November 2008 Vol. 63 No. 11
General
Workforce Crisis: Unique Training Facility Provides Multiple Workforce Solutions
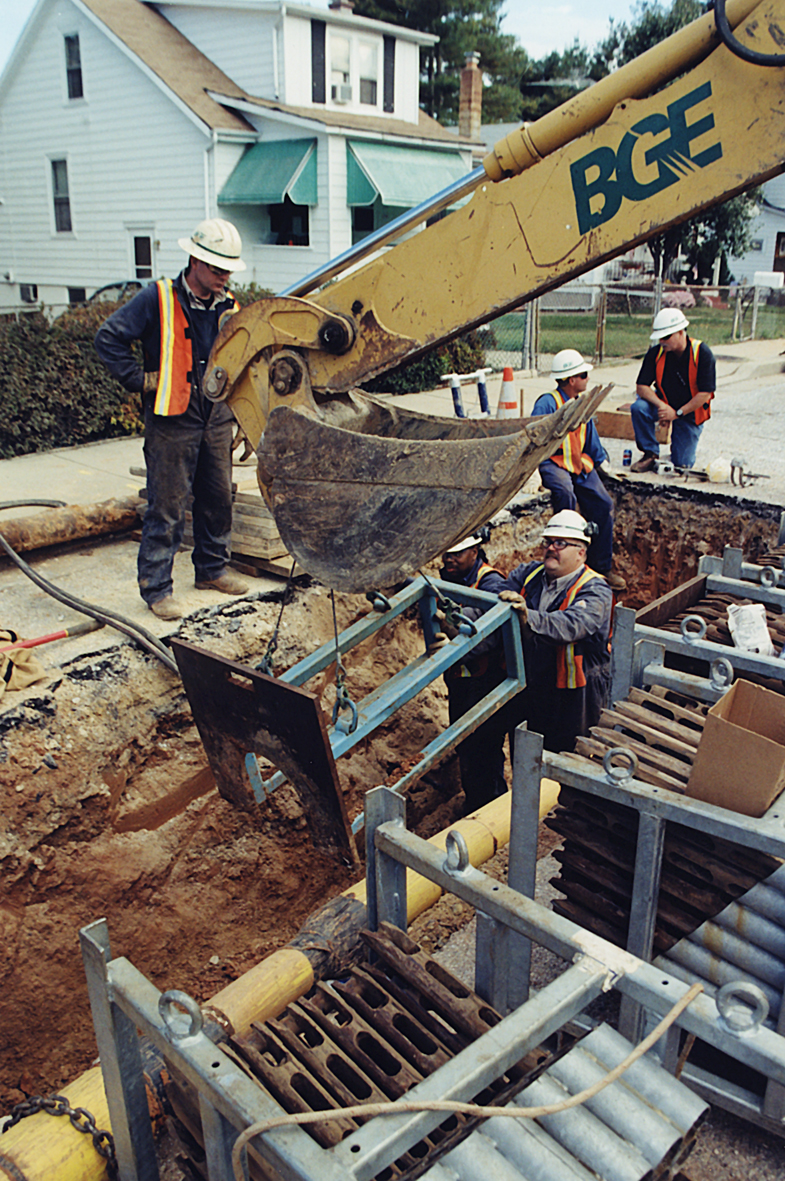
There’s no single solution to solving current and future workforce shortages of construction workers. Organizations usually must consider several options to address their individual situations.
Editor’s Note: This is the fifth installment in our ongoing series examining the skilled workforce shortage in many areas of the underground construction and rehabilitation industry.
As planners develop programs to find and retain qualified employees, training almost always is an important consideration. New employees must be trained and current personnel require additional training to replace personnel who have retired or left the company.
The impressive Training and Research Facility opened last year by the Mears Group was not a specific reaction to anticipated worker shortages, but it is expected to play an important role in ensuring Mears has the trained personnel it needs to complete projects in the years to come.
Unlike many contractors and utility providers, the Mears Group is not anticipating a large number of vacancies resulting from the retirement of senior employees, said Kevin Parker, director of safety training environment compliance.
“The primary labor issue for us is finding new employees as the company’s workload increases,” said Parker. “Equipment operator positions seem to be more difficult to fill, along with experienced crew foreman and supervisors, and applicants experienced and certified in NDT (non destructive testing, and corrosion technicians are always in demand.”
Significant role
The Mears facility plays an important role in training new employees and those already on the payroll.
“New employees go through several days of safety training followed by job specific training,” said Parker. “The job specific training covers the tasks they will have once they get to a project site. As their job tasks change, then on the job training takes place or we bring them back to our facility for additional training. As our new facility matures, we continue to add to it to address areas we believe will improve safety and make a more efficient work force.
“Employees with management potential go through various training avenues, both in house as well as third party. If we cannot provide a specific type of management training utilizing our own instructors or programs, then we’ll bring to our facility a course designed in that specific area of need.”
Parker said continuing training is important for two reasons: safety and productivity.
“We see a direct correlation between an increased amount of training and the reduction in on the job injuries,” he explained. “A well trained work force is a safer work force and a more productive work force.”
Located at Mears Group corporate headquarters in Rosebush, MI, the training and research facility occupies 2.75 acres and was planned and designed by a team of engineers, subject matter experts and construction specialists with the goal of replicating everyday challenges faced by personnel evaluating pipelines both above and below ground.
Parker called the center the cornerstone of Mears’ operator qualification programs for Mears employees, including field training capabilities for pipe excavation, pipe coating removal, surface preparation, coating application, evaluating casing isolation, external corrosion direct assessment (ECDA), indirect inspection surveys and pipe direct examinations.
Employees can hone survey skills on the test site which includes more than 1,800 feet of pipe in 10 , 12 , 20 , 24 and 30 inch diameters. The primary loop of pipe includes over 50 coating flaws that were intentionally created ranging in size, shape and pipe orientation.
Special features
Parker said a unique element of the test facility is a 100 foot segment of casing along a 10 inch carrier pipe for testing electrical isolation and the effects of electrolyte within the annular space. Test wires and reference electrode access holes for inserting the electrode into the annular space are positioned every 10 feet along the casing. The annular space can be flooded with varying amounts of water. Variable resistors every 10 feet can be used to change the location of contacts including simulating “high resistance” contacts. The carrier pipe contains prefabricated coating and metal loss anomalies of known sizes and locations.
“The casing section provides the ability to simulate scenarios that would actually happen out in the field,” said Parker.
The research features of the facility allows Mears to determine which coating flaws can be detected by the different ECDA survey techniques and/or equipment available in the marketplace. The impact of the different coatings along with the different cathodic protection configurations on the detection capabilities of the equipment can be analyzed. Real world surface conditions have been included such as soil, gravel, asphalt and concrete. The CP systems and piping can be configured in over 25 different setups using the Anodeflex, zinc ribbon, magnesium anodes and remote anode beds.
The facility’s features are not limited to Mears needs.
“In April,” said Parker, “we hosted a National Association of Corrosion Engineers (NACE) International Cathodic Protection Level 1 and 2 course at our facility and have the same event scheduled for April 2009. The Detroit NACE section also held an External Corrosion Direct Assessment (ECDA) 2 day seminar at our facility last summer. Among other projects, we are conducting research on casing ECDA for pipeline integrity.”
Founded in 1970 as a local engineering firm, the Mears Group, now a Quanta Services company, has grown into an international engineering and construction company encompassing pipeline and related services.
The Engineering/Technical Division provides turnkey pipeline integrity management services.
Services of the Mears Construction Division include bell hole excavation, pipeline repair, anodeflex installation, pipeline maintenance support, ILI inspection support and anomaly digs, and pipeline coating and reconditioning.
The Horizontal Directional Drilling Division is involved in projects for the pipeline, utility, water and fiber industries.
The Mears Group employs more than 500 people based in corporate headquarters, regional offices, and offices in Canada, Mexico, Brazil and Argentina.
FOR MORE INFORMATION:
Mears Group, (800) 632-7727, www.mears.net
Comments