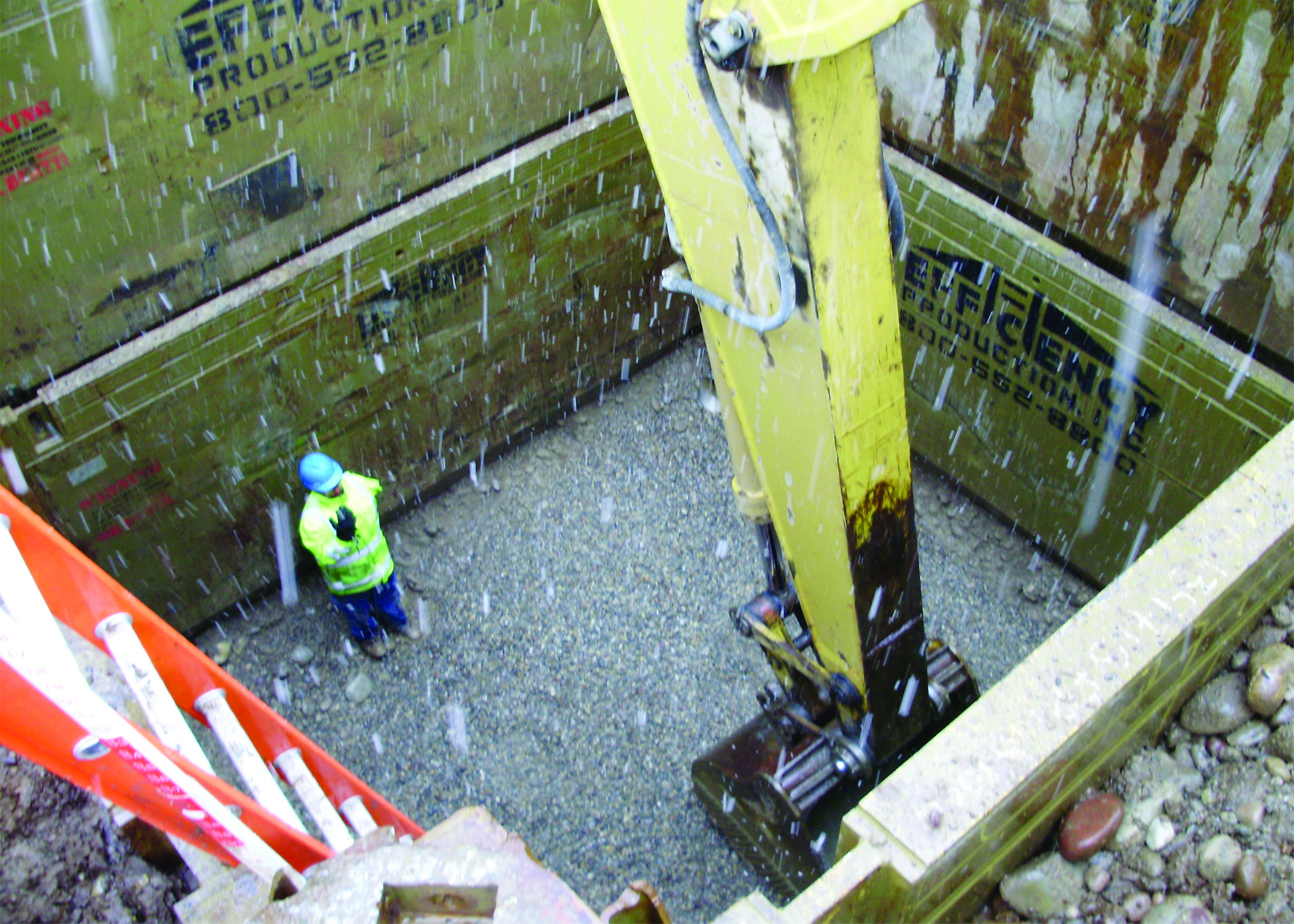
Evans Construction Co. of Jackson, WY, recently installed a new eight-foot diameter lift station in the suburbs near Jackson Hole.
Due to the limited space and multiple adjacent structures and cross utilities, Evans needed a non traditional shoring system.
Evans was originally contracted to replace the pumps for an overworked six-foot diameter lift station. But when it was discovered that the lift station was leaking, city officials and engineers decided to contract Evans to install a new lift station with new pumps. Evans also installed two manholes to reroute the sewer line to the new lift station.
“Because of the tight quarters where we installed the lift station, we had to truck out all the dirt we excavated, and truck it all back in again,” said Brad Shultz, Evans’ project manager. “The challenge was how to safely shore the excavation while expending as little money and effort as possible and working in some very tight and difficult spots.”
The three traditional shoring methods for four sided pits: tight sheeting, welded walers or four sided trench shields, were dismissed at bidding because the excavation needed to stay in the utility easement, and there were many mature trees and houses around the site. Plus, electrical utilities were adjacent to the pit within 15 feet. Sloping was definitely not an option.
Shultz started looking for a shoring solution by contacting Efficiency Production Inc., a leading manufacturer of trench shielding and shoring equipment.
Solution
Efficiency’s Slide Rail Systems Manager, Greg Ross, looked at Evans’ project specs and recommended Efficiency’s Universal Slide Rail System, a component shoring system comprised of steel panels (similar to trench shield sidewalls) and vertical steel posts. The versatile system can be used in a variety of configurations, such as small four sided pits; large unobstructed working pits as big as 50 by 50 feet; or in a linear multi bay configuration to install pipe lengths 40 feet.
Slide rail is installed simultaneously as the trench or pit is excavated by sliding the panels into integrated rails on the posts – an outside slotted rail first, then an open face rail on the inside – then pushing the panels and posts incrementally down to grade as the pit is dug; a process commonly referred to as a “dig and push” system. Efficiency Production is the only slide rail manufacturer to offer an open face rail design on their slide rail posts.
“The system is so ingenuous because if installed properly, all the components slide down as the hole is dug, just as the name suggests,” said Shultz. “The panels slide in the post’s rails, then the posts slide past the panels as they are pushed. There is very little binding, and almost no need to aggressively pound on the components.”
Evans rented a four sided configured slide rail system, utilizing a set of 16 by 16-foot long panels, and 24-foot corner posts to install the lift station at a 20-foot grade. To reach 20 feet, Evans’ crews installed an eight-foot panel stacked with a four-foot panel on top at the outside slotted rails of the slide rail posts. Next, they installed another set of eight-foot tall panels into the inside open face rails on the posts to reach 20 feet.
“Everything went exactly as planned, perfect really,” said Shultz. “With slide rail, we could excavate to the exact dimensions of the system without any over-cutting. This was a huge cost and time saver. We probably saved as much as the cost of a new trench box.”
Evans used Caterpillar 330 and 325 excavators to install the system and precast lift station.
FOR MORE INFORMATION:
Evans Construction Company, (307) 733 3029,
Efficiency Production Inc., (800) 552 8800, efficiencyproduction.com
Caterpillar, (309) 675-1000, www.cat.com
Comments