November 2008 Vol. 63 No. 11
General
NH Penstock Pipeline Replaced With Fiberglass Pipe
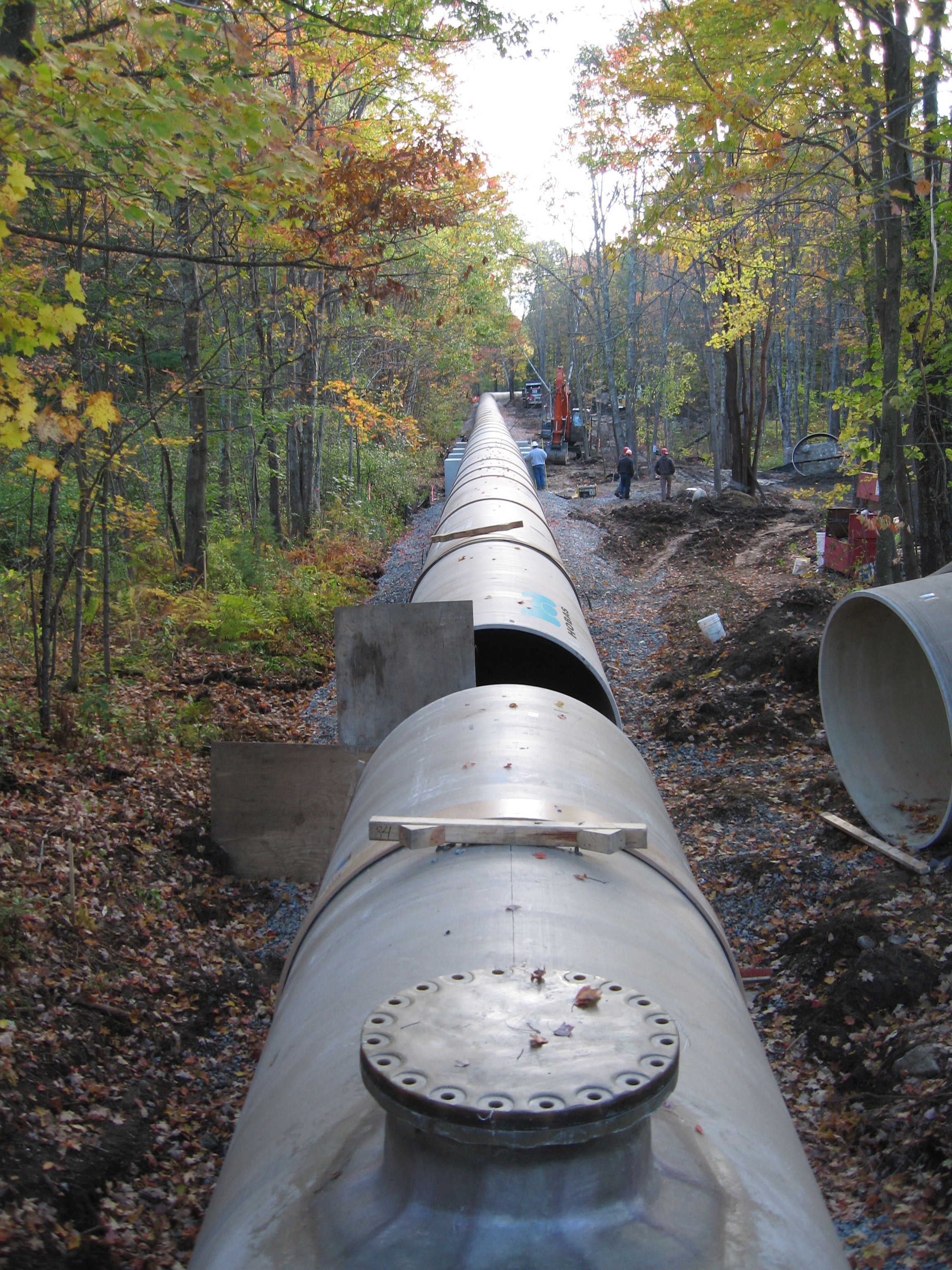
Meandering through New Hampshire’s White Mountains, a large wooden penstock pipeline served as the main water supply for a local hydro facility, Jackman Station.
The facility is fed by the Franklin Pierce Reservoir, which was created by the hydro facility’s dam and surrounding earthen dikes. The water elevation in the reservoir is managed according to spring run-off.
Public Service of New Hampshire (PSNH), the Granite State’s largest electric utility, serves more than 475,000 homes and businesses. PSNH’s power generation facilities consist of nine hydroelectric plants, including the Jackman Hydro station, which was built in 1926. This facility, located in Hillsborough, has been serving the area for years, but the penstock was approaching the end of its service life.
Prior to the recent improvements, 5,000 feet of wood stave penstock extended from the Franklin Pierce reservoir to a surge tank upstream of the powerhouse. This 7.5-foot diameter penstock was made up of vintage wood stave sections, circa 1926. Repairs were undertaken in 1954 and in the 1970s, yet the downstream sections of the wood penstock still leaked badly. This leakage caused icing problems during winter months and required constant maintenance. In 2003, the penstock had a significant rupture that impacted abutting properties. To prevent future failures and ensure reliable operations of the hydro facility, repairs to the existing penstock were necessary. In a series of contracts, PSNH decided to replace the remaining wood stave penstock with a new pipeline.
Kleinschmidt Energy & Water Resource Consultants, headquartered in Pittsfield, ME, was retained to develop a feasibility study and engineer a replacement pipeline. Kleinschmidt initially evaluated five pipe material options for the penstock replacement: wood stave, concrete, HDPE plastic, steel and fiber reinforced polymer (FRP). Factors that led to the final determination included the structural reliability, corrosion resistance, hydraulic capacity, ease of installation (pipe weight) and performance history of the pipe material. Kleinschmidt provided their evaluation and recommendations to PSNH, which chose the fiberglass pipe option and purchased CCFRPM pipe manufactured by Hobas Pipe USA of Houston.
Flexibility
“The corrosion resistance and relative stiffness of FRP pipe meant it could be supported on the existing grade and half buried, rather than placed on saddles or completely covered in a buried trench. This design flexibility, combined with a longer projected service life led to a competitive total construction cost for the FRP alternative,” stated Keith Martin, a project engineer and civil/structural engineer with Kleinschmidt.
“The lower frictional resistance of the FRP compared to other materials allowed the replacement pipe to be reduced to a 7-foot diameter without additional head loss,” added Martin.
The pipe was half buried in the shallow trench of the existing penstock, requiring minimal excavation costs and low environmental disturbance. Approximately 300 feet of the new penstock was supported above ground on steel saddles to accommodate the topography as well as minimizing the impact to the wetlands that the penstock crossed.
“HOBAS CCFRPM is manufactured by a unique computer controlled centrifugal casting process. To achieve the higher axial strength necessary for the aboveground installation, additional reinforcement is placed in the longitudinal direction during the manufacturing process,” explained Rene Garcia, Sr. Hobas engineering associate.
“PSNH bought the pipe directly and CCB Inc. of Westbrook, ME, was contracted to install it,” said Newell Porter, project manager with CCB.
Remote challenges
The job site posed some challenges as the pipe was installed in a remote area. “The pipe arrived as scheduled and unloaded near the roadside. This phase of the job called for 1,020 feet of 84-inch diameter pipe. The individual joints were then carried to the point of installation with an excavator. We had no truck access to the installation point. The first part of the installation was through a curve where 10-foot joint sections were connected and then deflected to make up the curve,” stated Porter.
The HOBAS FWC coupling joint utilized on this project was a pressure joint. It is commonly used in direct bury application and also for above ground installations such as penstocks. It is a structural filament wound sleeve over wrapped and mechanically locked to an internal full-faced elastomeric membrane. The sealing design includes both lip and compression elements so the joint is suitable for both non-pressure and pressure service up to 250 psi. “In our case, we air tested each joint after assembly with a 10 psi air test. None of the joints leaked. Once the line was in operation, we were required to visually inspect each and every joint for a sign of leakage and there was none,” explained Porter.
JML Trucking and Excavating of Errol, NH, was the installation subcontractor for CCB. Butch Lane echoed the general contractor’s sentiments, “The joints are really tight. We were able to put PSNH online two weeks ahead of schedule and that makes them happy.
“At the end of the project, it was found to be approximately seven times cheaper per foot to utilize the fiberglass pipe option partially backfilling the penstock than to support it above ground,” summarized Martin. Hydraulic advantages and longevity of the line will also provide life-long savings.
FOR MORE INFORMATION:
Hobas Pipe USA, (800) 856-7473 or (281) 821-2200, www.hobaspipe.com
Kleinschmidt Energy & Water Resource Consultants, (207) 487-3328, www.kleinschmidtusa.com
Comments