October 2008 Vol. 63 No. 10
Business
Power Outages Hasten Deere Plant Conversion To Underground
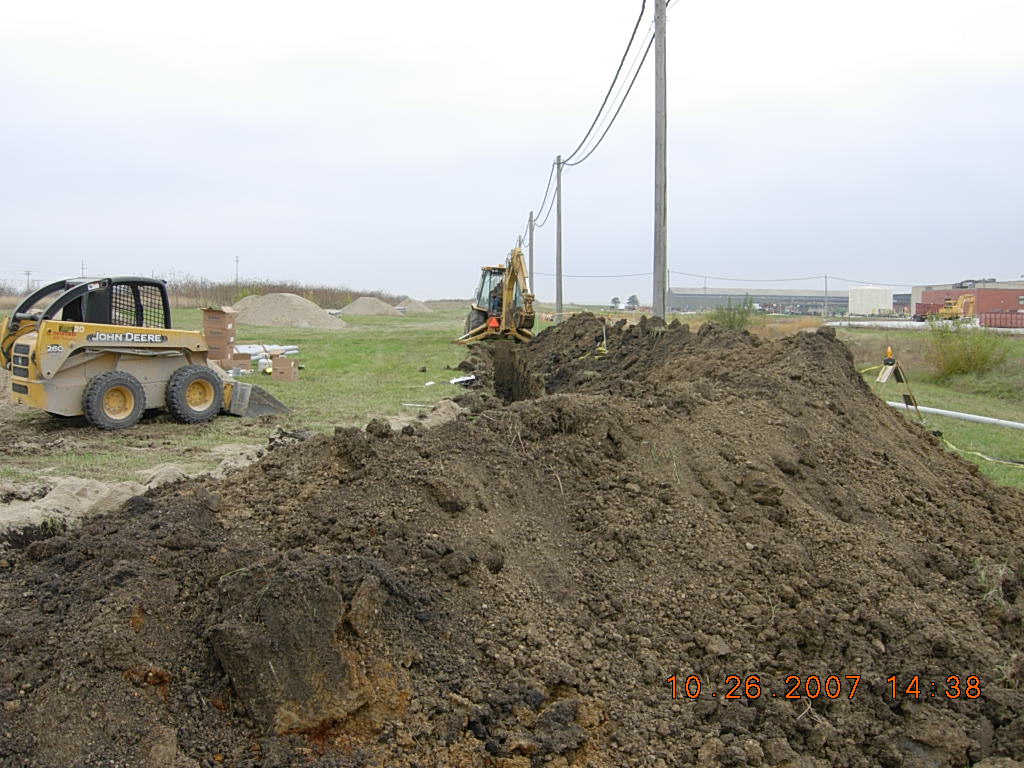
For years, electric and telecommunications cables to new residential, business and industrial developments have been placed underground where they are protected from wind storms, ice and other weather related risks.
Downed communications lines interrupt business activities and cause widespread inconvenience. Loss of electrical power shuts down lighting and most heating and cooling systems, and can cause life threatening conditions.
Even so, a surprising amount of cable remains suspended from poles that are subject to damage which causes outages requiring costly repairs. Because services must be restored as quickly as possible, following a major storm is not the time to plan an aerial to underground conversion program, and damaged aerial cable infrastructure usually is replaced on utility poles.
Why isn’t more aerial cable being replaced by buried cable to reduce the risk of future outages?
Money is the most often given reason. Utility providers cite high costs and question who will pay the bills. However, regulators in some states are beginning to take a hard look at those costs and are investigating ways to encourage replacement of overhead infrastructure, especially power distribution systems.
In addition, many business facilities and government agencies are replacing old overhead systems with underground cable. Because they own the systems, the decision can be made purely on economic and improved service factors.
For example, the John Deere Works, a division of Deere & Co., recently completed a major aerial to underground conversion at its Ankeny, IA, facility. On a site of approximately 450 acres, the operation’s more than 1,200 employees manufacture cotton picking equipment, sprayers and tillage machines. The project involved replacement of 15 KV aerial feeders to the plant with new underground feeders.
Failing infrastructure
“The project upgraded aging infrastructure,” said Jim Floersch, facilities engineer. “The 30 year old aerial feeders were responsible for several recent failures. Replacing them improved reliability of critical utility lines, reduced maintenance and reduces risks from wind and weather. Placing cable underground fit corporate goals for standardization and located 100 percent of the facility’s feeders underground. Removing aerial cable also improved ‘street appeal’ of the area.”
Baker Electric, Des Moines, IA, was the primary contractor for the project to replace three aerial feeders. Also included in the project was replacing underground feeders containing duct banks of four, five inch conduits approximately 2,500 feet long and placement of three, 8 by 10 by 8 foot precast manholes at feeder intersection points.
Contributing to the decision to replace the old feeders were failures of two of the three aerial feeders within a two week period, causing serious disruptions of plant operations, said Floersch.
“Baker Electric restored power to the plant in each of the two failures and was instrumental in the decision to replace the feeders which was considered urgent,” said Floersch. “Corporate specified the cable, the cable supplier, the terminations and required training for the terminations. Baker Electric submitted the design proposals.
“John Deere Des Moines Works, Facility Engineering, reviewed and approved the proposals, and Baker Electric completed the installation with no further interruptions of production in the plant.”
The three new feeders serve the plant’s 15 KV distribution system.
“Baker Electric furnished components and installed the complete system,” said Roger Innis, Baker project manager/estimator. “Feeders were 15 KV, 500 mcm, copper cables. These fed from overhead distribution at utility company drops to pad mounted 15 KV switch gear at individual buildings. The pad mounted switch gear was existing and 15 KV system fed into plant buildings from there.”
Digging and drilling
Innis said most of the duct bank was installed by open cut, using a backhoe for excavation. The trench was 24 inches wide and average depth ranged from 36 to 48 inches. Open-cut construction was used because it was most cost effective. The conduit’s route was in open areas, and width and depth requirements were a little to big for trenching, Innis said. One of the feeders was rerouted around a building, rather than through it, which fit with the company’s plans to extend the structure.
Two segments were directionally drilled. “One shot,” said Innis, “took four 5 inch ducts approximately 100 feet under existing railroad tracks. The other was for one 5 inch duct going approximately 300 feet from the road to a substation near a building. Duct used for these bores was Carlon Boreguard.”
The decision to place power cable underground depends on cost, whether the system is new, to make repairs or like the Deere project to replace old cable, said Innis.
“Most new installations we are doing are underground,” he added. “This project is a little different than normal because of it being a 15 KV project and the age and reliability was called into question with the first failure. The system was serving a large industrial plant, and I am sure costs of down time there was a major consideration in decisions about the new installation.”
Maintenance issues hasten change
If there are maintenance issues or the need to change existing feeders, most projects of this nature are planned to convert old aerial plant to underground, Innis pointed out.
“If there is going to be additional load added to existing feeders, there are major costs associated with feeders and gear,” Innis said. “Conversion is always examined at that point. In most cases, conversion is selected with the decision based on multiple factors: reliability, costs, future considerations and, in quite a few cases, aesthetics.
“Most of the projects we are dealing with are systems of 480 volt or 208 volt. Due the size of these feeds and the current National Electrical Code (NEC), in most cases the difference in costs to convert to underground is low enough and most of the old 480 or 208 volt systems are being replaced underground.”
Innis expects future revisions to the power distribution throughout the plant will all be done underground.
“I cannot imagine seeing another aerial run at this facility,” he said.
Innis added that the Deere project was typical of aerial to underground conversions. Most are projects that replace a customer’s complete service, usually due to age, required repairs or the need for larger capacity of service entrance to the facility.
“The utility company removes wooden poles and pole top transformers and installs a new pad mounted transformer,” he explained. “Our work is to provide concrete pads and all underground conduits and wiring for re-feeding the facility with electricity. On this project, we were required to pothole the entire length of the trench because there were so many existing critical utilities. Potholing was performed by a subcontractor using vacuum excavation equipment.”
Baker Electric did all underground work with crews from its underground division.”From a cost standpoint, this enables us to directly assist a project owner in the process of making a decision about going underground.”
FOR MORE INFORMATION:
Baker Electric Inc., www.bakerelectric.com
Carlon Boreguard, (877) 268-3700, www.carlonsales.com
Comments